IFM SMF420 Manual
IFM
Ikke kategoriseret
SMF420
Læs nedenfor 📖 manual på dansk for IFM SMF420 (73 sider) i kategorien Ikke kategoriseret. Denne guide var nyttig for 24 personer og blev bedømt med 4.5 stjerner i gennemsnit af 2 brugere
Side 1/73
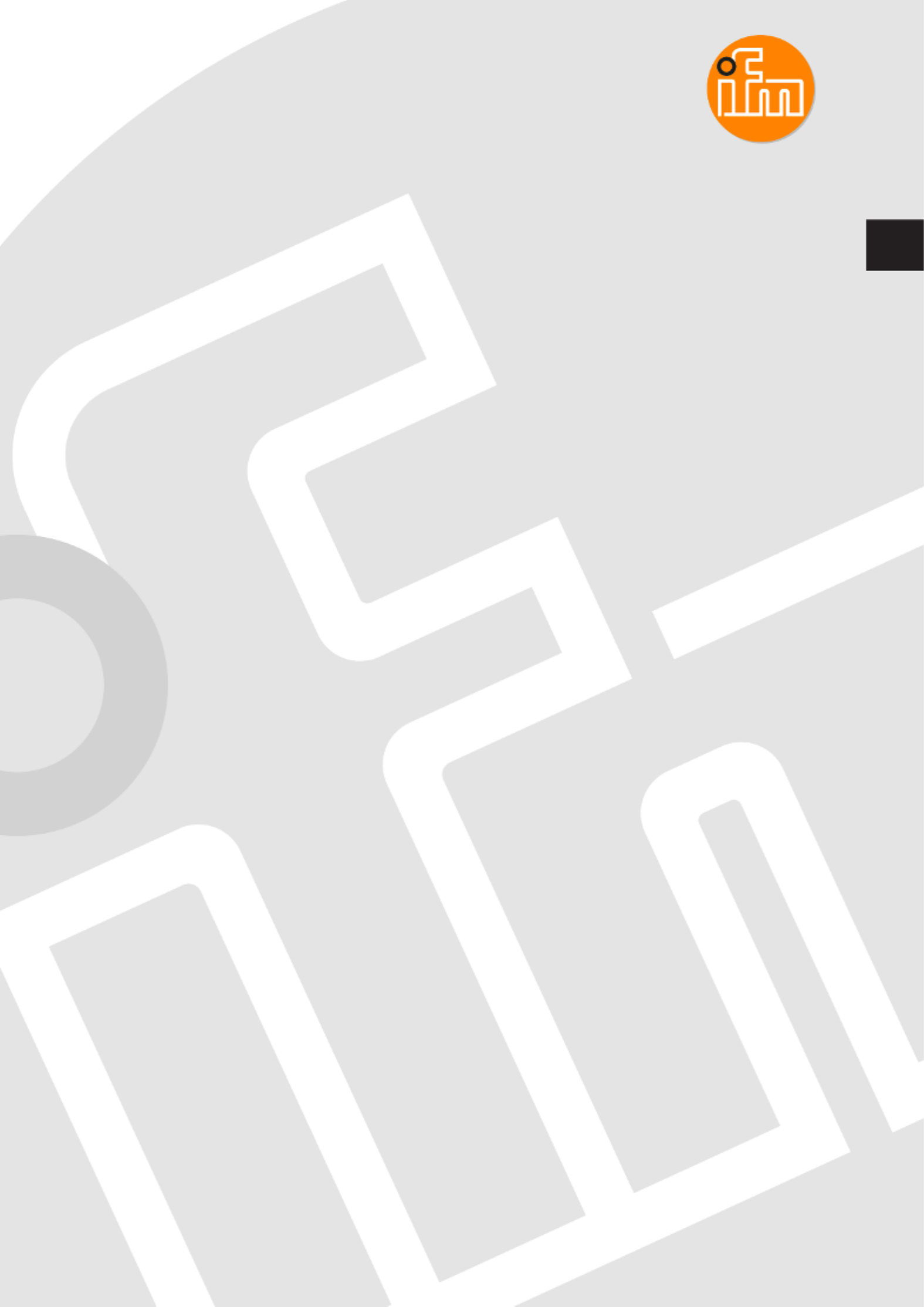
Operating instructions
Magnetic-inductive flow meter
SMFxxx
11541382 / 0003 / 2024
GB
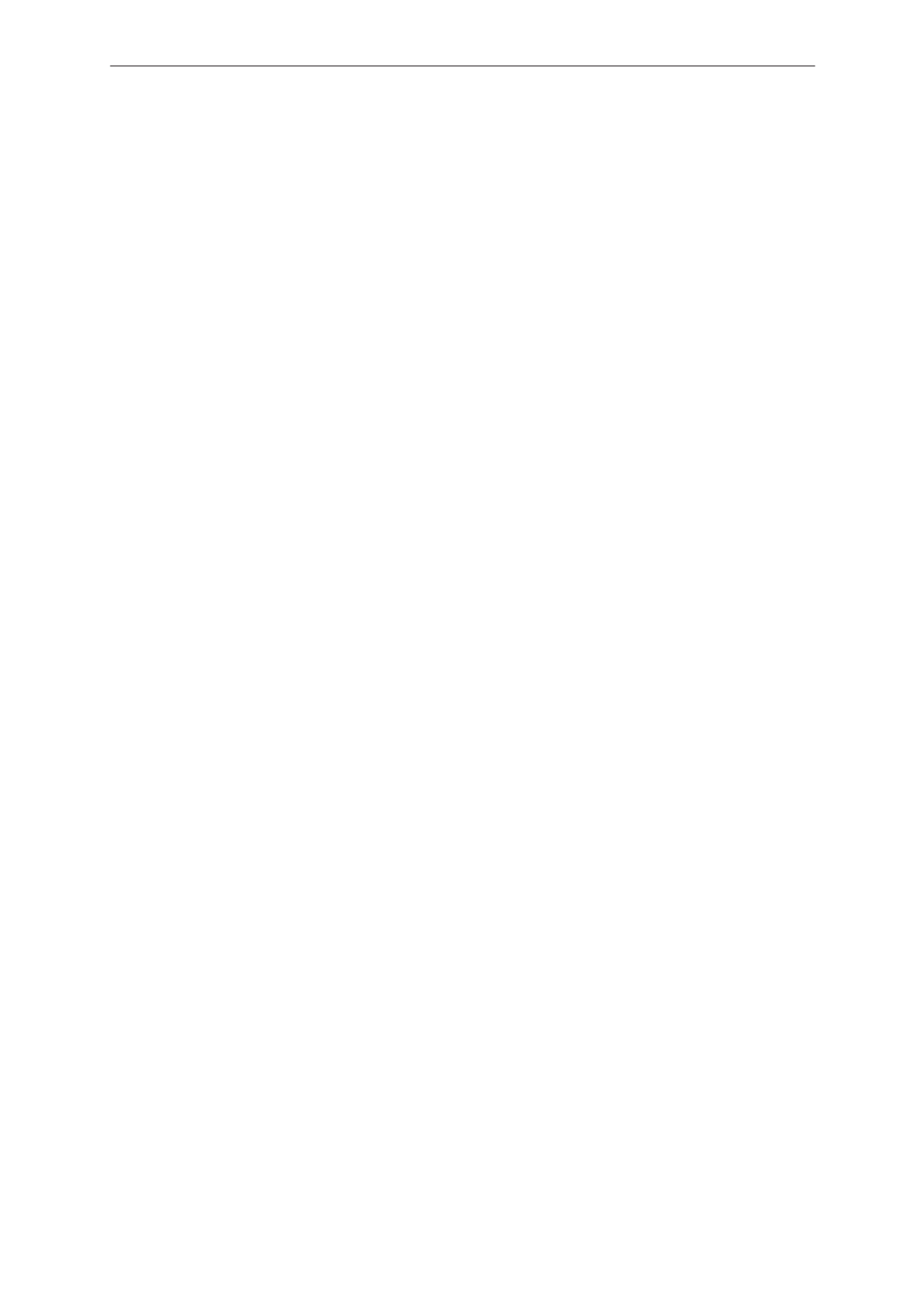
SMFxxx Magnetic-inductive flow meter
2
Contents
1 Preliminary note . . . . . . . . . . . . . . . . . . . . . . . . . . . . . . . . . . . . . . . . . . . . . . . . . . . . . . . . . . . . . 4
1.1 Symbols used . . . . . . . . . . . . . . . . . . . . . . . . . . . . . . . . . . . . . . . . . . . . . . . . . . . . . . . . . . 4
1.2 Warnings. . . . . . . . . . . . . . . . . . . . . . . . . . . . . . . . . . . . . . . . . . . . . . . . . . . . . . . . . . . . . . 4
2 Safety instructions. . . . . . . . . . . . . . . . . . . . . . . . . . . . . . . . . . . . . . . . . . . . . . . . . . . . . . . . . . . . 5
3 Intended use . . . . . . . . . . . . . . . . . . . . . . . . . . . . . . . . . . . . . . . . . . . . . . . . . . . . . . . . . . . . . . . . 6
3.1 Application area . . . . . . . . . . . . . . . . . . . . . . . . . . . . . . . . . . . . . . . . . . . . . . . . . . . . . . . . 6
4 Function ................................................................... 7
4.1 Output OUT1 selection options . . . . . . . . . . . . . . . . . . . . . . . . . . . . . . . . . . . . . . . . . . . . . 8
4.2 Output OUT2 selection options . . . . . . . . . . . . . . . . . . . . . . . . . . . . . . . . . . . . . . . . . . . . . 8
4.3 IO-Link ............................................................... 8
5 Mounting................................................................... 10
5.1 Device dimensions . . . . . . . . . . . . . . . . . . . . . . . . . . . . . . . . . . . . . . . . . . . . . . . . . . . . . . 10
5.2 Installation position . . . . . . . . . . . . . . . . . . . . . . . . . . . . . . . . . . . . . . . . . . . . . . . . . . . . . . 10
5.3 Inlet and outlet pipe lengths . . . . . . . . . . . . . . . . . . . . . . . . . . . . . . . . . . . . . . . . . . . . . . . 13
5.4 Process connection. . . . . . . . . . . . . . . . . . . . . . . . . . . . . . . . . . . . . . . . . . . . . . . . . . . . . . 13
5.4.1 Clamp adapters. . . . . . . . . . . . . . . . . . . . . . . . . . . . . . . . . . . . . . . . . . . . . . . . . . . . . 15
5.4.2 Welding adapter . . . . . . . . . . . . . . . . . . . . . . . . . . . . . . . . . . . . . . . . . . . . . . . . . . . . 16
5.4.3 Screw adapter. . . . . . . . . . . . . . . . . . . . . . . . . . . . . . . . . . . . . . . . . . . . . . . . . . . . . . 17
5.4.4 Flange adapter . . . . . . . . . . . . . . . . . . . . . . . . . . . . . . . . . . . . . . . . . . . . . . . . . . . . . 18
5.5 Use in hygienic areas . . . . . . . . . . . . . . . . . . . . . . . . . . . . . . . . . . . . . . . . . . . . . . . . . . . . 18
5.6 Use in hygienic areas according to 3-A . . . . . . . . . . . . . . . . . . . . . . . . . . . . . . . . . . . . . . . 18
6 Electrical connection . . . . . . . . . . . . . . . . . . . . . . . . . . . . . . . . . . . . . . . . . . . . . . . . . . . . . . . . . . 20
7 Operating and display elements . . . . . . . . . . . . . . . . . . . . . . . . . . . . . . . . . . . . . . . . . . . . . . . . . 22
8 Menu...................................................................... 24
8.1 Main menu . . . . . . . . . . . . . . . . . . . . . . . . . . . . . . . . . . . . . . . . . . . . . . . . . . . . . . . . . . . . 24
8.2 Submenus. . . . . . . . . . . . . . . . . . . . . . . . . . . . . . . . . . . . . . . . . . . . . . . . . . . . . . . . . . . . . 25
9 Set-up..................................................................... 31
9.1 Guided installation via an installation wizard . . . . . . . . . . . . . . . . . . . . . . . . . . . . . . . . . . . 31
10 Parameter setting . . . . . . . . . . . . . . . . . . . . . . . . . . . . . . . . . . . . . . . . . . . . . . . . . . . . . . . . . . . . 32
10.1 Parameter setting via the unit keys . . . . . . . . . . . . . . . . . . . . . . . . . . . . . . . . . . . . . . . . . . 32
10.2 Parameter setting via IO-Link . . . . . . . . . . . . . . . . . . . . . . . . . . . . . . . . . . . . . . . . . . . . . . 33
10.3 Output configuration . . . . . . . . . . . . . . . . . . . . . . . . . . . . . . . . . . . . . . . . . . . . . . . . . . . . . 33
10.3.1 Analogue signal . . . . . . . . . . . . . . . . . . . . . . . . . . . . . . . . . . . . . . . . . . . . . . . . . . . . 33
10.3.2 Switching signal diagnostics . . . . . . . . . . . . . . . . . . . . . . . . . . . . . . . . . . . . . . . . . . . 35
10.3.2.1 Switching signal for flow direction . . . . . . . . . . . . . . . . . . . . . . . . . . . . . . . . . . 35
10.3.2.2 Switching signal for fluid detection . . . . . . . . . . . . . . . . . . . . . . . . . . . . . . . . . 36
10.3.3 Consumed quantity monitoring (totaliser function). . . . . . . . . . . . . . . . . . . . . . . . . . . 37
10.3.3.1 Switching signal totaliser. . . . . . . . . . . . . . . . . . . . . . . . . . . . . . . . . . . . . . . . . 37
10.3.3.2 Pulse signal totaliser . . . . . . . . . . . . . . . . . . . . . . . . . . . . . . . . . . . . . . . . . . . . 38
10.3.4 Digital switching signal . . . . . . . . . . . . . . . . . . . . . . . . . . . . . . . . . . . . . . . . . . . . . . . 39
10.3.5 Output off . . . . . . . . . . . . . . . . . . . . . . . . . . . . . . . . . . . . . . . . . . . . . . . . . . . . . . . . . 42
10.4 Application configuration . . . . . . . . . . . . . . . . . . . . . . . . . . . . . . . . . . . . . . . . . . . . . . . . . . 42
10.4.1 Standard unit of measurement . . . . . . . . . . . . . . . . . . . . . . . . . . . . . . . . . . . . . . . . . 42
10.4.2 Process value for OUT2 . . . . . . . . . . . . . . . . . . . . . . . . . . . . . . . . . . . . . . . . . . . . . . 43
10.4.3 Error behaviour of the analogue output . . . . . . . . . . . . . . . . . . . . . . . . . . . . . . . . . . . 43
10.4.4 Damping . . . . . . . . . . . . . . . . . . . . . . . . . . . . . . . . . . . . . . . . . . . . . . . . . . . . . . . . . . 44
10.4.5 Low flow cut-off . . . . . . . . . . . . . . . . . . . . . . . . . . . . . . . . . . . . . . . . . . . . . . . . . . . . . 44
10.4.6 Output polarity. . . . . . . . . . . . . . . . . . . . . . . . . . . . . . . . . . . . . . . . . . . . . . . . . . . . . . 45
10.4.7 Flow direction . . . . . . . . . . . . . . . . . . . . . . . . . . . . . . . . . . . . . . . . . . . . . . . . . . . . . . 45
10.4.8 Zero calibration . . . . . . . . . . . . . . . . . . . . . . . . . . . . . . . . . . . . . . . . . . . . . . . . . . . . . 46
10.4.9 Calibration of the measurement characteristic. . . . . . . . . . . . . . . . . . . . . . . . . . . . . . 47
10.4.10 Influence of the medium on the temperature . . . . . . . . . . . . . . . . . . . . . . . . . . . . . . . 48
10.4.10.1 Determination of the temperature coefficient tempco . . . . . . . . . . . . . . . . . . . 48
10.4.11 Date/time . . . . . . . . . . . . . . . . . . . . . . . . . . . . . . . . . . . . . . . . . . . . . . . . . . . . . . . . . 49
10.4.12 Energy-saving mode . . . . . . . . . . . . . . . . . . . . . . . . . . . . . . . . . . . . . . . . . . . . . . . . . 49
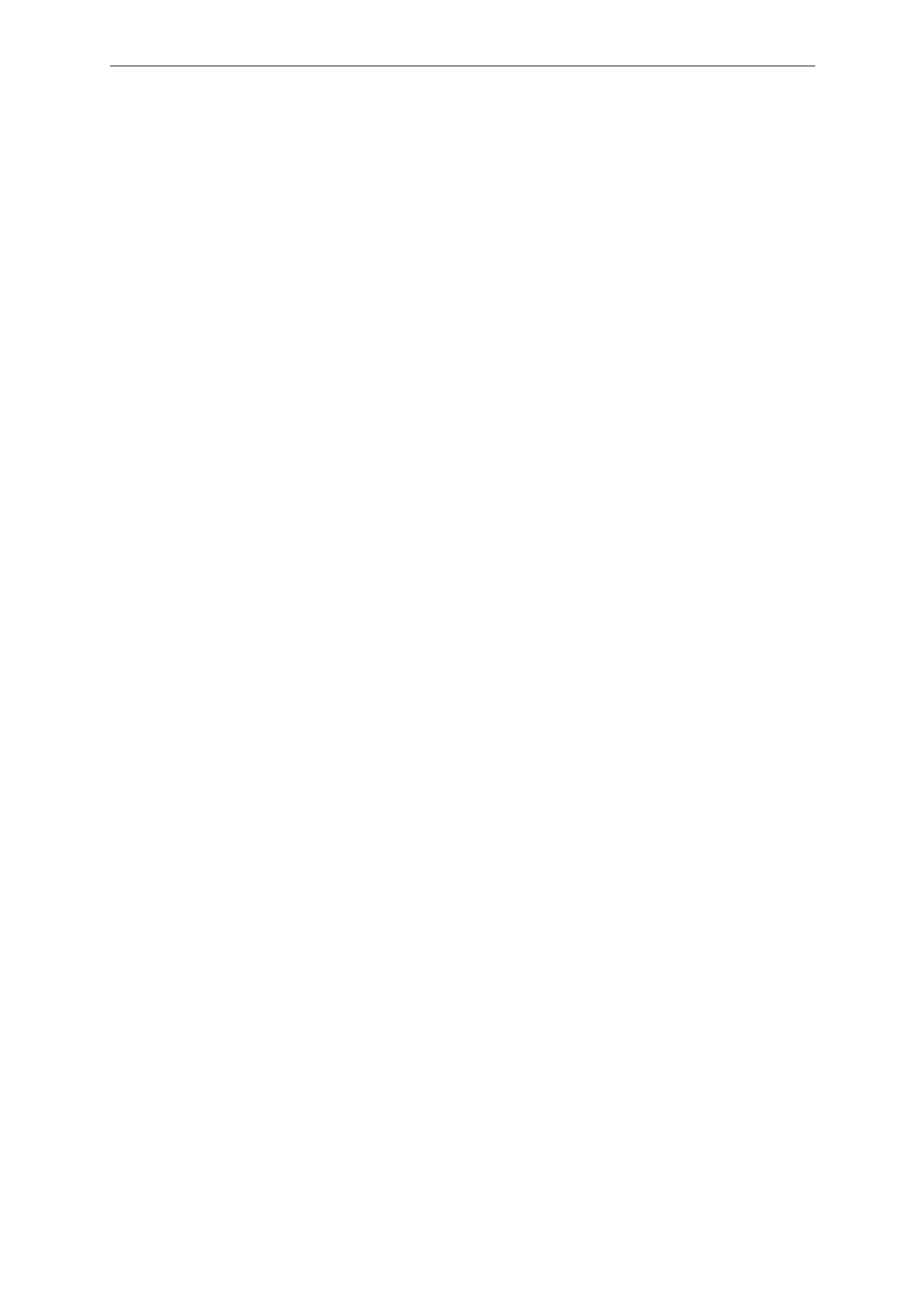
Magnetic-inductive flow meter SMFxxx
3
10.4.13 Totaliser reset . . . . . . . . . . . . . . . . . . . . . . . . . . . . . . . . . . . . . . . . . . . . . . . . . . . . . . 50
10.4.14 Counting method of the totalisers . . . . . . . . . . . . . . . . . . . . . . . . . . . . . . . . . . . . . . . 51
10.4.15 Reset the device . . . . . . . . . . . . . . . . . . . . . . . . . . . . . . . . . . . . . . . . . . . . . . . . . . . . 53
10.5 Display settings. . . . . . . . . . . . . . . . . . . . . . . . . . . . . . . . . . . . . . . . . . . . . . . . . . . . . . . . . 54
10.5.1 Display language . . . . . . . . . . . . . . . . . . . . . . . . . . . . . . . . . . . . . . . . . . . . . . . . . . . 54
10.5.2 Display rotation . . . . . . . . . . . . . . . . . . . . . . . . . . . . . . . . . . . . . . . . . . . . . . . . . . . . . 54
10.5.3 Display brightness. . . . . . . . . . . . . . . . . . . . . . . . . . . . . . . . . . . . . . . . . . . . . . . . . . . 55
10.5.4 Display update rate . . . . . . . . . . . . . . . . . . . . . . . . . . . . . . . . . . . . . . . . . . . . . . . . . . 55
10.5.5 Display layout . . . . . . . . . . . . . . . . . . . . . . . . . . . . . . . . . . . . . . . . . . . . . . . . . . . . . . 56
10.5.6 Display colour setting . . . . . . . . . . . . . . . . . . . . . . . . . . . . . . . . . . . . . . . . . . . . . . . . 56
10.6 Diagnostics . . . . . . . . . . . . . . . . . . . . . . . . . . . . . . . . . . . . . . . . . . . . . . . . . . . . . . . . . . . . 57
10.6.1 Read totaliser values. . . . . . . . . . . . . . . . . . . . . . . . . . . . . . . . . . . . . . . . . . . . . . . . . 58
10.6.2 Memory. . . . . . . . . . . . . . . . . . . . . . . . . . . . . . . . . . . . . . . . . . . . . . . . . . . . . . . . . . . 58
10.6.3 Operating hours counter . . . . . . . . . . . . . . . . . . . . . . . . . . . . . . . . . . . . . . . . . . . . . . 59
10.6.4 Internal temperature . . . . . . . . . . . . . . . . . . . . . . . . . . . . . . . . . . . . . . . . . . . . . . . . . 59
10.6.5 Operating status LED . . . . . . . . . . . . . . . . . . . . . . . . . . . . . . . . . . . . . . . . . . . . . . . . 60
10.6.6 Event history . . . . . . . . . . . . . . . . . . . . . . . . . . . . . . . . . . . . . . . . . . . . . . . . . . . . . . . 61
10.7 Service functions. . . . . . . . . . . . . . . . . . . . . . . . . . . . . . . . . . . . . . . . . . . . . . . . . . . . . . . . 61
10.7.1 Device information . . . . . . . . . . . . . . . . . . . . . . . . . . . . . . . . . . . . . . . . . . . . . . . . . . 61
10.7.2 Configuration. . . . . . . . . . . . . . . . . . . . . . . . . . . . . . . . . . . . . . . . . . . . . . . . . . . . . . . 62
10.7.3 Simulation . . . . . . . . . . . . . . . . . . . . . . . . . . . . . . . . . . . . . . . . . . . . . . . . . . . . . . . . . 62
10.7.4 Documents . . . . . . . . . . . . . . . . . . . . . . . . . . . . . . . . . . . . . . . . . . . . . . . . . . . . . . . . 63
10.7.5 Binary data transmission (BLOB) . . . . . . . . . . . . . . . . . . . . . . . . . . . . . . . . . . . . . . . 64
10.7.6 Optical localisation . . . . . . . . . . . . . . . . . . . . . . . . . . . . . . . . . . . . . . . . . . . . . . . . . . 64
10.7.7 Lock / unlock . . . . . . . . . . . . . . . . . . . . . . . . . . . . . . . . . . . . . . . . . . . . . . . . . . . . . . . 65
10.7.8 Guided installation (wizard) . . . . . . . . . . . . . . . . . . . . . . . . . . . . . . . . . . . . . . . . . . . . 65
11 Operation .................................................................. 67
12 Troubleshooting . . . . . . . . . . . . . . . . . . . . . . . . . . . . . . . . . . . . . . . . . . . . . . . . . . . . . . . . . . . . . 68
12.1 Warning messages . . . . . . . . . . . . . . . . . . . . . . . . . . . . . . . . . . . . . . . . . . . . . . . . . . . . . . 68
12.2 Error messages. . . . . . . . . . . . . . . . . . . . . . . . . . . . . . . . . . . . . . . . . . . . . . . . . . . . . . . . . 69
13 Maintenance, repair and disposal . . . . . . . . . . . . . . . . . . . . . . . . . . . . . . . . . . . . . . . . . . . . . . . . 70
13.1 Maintenance . . . . . . . . . . . . . . . . . . . . . . . . . . . . . . . . . . . . . . . . . . . . . . . . . . . . . . . . . . . 70
13.2 Replacing the display unit . . . . . . . . . . . . . . . . . . . . . . . . . . . . . . . . . . . . . . . . . . . . . . . . . 70
13.3 Disposal . . . . . . . . . . . . . . . . . . . . . . . . . . . . . . . . . . . . . . . . . . . . . . . . . . . . . . . . . . . . . . 71
14 Factory settings. . . . . . . . . . . . . . . . . . . . . . . . . . . . . . . . . . . . . . . . . . . . . . . . . . . . . . . . . . . . . . 72
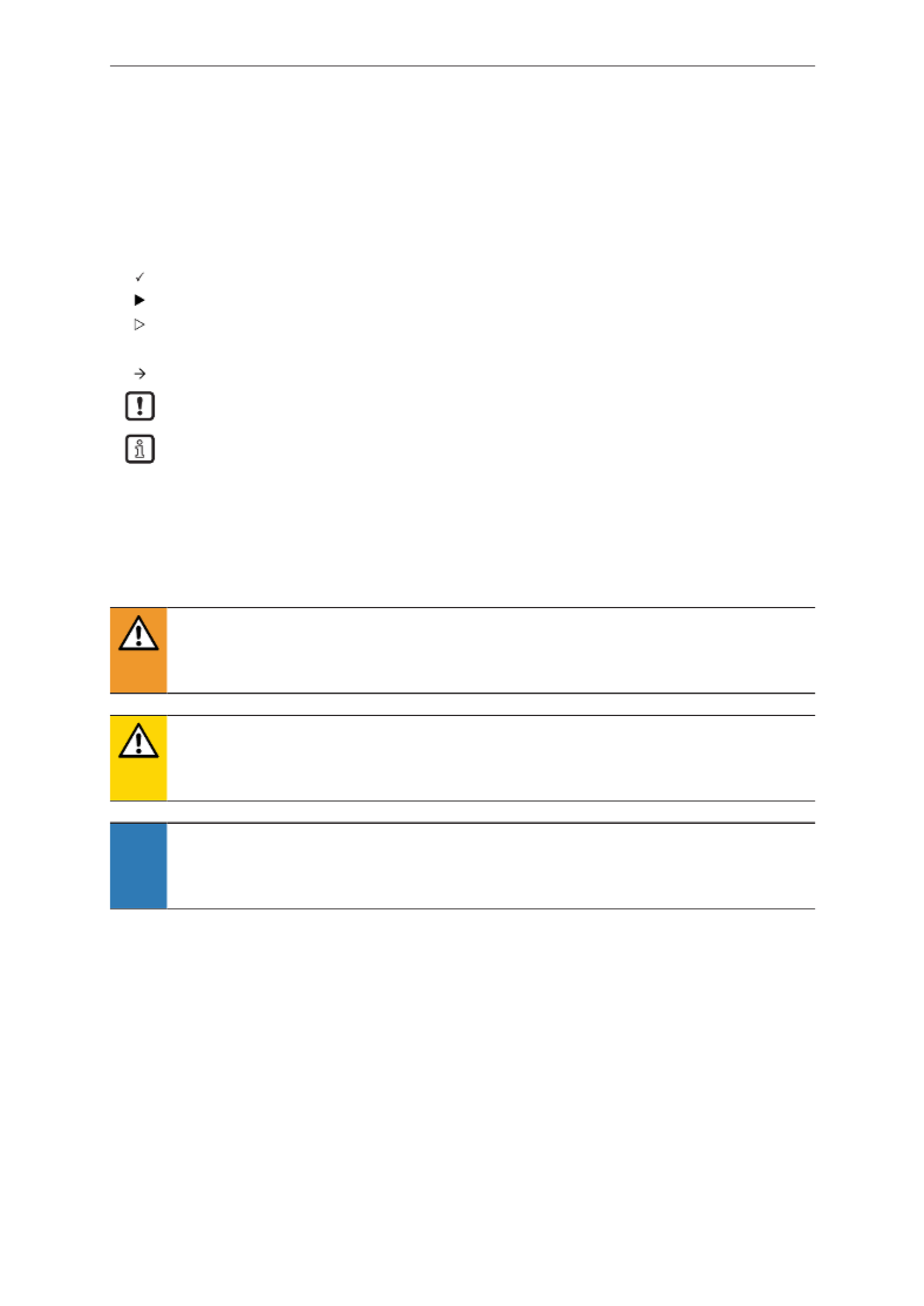
SMFxxx Magnetic-inductive flow meter
4
1 Preliminary note
You will find instructions, technical data, approvals and further information using the QR code on the
unit / packaging or at .
documentation.ifm.com
1.1 Symbols used
Requirement
Instructions
Reaction, result
[...] Designation of keys, buttons or indications
Cross-reference
Important note
Non-compliance may result in malfunction or interference.
Information
Supplementary note
1.2 Warnings
Warnings indicate the possibility of personal injury and damage to property. This enables safe product
handling. Warnings are graded as follows:
WARNING
Warning of serious personal injury
wIf the warning is not observed, fatal and serious injuries are possible.
CAUTION
Warning of minor to moderate personal injury
wIf the warning is not observed, minor to moderate injuries are possible.
ATTENTION
Warning of damage to property
wIf the warning is not observed, damage to property is possible.
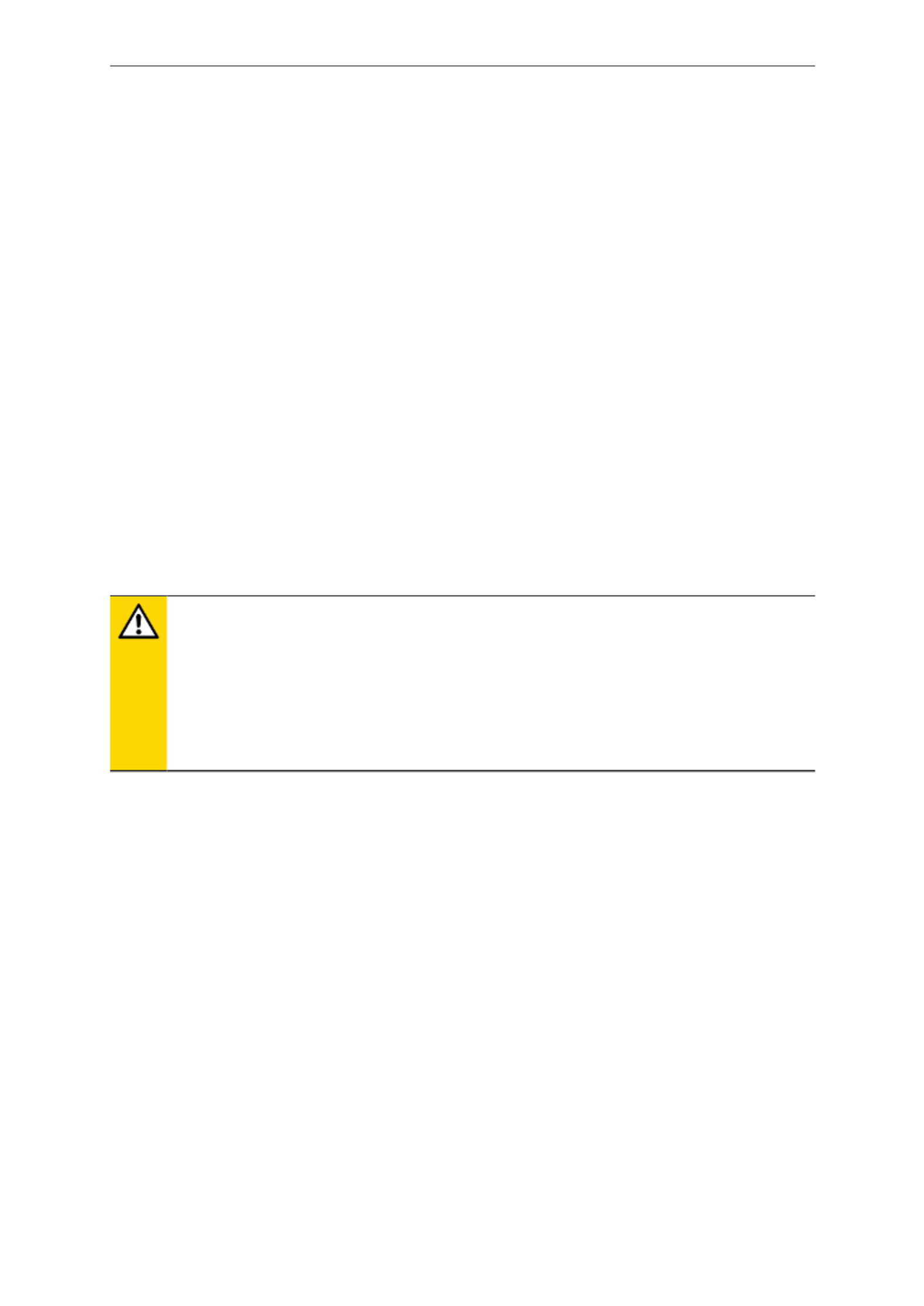
Magnetic-inductive flow meter SMFxxx
5
2 Safety instructions
• The unit described is a subcomponent for integration into a system.
– The system architect is responsible for the safety of the system.
– The system architect undertakes to perform a risk assessment and to create documentation in
accordance with legal and normative requirements to be provided to the operator and user of
the system. This documentation must contain all necessary information and safety instructions
for the operator, the user and, if applicable, for any service personnel authorised by the
architect of the system.
• Read this document before setting up the product and keep it during the entire service life.
• The product must be suitable for the corresponding applications and environmental conditions
without any restrictions.
• Only use the product for its intended purpose ( Intended use).Ò
• Only use the product for permissible media.
• If the operating instructions or the technical data are not adhered to, personal injury and/or damage
to property may occur.
• The manufacturer assumes no liability or warranty for any consequences caused by tampering with
the product or incorrect use by the operator.
• Installation, electrical connection, set-up, operation and maintenance of the product must be
carried out by qualified personnel authorised by the machine operator.
• Protect units and cables against damage.
CAUTION
Transport of heavy devices.
wPersonal injury or damage to devices is possible if heavy devices fall during
transportation.
uTransport the device to the assembly site in its original packaging.
uAfter unpackaging the device but leaving the protective caps in place, transport it using
the suitable tools (e.g. carrying straps).
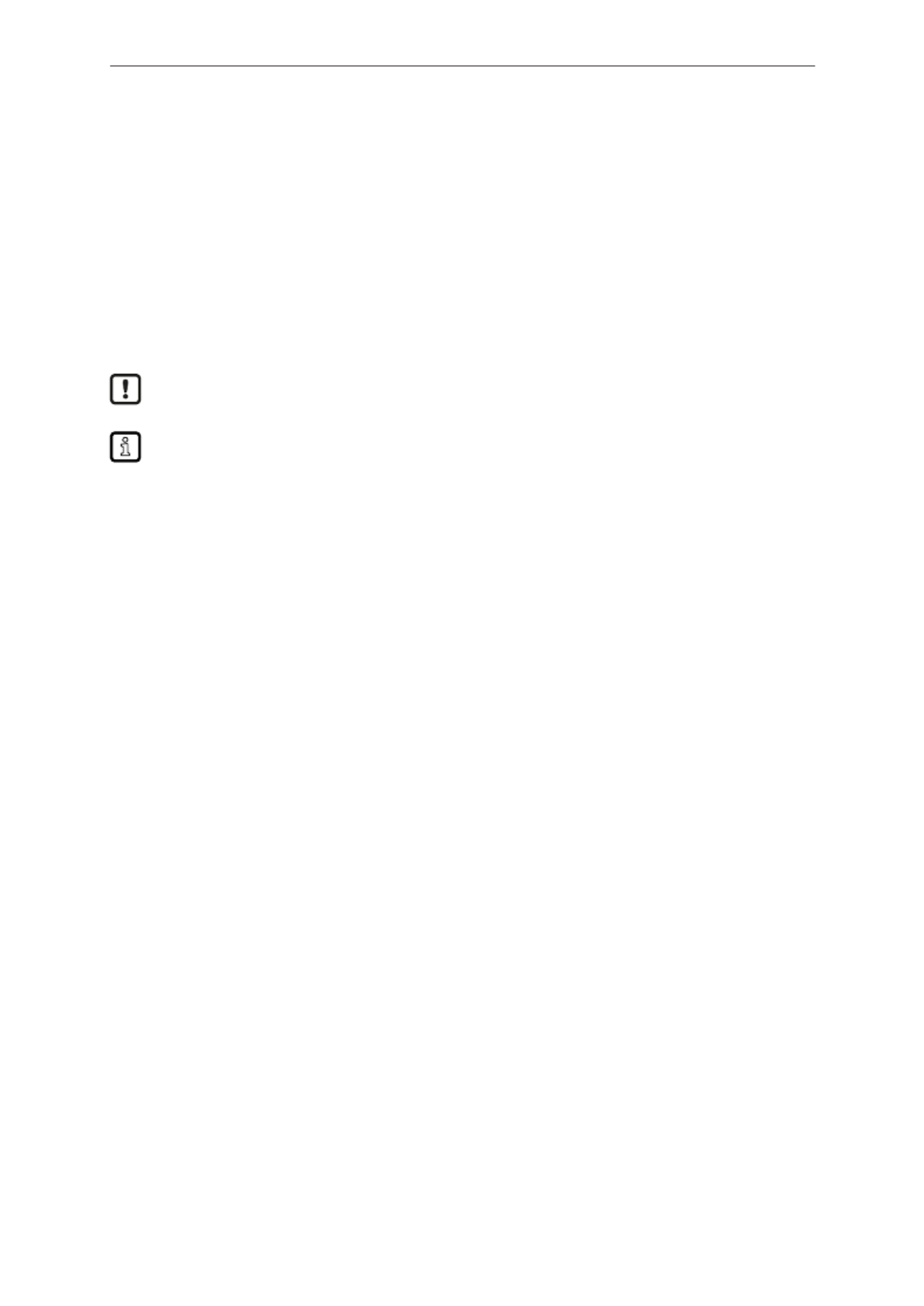
SMFxxx Magnetic-inductive flow meter
6
3 Intended use
The unit monitors liquid media.
The device measures the flow velocity, the volume flow (consumed quantity / time), the consumed
quantity, the medium temperature and the conductivity.
3.1 Application area
Use in hygienic areas for conductive fluids with the following properties:
• Water with conductivity of ≥20 µS/cm
• Other fluids with conductivity of ≥5 µS/cm
This is a class A product. This product may cause radio interference in domestic areas.
uIf required, take appropriate EMC screening measures.
Pressure Equipment Directive (PED):
The units comply with the Pressure Equipment Directive and are designed and manufactured
for group 2 fluids in accordance with the sound engineering practice. Use of media from group 1
fluids on request.
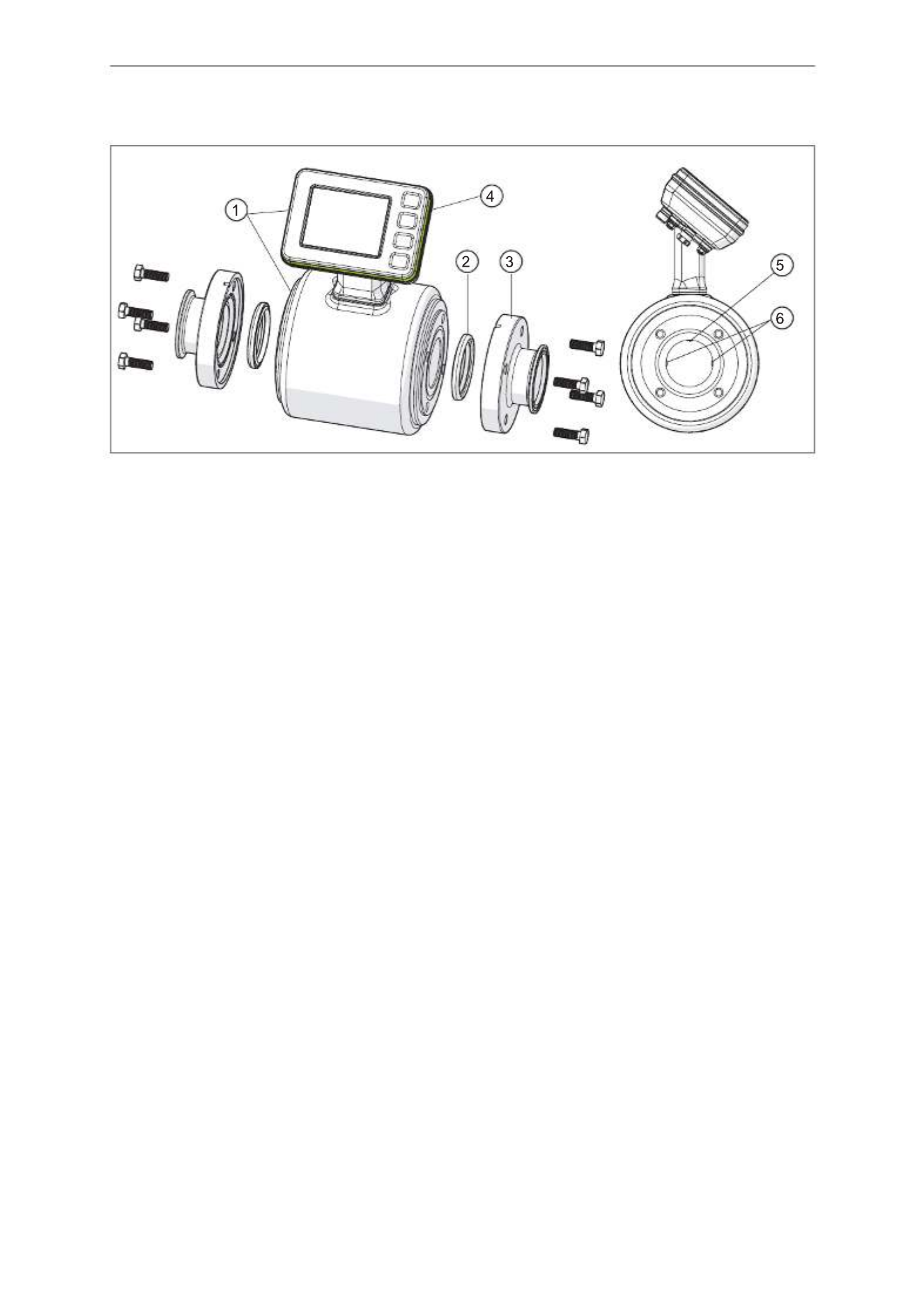
Magnetic-inductive flow meter SMFxxx
7
4 Function
Fig.1: Product description
1: SMFxxx device (measuring circuit and display)
2: Exxxxx seal, can be ordered separately from www.ifm.com
3: Exxxxx process adapter, can be ordered separately from www.ifm.com
4: Operating status LED (LED ring)
5: Temperature-measuring electrode in the measuring pipe
6: Flow-measuring electrodes in the measuring pipe
Operating principle:
• The device detects the volumetric flow on the magnetic-inductive volumetric flow measuring
principle.
• As additional process values the device measures the temperature of the medium.
• The unit displays the current process values.
• The unit can be operated in SIO mode (standard input-output ) or in IO-Link mode.
• The device indicates all self-diagnostic options through the colour signals of an operating status
LED.
• A simulation mode and guided installation via a wizard enable simplified set-up of the sensor.
• The device has the following output functions:
– :
Analogue signal ( 33)Ò/
flow, temperature, conductivity
– :
Consumed quantity monitoring (totaliser function) ( 37)Ò/
switching signal or pulse signal
– :
Switching signal diagnostics ( 35)Ò/
direction of flow, fluid detection
– :
Digital switching signal ( 39)Ò/
limit value monitoring of flow, temperature, conductivity, totaliser
• In addition, the device provides other diagnostic and service functions:
–Read totaliser values ( 58)Ò/
–Memory ( 58)Ò/
–Operating hours counter ( 59)Ò/
–Internal temperature ( 59)Ò/
–Operating status LED ( 60)Ò/
–Event history ( 61)Ò/
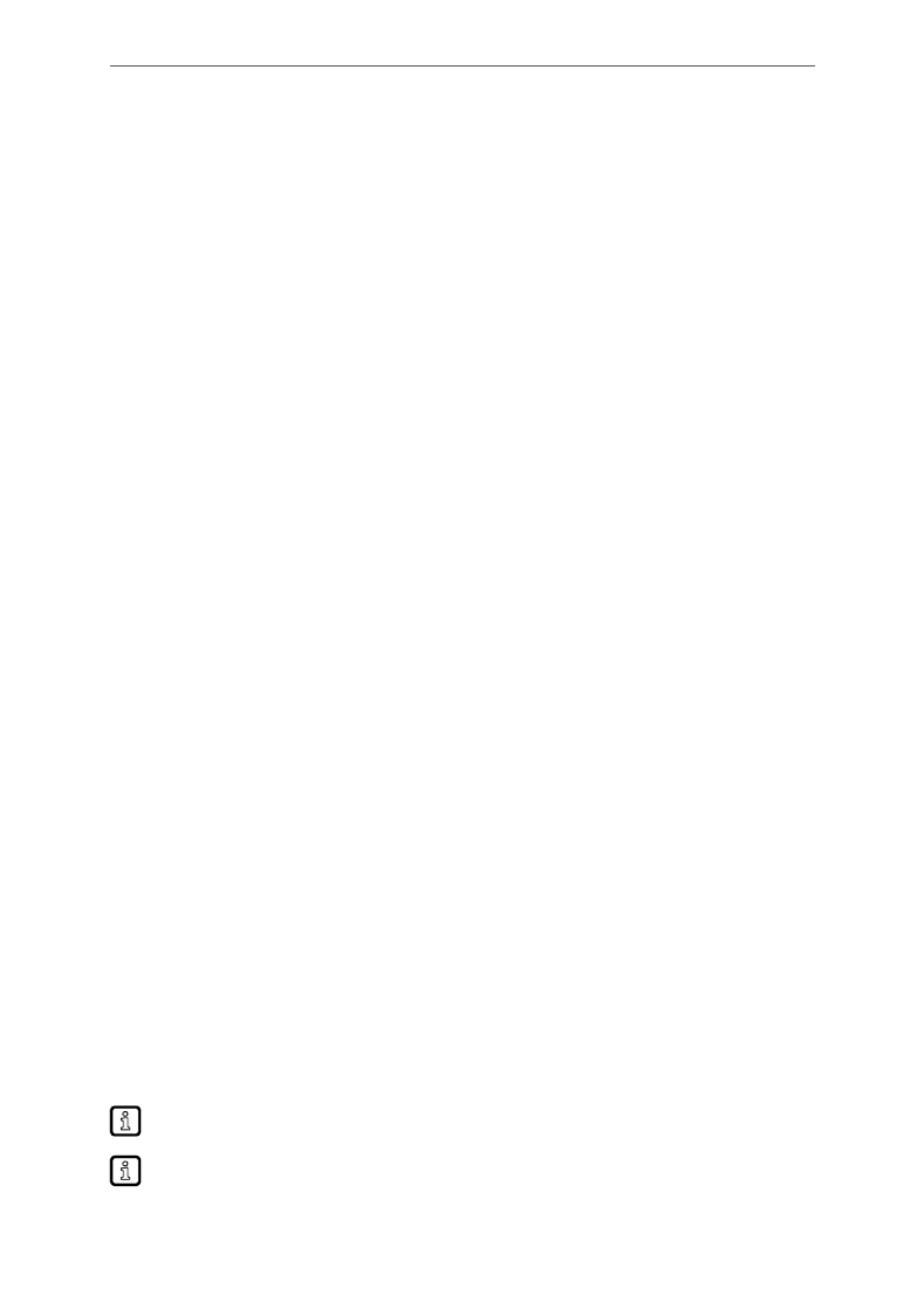
SMFxxx Magnetic-inductive flow meter
8
–Device information ( 61)Ò/
–Simulation ( 62)Ò/
–Configuration ( 62)Ò/
–Documents ( 63)Ò/
–Binary data transmission (BLOB) ( 64)Ò/
–Optical localisation ( 64)Ò/
–Lock / unlock ( 65)Ò/
–Reset the device ( 53)Ò/
–Display settings ( 54)Ò/
– , e.g. standard unit of measurement, measured valueApplication configuration ( 42)Ò/
damping, output polarity, low flow cut-off, calibration.
4.1 Output OUT1 selection options
• Pulse signal totaliser
• Switching signal totaliser
• Switching signal diagnosis
– Direction of flow
– Fluid detection
• IO-Link
• OFF (output switched to high impedance)
4.2 Output OUT2 selection options
• Pulse signal totaliser
• Switching signal totaliser
• Analogue signal flow
• Analogue signal temperature
• Analogue signal for conductivity
• Switching signal diagnosis
– Direction of flow
– Fluid detection
• Input for external totaliser reset
• OFF (output switched to high impedance)
4.3 IO-Link
IO-Link is a communication system for connecting intelligent sensors and actuators to automation
systems. IO-Link is standardised in the IEC 61131-9 standard.
General information on IO-Link at io-link.ifm
Input Output Device Description (IODD) with all parameters, process data and detailed
descriptions of the device at documentation.ifm.com
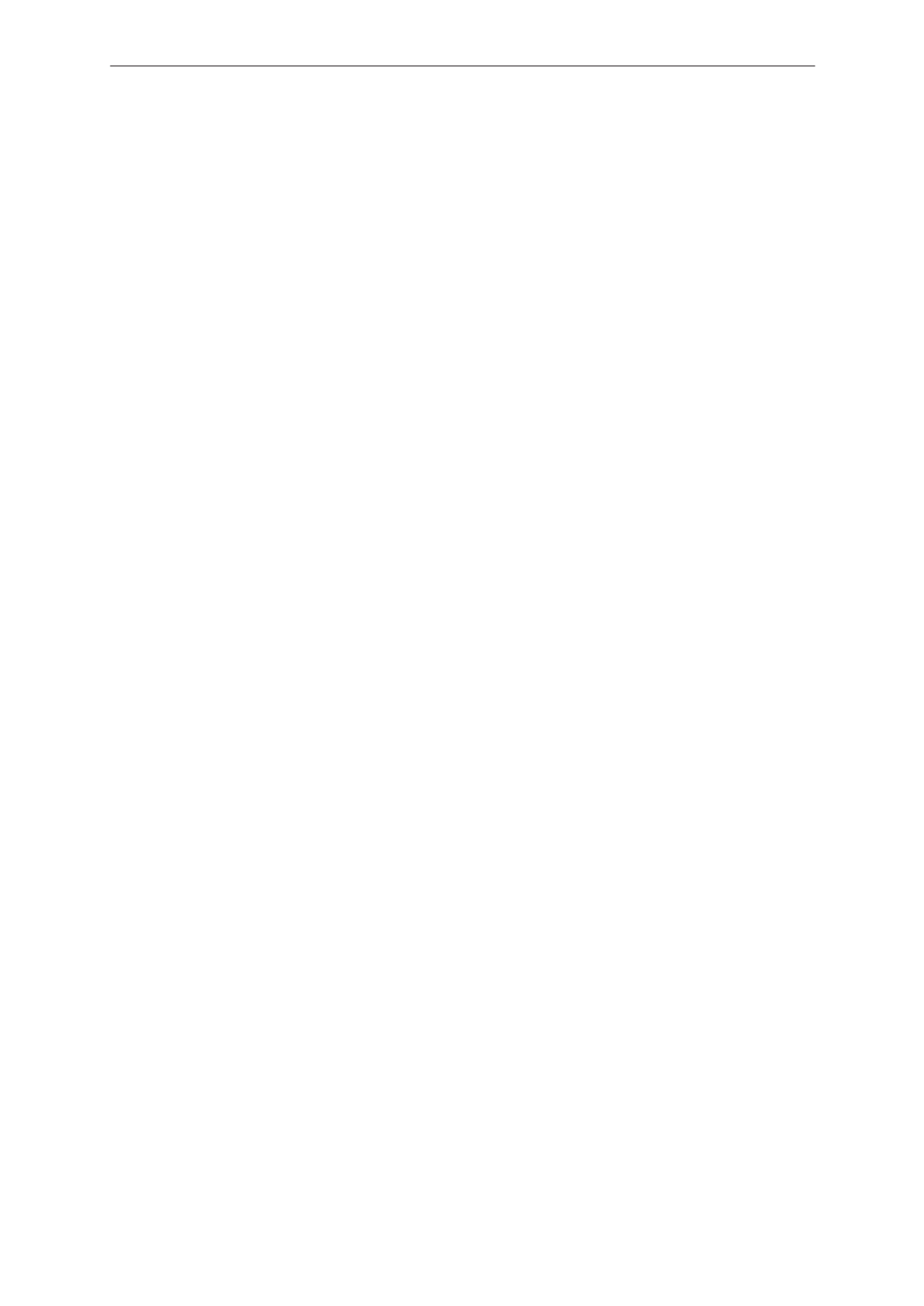
Magnetic-inductive flow meter SMFxxx
9
IO-Link offers the following advantages:
• Interference-free transmission of all data and process values
• Parameter setting in the running process or presetting outside the application
• Parameters for identifying the connected devices in the system
• Additional parameters and diagnostic functions
• Automatic backup and restore of parameter sets in case of device replacement (data storage)
• Logging of parameter sets, process values and events
• Device description file (IODD - Input Output Device Description) for easy project planning
• Standardised electrical connection
• Remote maintenance
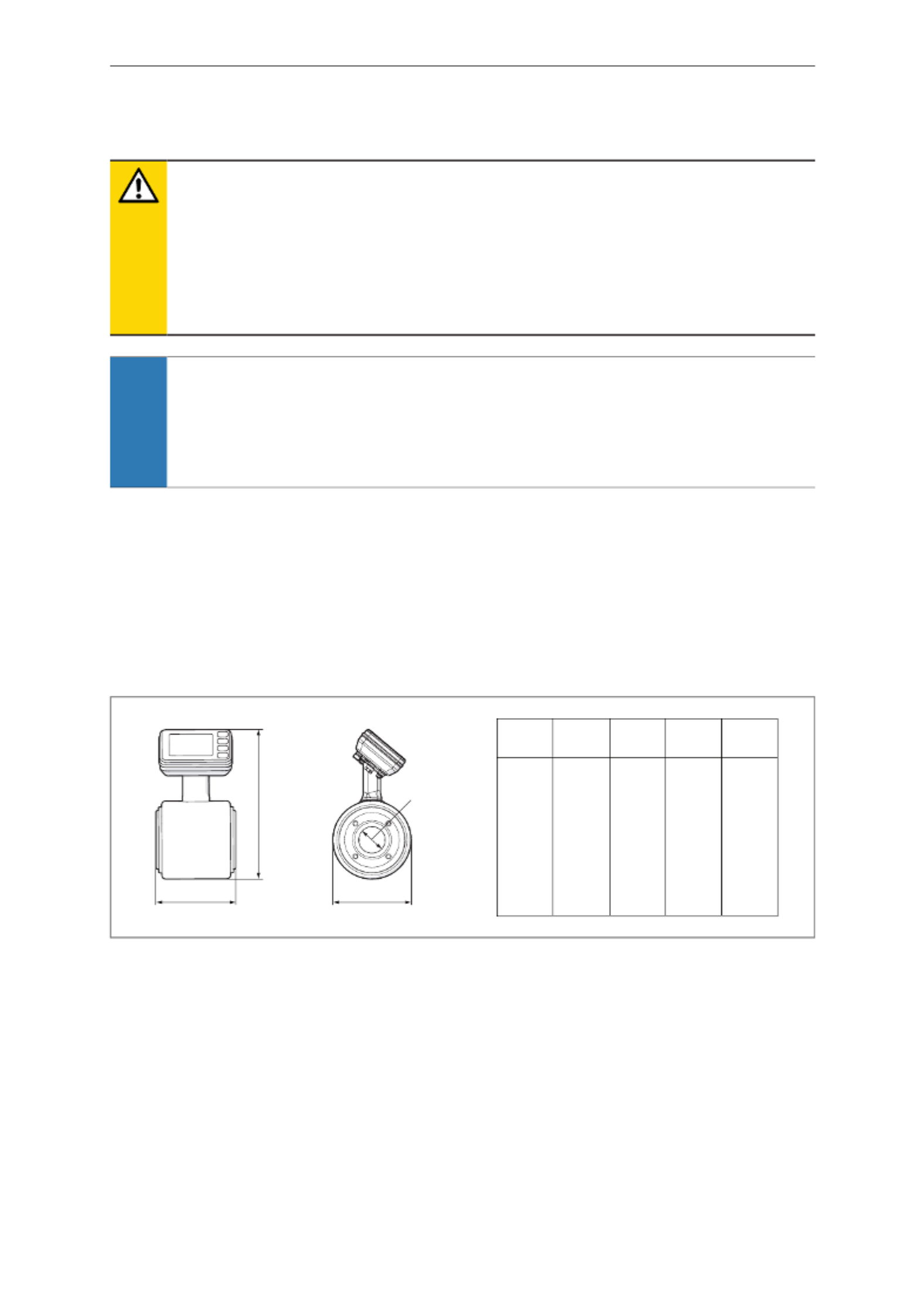
SMFxxx Magnetic-inductive flow meter
10
5 Mounting
CAUTION
If the medium temperature is above 50 °C (122 °F), parts of the housing can increase in
temperature to over 65 °C (149 °F).
wRisk of burns.
uProtect the housing against contact with flammable substances and unintentional
contact.
uApply the supplied warning label to the sensor cable.
ATTENTION
No functional earthing when installed in an ungrounded pipe system (e.g. plastic pipes).
wReduction in measurement accuracy or damage to the device.
uAttach the grounding clamp to the ground connection and establish an equalisation of
potential between the medium and the device ( Electrical connection).Ò
uMake sure that no pressure is applied to the system.
uEnsure that no media can leak at the mounting location during installation.
uAvoid deposits, accumulated gas and air in the pipe system.
After installation, air bubbles in the system can affect the measurement. Corrective measures:
uAfter installation, rinse the system for ventilation.
5.1 Device dimensions
G
L H
diA
DN
[mm] [mm] [mm] [mm] [mm]
40
50
65
80
100
140
140
140
140
140
252.6
267.5
281.6
295.9
319.6
125
139.7
154
168.3
192
34.3
47
59.7
72.4
96.9
L G H diA
Fig.2: Dimensions of the sensors depending on the design (nominal width DN)
5.2 Installation position
uInstall the unit so that the measuring pipe is always completely filled.
uInstall in front of or in a rising pipe.
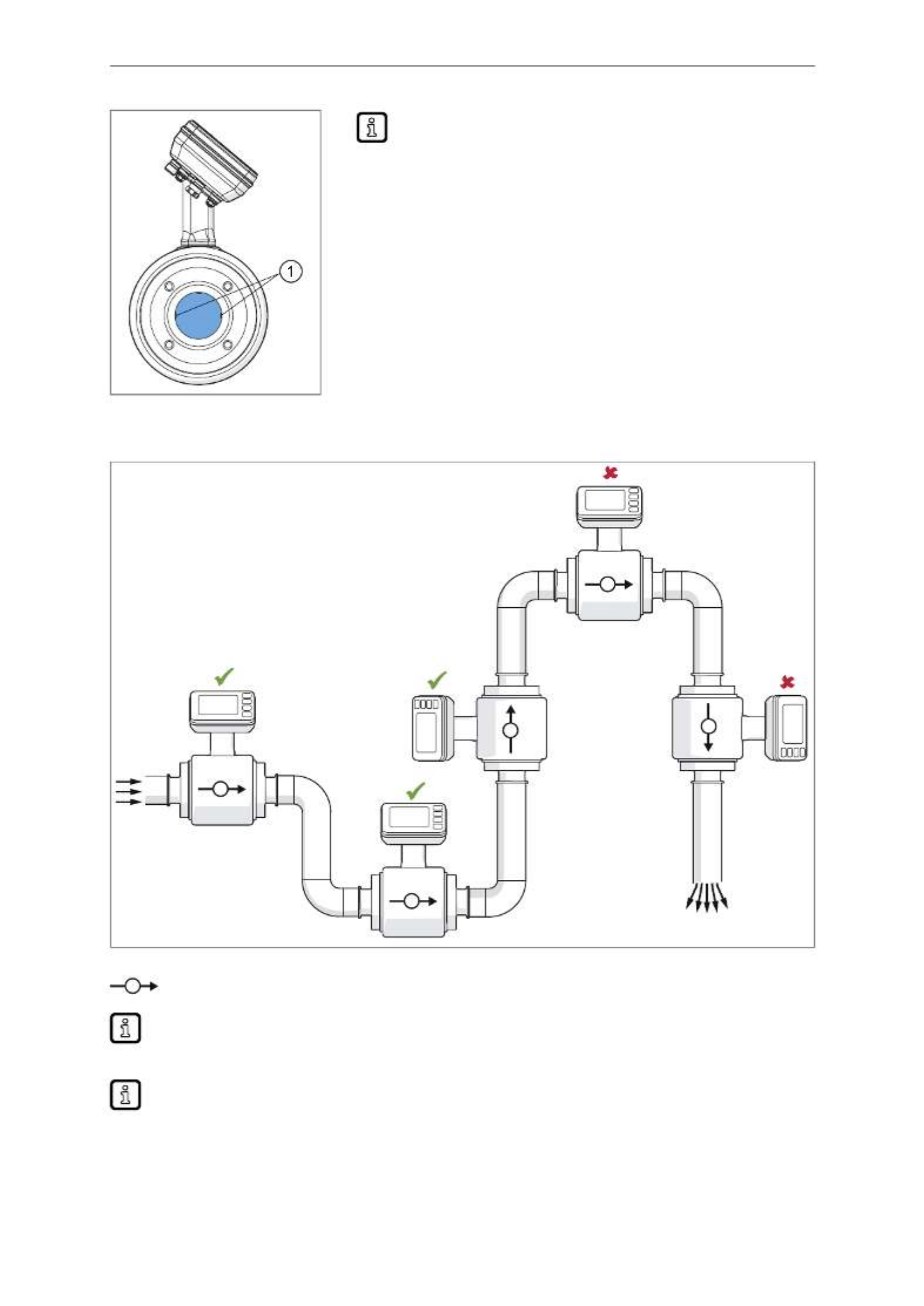
Magnetic-inductive flow meter SMFxxx
11
Fig.3: Orientation of the flow-
measuring electrodes
When installed in a vertical position, the electrodes for flow
measurement (1) should be in the same plane. Any
deviation from this can lead to measurement inaccuracies.
F
F
F
F
F
Fig.4: Recommended and non-recommended installation positions
F
Flow direction ( 45)Ò/
The unit can be installed independently of the orientation if the following is ensured:
- No air bubbles can form in the pipe system.
- The pipes are always completely filled.
In case of horizontal installation: as a result of design requirements a small quantity of the
medium always remains in the measuring channel after switching off the pump.
uEnsure that no medium remains in the measuring channel.
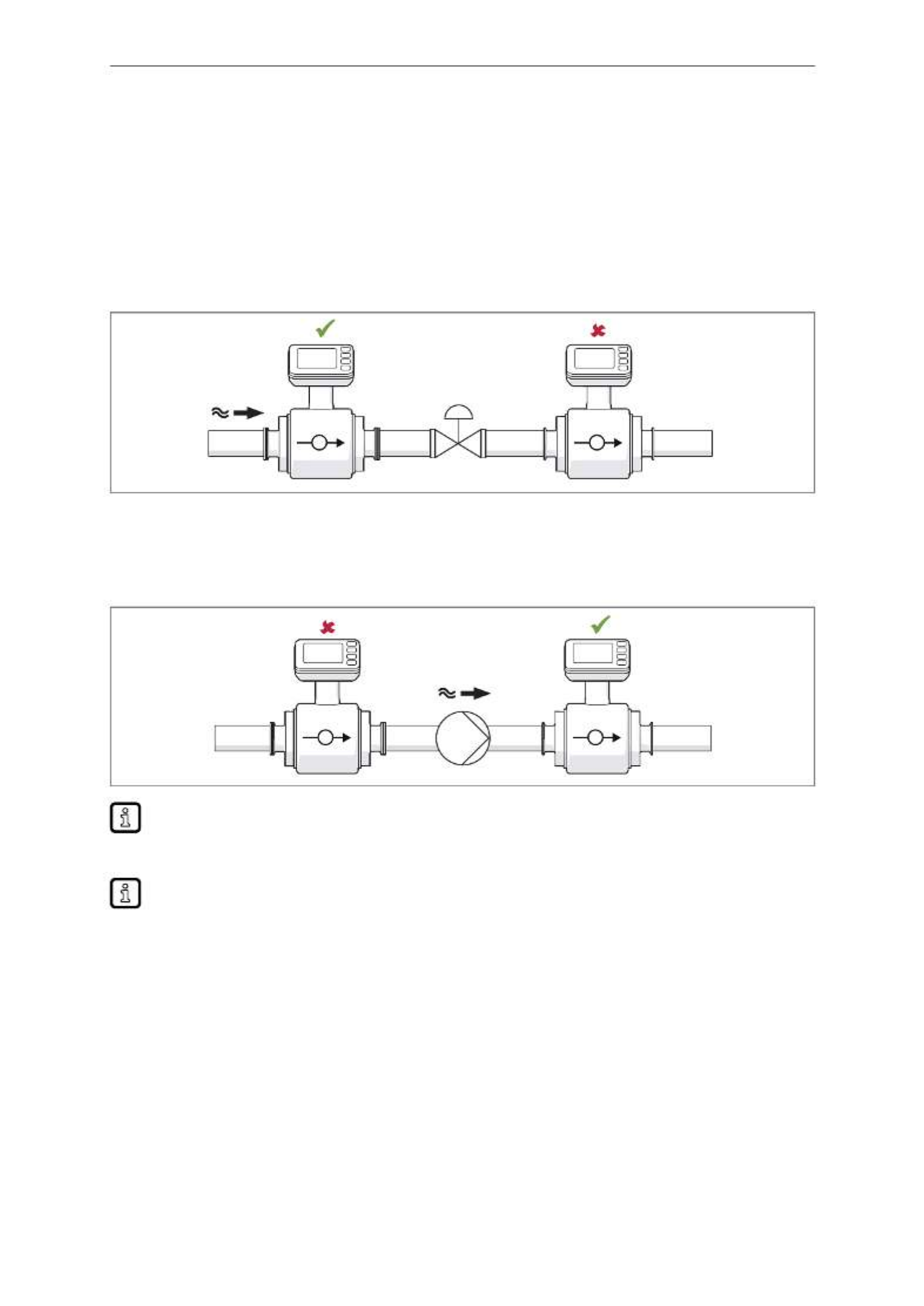
SMFxxx Magnetic-inductive flow meter
12
Avoid the following installation positions:
• At the highest point of the pipe system.
• Directly upstream of a free pipe spout in a downpipe
• On the suction side of a pump.
Installation in the vicinity of control valves:
uInstall the device upstream of the control valve in the direction of flow:
F F
Installation in the vicinity of pumps:
uInstall the device downstream of the pump in the direction of flow to avoid negative pressure in the
measuring pipe:
F F
When installed upstream of a pump, cavitation may occur if the pump is under low pressure or
high vacuum conditions.
wThis can lead to the sensor being damaged.
When using piston pumps, piston diaphragm pumps or peristaltic pumps:
uInstall pulsation damper.
Installation with very strong vibrations:
uSupport and secure the device and the pipe:
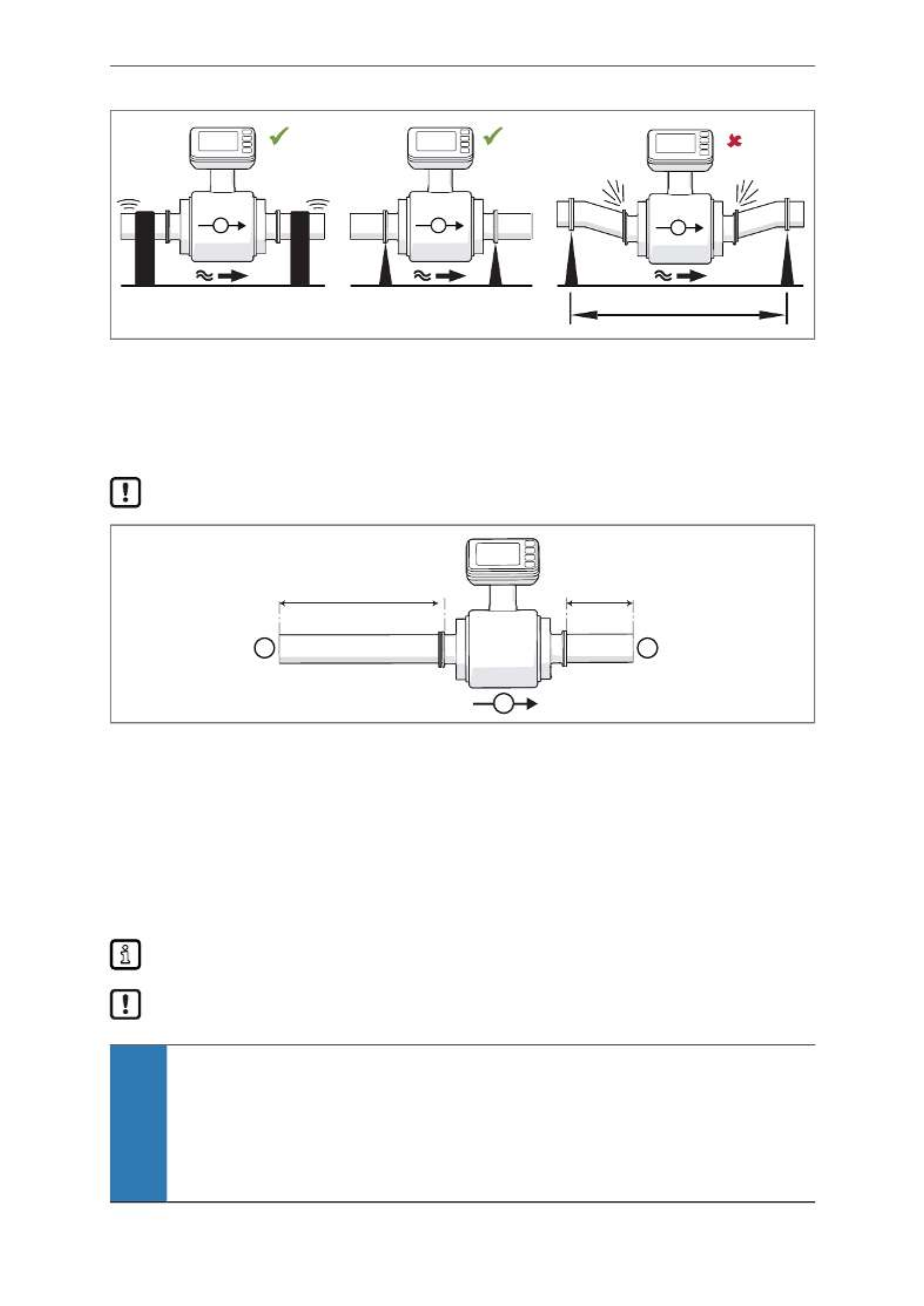
Magnetic-inductive flow meter SMFxxx
13
L > 10 m
F F F
5.3 Inlet and outlet pipe lengths
Structures in the pipe, bends, valves, reducing pieces and the like affect the function of the unit.
uAdhere to the distances between sensor and interference.
Shut-off valves and control devices are not allowed directly in front of the unit.
F
S S
>2 x DN>5 x DN
Fig.5: Inlet and outlet pipe lengths
DN: Nominal width of the sensor
S: Interference
5.4 Process connection
Using process adapters the unit can be adapted to different process connections.
ifm offers hygienic process adapters and seals made of the materials FKM, EPDM and VMQ, which
must be ordered separately as accessories.
Information about available accessories at .
documentation.ifm.com
uAdhere to the installation instructions for use in hygienic areas.
ATTENTION
Sensitive sealing areas on the flange of the process adapters.
wThe PFA material on the flange can be easily damaged after removing the protective
caps, which can lead to leaks in the process connection.
uCarefully remove the protective caps.
uAvoid any impact on or scratching of the PFA sealing area.
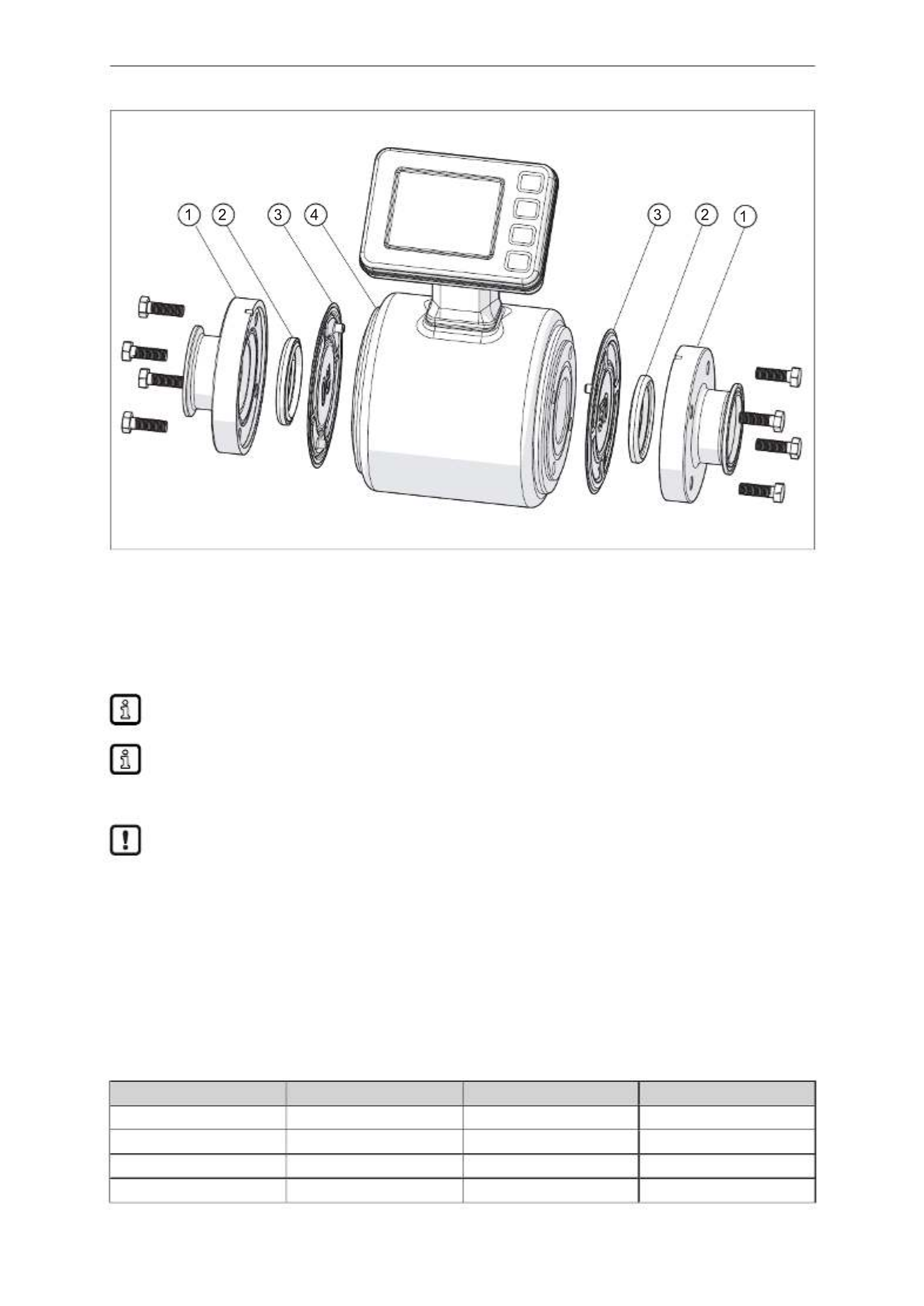
SMFxxx Magnetic-inductive flow meter
14
Fig.6: Installation of the device in the process
1: Process adapters
2: Seal
3: Protective cap
4: Sensor
Procedure:
The sensor, the process adapters and the seals must be ordered separately.
Additional instructions for the respective process adapters are described in the following
chapters.
uRemove the seal that fixes the protective caps to the sensor.
No replacement is possible after the product seal has been removed.
uCarefully remove the protective caps from the sensor.
uInsert the seals carefully into the grooves of the process adapters. Ensure that the seals are clean,
undamaged and correctly centred.
uFasten the process adapters to the device hand-tight using the enclosed screws.
uTighten the screw heads evenly in three steps and observe the maximum tightening torque:
• Step 1 approx. 50% of the specified maximum tightening torque.
• Step 2: approx. 80% of the specified maximum tightening torque.
• Step 3: 100% of the specified maximum tightening torque.
Nominal width Pressure rating screws Maximum tightening torque
DN 40 PN40 4xM8 16 Nm
DN 50 PN25 4xM8 16 Nm
DN 65 PN25 6xM8 16 Nm
DN 80 PN25 6xM8 16 Nm

Magnetic-inductive flow meter SMFxxx
15
Nominal width Pressure rating screws Maximum tightening torque
DN 100 PN25 6xM8 16 Nm
Tab.1: Maximum tightening torque
uConnect the device with the mounted process adapters to the pipe on both sides in the marked
direction of flow.
5.4.1 Clamp adapters
EL
Fig.7: Installation with clamp adapter
EL = Installation length of sensor + adapter see tableÒ
ifm electronic offers clamp adapters in compliance with ISO 2852 and DIN 32676-A for various pipe
standards:
Design Nominal width ifm adapters
available
Installation
length Applicable pipe standard
ISO 2852 EL = ISO 2037 DIN EN 10357
series D
BS 4825 part 1
SMF32x DN40 220 mm
SMF42x DN50 220 mm
SMF52x DN65 220 mm
SMF62x DN80 220 mm
SMF72x DN100 220 mm
Tab.2: Clamp ISO 2852
Design Nominal
width
ifm adapters
available
Installation
length Applicable pipe standard
DIN 32676-A EL = DIN EN
10357 series
A
DIN 11850
series 2
DIN 11866
series A
DIN 11850
series 1
SMF32x DN40 220 mm
SMF42x DN50 220 mm
SMF52x DN65 220 mm
SMF62x DN80 220 mm
SMF72x DN100 220 mm
Tab.3: Clamp DIN 32676-A
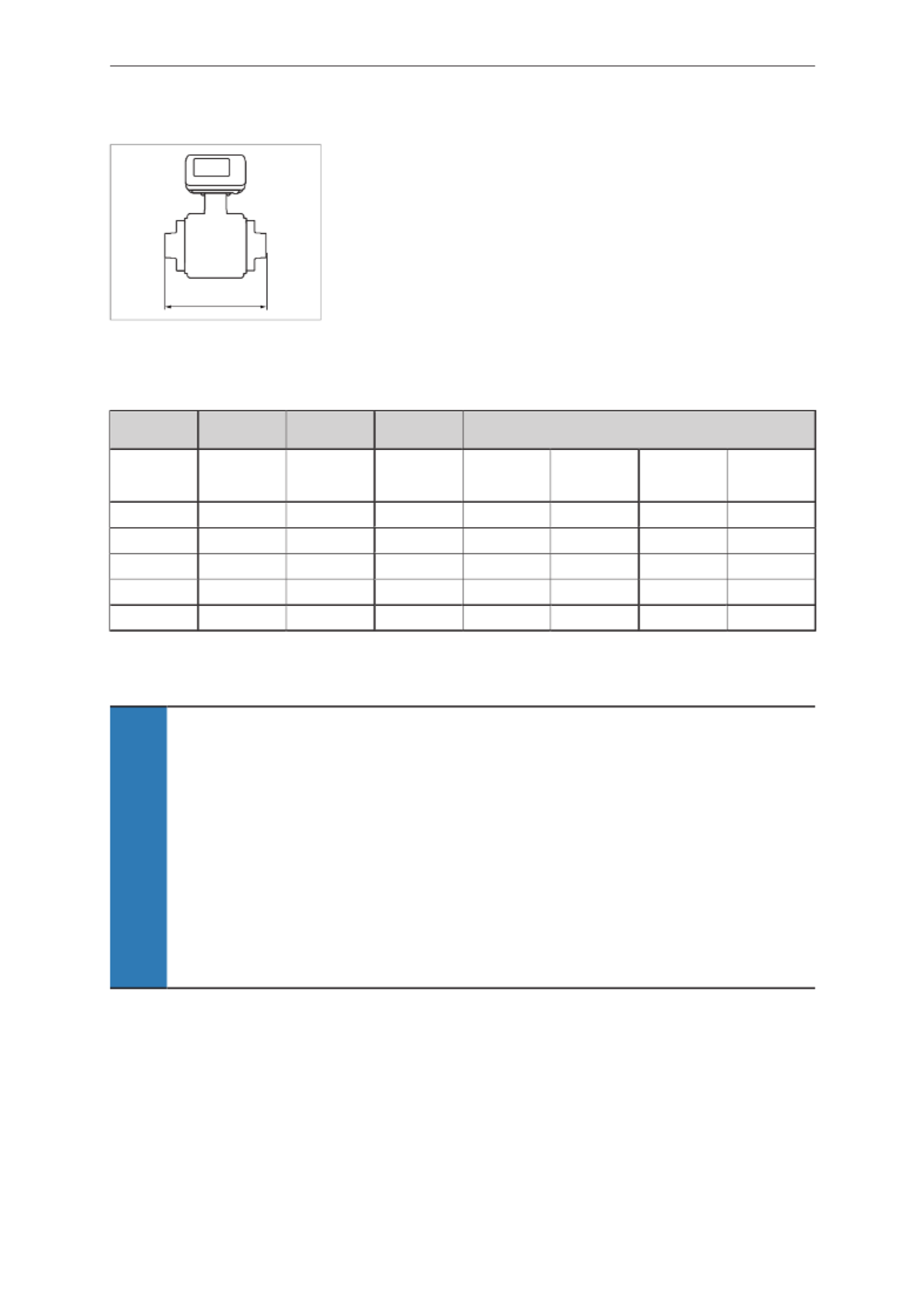
SMFxxx Magnetic-inductive flow meter
16
5.4.2 Welding adapter
EL
Fig.8: Installation with welding
adapter
EL = Installation length of sensor + adapter see tableÒ
ifm electronic offers welding adapters in compliance with EN10357 series A for various pipe
standards:
Design Nominal
width
ifm adapters
available
Installation
length Applicable pipe standard
EN 10357
series A
EL = DIN EN
10357 series
A
DIN 11850
series 2
DIN 11866
series A
DIN 11850
series 1
SMF32x DN40 220 mm
SMF42x DN50 220 mm
SMF52x DN65 220 mm
SMF62x DN80 220 mm
SMF72x DN100 220 mm
Tab.4: Welding adapters
Procedure:
ATTENTION
Welding work
wDestruction of the measuring electronics due to improper welding.
uThe welding must only be carried out by qualified personnel according to the state of the
art.
uPrepare the pipe ends carefully. The surfaces must be free from any contamination.
uThe welding materials must be suitable for the adapter and pipe.
uThe welds should be executed in such a way that the pipe and adapter do not warp
during welding.
uOnly install the device after the welding and subsequent cooling phase.
uDo not ground the welding system via the device.
uCarefully remove the protective caps from the sensor.
uFasten the process adapters to the device hand-tight using the enclosed screws.
uInsert the device with the pre-mounted process adapters into the pipe and weld the adapters to the
pipe with sufficient adhesive force using several welding spots.
uDisconnect the device from the process adapters by loosening the screws and carefully remove the
device.
uCarefully replace the protective caps on the two sensor connectors.
uNow weld the two process adapters firmly to the pipe.
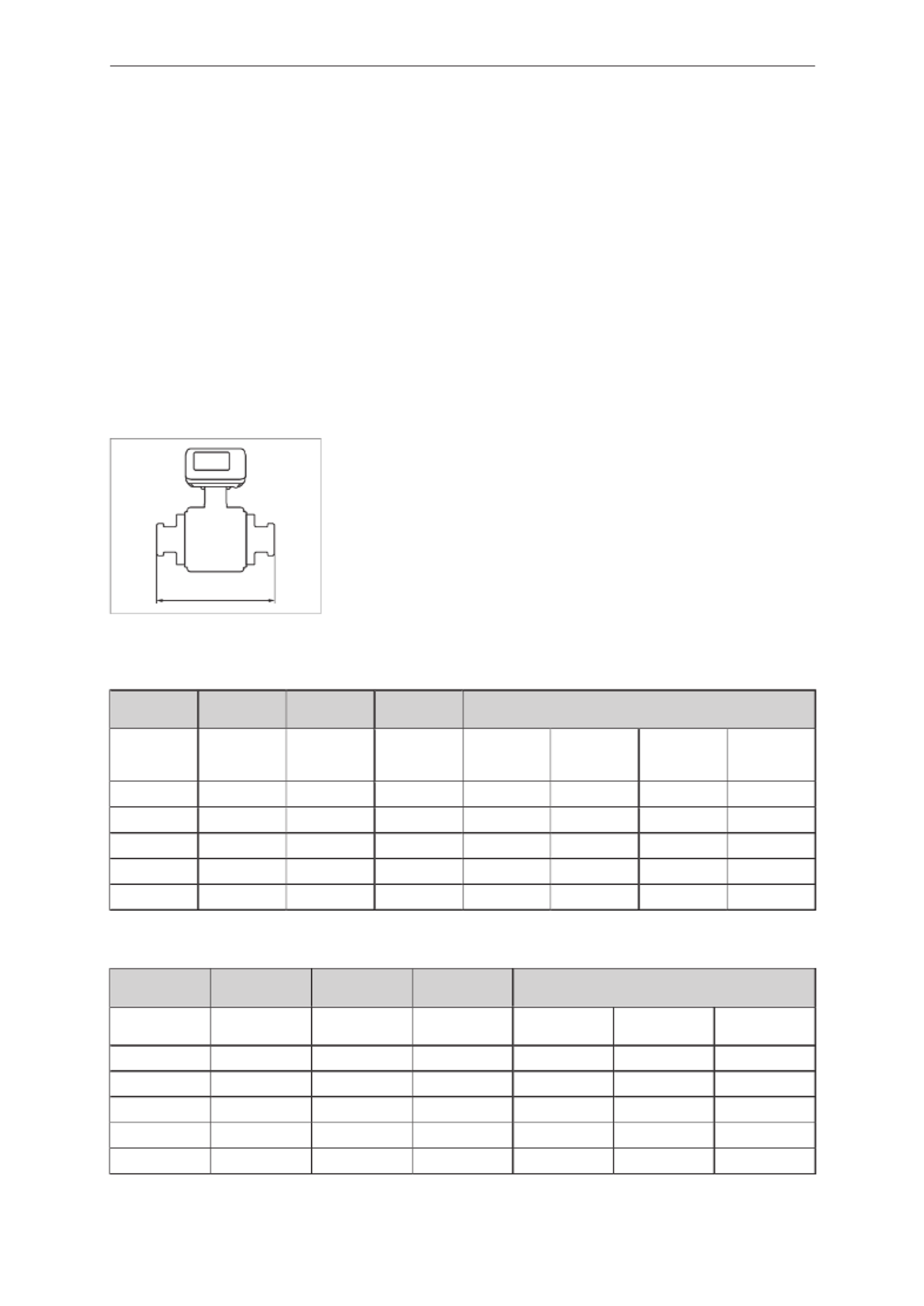
Magnetic-inductive flow meter SMFxxx
17
uEnsure sufficient intervals between the individual welding operations to avoid excessive heat
penetration or warping of the adapter due to overheating.
uLet the adapters and the pipe cool down.
uClean welding residue from the adapters, pipe and weld seams.
uCarefully remove the protective caps from the sensor.
uInsert the seals carefully into the grooves of the process adapters. Ensure that the seals are clean,
undamaged and correctly centred.
uPosition the device in the marked direction of flow between the two process adapters.
uFasten the process adapters to the device hand-tight using the enclosed screws.
uTighten the screw heads in three steps with the maximum tightening torque ( ProcessÒ
connection 14)/.
5.4.3 Screw adapter
EL
Fig.9: Installation with screw adapter
EL = Installation length of sensor + adapter see tableÒ
ifm electronic offers screw adapters in compliance with DIN11851 (pipe fitting) and SMS1145 for
various pipe standards:
Design Nominal
width
ifm adapters
available
Installation
length Applicable pipe standard
DIN11851 EL = DIN EN
10357 series
A
DIN 11850
series 2
DIN 11866
series A
DIN 11850
series 1
SMF32x DN40 260 mm
SMF42x DN50 260 mm
SMF52x DN65 270 mm
SMF62x DN80 280 mm
SMF72x DN100 290 mm
Tab.5: Screw connection DIN 11851 (pipe fitting)
Design Nominal width ifm adapters
available
Installation
length Applicable pipe standard
SMS 1145 EL = ISO 2037 DIN EN 10357
series D
BS 4825 part 1
SMF32x DN40 256 mm
SMF42x DN50 256 mm
SMF52x DN65 266 mm
SMF62x DN80 276 mm
SMF72x DN100 286 mm
Tab.6: Screw connection SMS 1145
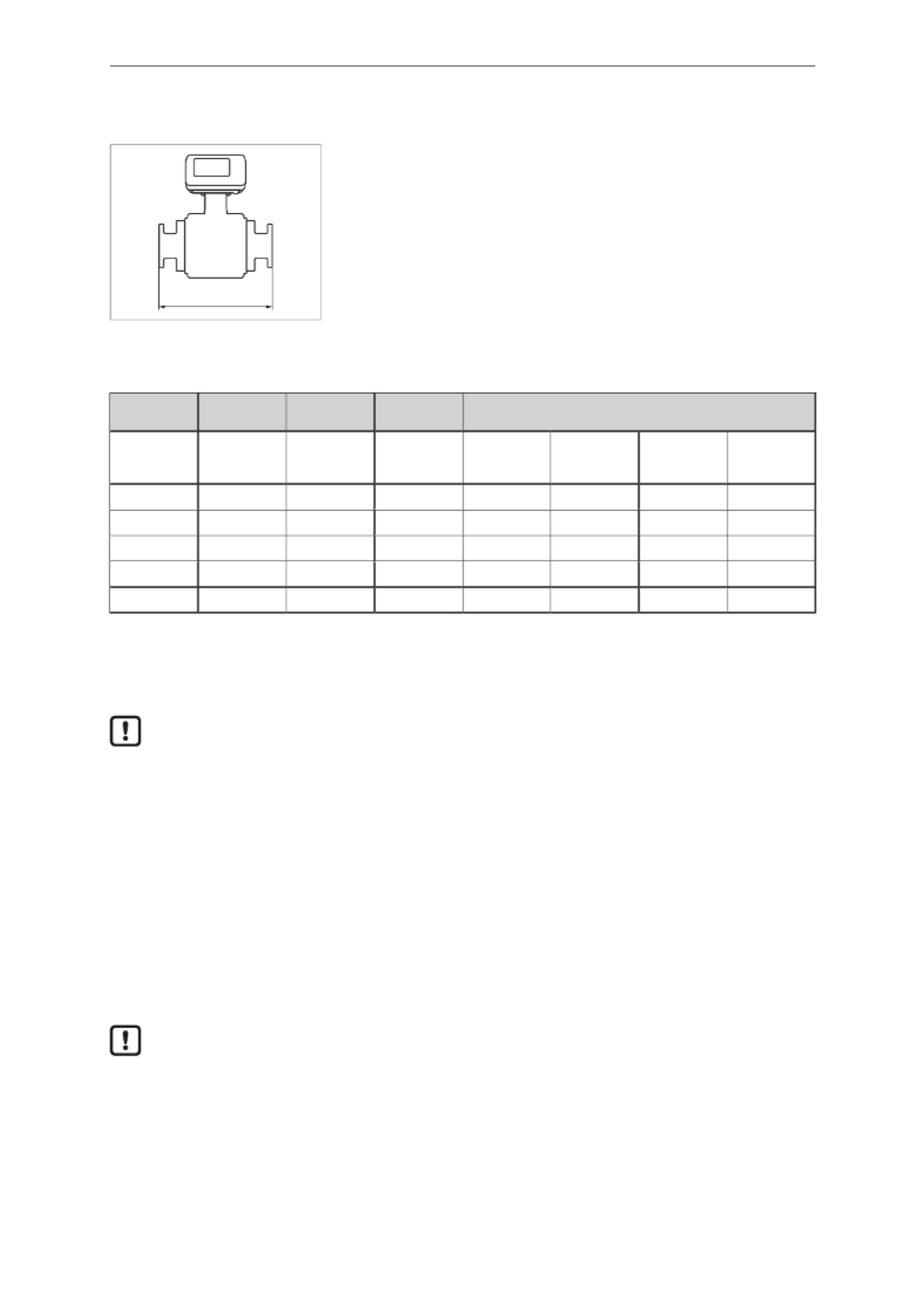
SMFxxx Magnetic-inductive flow meter
18
5.4.4 Flange adapter
EL
Fig.10: Installation with flange
adapter
EL = Installation length of sensor + adapter see tableÒ
ifm electronic offers aseptic flange adapters in compliance with DIN11864-2A:
Design Nominal
width
ifm adapters
available
Installation
length Applicable pipe standard
DIN11864-2
A
EL = DIN EN
10357 series
A
DIN 11850
series 2
DIN 11866
series A
DIN 11850
series 1
SMF32x DN40 246 mm
SMF42x DN50 246 mm
SMF52x DN65 246 mm
SMF62x DN80 270 mm
SMF72x DN100 278 mm
Tab.7: Aseptic flange adapter DIN11864-2A
5.5 Use in hygienic areas
The sensor is suited for CIP (cleaning in process) and SIP (sterilisation in place) when installed
correctly.
uObserve the application limits (temperature and material resistance) according to the data
sheet.
uInstall the device so that there is a minimum gradient in the measuring channel and no medium
remains in the pipe after switching off the pump.
uUse self-draining installation.
5.6 Use in hygienic areas according to 3-A
uEnsure that the installation of the unit in the system complies with 3-A guidelines.
u ÒUse only process adapters and seals with 3-A certification and marked with the 3-A symbol (
Accessories at ).
www.ifm.com
uFor use according to 3-A, take note of the corresponding regulations for cleaning and
maintenance.
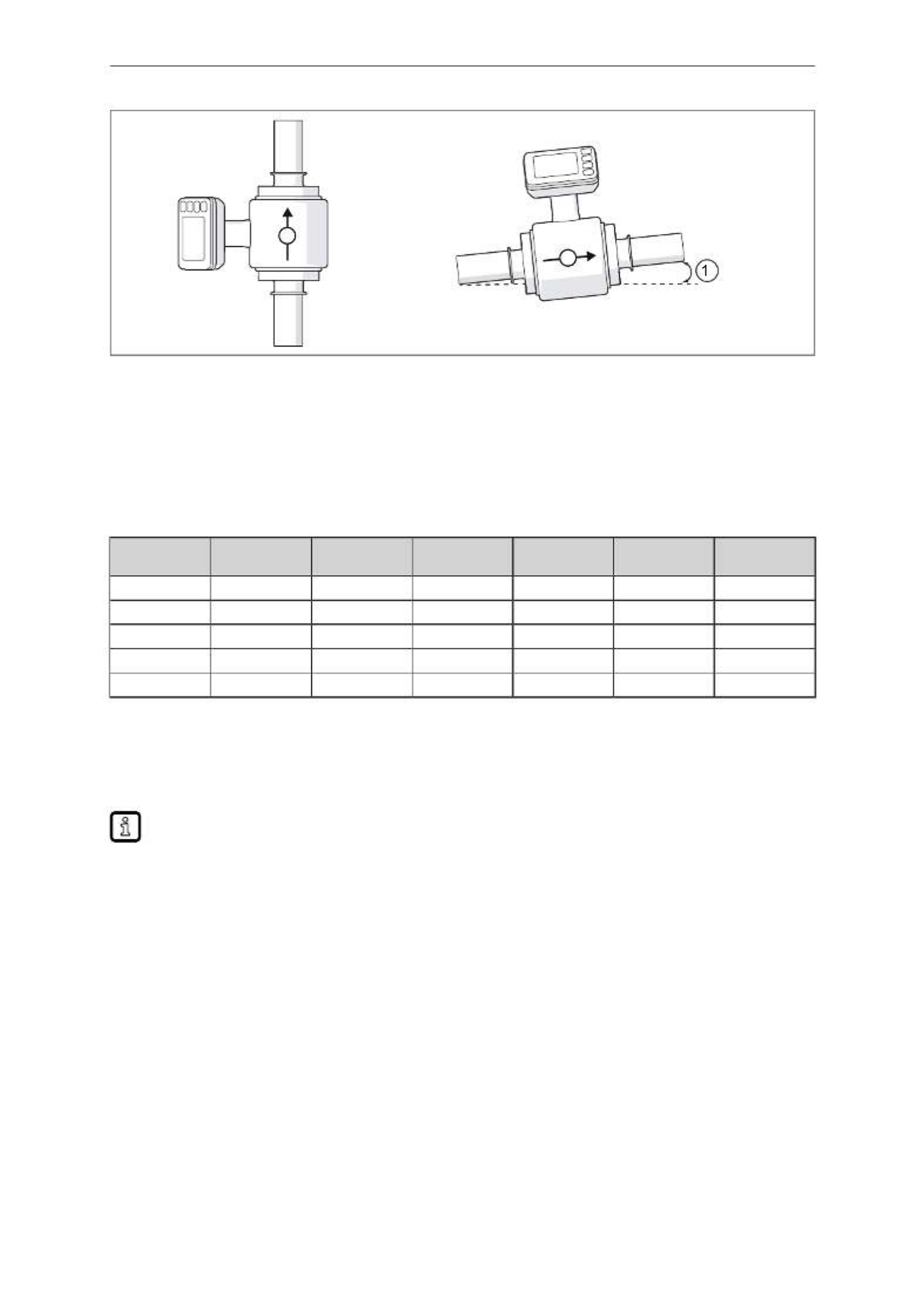
Magnetic-inductive flow meter SMFxxx
19
F
F
Fig.11: Process connection in compliance with 3-A
1: Minimum gradient
uTo allow the medium to flow out of the process adapter, mount the device in the following
installation position:
• Vertical installation in a rising pipe .
( Installation position 10)Ò/
- or –
• Horizontal position with a slight gradient so that the medium does not come to a standstill:
DN DIN32676-A ISO 2852 EN 10357
series A DIN11864-2A DIN11851 SMS1145
DN 40 6° 4° 6° 6° 6° 4°
DN 50 6° 4° 6° 6° 6° 4°
DN 65 10° 3° 10° 7° 7° 3°
DN 80 13° 3° 13° 8° 8° 3°
DN 100 6° 3° 6° 6° 6° 3°
Tab.8: Minimum gradient for drainage capacity
uRegularly check the seals between the device and the process adapter for deposits and damage.
uIn case of soiling, clean the seals with a suitable cleaning liquid (e.g. alcoholic solution).
uReplace the seals if necessary.
The frequency of the seal replacement depends on the frequency of the cleaning cycles, the
media temperature and the cleaning temperature.
uDefine regular cleaning cycles according to the process requirements.
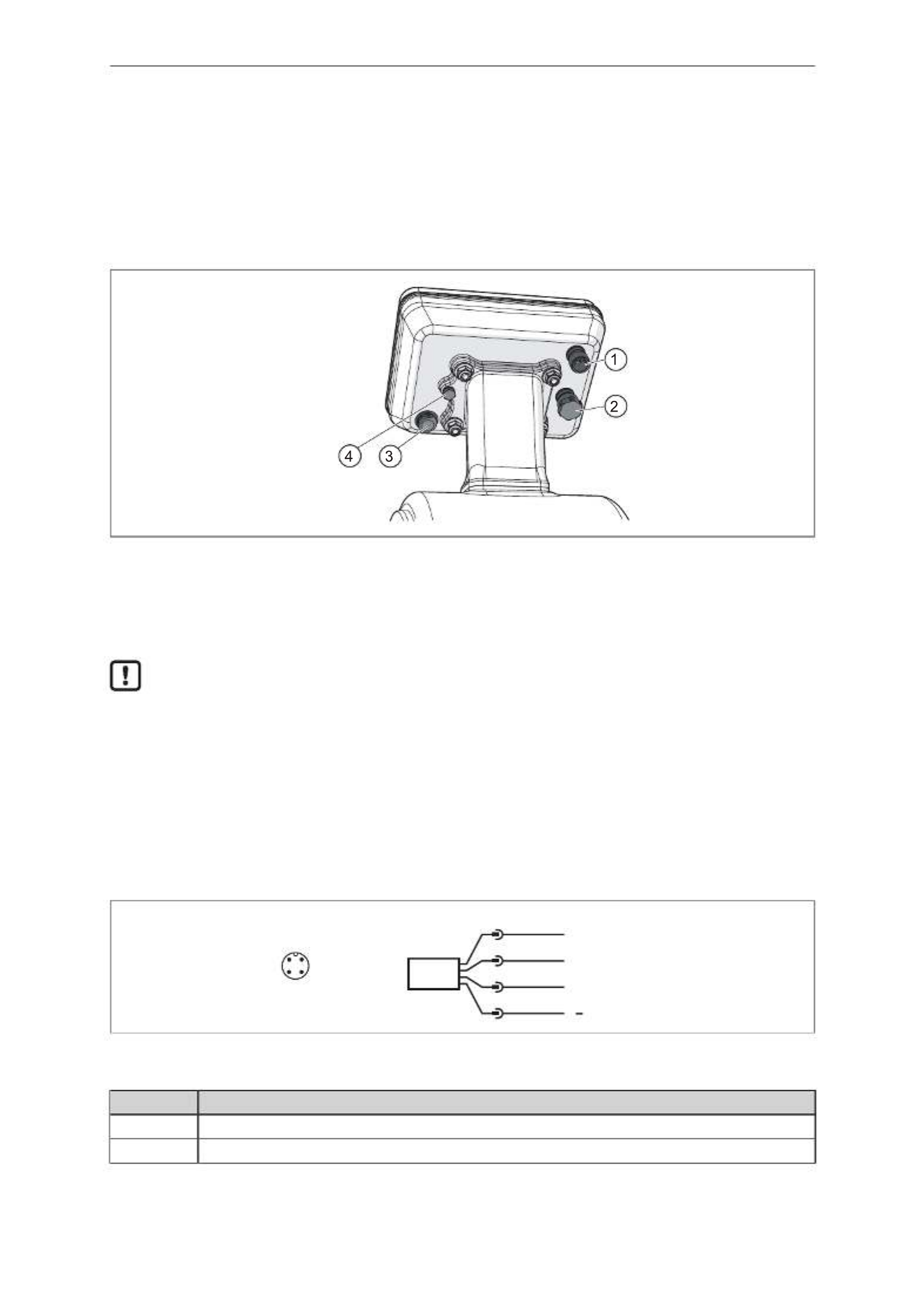
SMFxxx Magnetic-inductive flow meter
20
6 Electrical connection
The device has two M12 connectors:
1. The operating connector is for the operation of the device.
2. The service connector must only be used by ifm staff when the device is being serviced.
uCover the connectors with protective caps when they are not in use. Protective caps can be
ordered individually from .
documentation.ifm.com
Fig.12: Connectors
1: Operating connectors (see wiring diagram)
2: Service connector (only for service staff; delivered with protective cap)
3: Ventilation diaphragm (ensures reliable pressure compensation in the housing to prevent moisture build-up inside the
housing. The ventilation diaphragm is protected against damage by a screwed filter cover with circumferential ports.)
4: Ground connection Grounding clamps can be ordered from .www.ifm.com
The unit must be connected by a qualified electrician.
Observe the national and international regulations for the installation of electrical equipment.
Voltage supply according to SELV, PELV.
The input and output circuits are insulated from each other and from device surfaces that could be
touched with basic insulation according to IEC 61010-1 (secondary circuit with max. 32 V DC, supplied
from the mains circuit up to 300 V of overvoltage category II).
The external wiring has to be carried out in a way that ensures the required separation from other
circuits.
uDisconnect power.
uConnect the unit as follows:
43
2 1
L
1 BN
2 WH
4 BK
3 BU
OUT1/ IO-Link
OUT2
L+
Fig.13: Wiring diagram (colours according to IEC 60947-5-2)
BN: brown; WH: white; BK: black; BU: Blue
Pin Assignment
1 L+
3 L-
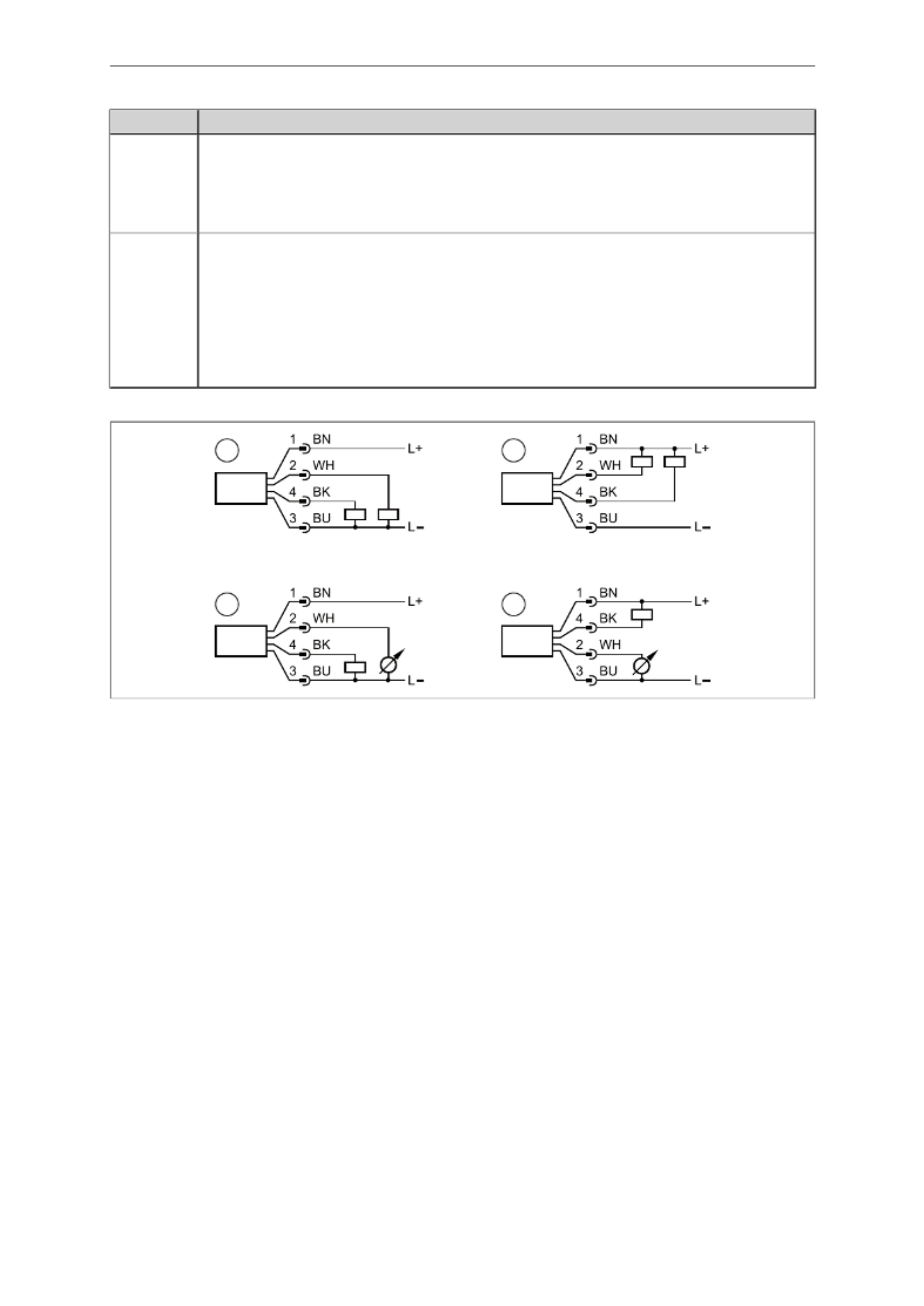
Magnetic-inductive flow meter SMFxxx
21
Pin Assignment
4 (OUT1) • Pulse signal totaliser
• Switching signal totaliser
• Switching signal diagnosis
• IO-Link
• OFF (output switched to high impedance)
2 (OUT2/InD) • Pulse signal totaliser
• Switching signal totaliser
• Analogue signal flow
• Analogue signal temperature
• Analogue signal for conductivity
• Switching signal diagnosis
• Input for external totaliser reset
• OFF (output switched to high impedance)
1 2
3 4
Fig.14: Circuit examples
1: 2 x positive switching
2: 2 x negative switching
3: 1 x positive switching / 1 x analogue
4: 1 x negative switching / 1 x analogue
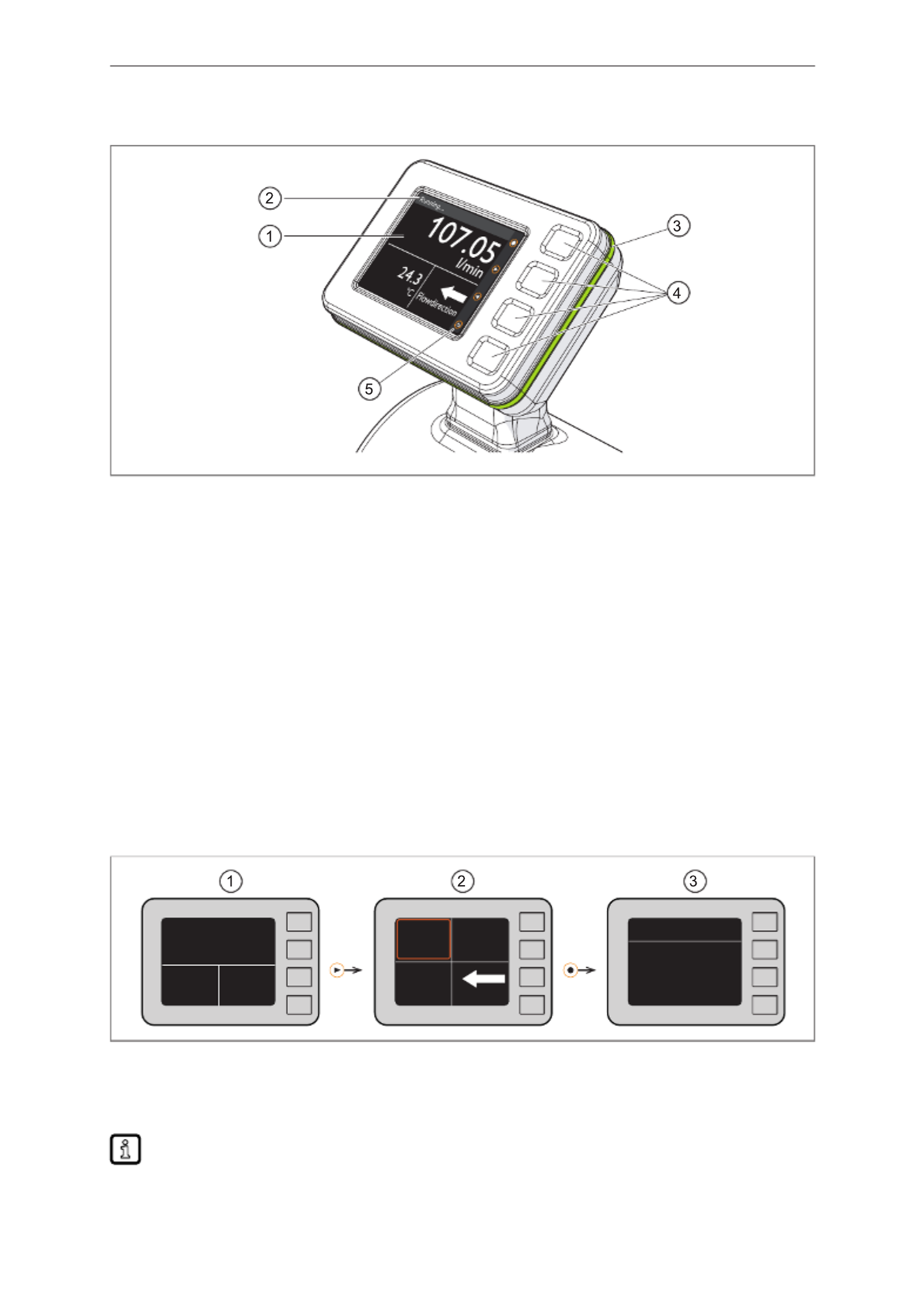
SMFxxx Magnetic-inductive flow meter
22
7 Operating and display elements
Fig.15: Operating and display elements
1: TFT-Display 3.5”: Shows 1 to 4 process values .
( Display layout 56)Ò/
2: Title line: Describes the status of the device (normal operation, warning messages, error messages).
3: Operating status LED (LED ring): Changes colour to signal the status of the device. ( Operating status LED 60)Ò/
4: Device keys: Keys for changing views and setting parameters .
( Parameter setting via the unit keys 32)Ò/
5: Key symbols: Indicate the functions of the corresponding device keys on the display.
The key symbols may be different on the process value display and in the individual menus.
Switching between display screens:
The device keys can be used to switch between different process value displays during operation:
uPress [►] or [◄].
wThe display shows the various display options.
uPress [►] or [◄] until the desired display screen is highlighted.
uPress [●] button.
wThe display shows all of the available information about the selected display screen.
uPress [▲] or [▼] to scroll through the selected display screen.
wAfter 30 s, the device returns to the standard display.
107.05
l
/
min
4.300
µS/cm
Conductivity
33.0
°C
Temperature
Flow
107.05
l/min
Flow
33
°C
Temperature
Flow direction
4.300
µS/cm
Conductivity
107.05 l/min
Flow minimum
l/min 2
Flow maximum
l/min 249
Analog starting point
l/min 12
Analog endpoint
l/min 300
Fig.16: Switching between display screens
1: Standard, pre-set display screen .
( Display layout 56)Ò/
2: Overview of all display options
3: Detailed view of the selected process value
The consumed quantity is automatically displayed in the unit of measurement providing the
highest resolution.
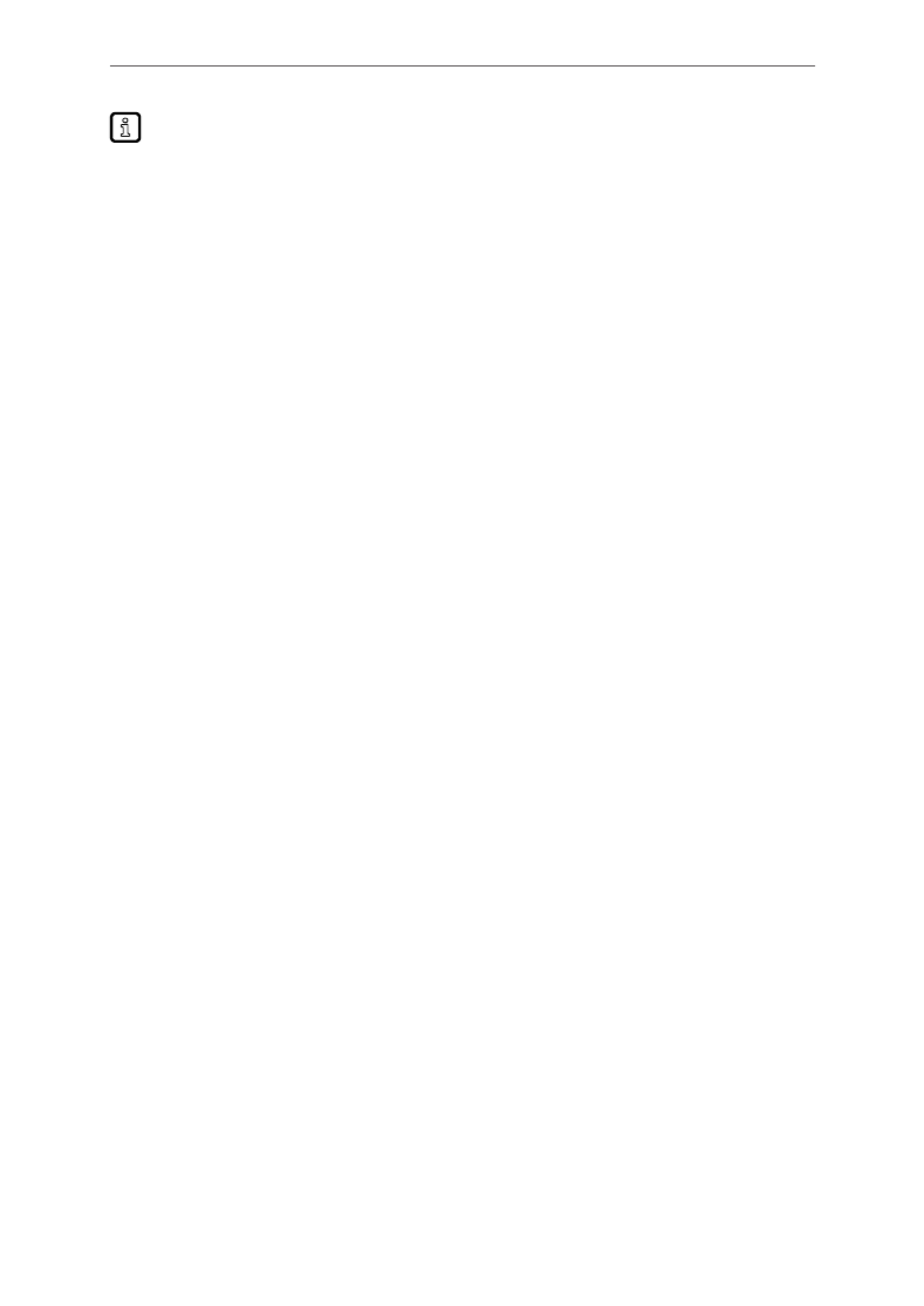
Magnetic-inductive flow meter SMFxxx
23
If the device measures a high internal temperature, the display brightness is automatically
adjusted:
Internal temperature >75°C: brightness is reduced to 25%.
Internal temperature≥90°C: display is automatically switched off.
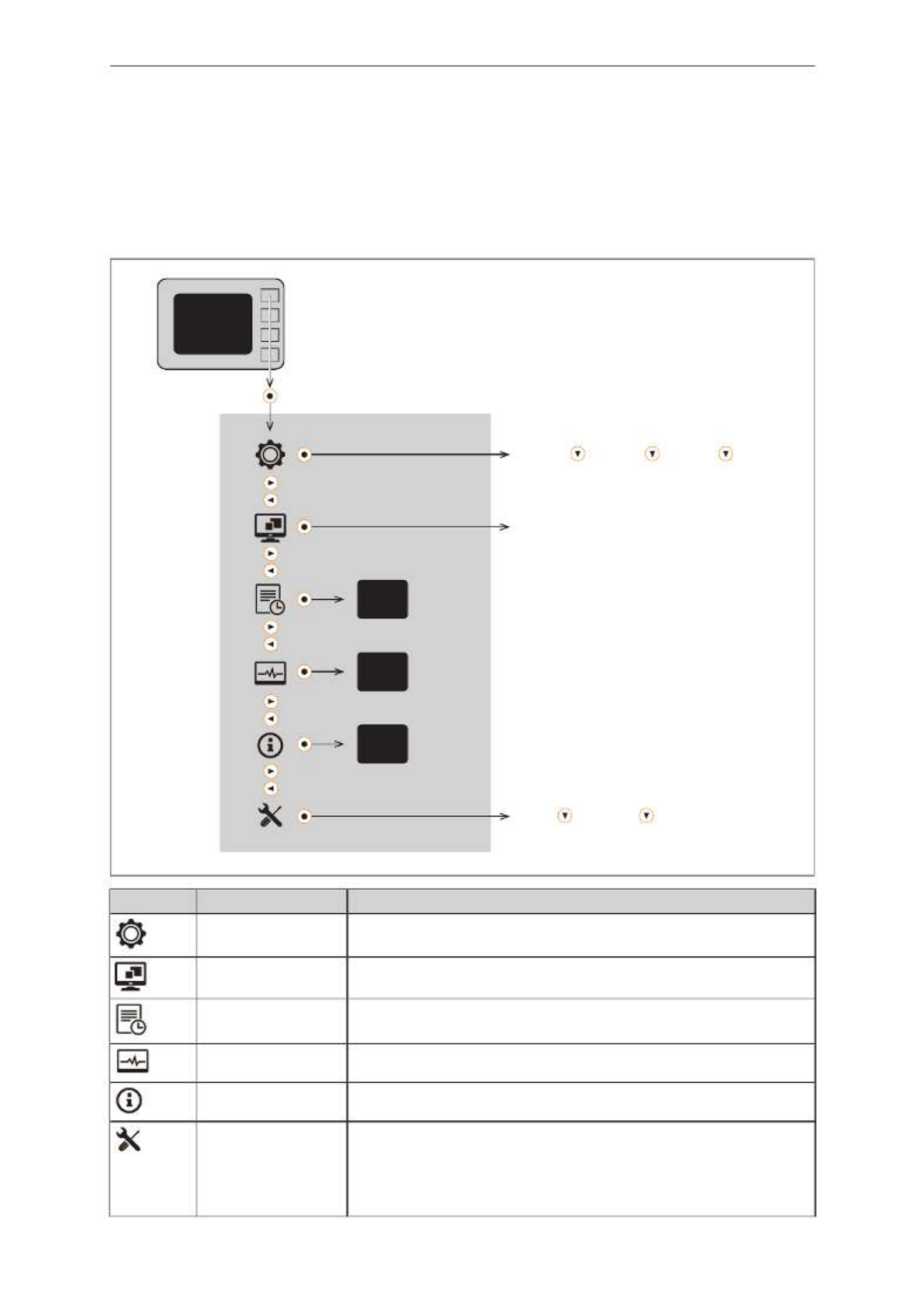
SMFxxx Magnetic-inductive flow meter
24
8 Menu
The figures in which the menus are displayed show the parameters that can be set on the unit by key
input. These parameters and other functions are also available via the IO-Link interface.
8.1 Main menu
107.05
l/min
[OUT1] [OUT2] [TOTL] [CFG]
[SIM] [O.CFG] [DOC]
XXXXX
xxx xx
XXXXX
xxx xx
XXXXX
xxx xx
XXXXX
xxx xx
XXXXX
xxx xx
XXXXX
xxx xx
XXXXX
xxx xx
XXXXX
xxx xx
XXXXX
xxx xx
Display
Symbol Name Explanation
Settings Switch to the following submenus : [OUT1]: output 1, [OUT2]:
( Submenus 25)Ò/
output 2, [TOTL]: totaliser, [CFG]: configuration.
Display Switch to the display menu .
( Submenus 29)Ò/
Event Shows previous events .
( Event history 61)Ò/
Diagnostics Shows diagnostics information :
( Diagnostics 57)Ò/
minimum and maximum flow, operating hours, internal temperature.
Device information Shows device-specific information .
( Device information 61)Ò/
Service Transition to the following submenus and display screens:
• [SIM]: Simulation . ( Submenus 30)Ò/
• [O.CFG]: .Configuration ( 62)Ò/
• [DOC]: Shows the QR codes that link to the data sheet, operating instructions
and certificate at www.ifm.com . ( Documents 63)Ò/
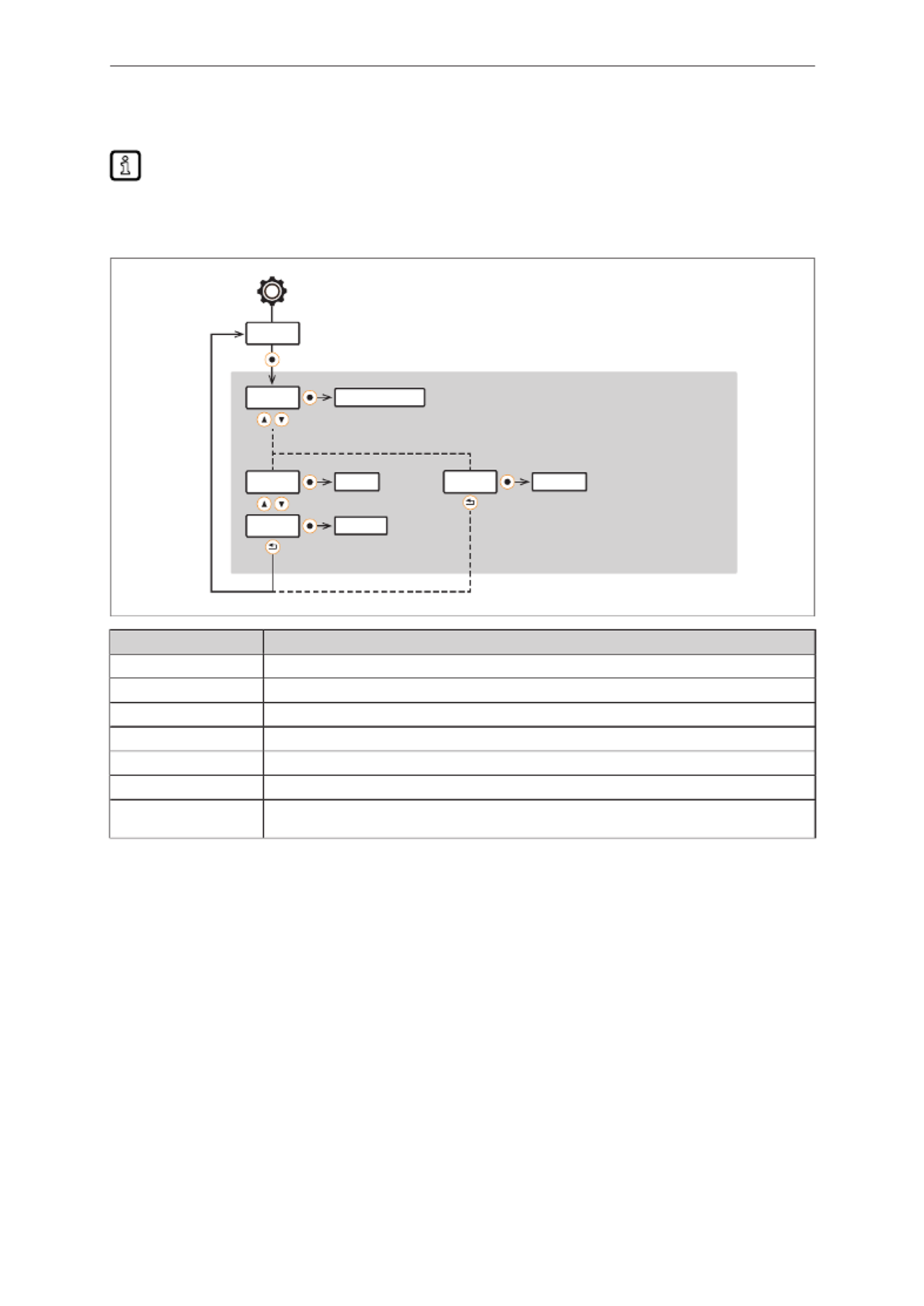
Magnetic-inductive flow meter SMFxxx
25
8.2 Submenus
The displayed parameters change when the factory setting is changed. The following menu
displays show the maximum available parameters.
Output1 menu [OUT1]:
ImPR1
ou1
---- dFu
YES│No
[OUT1]
OUT1
dOU│ImP│OFF
ImPS1 dir.F│FD
Parameter Explanation
ou1 Output function for output OUT1
dOU Diagnostic function
ImP Totaliser function
OFF Output off
ImPS1 Pulse value (= flow value at which 1 pulse is provided)
ImPR1 Totaliser function: pulse signal (ImPR1 = YES) or switching signal (ImPR1 = NO)
dFu Diagnostic switching signal for flow:
flow direction (= dir.F) or fluid detection (= FD)
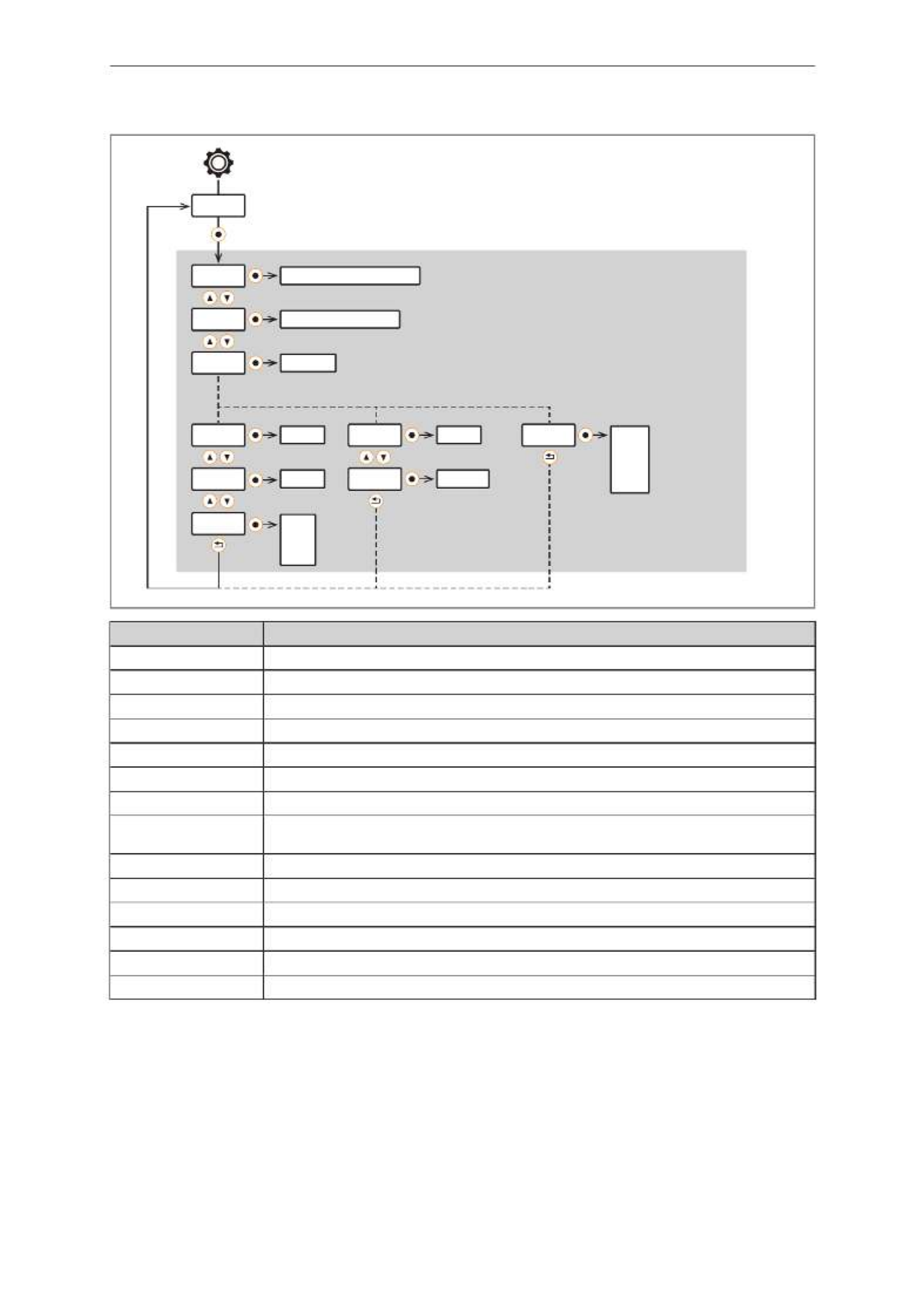
SMFxxx Magnetic-inductive flow meter
26
Output2 menu [OUT2]:
AEP2
DIn2│dOU│ImP│ I│OFF
ou2
FLOW│TEMP│COND
SEL2
----
ASP2
----
FOU2 ON
OFF
OU
OUT2
DIn2 HIGH
LOW
+EDG
-EDG
[OUT2]
ImPR2
----
YES│No
ImPS2
dir.F FD│
dFu
Parameter Explanation
ou2 Output function for output OUT2
I Analogue function
ImP Totaliser function
dOU Diagnostic function
DIn2 Totaliser reset via external signal
OFF Output off
SEL2 Process value for output OUT2
dFu Diagnostic switching signal for flow:
flow direction (= dir.F) or fluid detection (= FD)
ASP2 Analogue start point for OUT2 = process value at which the output signal is 4mA.
AEP2 Analogue end point for OUT2 = process value at which the output signal is 20mA.
ImPS2 Pulse value (= flow value at which 1 pulse is provided)
ImPR2 Totaliser function: pulse signal (ImPR2 = YES) or switching signal (ImPR2 = NO)
DIn2 Totaliser reset via external signal
FOU2 Behaviour of output OUT2 in case of error
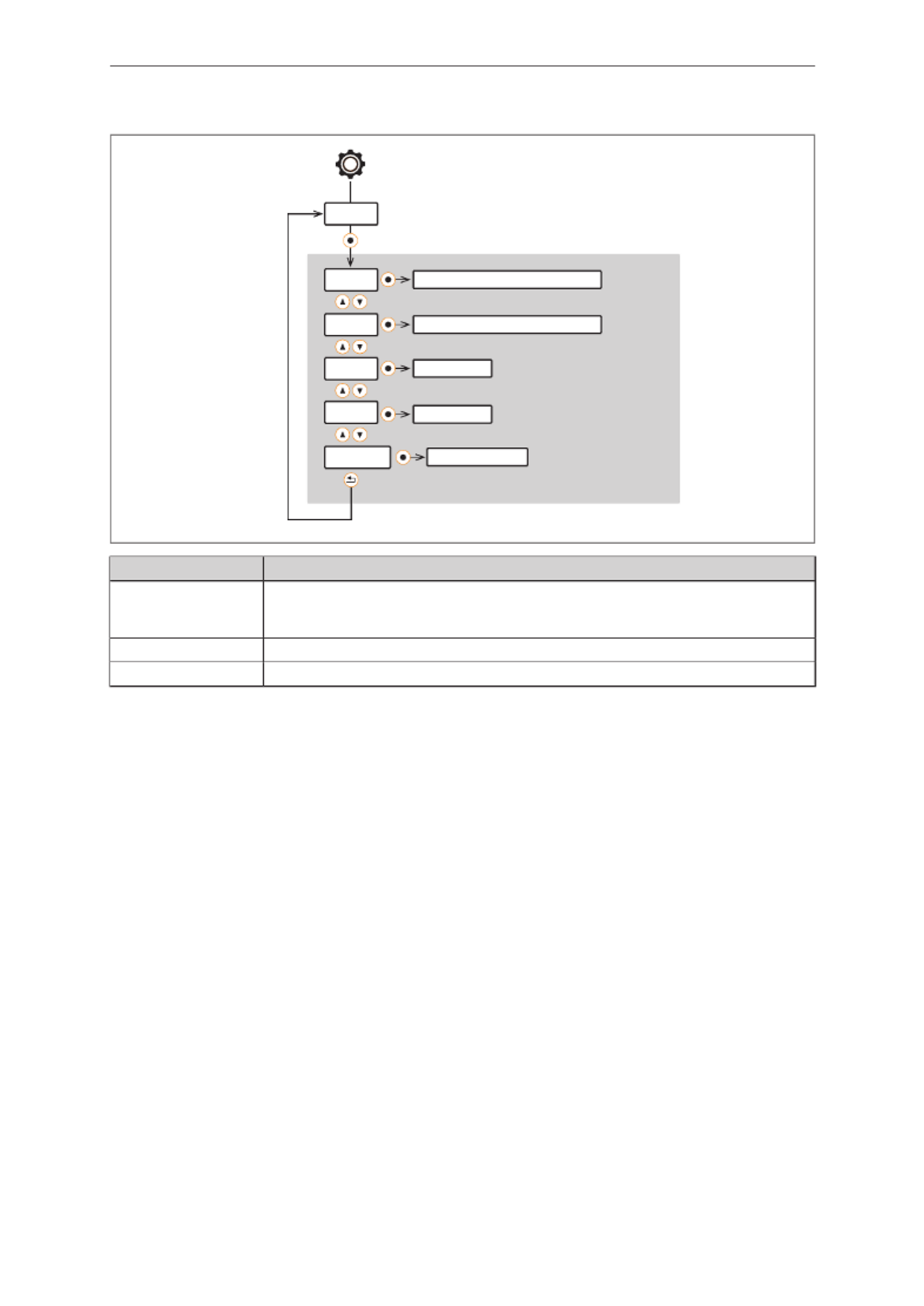
Magnetic-inductive flow meter SMFxxx
27
Totaliser menu [TOTL]:
rES.T1
rES.T2
[TOTL]
-+
-+
_I
Parameter Explanation
rTox Setting for the totaliser reset:
manual reset (= rES.Tx), time-controlled reset (= weeks, days, hours) or reset via overflow (=
OFF)
FProx Counting method of the totaliser: consideration of the direction of flow
TOTL_Info Shows totaliser values
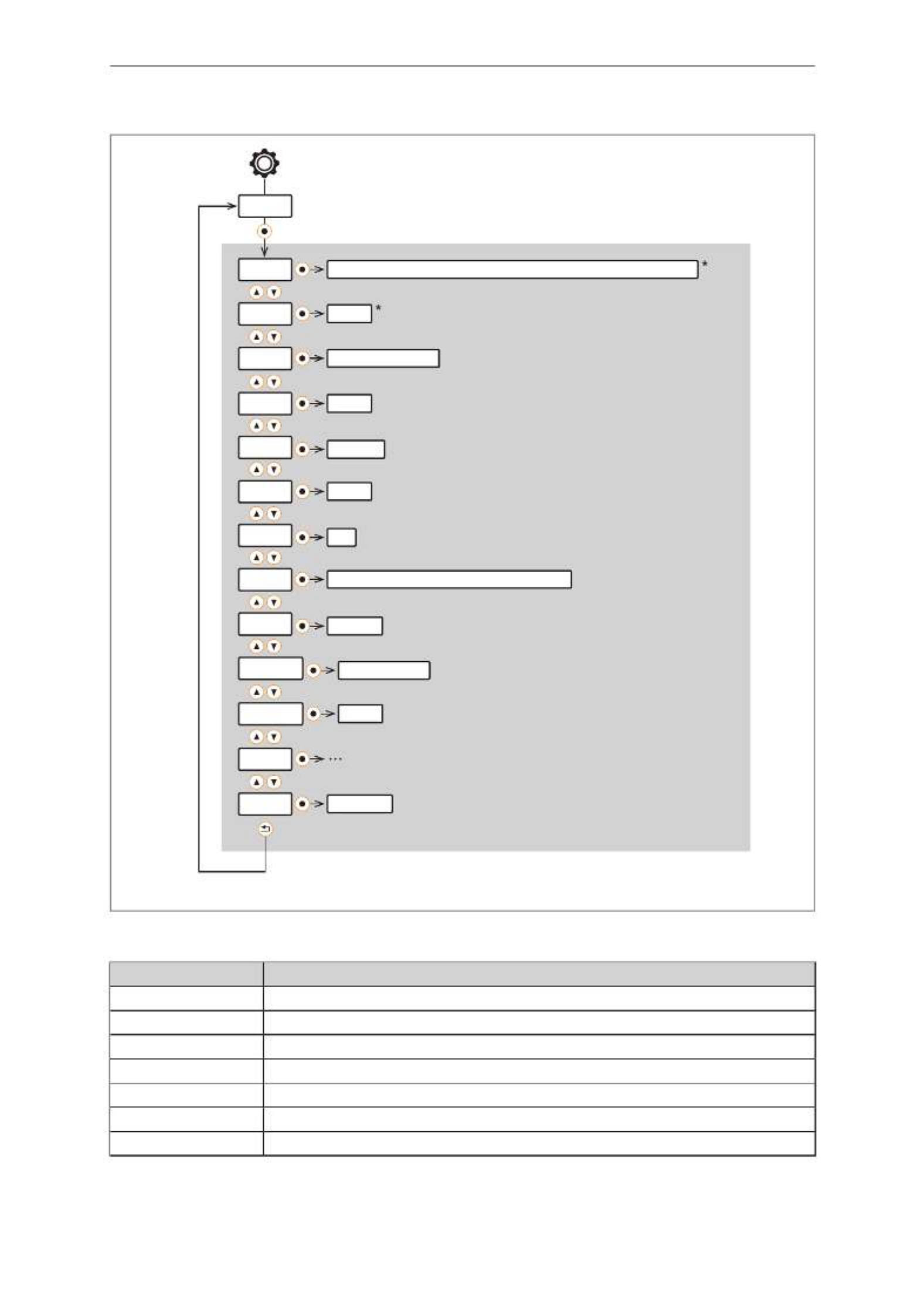
SMFxxx Magnetic-inductive flow meter
28
Configuration [CFG] menu:
3
3
[CFG]
----
----
----
APPL
*The options depend on the device type, see technical data at .documentation.ifm.com
Parameter Explanation
uni.F Standard unit of measurement for flow
uni.T Standard unit of measurement for temperature
uni.C Standard unit of measurement for conductivity
dAP.F Damping constant in seconds for flow (63 % rise time τ)
P-n Output polarity for the switching outputs
LFC Low flow cut-off
Fdir Direction of flow
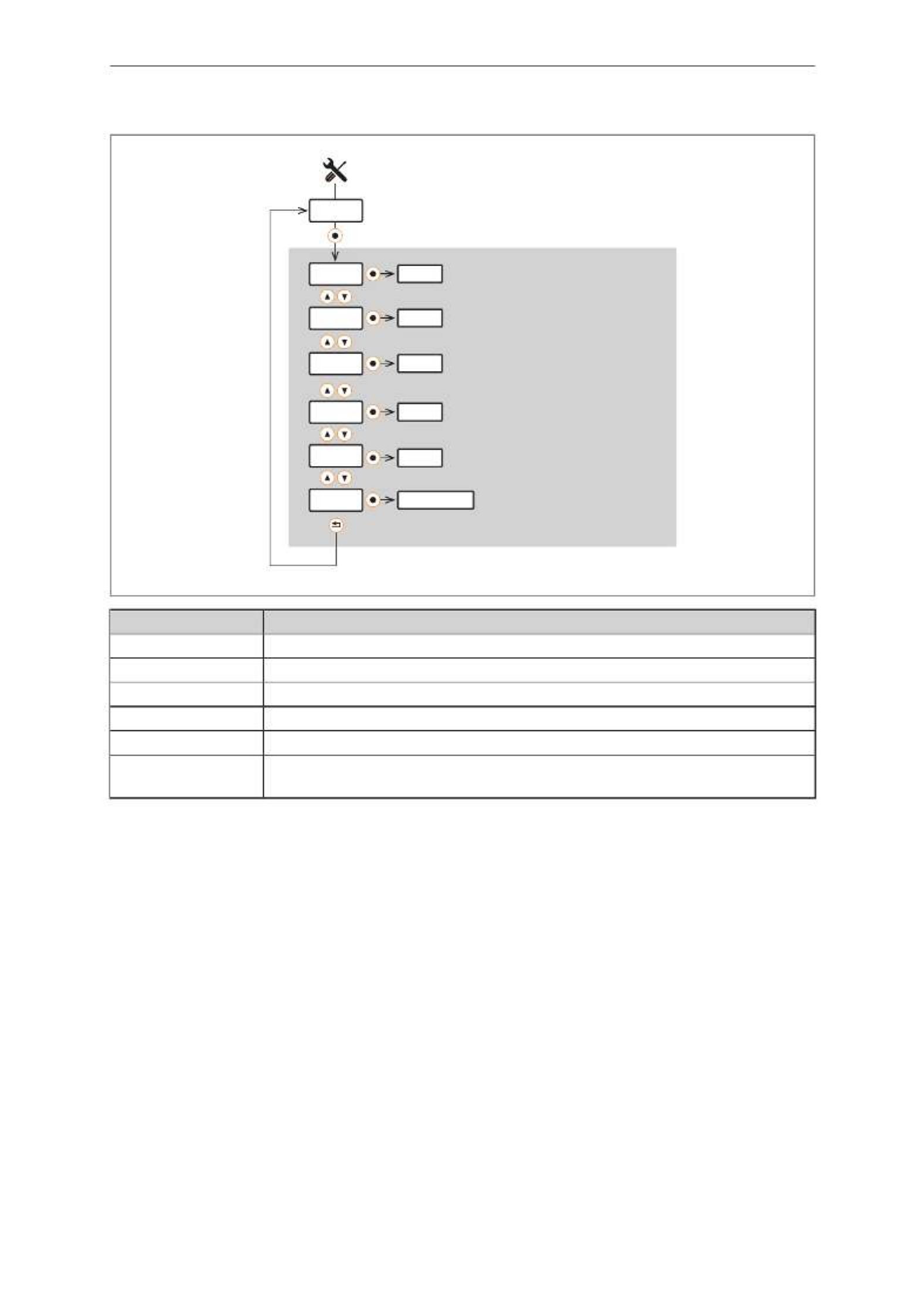
SMFxxx Magnetic-inductive flow meter
30
Simulation [SIM] menu:
D.Ok│FD.On
S.FLW
[SIM]
----
----
----
----
----
S.Tim
S.CND
S.TMP
S.On
S.DIAG
SIM
Parameter Explanation
S.FLW Simulated flow value in simulation mode
S.TMP Simulated temperature value in simulation mode
S.CND Simulated conductivity value in simulation mode
S.Tim Duration of the simulation in minutes
S.On Starts the simulation mode
S.DIAG Diagnostics value to be simulated:
device ok (= D.Ok); no medium in the measuring pipe (= FD.On)
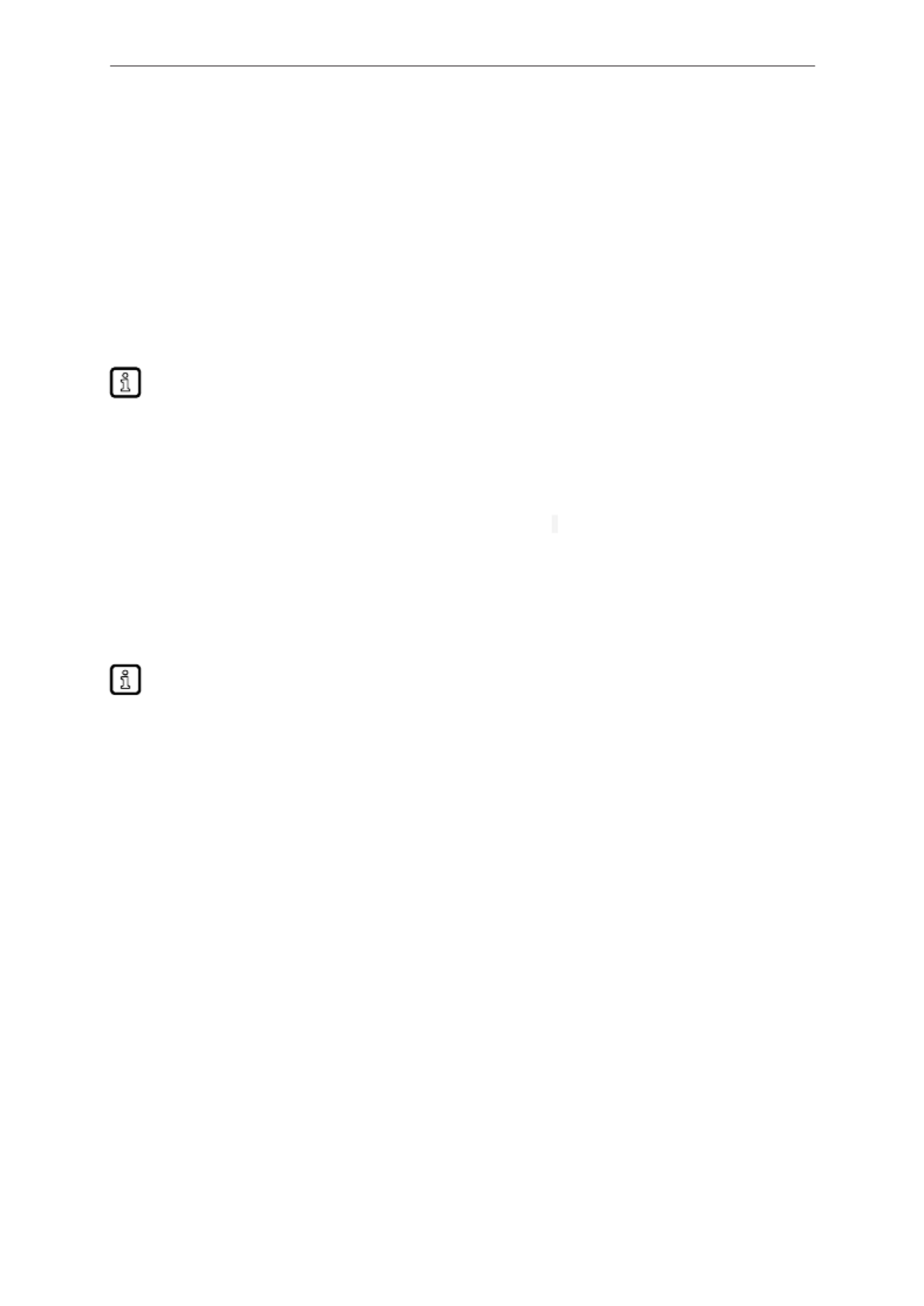
Magnetic-inductive flow meter SMFxxx
31
9 Set-up
After power on and expiry of the power-on delay time, the unit is in the normal operating mode. It
carries out its measurement and evaluation functions and generates output signals according to the
set parameters.
During the power-on delay time, the outputs are in the following status according to the set
parameters:
• ON for diagnostic function (dOU)
• ON for detection of direction (F.Dir)
• OFF for consumed quantity monitoring (ImP)
• 20 mA for current output (I)
When an IO-Link master is connected, the device automatically goes from SIO mode (standard
input-output) into IO-Link mode if the port of the master is set to IO-Link mode.
9.1 Guided installation via an installation wizard
New unboxed and factory reset devices – setup via main menu. When changing from process value
display to main menu you will be given the option to use the guided installation wizard (if the device
has been set up using IO-Link this option is no longer available).
uSelect [Yes] or [No].
wIf [Yes] is selected, parameters, questions and instructions appear in succession. Use the [▲] and
[▼] keys to choose from the available options and the [●] key to confirm the selection.
wIf [No] is selected, the main menu appears and the sensor functions according to the factory
settings. If necessary, change the parameter settings, see chapter Parameter setting.
The guided installation can be called up again at any time via the parameter [CFG] > [Wizard].
After the message that the guided installation is completed, you are asked whether you want to start
the measurement.
uSelect [Yes], [No] or [Info].
wIf [Yes] is selected, the installation process is completed. The display shows the chosen parameter
settings for 30 seconds. It then switches to the process value display.
wIf [No] is selected, individual parameters can be accessed and modified again, or the guided
installation can be restarted from the beginning using the [Restart wizard] command.
wIf [Info] is selected, the device displays the previously set device configuration.
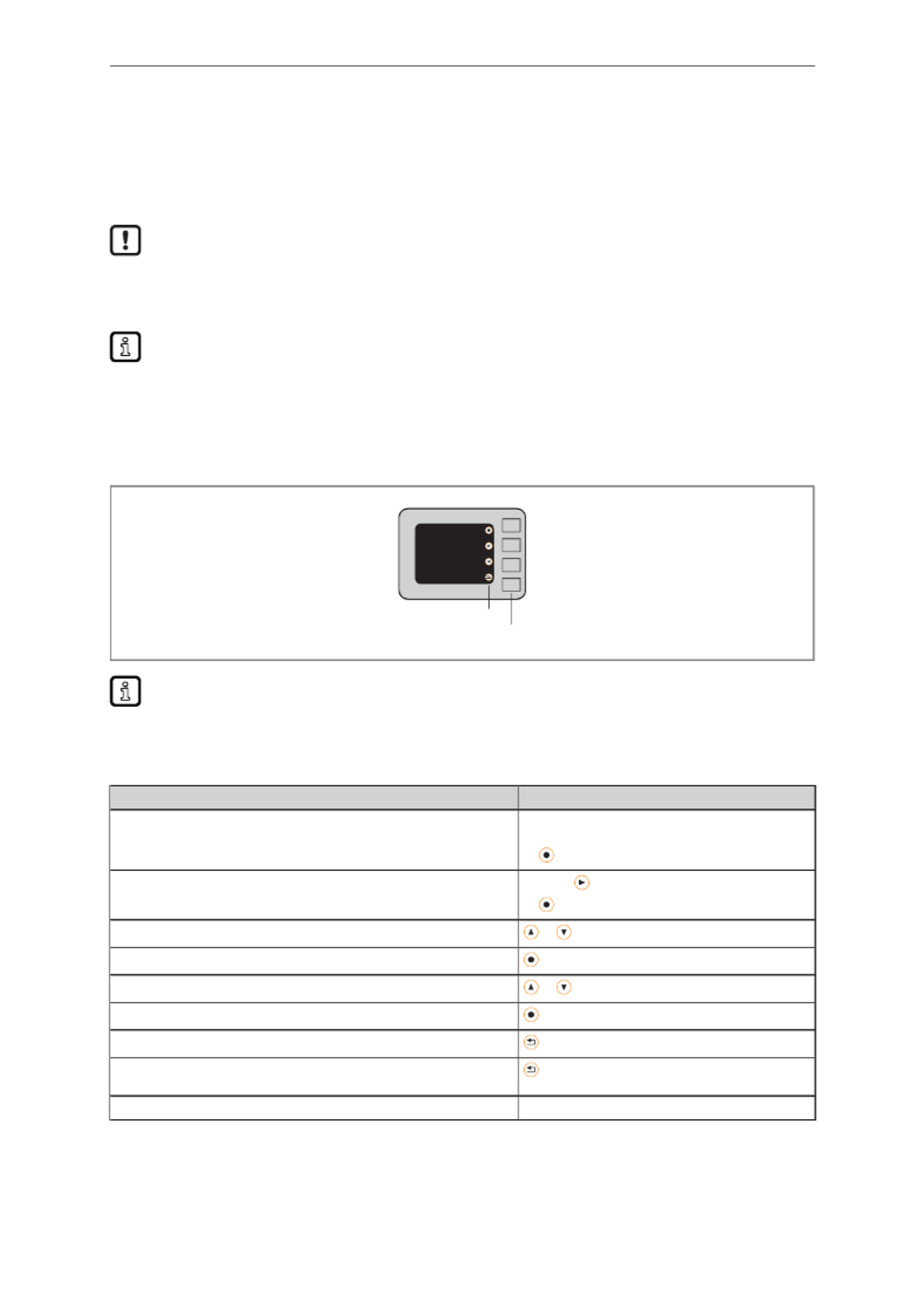
SMFxxx Magnetic-inductive flow meter
32
10 Parameter setting
Parameter setting can be carried out via the IO-Link interface or via the operating elements on the
unit.
Parameters can be set before installation or during operation.
If you change parameters during operation, this will influence the function of the plant.
uEnsure that there will be no malfunctions in your plant.
During parameter setting the unit remains in the operating mode. It continues to monitor with the
existing parameter until the parameter setting has been completed.
Depending on the parameter setting, the parameters available in the menu may change.
10.1 Parameter setting via the unit keys
Parameters are set on the device using capacitive pushbuttons that are operated by pressing gently
on them with a finger.
Key symbols Pushbuttons
The key symbols on the display show the function of the corresponding device key and may
differ in the process value display and the individual menus.
Parameter setting process in general:
uSet parameters according to the following table:
Intention Action
Change from the process value display to the main menu 1. Press any key to make the key symbols appear
on the display.
2. *
Change from main menu to submenu / other display screens 1. Press to reach a symbol, e.g. .
2.
Select the required parameter / the required display screen or
Change to the setting mode / change to lower-level display screens
Modify the parameter value or
Apply the set parameter
Exit parameter setting without saving or [Back] in the device menu
Return to the next higher menu level
(repeat several times to reach process value display) or [Back] in the device menu
Return to the process value display > 30 seconds (timeout)
Tab.9: Function of the device keys
* Guided installation is offered for initial set-up .
( Guided installation via an installation wizard 31)Ò/
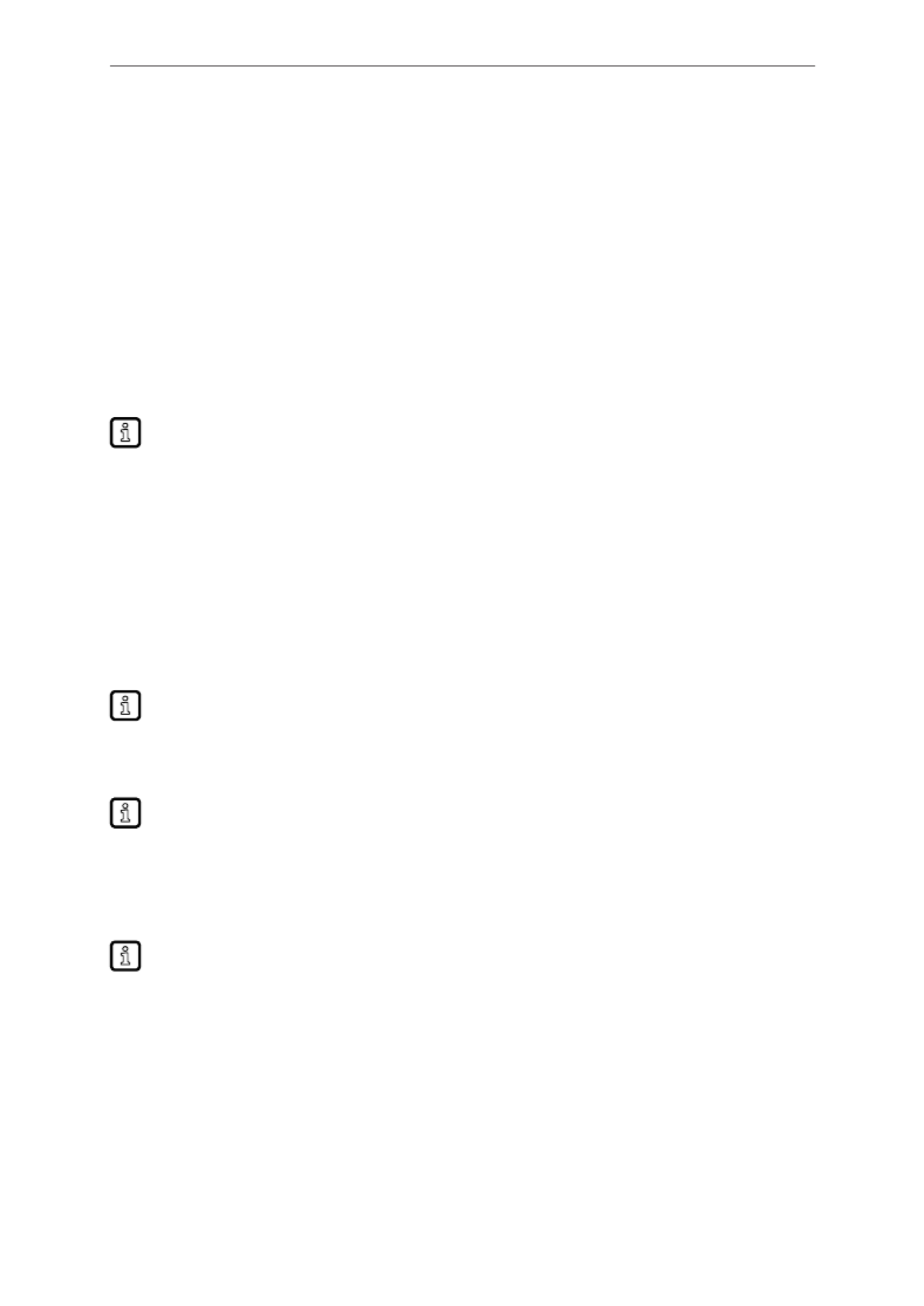
Magnetic-inductive flow meter SMFxxx
33
10.2 Parameter setting via IO-Link
Requirements for parameter setting via the IO-Link interface:
üA suitable parameter setting software, e.g. ifm moneo|configure
üThe Input Output Device Description (IODD) for the device, see documentation.ifm.com
üOne IO-Link master
uConnect the IO-Link master to a parameter setting software.
uSet the port of the master to the IO-Link operating mode.
uConnect the device to a free port of the IO-Link master.
wThe unit switches to IO-Link mode.
uChange parameter settings in the software.
uWrite parameter settings to the unit.
Notes on parameter setting Manual of the parameter setting softwareÒ
10.3 Output configuration
10.3.1 Analogue signal
The device provides an analogue signal proportional to the process value.
Within the measuring range the analogue signal is between 4...20 mA.
The measuring range can be scaled between -100% and 100% of the final value of the measuring
range.
A negative flow value means flow against the flow direction set under [Fdir]. ( FlowÒ
direction 45)/
• [ASP2] determines at which measured value the output signal is 4mA.
• [AEP2] determines at which measured value the output signal is 20mA.
Minimum distance between [ASP2] and [AEP2] = 20 % of the final value of the measuring
range.
If the measured value is outside the measuring range or in the event of an internal error, the current
signal indicated in the following figure is provided.
For measured values outside the display range or in case of an error, messages are displayed (cr.UL,
UL, OL, cr.OL, Err).
The analogue signal in case of a fault can be set via the parameter [FOU] ( Error behaviour ofÒ
the analogue output 43)/.
The analogue signal can be stabilised by setting the damping time [dAP] .
( Damping 44)Ò/
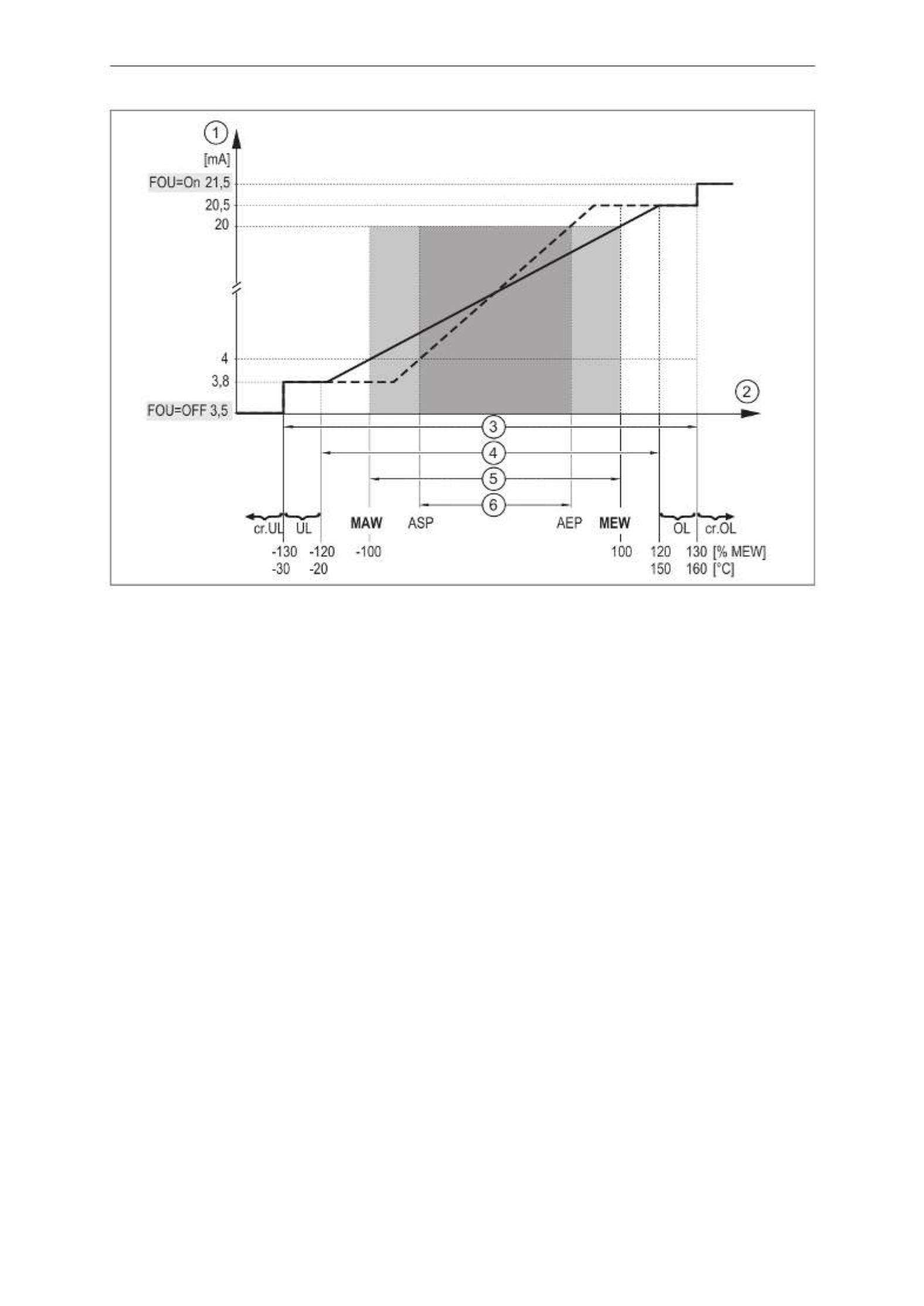
SMFxxx Magnetic-inductive flow meter
34
Fig.17: Characteristics of the analogue output according to the standard IEC 60947-5-7
1: Analogue signal MAW: Initial value of the measuring range
2: Measured value MEW: Final value of the measuring range
3: Detection range ASP: Analogue start point
4: Display range AEP: Analogue end point
5: Measuring range UL: Below the display range
6: Scaled measuring range cr.UL: Below the detection range
OL: Above the display range
cr.OL: Above the detection range
10.3.1.1 Parameter setting via unit keys: Analogue signal
üThe standard unit of measurement is selected: [Settings] > [CFG] > [uni.F].
uGo to menu [Settings] > [OUT2] to configure output OUT2.
uSelect [ou2] and set the function: [I] (analogue signal 4...20 mA.).
uSelect [SEL2] and set the process value: [FLOW], [TEMP] or [COND].
uSelect [ASP2] and set the measurement value at which the output signal is 4 mA.
uSelect [AEP2] and set the measurement value at which the output signal is 20 mA.
10.3.1.2 Parameter setting via IO-Link: Analogue signal
üStandard unit of measurement is selected: [Parameter] > [Basic settings] > [uni.x].
uGo to [Parameter] > [Output configuration].
uSelect [SEL2] and set the process value: [FLOW], [TEMP] or [COND].
uSelect [ou2] and set the function: [I] (analogue signal 4...20 mA.).
uSelect [Parameter] > [Analog output2].
uGo to [Flow], [Temperature] or [Conductivity].
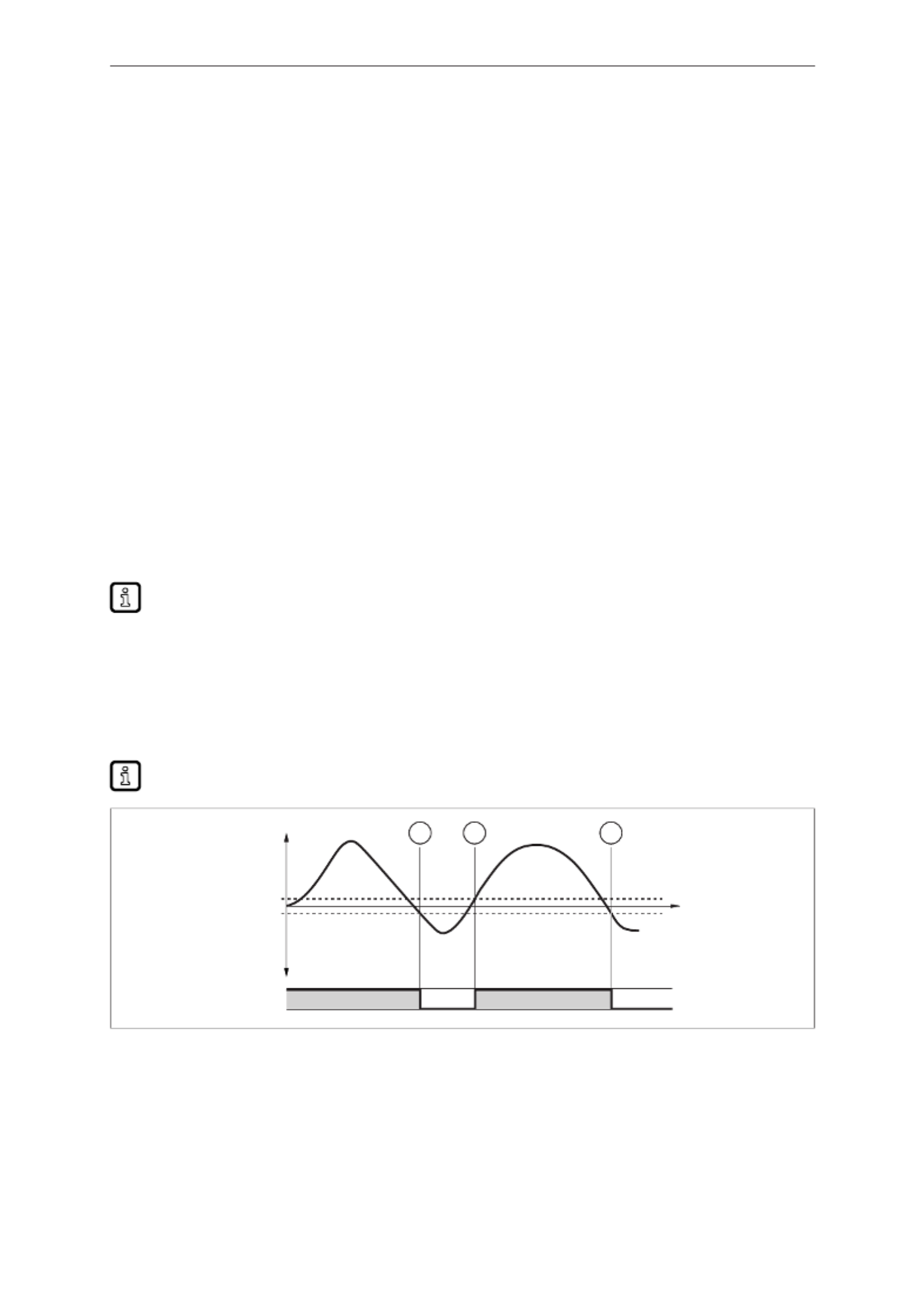
Magnetic-inductive flow meter SMFxxx
35
uSelect [ASP2-FLOW], [ASP2-TEMP] or [ASP2-COND] and set the measurement value at which the
output signal is 4mA.
uSelect [AEP2-FLOW], [AEP2-TEMP] or [ASP2-COND] and set the measurement value at which the
output signal is 20mA.
10.3.2 Switching signal diagnostics
The device features an integrated diagnostic function. When the diagnostic function is used, a
switching signal is provided via the hardware output.
The switching output is switched on in normal operation (normally closed). If the device detects a
diagnostic case, the output will be switched off.
Diagnostic cases include:
• reversal of the flow direction ( Switching signal for flow direction 35)Ò/
• no medium detected ( Switching signal for fluid detection 36)Ò/
10.3.2.1 Switching signal for flow direction
A flow direction change can be monitored by providing a switching signal.
An arrow with the text “flow direction” on the device indicates the positive flow direction. The direction
of the flow measurement can be reversed using the parameter [Fdir].
See .
Flow direction ( 45)Ò/
The flow direction that is currently indicated as positive can be viewed on the display (Ò
Operating and display elements 22)/.
The output is switched on until the volumetric flow falls below the set minimum volumetric flow quantity
in negative flow direction (-LFC)(1).
Then the following applies:
• The output switches ON when volumetric flow is above +LFC (2).
• The output switches OFF when volumetric flow is below -LFC (3).
LFC = low flow cut-off: Low flow cut-off.
+ LFC
+ Q
t
- Q
- LFC
1
0
1 2 3
Fig.18: Monitoring of the flow direction by switching signals
+Q Volumetric flow in positive flow direction
-Q Volumetric flow in negative flow direction
+LFC Minimum volumetric flow (low flow cut-off) in positive flow direction
-LFC Minimum volumetric flow (low flow cut-off) in negative flow direction
Parameter setting via unit keys: switching signal for flow direction
uGo to menu [Settings] > [OUTx].
uSelect [oux] and set [dOU].
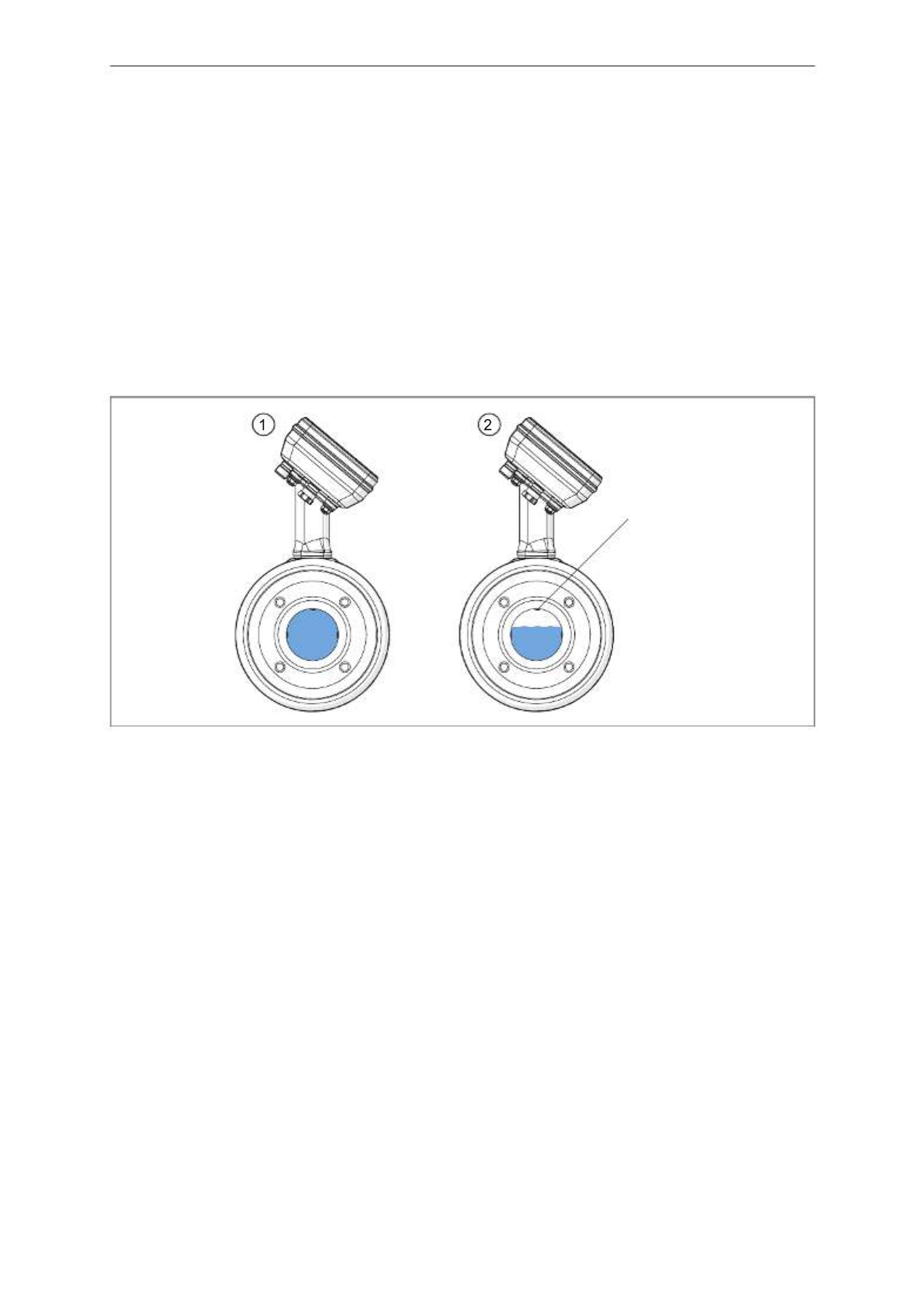
SMFxxx Magnetic-inductive flow meter
36
uSelect [dFU] and set [dir.F].
Parameter setting via IO-Link: switching signal for flow direction
uCall up [Parameters] > [Output Configuration].
uSelect [oux] and set [dOU].
uSelect [dFUx] and set [Flow direction].
10.3.2.2 Switching signal for fluid detection
The unit can provide a switching signal when it cannot detect a medium in the pipe.
The device uses this diagnostic function to identify whether the temperature electrode is wetted by
fluid. If it is not, the device interprets this as the pipe being empty and provides a digital switching
signal. The flow process value is set to zero.
Temperature electrode
Fig.19: Fluid detection:
1: Medium detected
2: Medium not detected
Parameter setting via the device keys: Switching signal for fluid detection
uGo to menu [Settings] > [OUTx].
uSelect [oux] and set [dOU].
uSelect [dFU] and set [FD].
uGo to menu [Settings] > [CFG].
uSelect [FD.On] and [YES].
Parameter setting via IO-Link: Switching signal for fluid detection
uCall up [Parameters] > [Output Configuration].
uSelect [oux] and set [dOU].
uSelect [dFUx] and set [Fluid detection].
uSelect [Parameters] > [Basic settings].
uSelect [FD.On] and set [On].
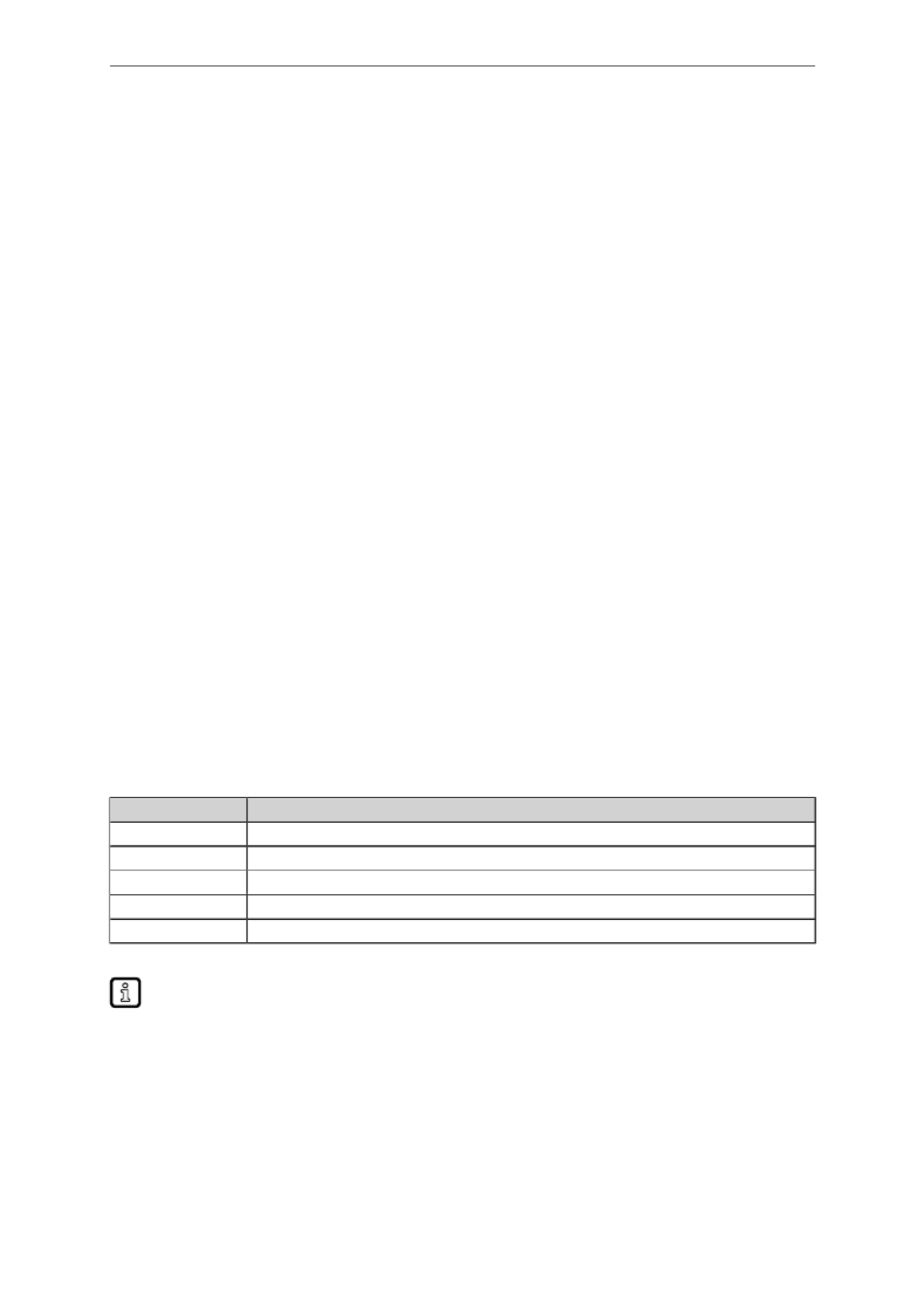
SMFxxx Magnetic-inductive flow meter
38
Parameter setting via unit keys: Switching signal totaliser
üThe standard unit of measurement is selected: [Settings] > [CFG] > [uni.F].
uGo to menu [Settings] > [OUTx] to configure output OUTx.
uSelect [oux] and set [ImP].
uSelect [ImPSx] and set the volumetric flow quantity at which the output switches.
• Press ▲ or ▼ to select the setting range.
• Briefly press ● to confirm the setting range.
• Press ▲ or ▼ to set the requested numeric value.
• Briefly press ● to apply the value.
uSelect [ImPRx] and set [No].
Parameter setting via IO-Link: Switching signal totaliser
üThe standard unit of measurement is selected: [Parameters] > [Basic settings] > [uni.F].
uGo to [Parameter] > [Output configuration].
uSelect [oux] and set [ImP].
uSelect [Parameter] > [Impulse output x].
uSelect [ImPSx-TOTL] and set the consumed quantity at which the output switches.
uSelect [ImPRx] and set [No].
10.3.3.2 Pulse signal totaliser
Pulse signals can be provided for consumed quantity monitoring.
Every time the consumed quantity (pulse value) set under [ImPS] has been reached, the output
provides a pulse signal.
The pulse signal consists of a short switching on and off of the output.
The pulse width depends on the pulse value and the flow speed: The lower the pulse value and the
higher the flow speed, the greater the pulse width. This applies up to a pulse width of 2s. Beyond this,
it remains at 2s.
DN Minimum pulse value [ImPS1]
40 2 ml
50 2 ml
65 4 ml
80 5 ml
100 9 ml
Tab.10: Lower setting range for [ImPS1] by device
Pulse signals are not available via the IO-Link interface.
Parameter setting via unit keys: Pulse signal totaliser
üThe standard unit of measurement is selected: [Settings] > [CFG] > [uni.F].
uGo to menu [Settings] > [OUTx] to configure output OUTx.
uSelect [oux] and set [ImP].
uSelect [ImPSx] and set the volumetric flow quantity at which 1 pulse is provided (pulse value).
• Press ▲ or ▼ to select the setting range.
• Briefly press ● to confirm the setting range.
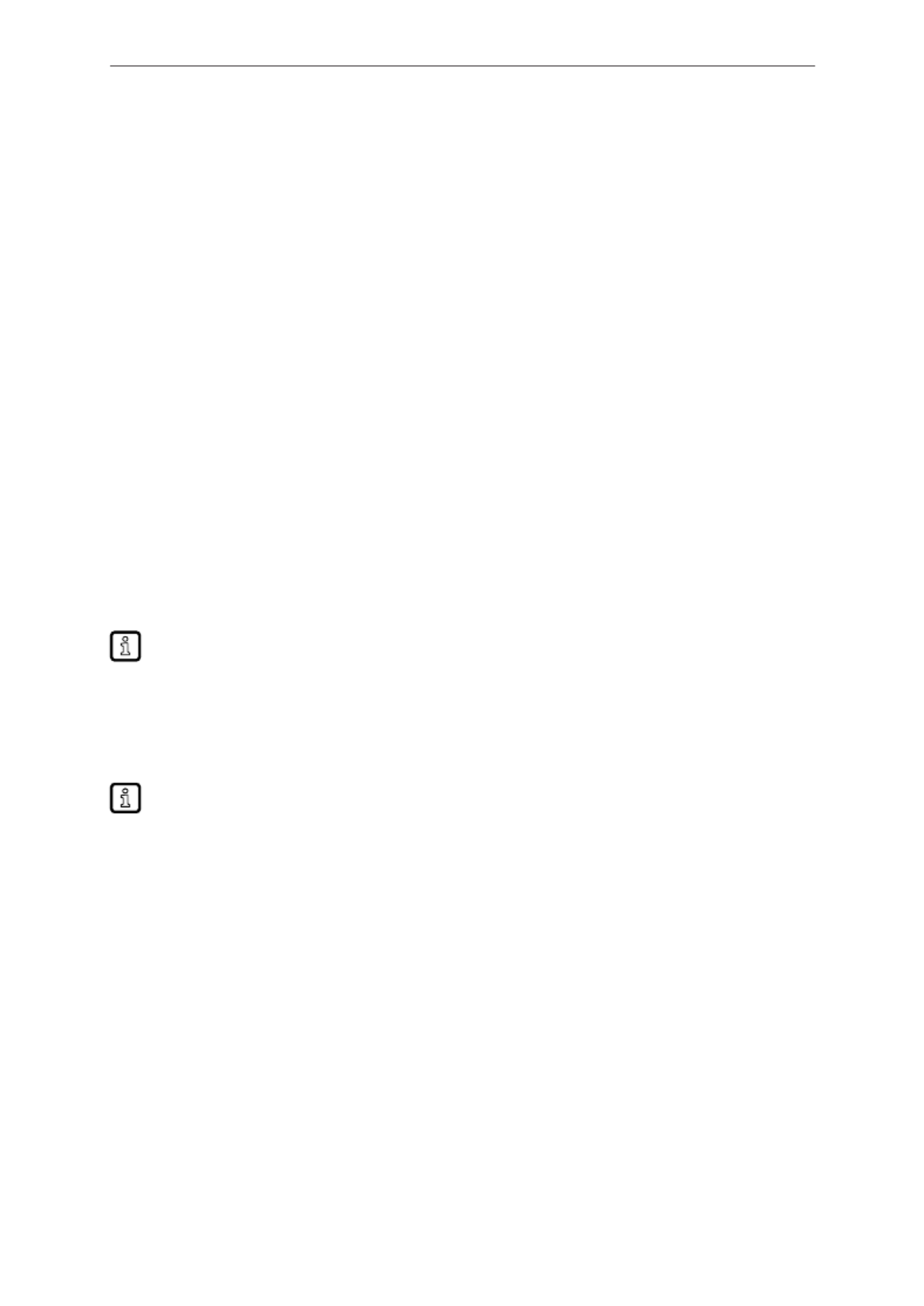
Magnetic-inductive flow meter SMFxxx
39
• Press ▲ or ▼ to set the requested numeric value.
• Briefly press ● to apply the value.
uSelect [ImPRx] and set [Yes].
Parameter setting via IO-Link: Pulse signal totaliser
üThe standard unit of measurement is selected: [Parameters] > [Basic settings] > [uni.F].
uGo to [Parameter] > [Output configuration].
uSelect [oux] and set [ImP].
uSelect [Parameter] > [Impulse output x].
uSelect [ImPSx-TOTL] and set the consumed quantity at which 1 pulse is provided (pulse value).
uSelect [ImPRx] and set [Yes].
10.3.4 Digital switching signal
The device provides digital switching signals via switching signal channels (SSC = Switching Signal
Channel).
The device has 2 digital switching signal channels SSCx.1 and SSCx.2 for each process value:
• SSC1.1 and SSC1.2 = switching signal channels for consumed quantity (totaliser)
• SSC2.1 and SSC2.2 = switching signal channels for flow
• SSC3.1 and SSC3.2 = switching signal channels for temperature
• SSC4.1 and SSC4.2 = switching signal channels for conductivity
Explanation of the numbering of the switching signal channels SSCx.y:
x = process value; y = switching signal channel
The switching signal channels can only be evaluated via the IO-Link interface.
The parameters for each switching signal channel can be set individually.
The switch point mode, switch points and the switch point logic are set when the switching signal
channel parameters are set.
The parameters for switching signal channels can only be set via the IO-Link interface.
Switch point mode
You can choose between the following switch point modes according to the IO-Link smart sensor
profile ‒ Function Class “Object Detection”:
• [Deactivated]
• [Single Point Mode]
• [Two Point Mode]
• [Window Mode]
The switching signal channel changes to the active state depending on the process data value (PDV).
The active state is above the switch point in [Single Point Mode] and [Two Point Mode] and within the
window section in [Window Mode].
Switch point logic
By setting the switch point logic [High active] or [Low active], you can specify which value the
switching signal channel has in the active state:
• [High active]: The switching signal channel is “high” in the active state (= ON = normally open = 1)
• [Low active]: The switching signal channel is “low” in the active state (= OFF = normally closed = 0)
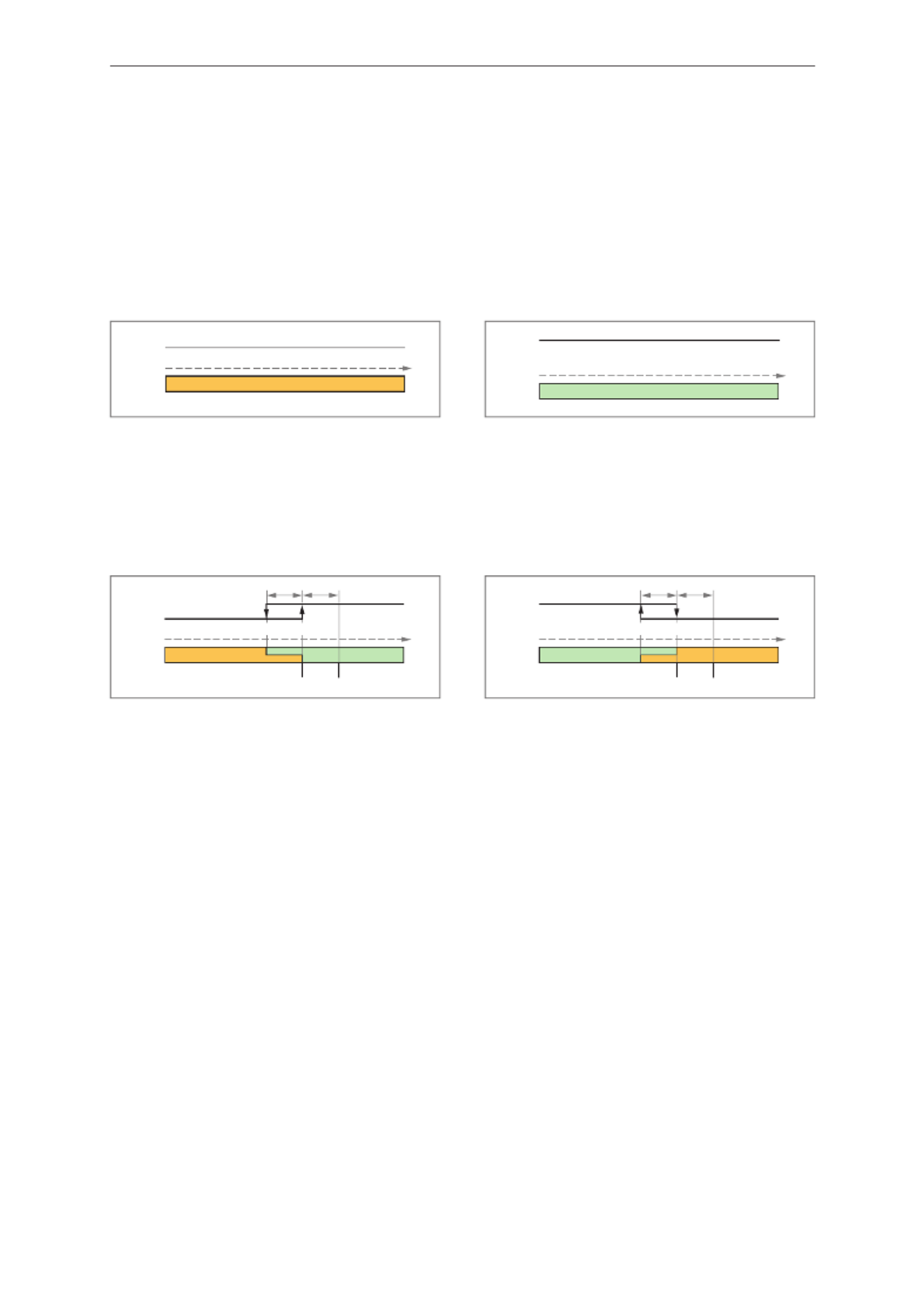
SMFxxx Magnetic-inductive flow meter
40
The following figures show the status of the switching signal channels depending on the switch point
mode, switch point logic and process data value (PDV).
Deactivated
If the [Deactivated] switch point mode is set for a switching signal channel, then the switching signal
channel will permanently have the following value regardless of the process value:
• For switch point logic [High active]: permanently “low”.
• For switch point logic [Low active]: permanently “high”.
low
PDV
0
Fig.20: [Deactivated] / [High active]
high
PDV
1
Fig.21: [Deactivated] / [Low active]
Single Point Mode
Only one switch point (SP1) is manually set or taught.
The reset point (SP1-H) results from the switch point and the set hysteresis.
When teaching, the switch point is set below the taught process value (TP1) by the hysteresis.
SP1
low high
TP1
PDV
0
1
H H
SP1
-
H TP1
-
H
Fig.22: [Single Point Mode] / [High active]
H: Hysteresis
SP1: Switch point
TP1: Teach point
TP1-H: Switch point during teach (= SP1)
SP1-H Reset point
SP1
low
high
TP1
PDV
1
0
H H
SP1
-
H TP1
-
H
Fig.23: [Single Point Mode] / [Low active]
H: Hysteresis
SP1: Switch point
TP1: Teach point
TP1-H: Switch point during teach (= SP1)
SP1-H Reset point
Two Point Mode
One switch point SP1 and one switch point SP2 are manually set or taught.
The position of the switch points is freely selectable: SP1 can be below or above SP2. The lower
switch point is the reset point. In the example shown, SP1 is the switch point and SP2 is the reset
point.
When teaching, the switch point is set directly to the taught process value. The following applies:
[TeachSP1] sets SP1, [TeachSP2] sets SP2.
The hysteresis will be ignored in Two Point Mode.
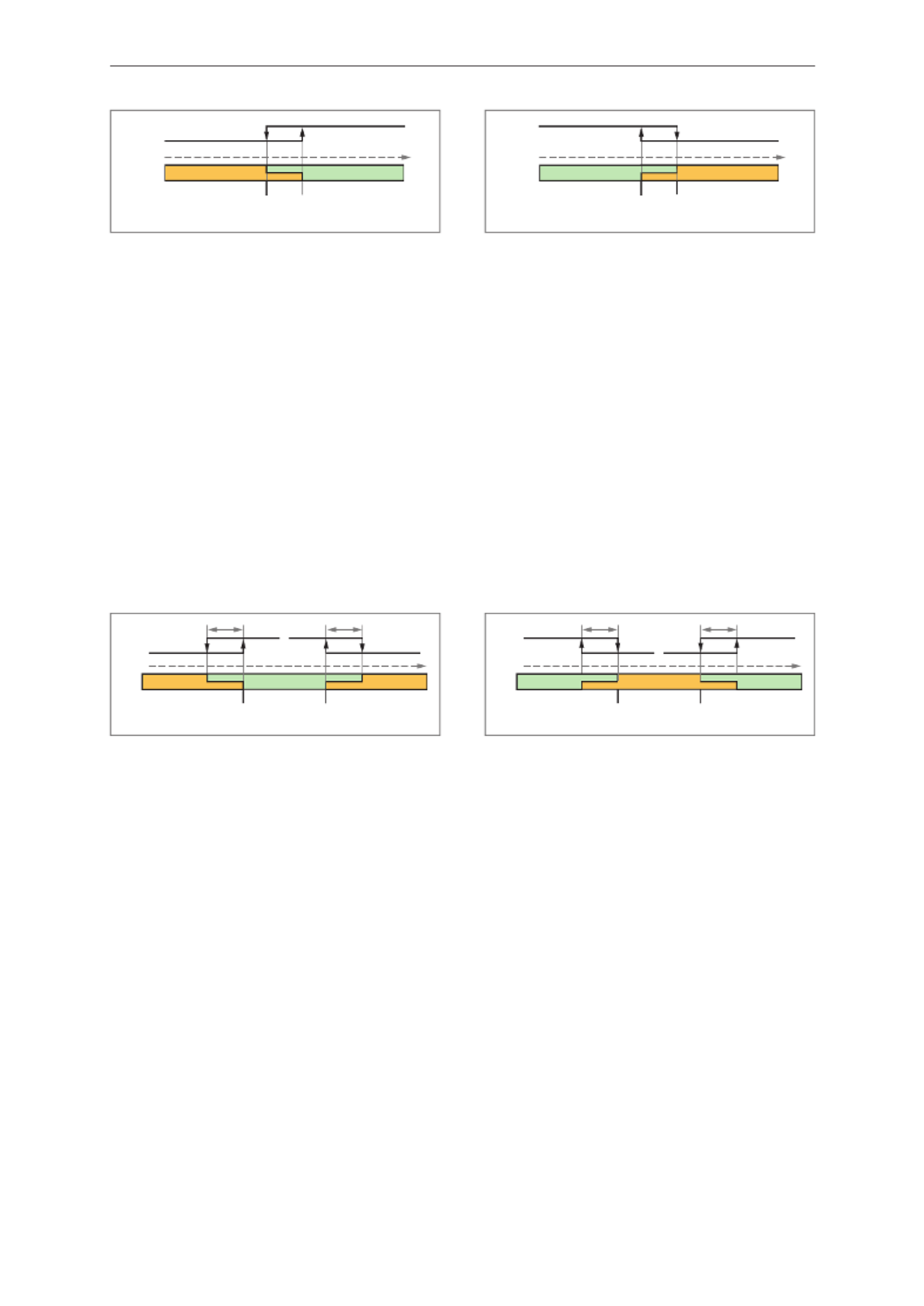
Magnetic-inductive flow meter SMFxxx
41
SP1
low high
SP2
(TP1)(TP2)
PDV
0
1
Fig.24: [Two Point Mode] / [High active]
SP1: Switch point 1
SP2: Switch point 2
TP1: Teach point 1 (= SP1)
TP2: Teach point 2 (= SP2)
SP1
high low
SP2
(TP1)(TP2)
PDV
1
0
Fig.25: [Two Point Mode] / [Low active]
SP1: Switch point 1
SP2: Switch point 2
TP1: Teach point 1 (= SP1)
TP2: Teach point 2 (= SP2)
Window mode
Two switch points (SP1) and (SP2) are manually set or taught.
The two switch points define a window area.
The position of the switch points is freely selectable: SP1 can be below or above SP2. The lower
switch point is the lower limit value, the higher switch point is the upper limit value of the window area.
When teaching, the switch point is set directly to the taught process value. The following applies:
[TeachSP1] sets SP1, [TeachSP2] sets SP2.
When the process data value enters the window area, the status of the switching signal channel
changes immediately when the switch points are exceeded/not reached.
If the process data value leaves the window area, the status of the switching signal channel changes
when the switch point plus hysteresis (SP1+H or SP2-H) is exceeded/not reached.
SP2 SP1
(TP2) (TP1)
lowlow high
PDV
0 0
1
H
H
Fig.26: [Window Mode] / [High active]
H: Hysteresis
SP1: Switch point 1
SP2: Switch point 2
TP1: Teach point 1 (= SP1)
TP2: Teach point 2 (= SP2)
SP2 SP1
(TP2) (TP1)
low highhigh
PDV
0
1 1
HH
Fig.27: [Window Mode] / [Low active]
H: Hysteresis
SP1: Switch point 1
SP2: Switch point 2
TP1: Teach point 1 (= SP1)
TP2: Teach point 2 (= SP2)
10.3.4.1 Parameter setting via IO-Link: Switching signal channels
üThe standard unit of measurement is selected: [Parameters] > [Basic settings] > [uni.x].
uGo to [Parameter] > [SSCx.x] to configure SSCx.x switching signal channel.
uSelect [SSCx.xConfig.Mode] and set the switch point mode: [Single Point], [Two Point], [Window]
or [Deactivated].
uSelect [SSCx.xParam.SP1] and set switch point 1.
uSelect [SSCx.xParam.SP2] and set switch point 2.*
uSelect [SSCx.xConfig.Hyst] and set the hysteresis.**
uSelect [SSCx.xConfig.Logic] and set the switch-point logic: [High active] or [Low active].
uSelect [SSCx.xDelay.Switching delay] and set the switching delay time.
uSelect [SSCx.xDelay.Reset delay] and set the switch-off delay time.
*Only for switch-point modes [Two Point] or [Window].
**Only for switch-point modes [Single Point] or [Window].
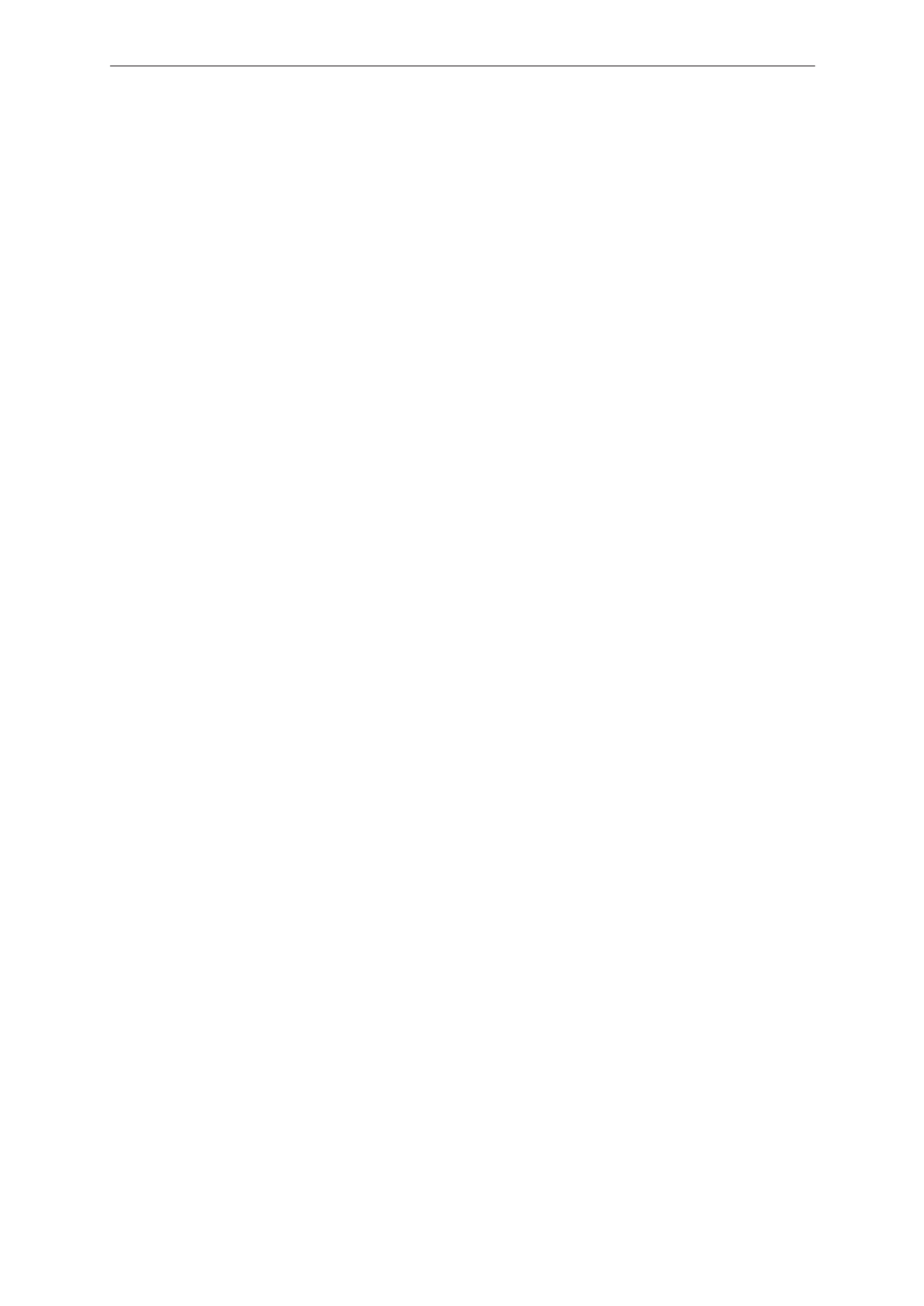
SMFxxx Magnetic-inductive flow meter
42
10.3.4.2 Teach via IO-Link: Switching signal channels
uGo to [Parameter] > [SSCx.x] to configure SSCx.x switching signal channel to be taught.
uSelect [SSCx.xConfig.Mode] and set the switch point mode: [Single Point], [Two Point], [Window]
or [Deactivated].
uSelect [SSCx.xConfig.Hyst] and set the hysteresis.**
uSelect [SSCx.xConfig.Logic] and set the switch-point logic: [High active] or [Low active].
uSelect [SSCx.xDelay.Switching delay] and set the switching delay time.
uSelect [SSCx.xDelay.Reset delay] and set the switch-off delay time.
uSave parameter set.
uSelect [Write to device].
wThe changed values are transferred to the unit.
uApproach the process value for the desired switch point and keep it constant.
uSelect [Parameters] > [Teach].
uSelect [Teach Select] and set the switching signal channel [SSCx.x].
wThe following “Teach” will be executed for the selected switching signal channel.
uExecute the command: [Teach SP1].
uApproach the process value for the desired switch point2 and keep it constant.*
uExecute the command: [Teach SP2].*
*Only for switch-point modes [Two Point] or [Window].
**Only for switch-point modes [Single Point] or [Window].
10.3.5 Output off
The output signal can be deactivated. The output then goes to high impedance.
Communication via the IO-Link interface on OUT1 remains active.
10.3.5.1 Parameter setting via unit keys: output off
uGo to menu [Settings] > [OUTx].
uSelect [oux] and set [OFF].
10.3.5.2 Parameter setting via IO-Link: output off
uCall up [Parameters] > [Output Configuration].
uSelect [oux] and set [OFF].
10.4 Application configuration
The chapter describes the setting options for adaptation to your specific application.
10.4.1 Standard unit of measurement
A unit of measurement can be selected with which the process value is shown in the display by
default. All further parameter settings are based on this unit.
Selectable values:
• [uni.F] for flow:
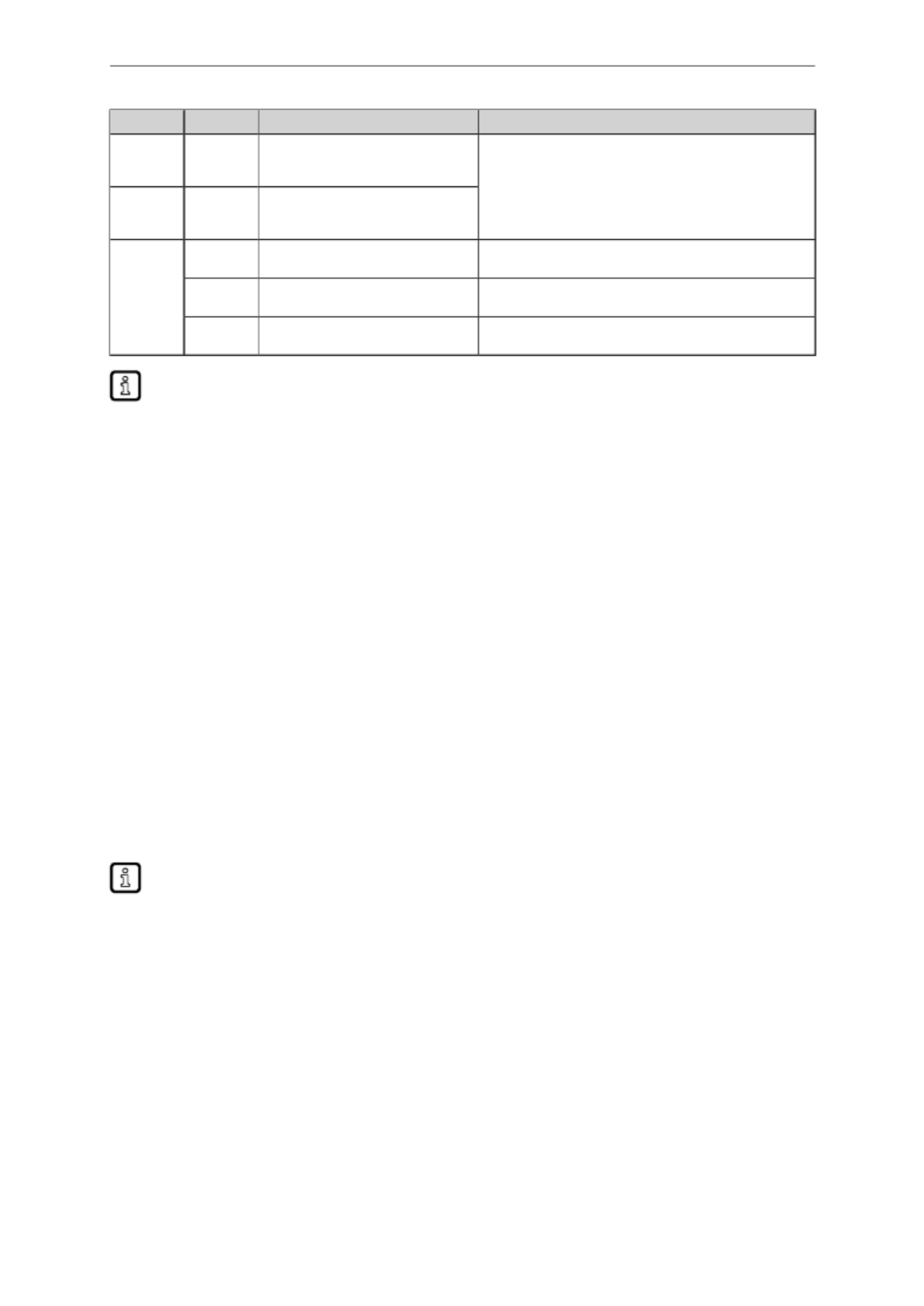
SMFxxx Magnetic-inductive flow meter
44
[FOU2] [SEL2] Output signal Explanation
ON FLOW
TEMP
COND
In case of an error the output goes to
21.5mA.
As soon as a defective process value is present, the device
sets all process values to invalid.
OFF FLOW
TEMP
COND
In case of an error the output goes to
3.5mA.
OU FLOW In case of an error the output goes to
3.5mA.
If the process value “Flow” is defective, the device contin-
ues to provide the other process values.
TEMP In case of an error the output goes to
21.5mA.
If the process value “Temperature” is defective, the device
continues to provide the other process values.
COND In case of an error the output goes to
3.5mA.
If the process value “Conductivity” is defective, the device
continues to provide the other process values.
The parameter [FOU] has no influence on the pulse signal, the diagnostic switching signal and
the IO-Link process data transmission.
10.4.3.1 Parameter setting via unit keys: Error behaviour of the outputs
üThe output function [I] = analogue signal is selected for OUT2: > [OUT2] > [ou2].
uGo to menu > [OUT2].
uSelect [FOU2] and set the error behaviour for output OUT2.
10.4.3.2 Parameter setting via IO-Link: Error behaviour of the outputs
uCall up [Parameters] > [Output Configuration].
uSelect [FOU2] and set the error behaviour for output OUT2.
10.4.4 Damping
The set damping constant stabilises the output signals. Abrupt changes in the physical process values
are smoothed out.
This concerns the switching outputs, the display and the process value transmission via the IO-Link
interface.
The damping constant is added to the response time of the sensor ( Technical data).Ò
The UL and OL signals are defined under consideration of the damping time.
Measured value damping only has an effect on the measured variable flow.
10.4.4.1 Parameter setting via unit keys: Measured value damping
uGo to menu [Settings] > [CFG].
uSelect [dAP.F] and set the damping time in seconds (τ value 63%).
10.4.4.2 Parameter setting via IO-Link: Measured value damping
uCall up [Parameters] > [Damping].
uSelect [dAP.F] and set the damping time in seconds (τ value 63%).
10.4.5 Low flow cut-off
With the low flow cut-off [LFC] function it is possible to suppress low consumed quantities. Flow below
the LFC value is evaluated by the sensor as standstill (Q = 0).
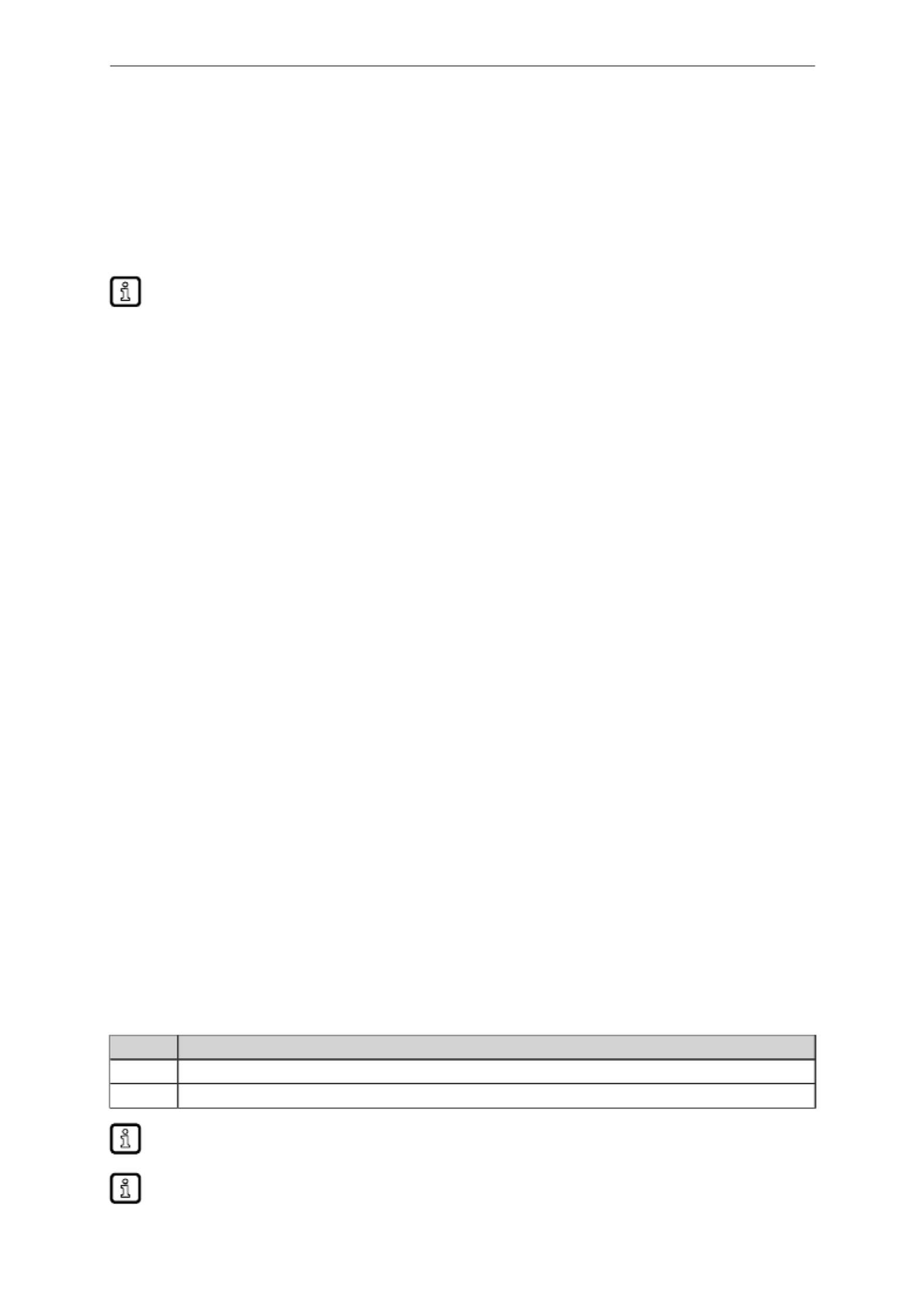
Magnetic-inductive flow meter SMFxxx
45
The LFC value influences:
• the process value for flow shown on the display
• the digital switching signal for flow
• the analogue signal for flow
• the consumed quantity monitoring (switching or pulse signal for flow)
• the memory values for minimum and maximum flow
The accuracy indicated in the data sheet applies to the factory-set LFC value. If a lower LFC
value is set, the accuracy of the sensor will decrease.
10.4.5.1 Parameter setting via unit keys: low flow cut-off
uGo to menu [Settings] > [CFG].
uSelect [LFC] and set the limit below which a flow is evaluated as standstill.
10.4.5.2 Parameter setting via IO-Link: low flow cut-off
uSelect [Parameter] > [Other settings] > [Flow].
uSelect [LFC] and set the limit below which a flow is evaluated as standstill.
10.4.6 Output polarity
The parameter [P-n] can be used to select whether the outputs are positive switching or negative
switching.
10.4.6.1 Parameter setting via unit keys: Output polarity
uGo to menu [Settings] > [CFG].
uSelect [P-n] and set [PnP] or [nPn].
10.4.6.2 Parameter setting via IO-Link: Output polarity
uSelect [Parameters] > [Basic settings].
uSelect [P-n] and set [PnP] or [nPn].
10.4.7 Flow direction
The positive flow direction can be defined by the user. This setting affects the following functions:
• Consumed quantity monitoring
• Flow direction monitoring via switching signal
An arrow with the text “flow direction” on the device indicates the positive flow direction (factory
setting). The direction of the flow rate measurement can be reversed using the parameter [Fdir]:
[Fdir] Direction of flow
+ Flow direction in case of factory setting
- Flow direction contrary to the factory setting
uUse the supplied label to mark the changed flow direction (new positive flow direction) on the
device.
The flow direction that is currently indicated as positive can be viewed on the display (Ò
Operating and display elements 22)/.
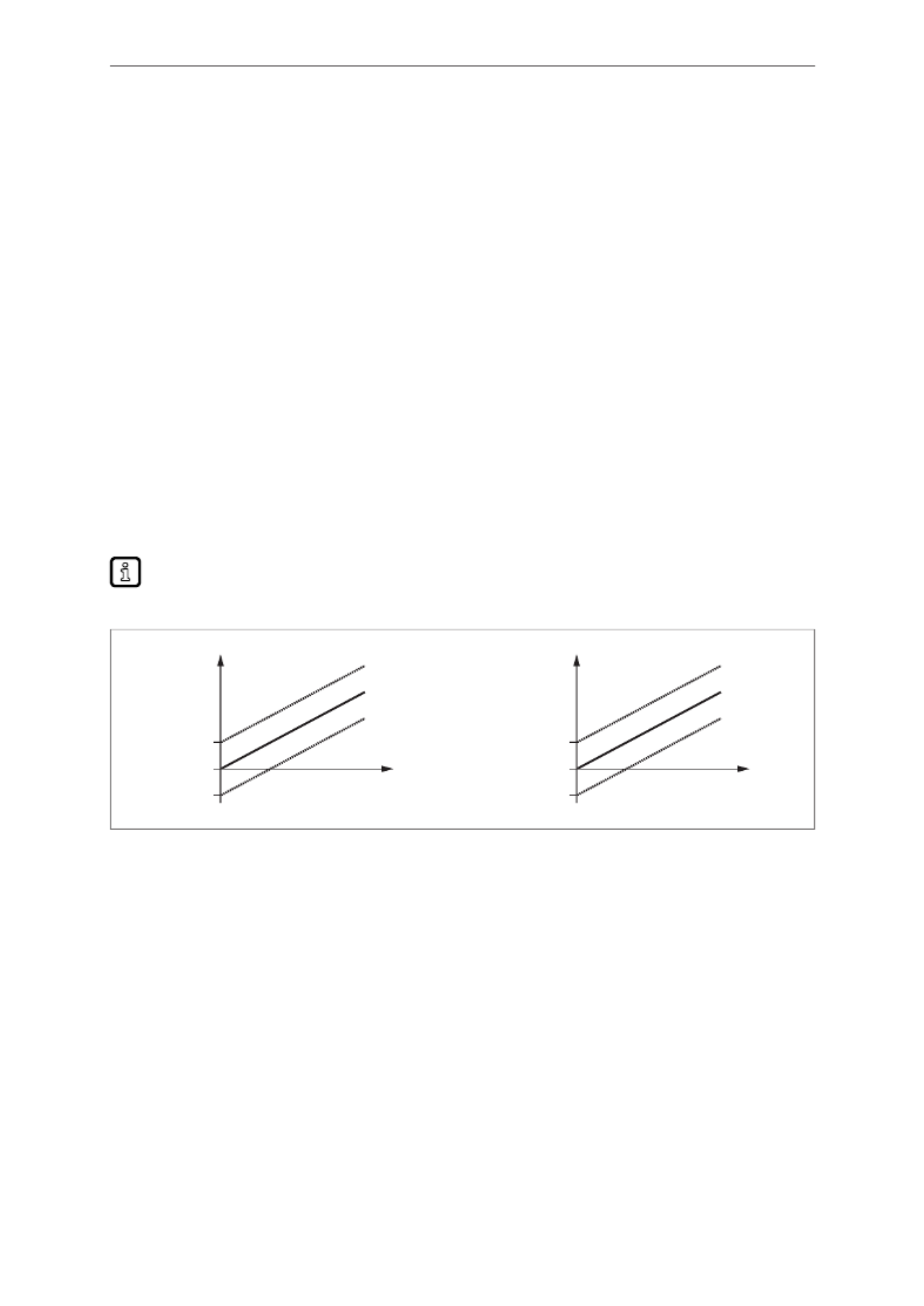
SMFxxx Magnetic-inductive flow meter
46
See also: .Switching signal for flow direction ( 35)Ò/
10.4.7.1 Parameter setting via unit keys: flow direction
uGo to menu [Settings] > [CFG].
uSelect [Fdir] and set the direction of media flow.
10.4.7.2 Parameter setting via IO-Link: flow direction
uSelect [Parameter] > [Other settings] > [Flow].
uSelect [Fdir] and set the direction of media flow.
10.4.8 Zero calibration
The combination of display unit (converter) and measuring circuit can lead to measurement
inaccuracies, particularly depending on the respective ambient conditions.
If there is a systematic deviation between the measured value and the actual process value, this
measurement inaccuracy can be corrected using the correction factor [coF.x].
• [coF.F] = correction factor for measuring flow
• [coF.C] = correction factor for measuring conductivity
The unit of measurement for [coF.F] and [coF.C] is the set standard unit of measurement for the
process values flow and conductivity .
( Standard unit of measurement 42)Ò/
The internal zero point is shifted by the set value.
t
MEW
[µS/cm]
5 000
-5 000
0
V1
V0
V2
MEW
[%]
t
10
0
-10
V1
V0
V2
Fig.28: Zero-point calibration (calibration offset)
MEW: Final value of the measuring range
t: time
V0: Curve of measured values at factory setting
V1: Curve of measured values after offset
V2: Curve of measured values after offset
Factory calibration:
The sensor is calibrated for flow measurement at the factory.
The correction factor used to calibrate the device in the factory can be read via the [OF] parameter on
the display or via the IO-Link interface and cannot be configured.
The correction factor (offset value) is also listed in the calibration certificate.
Reading the factory-set correction factor via the device keys:
uGo to [Device information] menu and read [OF].
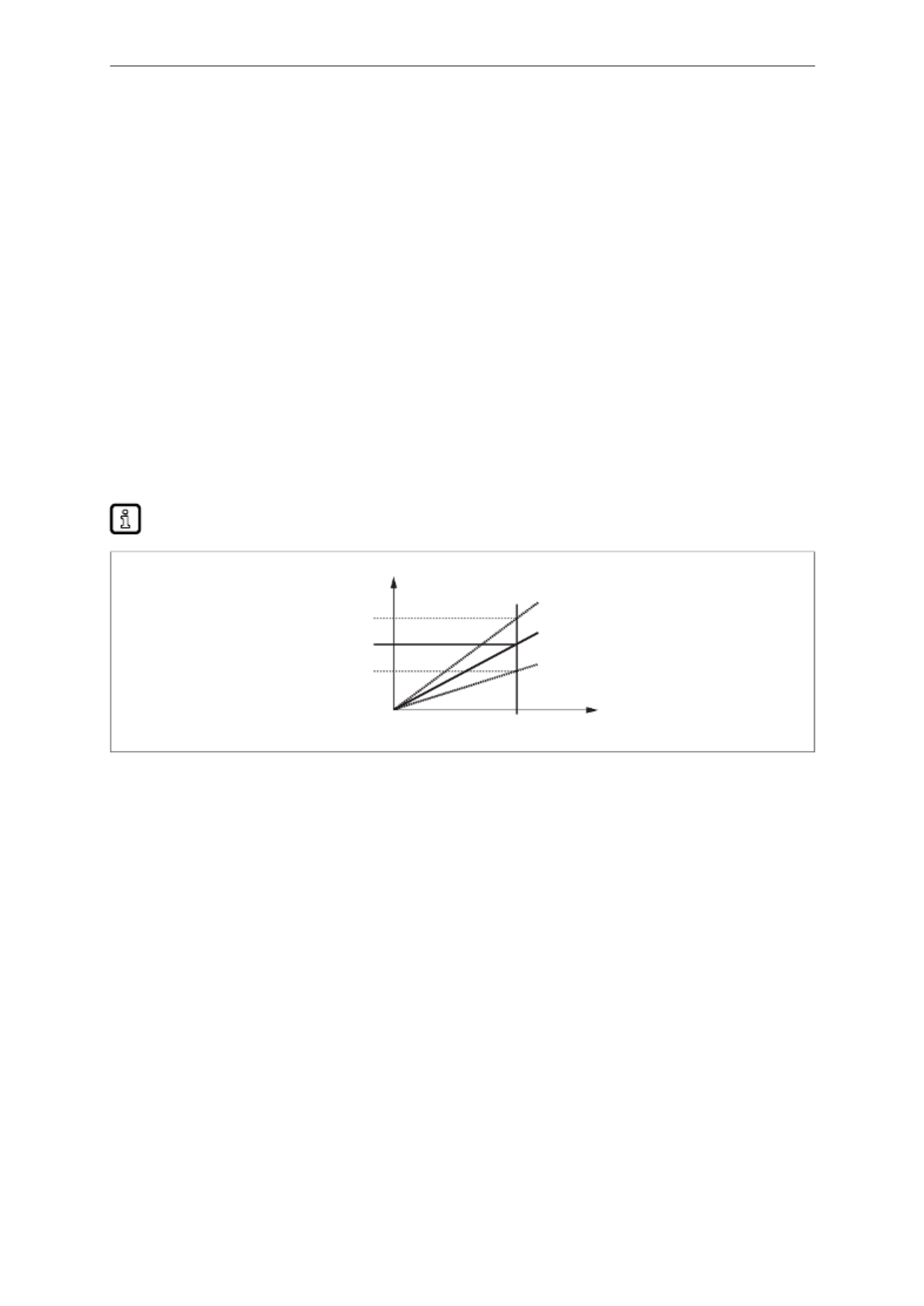
Magnetic-inductive flow meter SMFxxx
47
10.4.8.1 Parameter setting via unit keys: Zero calibration
uGo to menu [Settings] > [CFG] > [CAL].
uSelect [CoF] and set the correction factor.
10.4.8.2 Parameter setting via IO-Link: Zero calibration
uSelect [Parameter] > [Application].
uGo to [Flow] or [Conductivity].
uSelect [coF-FLOW] for flow or [coF-COND] for conductivity and set the value.
10.4.9 Calibration of the measurement characteristic
The calibration factor [CGA.x] is used to adjust the temperature-viscosity compensation of the sensor
to the characteristics of the medium used. The calibration factor influences the gradient of the flow
measurement characteristic.
• [CGA.F] = calibration factor for measuring flow
• [CGA.C] = calibration factor for measuring conductivity
The slope modification of the measurement characteristic is indicated in per cent. The factory
setting is [CGA]=100%. After a change the calibration can be reset to factory setting.
MW
CGA
150 %
V1
V0
V2
100 %
50 %
Fig.29: Calibration of the measurement characteristic
MW: Measured value
V0: Measurement characteristic at factory setting
V1: Measurement characteristic after offset by +50%
V2: Measurement characteristic after offset by -50%
Factory calibration:
The sensor is calibrated for flow measurement at the factory.
The calibration factor that was used to calibrate the device in the factory can be read via the [CF]
parameter on the display or via the IO-Link interface and cannot be configured.
The calibration factor is also listed in the calibration certificate.
Reading via the device keys:
uGo to [Device information] menu and read [CF].
10.4.9.1 Parameter setting via unit keys: calibration
uGo to menu [Settings] > [CFG] > [CAL].
uSelect [CGA] and set the slope of the measuring characteristic in per cent.
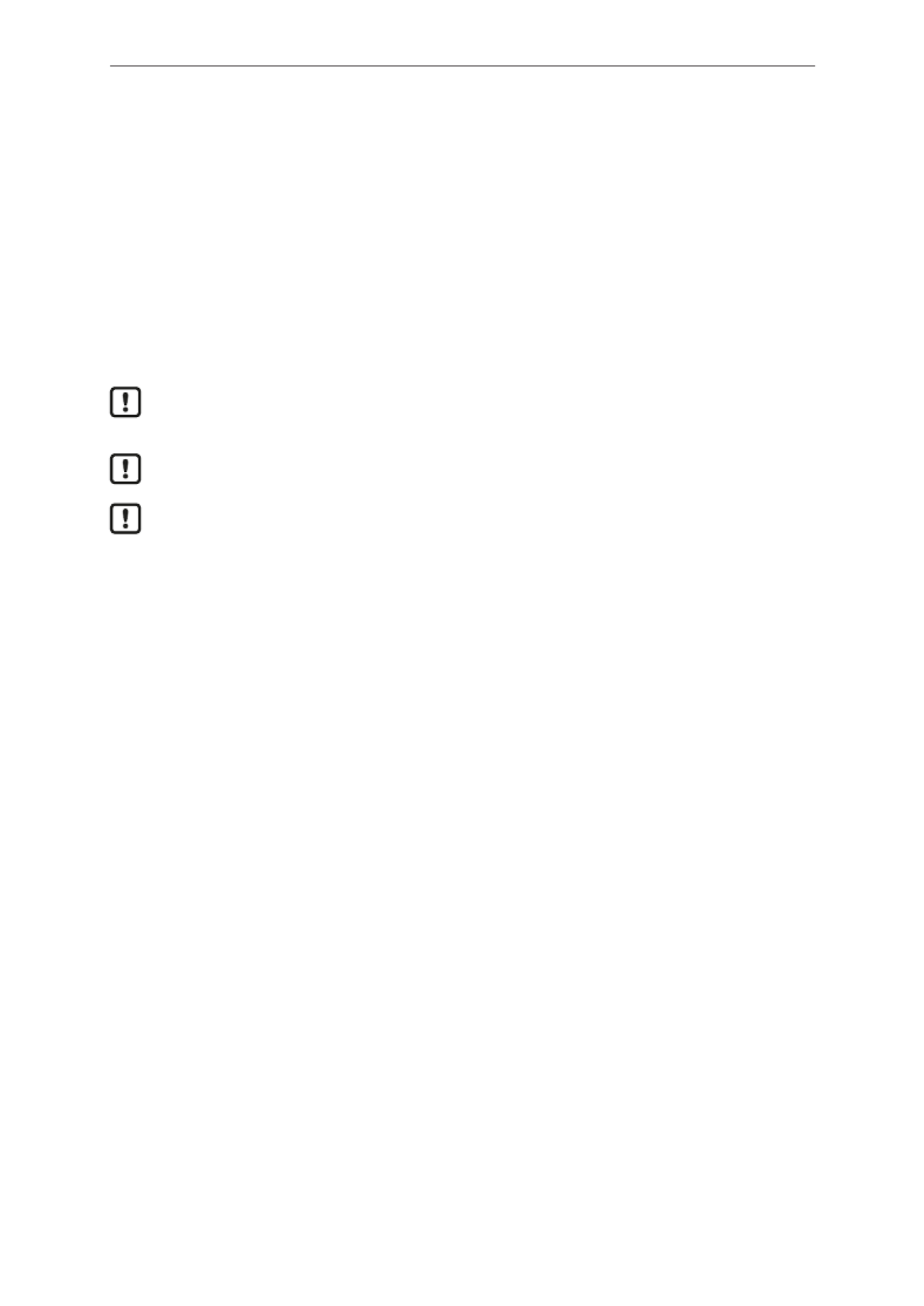
SMFxxx Magnetic-inductive flow meter
48
10.4.9.2 Parameter setting via IO-Link: calibration
uSelect [Parameter] > [Application].
uselect [CGA-FLOW] for flow or [CGA-COND] for conductivity and set the gradient of the
measurement characteristic in %.
10.4.10 Influence of the medium on the temperature
The conductivity depends on the temperature. When the temperature increases, the conductivity
changes. This temperature influence depends on the respective medium and can be compensated by
the unit if the temperature coefficient (tempco) of the medium is known. The temperature
compensation is set via the parameter [T.Cmp]. Then the temperature-compensated conductivity
value corresponds to the conductivity at standard temperature (25 °C; factory setting of the parameter
[rEF.T]).
For medium that is not changed the same tempco value has to be set for all sensors (unit-
independent characteristic value). There is no further dependence on the measuring principle,
the lot or the manufacturer of the sensors.
If the temperature coefficient of the medium is not known, it can be determined.
See: Determination of the temperature coefficient tempco ( 48)Ò/
In an IO-Link environment, existing tempcos of the media can be stored as recipe in the
controller so that the accuracy of the values to be detected is improved.
10.4.10.1 Determination of the temperature coefficient tempco
1. Set the parameters [T.Cmp] and [dAP] to zero: [T.Cmp] = [0], [dAP] = [0].
uWrite the changed values to the sensor.
1. Adjust the medium to 25 °C, for example, and take down
the value of the conductivity after 2 min.
2. Heat up the medium to 45°C, for example, and take down
the value of the conductivity after 2min.
Example of values taken down:
Medium at 25°C = 500 µS/cm; medium at 45°C = 800 µS/cm
Temperature change = 20 K
1. Calculate the change of the conductivity in percent.
The conductivity has increased by 300µS/cm.
The percentage change is 300/500 = 60%.
2. Calculate the temperature coefficient tempco: The tempco is calculated from the change in percent
and the temperature change: Tk = 60 % / 20 K = 3 % / K
3. The calculated tempco can now be adopted into the parameter [T.Cmp].
Example: [T.Cmp] = [3]. If necessary, set the damping (parameter [dAP]) again.
uWrite values to the sensor.
10.4.10.2 Parameter setting via the device keys: Temperature compensation
uGo to menu [Settings] > [CFG] > [CAL].
uSelect [T.Cmp] and set the temperature coefficient of the medium.
uSelect [rEF.T] and enter the standard temperature.
10.4.10.3 Parameter setting via IO-Link: Temperature compensation
uSelect [Parameter] > [Application].
uSelect [T.Cmp] and set the temperature coefficient of the medium.
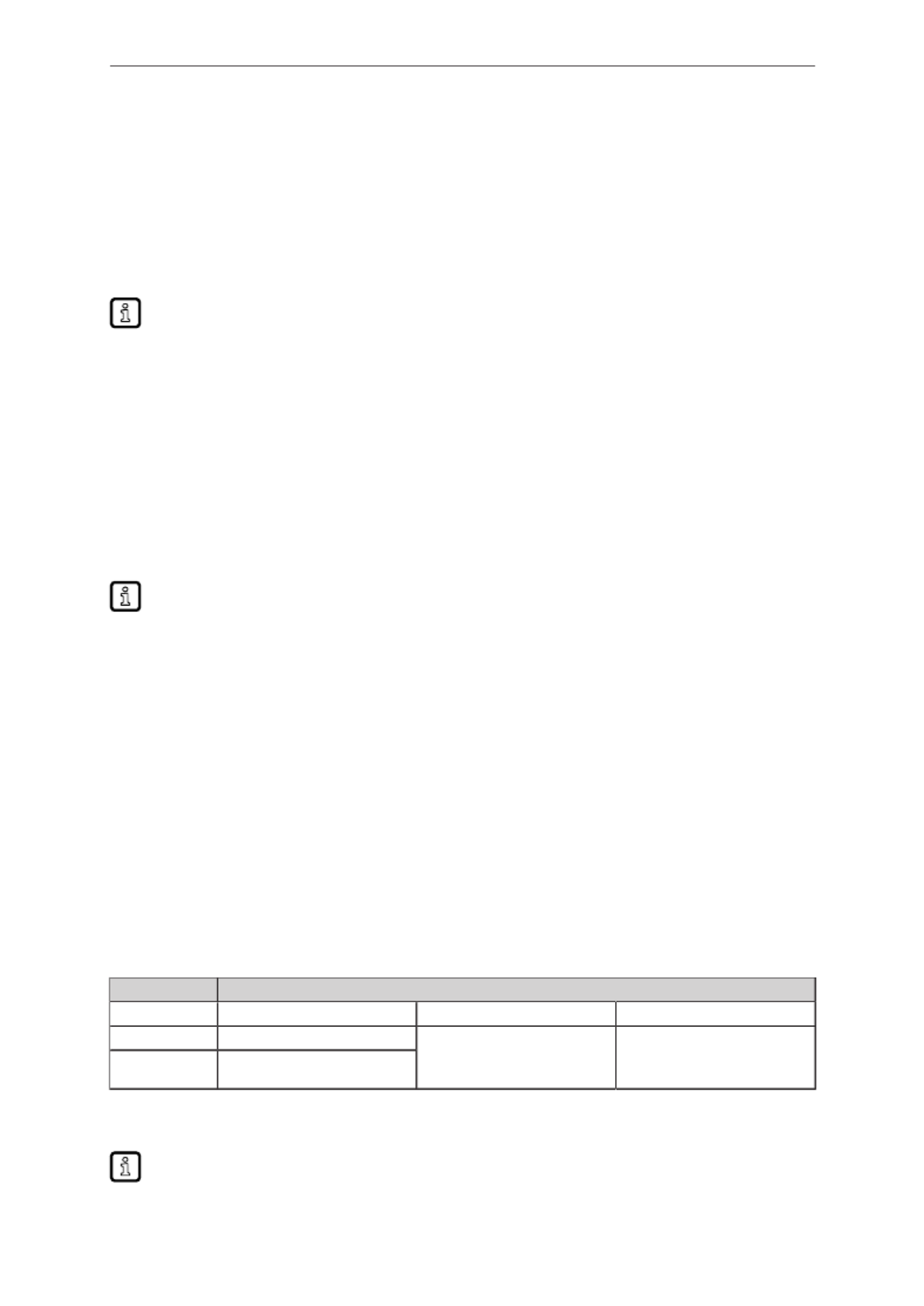
Magnetic-inductive flow meter SMFxxx
49
uGo to [Temperature].
uSelect [rEF.T] and enter the standard temperature.
10.4.11 Date/time
Setting the date and time serves to provide events and measurements with a time stamp.
For this, the date and time must be set during set-up. When setting the time, wither a 12hr or 24hr
format can be chosen. If the time is not set, the clock will start from an initial value (2024/01/01).
The device contains an internal energy storage unit so that, in the event of a power failure, the
settings are saved for a transitional period. If the power supply is interrupted for too long, the
display will show the symbol and the message that the date and time are no longer set.
uReset the date and time.
10.4.11.1 Parameter setting via the device keys: Date/time
uGo to menu [Settings] > [CFG].
uSelect [Date] and set the date and time:
• Date: year, month, day
• Clock format: 24h or 12h
• Time: hour, minute
uChange numerical value changes with [▼] or [▲].
uConfirm numerical value and jump to next setting with [●].
10.4.11.2 Parameter setting via IO-Link: Date/time
uSelect [Parameters] > [Basic settings].
uSet the [date and time].
uSelect [Set time] and [yes].
uSelect [time format]: [24h] or [12h].
10.4.12 Energy-saving mode
The device can be operated in energy-saving mode.
The [Eco mode] parameter can be used to select between two energy-saving levels: [Eco] and [Eco+].
The energy-saving mode is switched off via the [OFF] setting.
Both energy-saving modes can be configured via the parameters [dis.B.Eco] and [LED.M.ECO]. In
[Eco+] mode, the measuring rate can also be set.
[Eco-Mode] Setting options for the energy-saving mode
[Measuring Rate Eco] [diS.B.Eco] [LED.M.ECO]
[Eco] ---- 25 %, 50%, 75%, 100%, OFF On, OFF, Noti, PdOU, PArA
See Operating status LED
( 60)Ò/
[Eco+] Current measuring rate*: 60…900
s
Tab.11: Setting options for the two energy-saving modes.
* The accuracy indicated in the data sheet applies to the factory settings. Changing the measuring rate in [Eco+] mode has a
direct impact on the sensor’s measurement accuracy.
If [Eco mode] = [OFF] is set, the general settings for and
Display brightness ( 55)Ò/
Operating status LED ( 60)Ò/ apply.
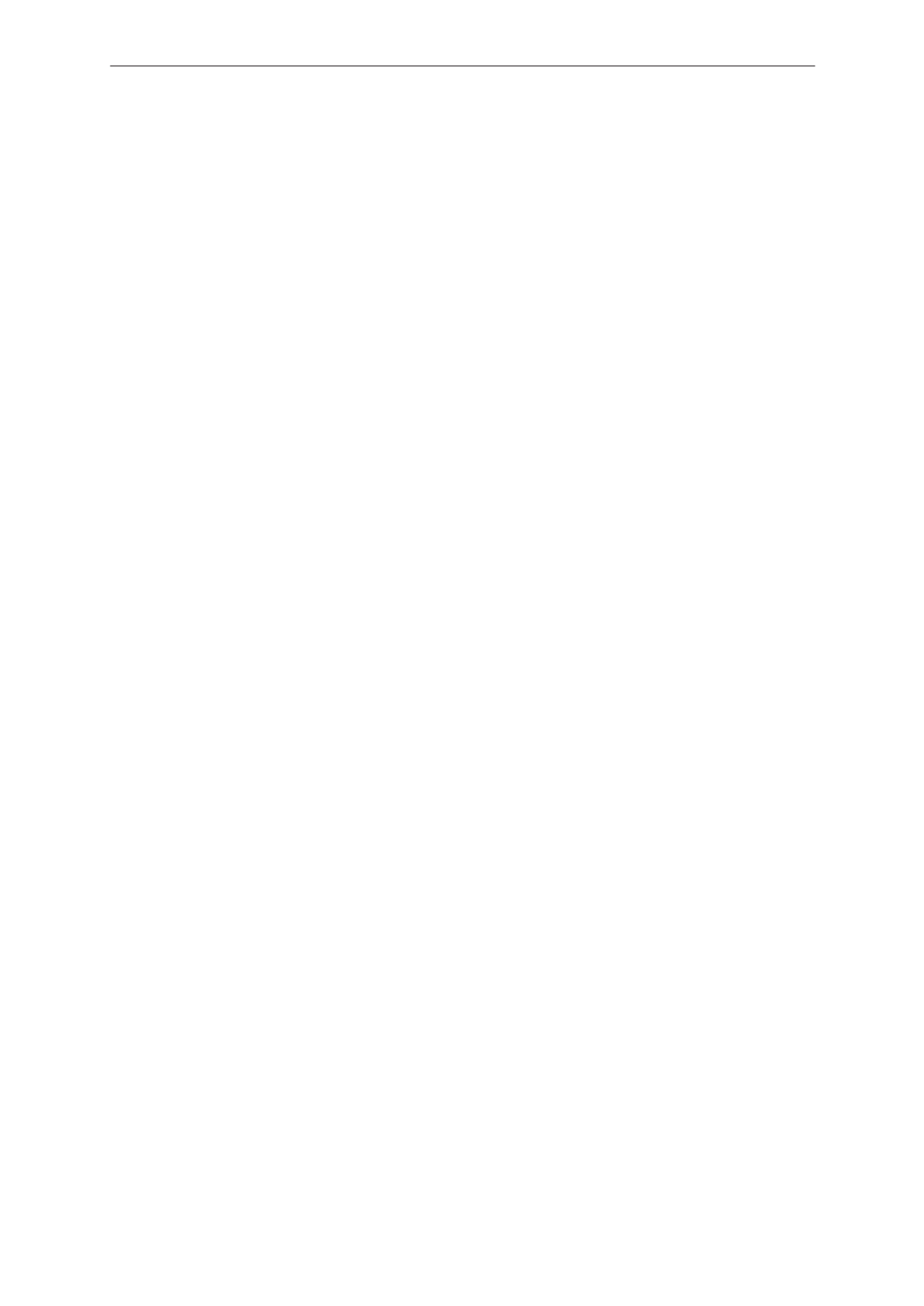
SMFxxx Magnetic-inductive flow meter
50
10.4.12.1 Parameter setting via the device keys: Energy-saving mode
uGo to menu [Settings] > [CFG].
uSelect [Eco-mode]: [OFF], [Eco] or [Eco+].
uSelect [diS.B.ECO] and set the display brightness: [25%], [50%], [75%], [100%],[OFF].
uSelect [LED.M.ECO] and select the display options for the operating status LED: [On], [OFF],
[Notification], [PArA], [PdOU].
Only if [Eco+] is selected
uSelect [Measuring RateECO] and set the measuring rate.
10.4.12.2 Parameter setting via IO-Link: Energy-saving mode
uGo to [Parameters] > [Configuration] > [energy-saving mode].
uSelect [Eco-mode]: [OFF], [Eco] or [Eco+].
uSelect [diS.B.ECO] and set the display brightness: [25%], [50%], [75%], [100%],[OFF].
uSelect [LED.M.ECO] and select the display options for the operating status LED: [On], [OFF],
[Notification], [PArA], [PdOU].
Only if [Eco+] is selected
uSelect [Measuring RateECO] and set the measuring rate.
10.4.13 Totaliser reset
The totalisers Vol.1 and Vol.2 can be reset in different ways:
1. manual reset
2. time-controlled reset
3. reset via external signal
4. reset via overflow (maximum display range is reached).
Totaliser Vol.L cannot be reset.
10.4.13.1 Parameter setting via unit keys: Totaliser reset
1. Manual reset:
uGo to menu [Settings] > [TOTL].
uSelect [rTox] and set [rES.T].
wThe totaliser is reset.
2. Time-controlled reset:
uGo to menu [Settings] > [TOTL].
uSelect [rTox], then set time in weeks (w), days (d) or hours (h).
wThe totaliser is automatically reset after the set time.
3. Reset via external signal:
uGo to menu [Settings] > [OUT2].
uSelect [ou2] and set digital input: [DIn2].
uSelect [DIn2] and set the reset signal:
• [HIGH]: reset for high signal
• [LOW]: reset for low signal
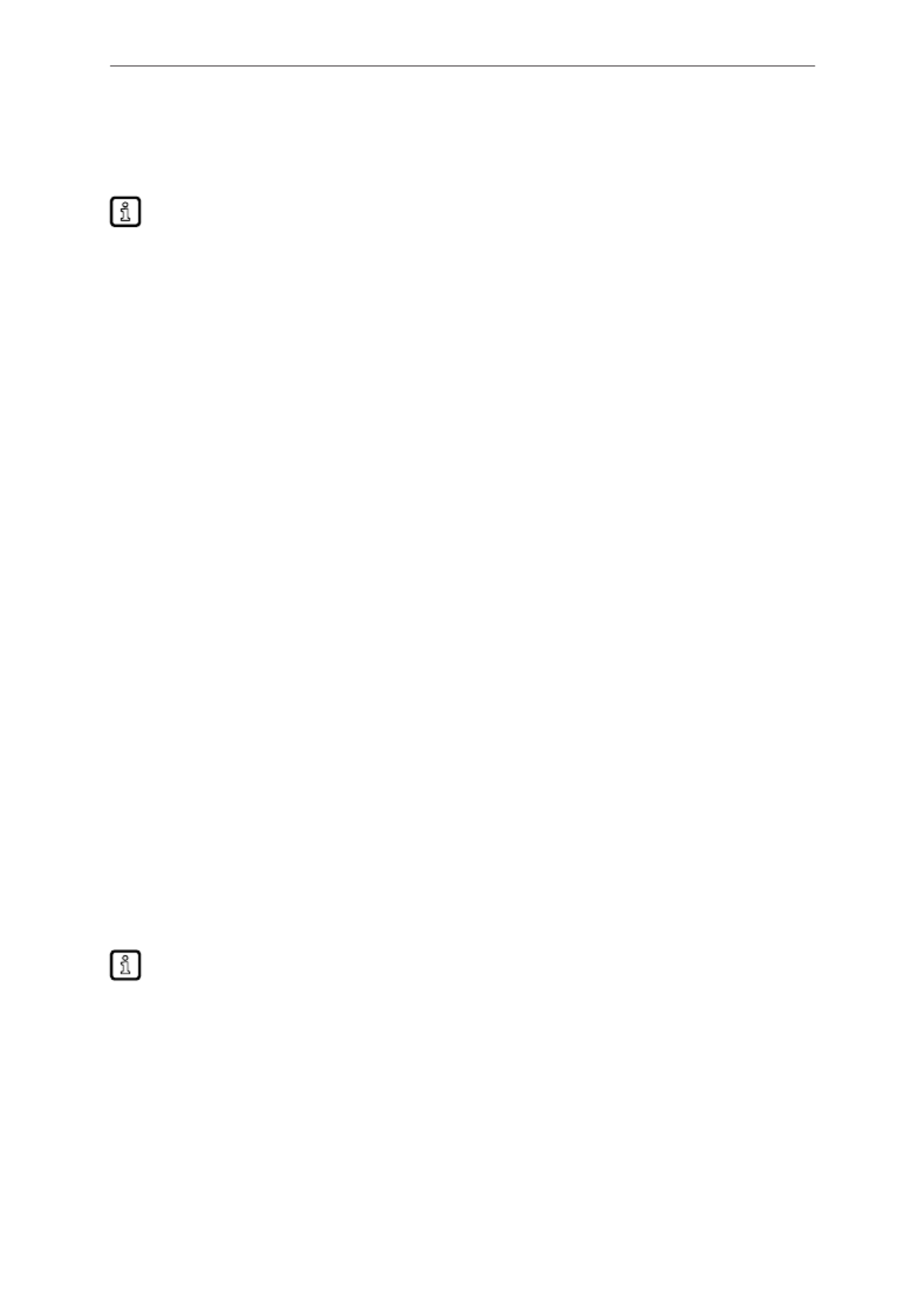
Magnetic-inductive flow meter SMFxxx
51
• [+EDG]: reset for rising edge
• [–EDG]: reset for falling edge
> The totaliser Vol.1 is reset when receiving the reset signal via pin 2.
An external reset is only possible for totaliser Vol.1.
4. Reset via overflow:
uGo to menu [Settings] > [TOTL].
uSelect [rTox] and set [OFF].
wThe totaliser is reset as soon as the maximum display range is exceeded.
10.4.13.2 Parameter setting via IO-Link: totaliser reset
1. Manual reset:
uSelect [Parameter] > [Totaliser].
uExecute command:
• [totaliser 1 reset]
• [totaliser 2 reset]
2. Time-controlled reset:
uSelect [Parameter] > [Totaliser].
uSelect [rTox], then set time in weeks (w), days (d) or hours (h).
wThe totaliser is automatically reset after the set time.
3. Reset via external signal:
uCall up [Parameters] > [Output Configuration].
uSelect [ou2] and set digital input: [In.D].
uSelect [Parameters] > [Digital input 2].
uSelect [DIn2] and set the reset signal:
• [HIGH]: reset for high signal
• [LOW]: reset for low signal
• [+EDG]: reset for rising edge
• [–EDG]: reset for falling edge
> The totaliser Vol.1 is reset when receiving the reset signal via pin 2.
An external reset is only possible for totaliser Vol.1.
4. Reset via overflow:
uSelect [Parameter] > [Totaliser].
uSelect [rTox] and set [OFF].
wThe totaliser is reset as soon as the maximum display range is exceeded.
10.4.14 Counting method of the totalisers
The totalisers Vol.1 and Vol.2 take account of the flow direction when totalising the consumed
quantity. The following counting methods can be defined via the parameter [FProx]:
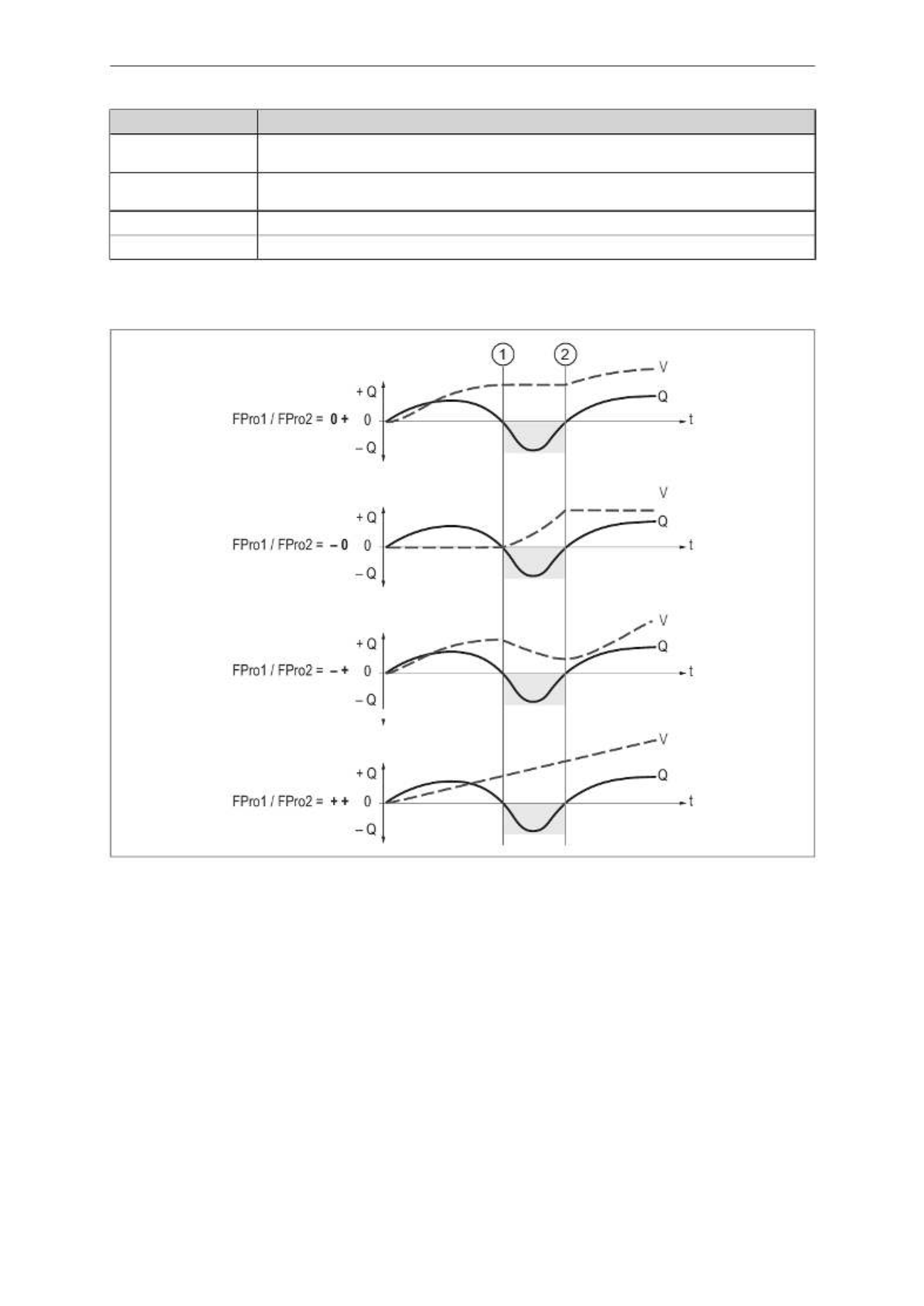
SMFxxx Magnetic-inductive flow meter
52
[FProx] Counting method
0+ Negative volumetric flow values (against the marked flow direction) are not taken into account for
totalling.
-0 Positive volumetric flow values (corresponding to the marked flow direction) are not taken into ac-
count for totalling.
-+ Negative flow values are subtracted from the consumed quantity.
++ All volumetric flow values are totalled irrespective of the volumetric flow direction.
Tab.12: Counting method of the totalisers
The counting method of Vol.L cannot be set. The lifetime totaliser totals all volumetric flow quantities
irrespective of the flow direction.
Fig.30: taking account of the volumetric flow direction when totalling the consumed quantity
+Q: volumetric flow quantity in positive direction
-Q: volumetric flow quantity in negative direction
V: volumetric flow quantity absolute (= sum of negative and positive volumetric flow)
1: volumetric flow changes to negative direction
2: volumetric flow changes to positive direction
When the volumetric flow direction is changed a minimum volumetric flow quantity is taken into
account. See Switching signal for flow direction.
10.4.14.1 Parameter setting via unit keys: counting method of the totalisers
uGo to menu [Settings] > [TOTL].
uSelect [FPro1] and set the counting method for totaliser Vol.1.
uSelect [FPro2] and set the counting method for totaliser Vol.2.
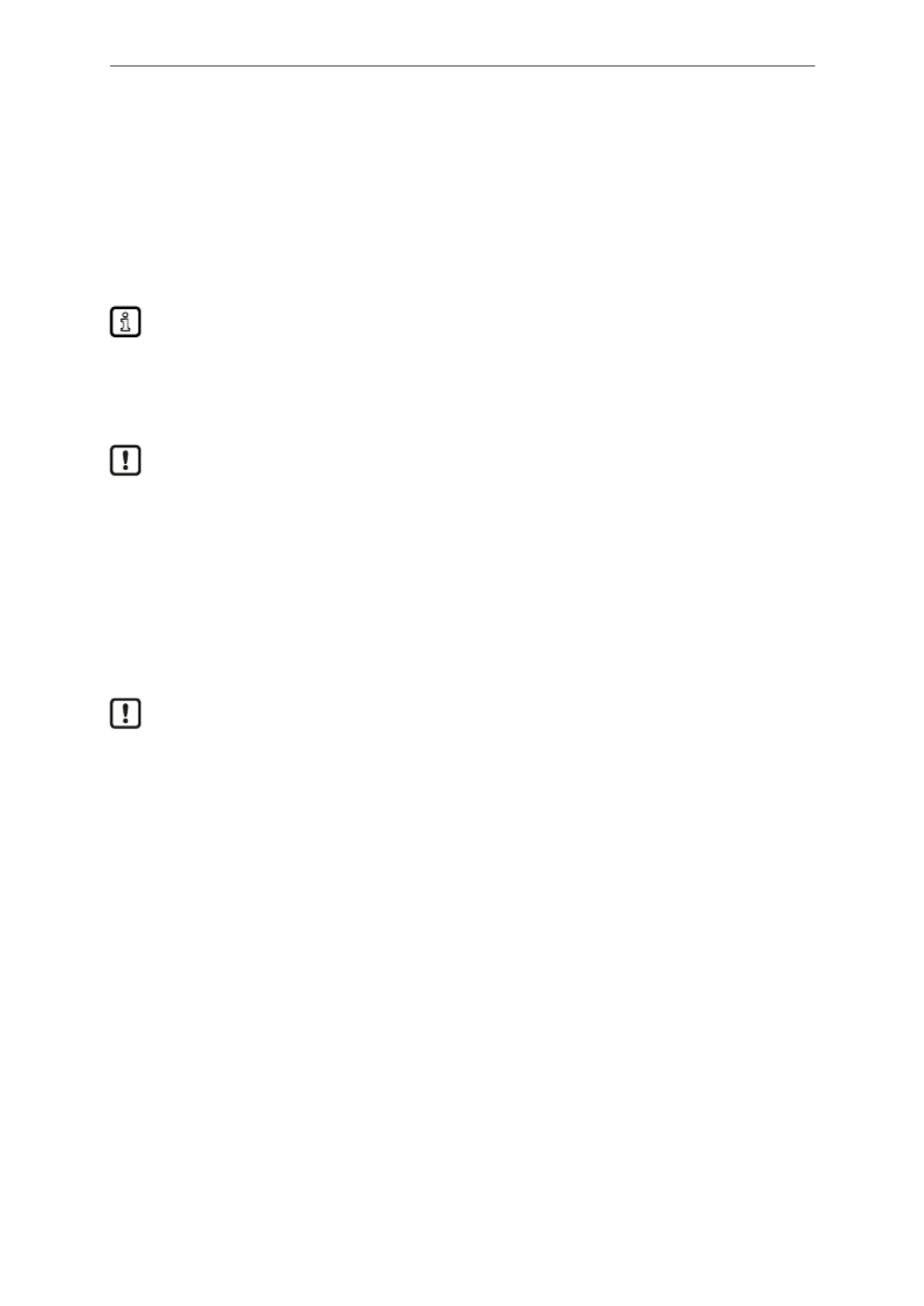
Magnetic-inductive flow meter SMFxxx
53
10.4.14.2 Parameter setting via IO-Link: counting method of the totalisers
uSelect [Parameter] > [Totaliser].
uSelect [FPro1] and set the counting method for totaliser Vol.1.
uSelect [FPro2] and set the counting method for totaliser Vol.2.
10.4.15 Reset the device
The device can be reset in two ways.
With both reset applications, the operating hours since the first set-up are not reset.
[APPL] = application reset
The following is reset:
• All changed application-specific parameters
If IO-Link data storage is activated, this triggers a parameter update in the master. This writes
the parameters configured in the master to the device again. An application reset may therefore
be ineffective.
[BtB] = Back to Box
The following is reset:
• All changed application-specific parameters
• All writeable unit identification parameters such as [Application Specific Tag], [Function Tag] or
[Location Tag].
• Diagnostic parameters, status parameters, events.
• Minimum and maximum memory value
After the Back to Box reset, the sensor suspends communication and measurement operation
until the voltage is interrupted. The IO-Link data storage is not triggered.
10.4.15.1 Resetting the device using device keys
uGo to menu [Settings] > [CFG] > [rES].
uSelect [APPL] or [BtB] and set [Yes].
Only if [BtB] is selected:
uDisconnect and reconnect the voltage supply.
wThe device carries out a reboot.
10.4.15.2 Resetting the device via IO-Link
uSelect [Parameters] > [Basic settings].
uExecute command: [Application reset] or [Back to Box].
Only if BtB is selected:
uDisconnect and reconnect the voltage supply.
wThe device carries out a reboot.
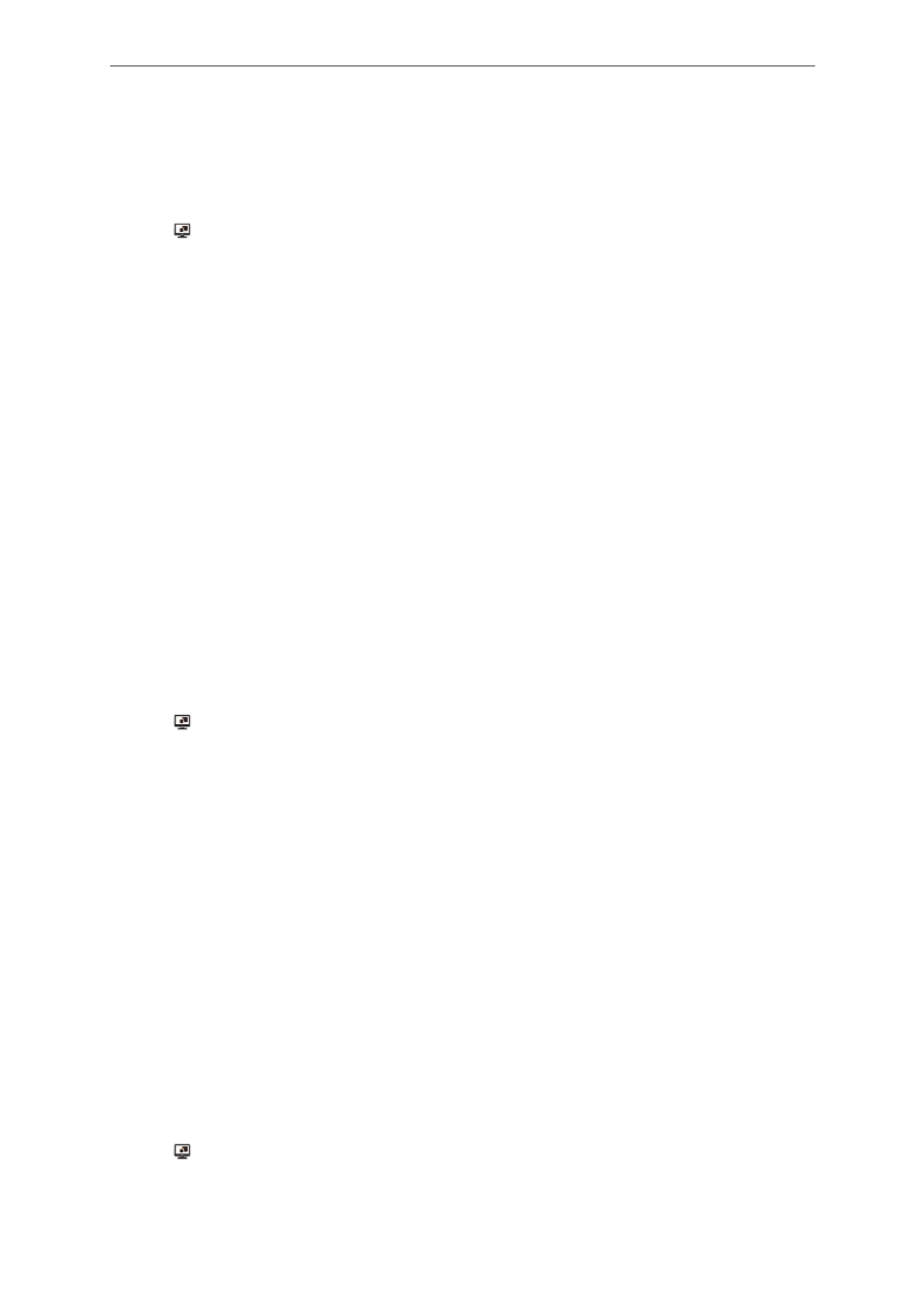
SMFxxx Magnetic-inductive flow meter
54
10.5 Display settings
The presentation in the display can be adjusted via various parameters. The parameters described
below are set as follows:
Parameter setting via the device keys:
uGo to menu [Display].
Parameter setting via IO-Link:
uCall up [Parameters] > [Display Setting].
10.5.1 Display language
The display language can be set via the parameter [LanG].
Selectable languages:
• DE: German
• EN: English
• ES: Spanish
• FR: French
• IT: Italian
• JA: Japanese
• KO: Korean
• PT: Portuguese
• ZH: Chinese
10.5.1.1 Parameter setting via unit keys: display language
uGo to menu [Display].
uSelect [LanG] and set the language.
10.5.1.2 Parameter setting via IO-Link: display language
uSelect [Parameters] > [Basic settings].
uSelect [LanG] and set the language.
10.5.2 Display rotation
Use the parameter [diS.R] to rotate the text in the display clockwise for better readability.
Selectable values:
• 0° (not rotated)
• 90°
• 180°
• 270°
10.5.2.1 Parameter setting via unit keys: display rotation
uGo to menu [Display].
uSelect [diS.R] and set the display rotation.
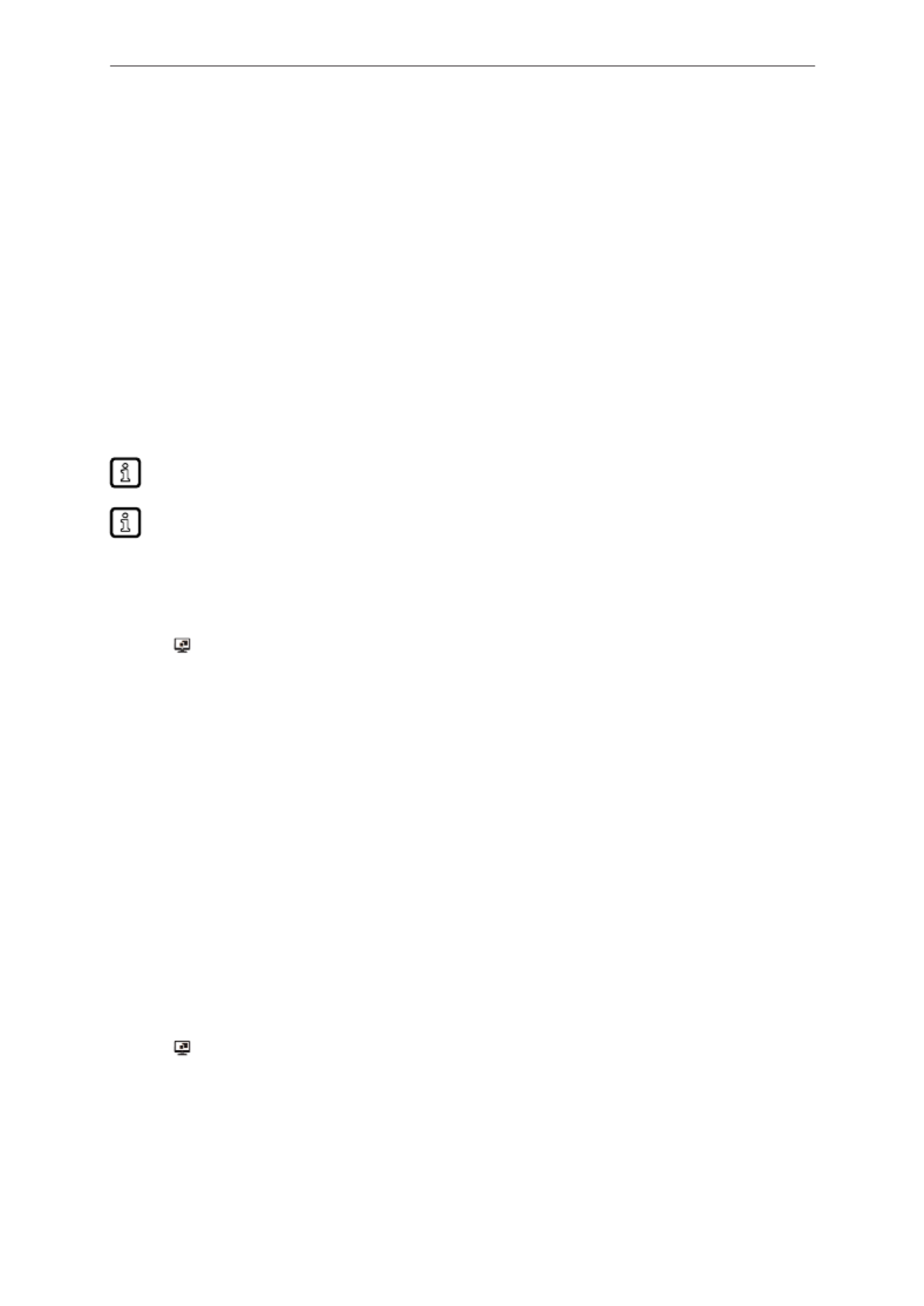
Magnetic-inductive flow meter SMFxxx
55
10.5.2.2 Parameter setting via IO-Link: display rotation
uCall up [Parameters] > [Display Setting].
uSelect [diS.R] and set the display rotation.
10.5.3 Display brightness
The display brightness can be set via the parameter [diS.B].
Selectable values:
• 25%
• 50%
• 75%
• 100%
• OFF: energy-saving mode. the display is switched off in the operating mode.
Display activation by pressing any key. After 30s of inactivity, the display is switched off again.
In case of warnings or error messages and in case of optical localisation, the display will come
back on even with the setting [OFF].
If the device measures a high internal temperature, the display brightness is automatically
adjusted:
Internal temperature >75°C: brightness is reduced to 25%.
Internal temperature≥90°C: display is automatically switched off.
10.5.3.1 Parameter setting via unit keys: display brightness
uGo to menu [Display].
uSelect [diS.B] and set the brightness of the display.
10.5.3.2 Parameter setting via IO-Link: display brightness
uCall up [Parameters] > [Display Setting].
uSelect [diS.B] and set the brightness of the display.
10.5.4 Display update rate
The update rate of the display can be set via the parameter [diS.U].
Selectable values:
• d1: fast
• d2: medium
• d3: slow
10.5.4.1 Parameter setting via unit keys: display update rate
uGo to menu [Display].
uSelect [diS.U] and set the update rate.
10.5.4.2 Parameter setting via IO-Link: display update rate
uCall up [Parameters] > [Display Setting].
uSelect [diS.U] and set the update rate.
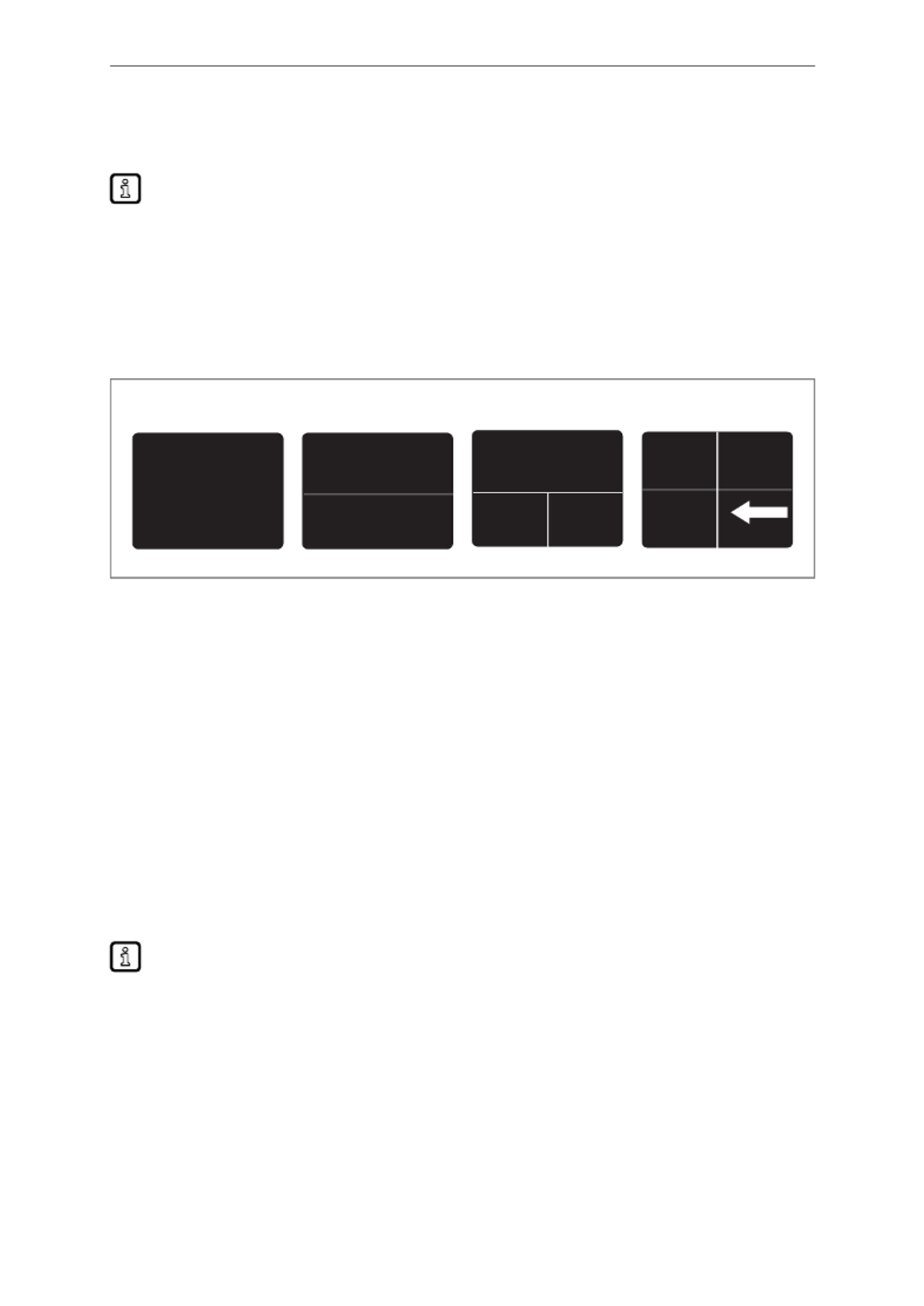
SMFxxx Magnetic-inductive flow meter
56
10.5.5 Display layout
The standard display can be set via the parameter [diS.L].
This function is only available via the IO-Link interface or the wizard.
A maximum of four of the following display screens can be selected:
• Process value: current flow
• Process value: current consumed quantity (totaliser)
• Process value: current temperature
• Process value: current conductivity
• Displays the flow direction defined as positive ( Flow direction 45)Ò/
107.05
l/min Flow
107.05
l/min
Flow
11.532
l
Totalizer
107.05
l/min
4.300
µS/cm
Conductivity
33.0
°C
Temperature
Flow
107.05
l/min
Flow
11.532
l
Totalizer
33
°C
Temperature Flow direction
L1 L2 L3 L4
Fig.31: Display layouts
10.5.5.1 Parameter setting via the device keys: Display layout
uGo to menu [Settings] > [CFG].
uSelect [Wizard].
uPress [●] until the device requests that the display layout be set.
uDetermine number of process values, main process value and other process values.
10.5.5.2 Parameter setting via IO-Link: display layout
uCall up [Parameters] > [Display Setting].
uSelect [diS.L] and set layout.
10.5.6 Display colour setting
This function is only available via the IO-Link interface.
The font colour in the display can be set via the parameter [coL.x].
• [coL.F]: font colour for flow
• [coL.T]: font colour for temperature
• [coL.C]: font colour for conductivity
The colour can be defined individually for each process value.
Permanent colour selection
The parameter setting [coL.x] = [bk/wh] permanently sets the display to white text and black
background.
Produkt Specifikationer
Mærke: | IFM |
Kategori: | Ikke kategoriseret |
Model: | SMF420 |
Har du brug for hjælp?
Hvis du har brug for hjælp til IFM SMF420 stil et spørgsmål nedenfor, og andre brugere vil svare dig
Ikke kategoriseret IFM Manualer

9 April 2025

13 Marts 2025

10 Marts 2025

25 Januar 2025

25 Januar 2025

25 Januar 2025

25 Januar 2025

25 Januar 2025

25 Januar 2025

25 Januar 2025
Ikke kategoriseret Manualer
- Ikke kategoriseret DeLonghi
- Ikke kategoriseret Scheppach
- Ikke kategoriseret QNAP
- Ikke kategoriseret Nilox
- Ikke kategoriseret Sinbo
- Ikke kategoriseret Ikea
- Ikke kategoriseret Bosch
- Ikke kategoriseret SilverCrest
- Ikke kategoriseret Acer
- Ikke kategoriseret Honda
- Ikke kategoriseret BMW
- Ikke kategoriseret OBH Nordica
- Ikke kategoriseret Ozito
- Ikke kategoriseret PKM
- Ikke kategoriseret Gram
- Ikke kategoriseret Denver
- Ikke kategoriseret Sencor
- Ikke kategoriseret TCL
- Ikke kategoriseret Sony
- Ikke kategoriseret EasyMaxx
- Ikke kategoriseret Canon
- Ikke kategoriseret Aruba
- Ikke kategoriseret Singer
- Ikke kategoriseret Suunto
- Ikke kategoriseret Juki
- Ikke kategoriseret Krups
- Ikke kategoriseret Maxxmee
- Ikke kategoriseret Zibro
- Ikke kategoriseret Siemens
- Ikke kategoriseret Netis
- Ikke kategoriseret Samsung
- Ikke kategoriseret Scandomestic
- Ikke kategoriseret Stiga
- Ikke kategoriseret Wilfa
- Ikke kategoriseret GE
- Ikke kategoriseret Beurer
- Ikke kategoriseret Breville
- Ikke kategoriseret Daikin
- Ikke kategoriseret Zanussi
- Ikke kategoriseret Cylinda
- Ikke kategoriseret CyberPower
- Ikke kategoriseret Metro Therm
- Ikke kategoriseret Panasonic
- Ikke kategoriseret HyperJuice
- Ikke kategoriseret Hager
- Ikke kategoriseret Candy
- Ikke kategoriseret Owon
- Ikke kategoriseret Fisher & Paykel
- Ikke kategoriseret Metabo
- Ikke kategoriseret Gorenje
- Ikke kategoriseret Martha Stewart
- Ikke kategoriseret DeWalt
- Ikke kategoriseret Extech
- Ikke kategoriseret AENO
- Ikke kategoriseret Moog
- Ikke kategoriseret Husqvarna
- Ikke kategoriseret VOX
- Ikke kategoriseret Pro-Ject
- Ikke kategoriseret TP-Link
- Ikke kategoriseret RYOBI
- Ikke kategoriseret Miele
- Ikke kategoriseret Volkswagen
- Ikke kategoriseret Ninja
- Ikke kategoriseret Ei Electronics
- Ikke kategoriseret Silverline
- Ikke kategoriseret Blomberg
- Ikke kategoriseret Philips
- Ikke kategoriseret Lenco
- Ikke kategoriseret Aukey
- Ikke kategoriseret Caso
- Ikke kategoriseret Concept
- Ikke kategoriseret Skil
- Ikke kategoriseret Gastroback
- Ikke kategoriseret Steba
- Ikke kategoriseret G-LAB
- Ikke kategoriseret Teka
- Ikke kategoriseret Aprilia
- Ikke kategoriseret Vitek
- Ikke kategoriseret Medisana
- Ikke kategoriseret Nintendo
- Ikke kategoriseret Rommelsbacher
- Ikke kategoriseret Mafell
- Ikke kategoriseret OK
- Ikke kategoriseret LG
- Ikke kategoriseret AEG
- Ikke kategoriseret Happy Plugs
- Ikke kategoriseret Musway
- Ikke kategoriseret Victron Energy
- Ikke kategoriseret Audio-Technica
- Ikke kategoriseret Doro
- Ikke kategoriseret Electrolux
- Ikke kategoriseret VitalMaxx
- Ikke kategoriseret Peavey
- Ikke kategoriseret Thetford
- Ikke kategoriseret Bauknecht
- Ikke kategoriseret Gigaset
- Ikke kategoriseret Pioneer
- Ikke kategoriseret Finder
- Ikke kategoriseret TOA
- Ikke kategoriseret Shark
- Ikke kategoriseret Elica
- Ikke kategoriseret Hifonics
- Ikke kategoriseret Whirlpool
- Ikke kategoriseret Vestfrost
- Ikke kategoriseret Mitsubishi
- Ikke kategoriseret Master
- Ikke kategoriseret Braun
- Ikke kategoriseret Apple
- Ikke kategoriseret Senco
- Ikke kategoriseret Sharp
- Ikke kategoriseret Tanita
- Ikke kategoriseret Roxio
- Ikke kategoriseret Ferplast
- Ikke kategoriseret Hotpoint
- Ikke kategoriseret Dacor
- Ikke kategoriseret Melissa
- Ikke kategoriseret Nautilus
- Ikke kategoriseret Dynacord
- Ikke kategoriseret Logitech
- Ikke kategoriseret Behringer
- Ikke kategoriseret Atag
- Ikke kategoriseret Emos
- Ikke kategoriseret Lexmark
- Ikke kategoriseret Kenwood
- Ikke kategoriseret Gardena
- Ikke kategoriseret Mobicool
- Ikke kategoriseret Epson
- Ikke kategoriseret Google
- Ikke kategoriseret Neumann
- Ikke kategoriseret Sage
- Ikke kategoriseret AL-KO
- Ikke kategoriseret Metrix
- Ikke kategoriseret Omega
- Ikke kategoriseret Hoover
- Ikke kategoriseret Zipper
- Ikke kategoriseret Amazfit
- Ikke kategoriseret Daewoo
- Ikke kategoriseret Technaxx
- Ikke kategoriseret Lowrance
- Ikke kategoriseret Korona
- Ikke kategoriseret Pfaff
- Ikke kategoriseret MB Quart
- Ikke kategoriseret Arçelik
- Ikke kategoriseret Stihl
- Ikke kategoriseret IRobot
- Ikke kategoriseret Smart
- Ikke kategoriseret HP
- Ikke kategoriseret UTEPO
- Ikke kategoriseret ProfiCare
- Ikke kategoriseret TFA
- Ikke kategoriseret JennAir
- Ikke kategoriseret Sennheiser
- Ikke kategoriseret Soler & Palau
- Ikke kategoriseret Gustavsberg
- Ikke kategoriseret BaByliss
- Ikke kategoriseret Harman Kardon
- Ikke kategoriseret Waeco
- Ikke kategoriseret Aduro
- Ikke kategoriseret AOC
- Ikke kategoriseret Emporia
- Ikke kategoriseret OpenVox
- Ikke kategoriseret McCulloch
- Ikke kategoriseret Garmin
- Ikke kategoriseret Sanyo
- Ikke kategoriseret Baxi
- Ikke kategoriseret Thinkware
- Ikke kategoriseret Nilfisk
- Ikke kategoriseret Carel
- Ikke kategoriseret Easypix
- Ikke kategoriseret Grundig
- Ikke kategoriseret Makita
- Ikke kategoriseret Akuvox
- Ikke kategoriseret Leitz
- Ikke kategoriseret Nikkei
- Ikke kategoriseret Worx
- Ikke kategoriseret JLab
- Ikke kategoriseret De Buyer
- Ikke kategoriseret Nimble
- Ikke kategoriseret D-Link
- Ikke kategoriseret Dolmar
- Ikke kategoriseret Falmec
- Ikke kategoriseret Progress
- Ikke kategoriseret Volvo
- Ikke kategoriseret Thule
- Ikke kategoriseret Motorola
- Ikke kategoriseret MTM
- Ikke kategoriseret Witt
- Ikke kategoriseret Roland
- Ikke kategoriseret Asus
- Ikke kategoriseret Bushnell
- Ikke kategoriseret Indesit
- Ikke kategoriseret GYS
- Ikke kategoriseret Golden Age Project
- Ikke kategoriseret SKS
- Ikke kategoriseret Gigabyte
- Ikke kategoriseret Hotpoint Ariston
- Ikke kategoriseret Ernesto
- Ikke kategoriseret Livoo
- Ikke kategoriseret Lego
- Ikke kategoriseret GIMA
- Ikke kategoriseret Toshiba
- Ikke kategoriseret Pyle
- Ikke kategoriseret Fujifilm
- Ikke kategoriseret Argon
- Ikke kategoriseret Klarstein
- Ikke kategoriseret Nikon
- Ikke kategoriseret Kodak
- Ikke kategoriseret Güde
- Ikke kategoriseret ABB
- Ikke kategoriseret Tracer
- Ikke kategoriseret Eheim
- Ikke kategoriseret Brother
- Ikke kategoriseret Bodum
- Ikke kategoriseret Furrion
- Ikke kategoriseret Etna
- Ikke kategoriseret Denon
- Ikke kategoriseret Tefal
- Ikke kategoriseret InFocus
- Ikke kategoriseret One For All
- Ikke kategoriseret Lenovo
- Ikke kategoriseret Asrock
- Ikke kategoriseret Yamaha
- Ikke kategoriseret Infiniton
- Ikke kategoriseret OnePlus
- Ikke kategoriseret Trisa
- Ikke kategoriseret Princess
- Ikke kategoriseret Olympus
- Ikke kategoriseret Bowers & Wilkins
- Ikke kategoriseret Matsui
- Ikke kategoriseret Biltema
- Ikke kategoriseret AVM
- Ikke kategoriseret Nedis
- Ikke kategoriseret Emerio
- Ikke kategoriseret Severin
- Ikke kategoriseret Dymo
- Ikke kategoriseret Kubota
- Ikke kategoriseret American DJ
- Ikke kategoriseret Friedland
- Ikke kategoriseret Humminbird
- Ikke kategoriseret Silver Cross
- Ikke kategoriseret Baby Jogger
- Ikke kategoriseret Buzz Rack
- Ikke kategoriseret Logik
- Ikke kategoriseret Abus
- Ikke kategoriseret Jonsered
- Ikke kategoriseret Butler
- Ikke kategoriseret Kicker
- Ikke kategoriseret Hendi
- Ikke kategoriseret Bartscher
- Ikke kategoriseret Polar
- Ikke kategoriseret Planet
- Ikke kategoriseret Adj
- Ikke kategoriseret Optoma
- Ikke kategoriseret Be Quiet!
- Ikke kategoriseret Renegade
- Ikke kategoriseret Vonroc
- Ikke kategoriseret Moulinex
- Ikke kategoriseret Sunbeam
- Ikke kategoriseret LD Systems
- Ikke kategoriseret Sauber
- Ikke kategoriseret Da-Lite
- Ikke kategoriseret Westinghouse
- Ikke kategoriseret Hama
- Ikke kategoriseret Auna
- Ikke kategoriseret Bowflex
- Ikke kategoriseret Muse
- Ikke kategoriseret Ilve
- Ikke kategoriseret Eico
- Ikke kategoriseret Creative
- Ikke kategoriseret Thomson
- Ikke kategoriseret Constructa
- Ikke kategoriseret Hyundai
- Ikke kategoriseret Aiwa
- Ikke kategoriseret Perfecta
- Ikke kategoriseret Milwaukee
- Ikke kategoriseret Nokia
- Ikke kategoriseret Aqua Joe
- Ikke kategoriseret Rega
- Ikke kategoriseret Azden
- Ikke kategoriseret Yorkville
- Ikke kategoriseret Selec
- Ikke kategoriseret Sena
- Ikke kategoriseret Proctor Silex
- Ikke kategoriseret Belkin
- Ikke kategoriseret BENNING
- Ikke kategoriseret Pyle Pro
- Ikke kategoriseret Jura
- Ikke kategoriseret Edimax
- Ikke kategoriseret Theben
- Ikke kategoriseret Dyson
- Ikke kategoriseret Casio
- Ikke kategoriseret Burg Wächter
- Ikke kategoriseret Palm
- Ikke kategoriseret Kettler
- Ikke kategoriseret JBL
- Ikke kategoriseret Black Box
- Ikke kategoriseret Imetec
- Ikke kategoriseret AKAI
- Ikke kategoriseret Wago
- Ikke kategoriseret Hisense
- Ikke kategoriseret TriStar
- Ikke kategoriseret Teufel
- Ikke kategoriseret Clas Ohlson
- Ikke kategoriseret DataVideo
- Ikke kategoriseret Strong
- Ikke kategoriseret Audio Pro
- Ikke kategoriseret RCF
- Ikke kategoriseret Maxell
- Ikke kategoriseret TRENDnet
- Ikke kategoriseret Weber
- Ikke kategoriseret Sanitas
- Ikke kategoriseret Brandt
- Ikke kategoriseret Metrel
- Ikke kategoriseret Pure
- Ikke kategoriseret Optex
- Ikke kategoriseret Smartwares
- Ikke kategoriseret Skullcandy
- Ikke kategoriseret Chef's Choice
- Ikke kategoriseret Zaor
- Ikke kategoriseret Chandler
- Ikke kategoriseret Peugeot
- Ikke kategoriseret Kyoritsu
- Ikke kategoriseret Trevi
- Ikke kategoriseret Hansgrohe
- Ikke kategoriseret Trust
- Ikke kategoriseret Fysic
- Ikke kategoriseret Microlife
- Ikke kategoriseret Omron
- Ikke kategoriseret Topcom
- Ikke kategoriseret Flex
- Ikke kategoriseret Laserliner
- Ikke kategoriseret Parkside
- Ikke kategoriseret Trimble
- Ikke kategoriseret Florabest
- Ikke kategoriseret Adler
- Ikke kategoriseret Black And Decker
- Ikke kategoriseret Camry
- Ikke kategoriseret Crivit
- Ikke kategoriseret Dometic
- Ikke kategoriseret Mestic
- Ikke kategoriseret Outwell
- Ikke kategoriseret Rocktrail
- Ikke kategoriseret Habitat
- Ikke kategoriseret JYSK
- Ikke kategoriseret Leen Bakker
- Ikke kategoriseret Livarno
- Ikke kategoriseret Mio
- Ikke kategoriseret Parisot
- Ikke kategoriseret Busch-Jaeger
- Ikke kategoriseret FERM
- Ikke kategoriseret Power Craft
- Ikke kategoriseret Wagner
- Ikke kategoriseret Eurom
- Ikke kategoriseret Trotec
- Ikke kategoriseret Blaupunkt
- Ikke kategoriseret JVC
- Ikke kategoriseret Silva
- Ikke kategoriseret Einhell
- Ikke kategoriseret Asko
- Ikke kategoriseret Atlas
- Ikke kategoriseret Becken
- Ikke kategoriseret BEKO
- Ikke kategoriseret Gaggenau
- Ikke kategoriseret Küppersbusch
- Ikke kategoriseret Neff
- Ikke kategoriseret Privileg
- Ikke kategoriseret Sandstrøm
- Ikke kategoriseret Smeg
- Ikke kategoriseret Ordex
- Ikke kategoriseret Proxxon
- Ikke kategoriseret Leica
- Ikke kategoriseret Stanley
- Ikke kategoriseret Honeywell
- Ikke kategoriseret Woonexpress
- Ikke kategoriseret Uniden
- Ikke kategoriseret Alpina
- Ikke kategoriseret Champion
- Ikke kategoriseret Clatronic
- Ikke kategoriseret Mesko
- Ikke kategoriseret Quigg
- Ikke kategoriseret Hikoki
- Ikke kategoriseret Hilti
- Ikke kategoriseret Hitachi
- Ikke kategoriseret Buffalo
- Ikke kategoriseret FoodSaver
- Ikke kategoriseret Crunch
- Ikke kategoriseret Proficook
- Ikke kategoriseret United Office
- Ikke kategoriseret Elite
- Ikke kategoriseret Rowenta
- Ikke kategoriseret Miomare
- Ikke kategoriseret Noveen
- Ikke kategoriseret Alpha Tools
- Ikke kategoriseret Bavaria
- Ikke kategoriseret Greenworks
- Ikke kategoriseret Kress
- Ikke kategoriseret Razer
- Ikke kategoriseret Remington
- Ikke kategoriseret Silk'n
- Ikke kategoriseret Zoofari
- Ikke kategoriseret Dualit
- Ikke kategoriseret Graef
- Ikke kategoriseret Melitta
- Ikke kategoriseret Dentalux
- Ikke kategoriseret Nevadent
- Ikke kategoriseret T'nB
- Ikke kategoriseret Handicare
- Ikke kategoriseret Medion
- Ikke kategoriseret Sweex
- Ikke kategoriseret Vivanco
- Ikke kategoriseret Playtive Junior
- Ikke kategoriseret Liebherr
- Ikke kategoriseret Olivetti
- Ikke kategoriseret Texas Instruments
- Ikke kategoriseret Linksys
- Ikke kategoriseret Intex
- Ikke kategoriseret Meradiso
- Ikke kategoriseret Megasat
- Ikke kategoriseret Festool
- Ikke kategoriseret Soehnle
- Ikke kategoriseret Fagor
- Ikke kategoriseret Haier
- Ikke kategoriseret Cambridge
- Ikke kategoriseret Cisco
- Ikke kategoriseret EZVIZ
- Ikke kategoriseret Huawei
- Ikke kategoriseret König
- Ikke kategoriseret Technicolor
- Ikke kategoriseret TechniSat
- Ikke kategoriseret Atika
- Ikke kategoriseret Cramer
- Ikke kategoriseret Echo
- Ikke kategoriseret EGO
- Ikke kategoriseret Solo
- Ikke kategoriseret Texas
- Ikke kategoriseret LiftMaster
- Ikke kategoriseret Truma
- Ikke kategoriseret FireAngel
- Ikke kategoriseret Reebok
- Ikke kategoriseret AFK
- Ikke kategoriseret Bifinett
- Ikke kategoriseret Bomann
- Ikke kategoriseret Morphy Richards
- Ikke kategoriseret Redmond
- Ikke kategoriseret Russell Hobbs
- Ikke kategoriseret WMF
- Ikke kategoriseret Ariete
- Ikke kategoriseret Elro
- Ikke kategoriseret Innoliving
- Ikke kategoriseret Lucide
- Ikke kategoriseret Maul
- Ikke kategoriseret Max
- Ikke kategoriseret Nordlux
- Ikke kategoriseret Osram
- Ikke kategoriseret Ranex
- Ikke kategoriseret KitchenAid
- Ikke kategoriseret Steinel
- Ikke kategoriseret Zelmer
- Ikke kategoriseret REV
- Ikke kategoriseret Tivoli Audio
- Ikke kategoriseret Melinera
- Ikke kategoriseret Hapro
- Ikke kategoriseret AquaPur
- Ikke kategoriseret Leifheit
- Ikke kategoriseret Tanaka
- Ikke kategoriseret Wolf Garten
- Ikke kategoriseret Seagate
- Ikke kategoriseret Invacare
- Ikke kategoriseret Gembird
- Ikke kategoriseret Targus
- Ikke kategoriseret TranzX
- Ikke kategoriseret B-Tech
- Ikke kategoriseret Barkan
- Ikke kategoriseret Deltaco
- Ikke kategoriseret NewStar
- Ikke kategoriseret Sanus
- Ikke kategoriseret Exit
- Ikke kategoriseret Salta
- Ikke kategoriseret Bang And Olufsen
- Ikke kategoriseret Luxor
- Ikke kategoriseret Brabantia
- Ikke kategoriseret Weihrauch Sport
- Ikke kategoriseret Bose
- Ikke kategoriseret Geemarc
- Ikke kategoriseret Jabra
- Ikke kategoriseret Dremel
- Ikke kategoriseret Klipsch
- Ikke kategoriseret Rosieres
- Ikke kategoriseret Soundcore
- Ikke kategoriseret Kohler
- Ikke kategoriseret Fein
- Ikke kategoriseret Leatherman
- Ikke kategoriseret Rapid
- Ikke kategoriseret Topcraft
- Ikke kategoriseret FIAP
- Ikke kategoriseret Oase
- Ikke kategoriseret Pontec
- Ikke kategoriseret Krinner
- Ikke kategoriseret Vivax
- Ikke kategoriseret Auriol
- Ikke kategoriseret Cottons
- Ikke kategoriseret Ultimate Speed
- Ikke kategoriseret Ventus
- Ikke kategoriseret Thermex
- Ikke kategoriseret Suzuki
- Ikke kategoriseret Loewe
- Ikke kategoriseret Beretta
- Ikke kategoriseret Vaillant
- Ikke kategoriseret GFI System
- Ikke kategoriseret Bionaire
- Ikke kategoriseret EWT
- Ikke kategoriseret JML
- Ikke kategoriseret Stadler Form
- Ikke kategoriseret PetSafe
- Ikke kategoriseret Powerfix
- Ikke kategoriseret Crosley
- Ikke kategoriseret Hayward
- Ikke kategoriseret Alpine
- Ikke kategoriseret Netgear
- Ikke kategoriseret Vipack
- Ikke kategoriseret Babymoov
- Ikke kategoriseret Easy Camp
- Ikke kategoriseret Ventura
- Ikke kategoriseret George Foreman
- Ikke kategoriseret Lansinoh
- Ikke kategoriseret Medela
- Ikke kategoriseret Galanz
- Ikke kategoriseret EnVivo
- Ikke kategoriseret Woox
- Ikke kategoriseret Maginon
- Ikke kategoriseret Navman
- Ikke kategoriseret Avaya
- Ikke kategoriseret Parrot
- Ikke kategoriseret Tetra
- Ikke kategoriseret Amana
- Ikke kategoriseret Amica
- Ikke kategoriseret Euromaid
- Ikke kategoriseret C3
- Ikke kategoriseret Master Lock
- Ikke kategoriseret Yale
- Ikke kategoriseret Hozelock
- Ikke kategoriseret Kärcher
- Ikke kategoriseret Michelin
- Ikke kategoriseret Ford
- Ikke kategoriseret Gaggia
- Ikke kategoriseret Calor
- Ikke kategoriseret RADEMACHER
- Ikke kategoriseret Coleman
- Ikke kategoriseret Skandika
- Ikke kategoriseret Vango
- Ikke kategoriseret KKT Kolbe
- Ikke kategoriseret Vroomshoop
- Ikke kategoriseret 3M
- Ikke kategoriseret Tamron
- Ikke kategoriseret Festo
- Ikke kategoriseret Carrier
- Ikke kategoriseret Comfee
- Ikke kategoriseret Gree
- Ikke kategoriseret Wood's
- Ikke kategoriseret Seiko
- Ikke kategoriseret Danfoss
- Ikke kategoriseret Nilan
- Ikke kategoriseret Tesy
- Ikke kategoriseret AXI
- Ikke kategoriseret Little Tikes
- Ikke kategoriseret Smoby
- Ikke kategoriseret Sunny
- Ikke kategoriseret Revitive
- Ikke kategoriseret Balance
- Ikke kategoriseret Terraillon
- Ikke kategoriseret Croozer
- Ikke kategoriseret Wolf
- Ikke kategoriseret Zuiver
- Ikke kategoriseret Totolink
- Ikke kategoriseret Dimplex
- Ikke kategoriseret Eberle
- Ikke kategoriseret Grässlin
- Ikke kategoriseret Junkers
- Ikke kategoriseret Salus
- Ikke kategoriseret Weishaupt
- Ikke kategoriseret Shoprider
- Ikke kategoriseret GA.MA
- Ikke kategoriseret Wacom
- Ikke kategoriseret Telefunken
- Ikke kategoriseret Kerbl
- Ikke kategoriseret SureFlap
- Ikke kategoriseret CaterCool
- Ikke kategoriseret Triax
- Ikke kategoriseret Vitamix
- Ikke kategoriseret Kernau
- Ikke kategoriseret Carena
- Ikke kategoriseret Kidsmill
- Ikke kategoriseret Fisher-Price
- Ikke kategoriseret Graco
- Ikke kategoriseret Vtech
- Ikke kategoriseret BlueBuilt
- Ikke kategoriseret Tronic
- Ikke kategoriseret Tripp Lite
- Ikke kategoriseret BenQ
- Ikke kategoriseret Bertazzoni
- Ikke kategoriseret Caple
- Ikke kategoriseret Bébé Confort
- Ikke kategoriseret Chicco
- Ikke kategoriseret Hauck
- Ikke kategoriseret Cuisinart
- Ikke kategoriseret Maxi-Cosi
- Ikke kategoriseret Schütte
- Ikke kategoriseret Tiger
- Ikke kategoriseret Cherry
- Ikke kategoriseret Contour
- Ikke kategoriseret Exibel
- Ikke kategoriseret Microsoft
- Ikke kategoriseret Penclic
- Ikke kategoriseret Rapoo
- Ikke kategoriseret Cadel
- Ikke kategoriseret CLINIC
- Ikke kategoriseret Herkules
- Ikke kategoriseret Mercury
- Ikke kategoriseret Dahle
- Ikke kategoriseret Fellowes
- Ikke kategoriseret Genie
- Ikke kategoriseret Peach
- Ikke kategoriseret Primo
- Ikke kategoriseret Rexel
- Ikke kategoriseret GBC
- Ikke kategoriseret Lervia
- Ikke kategoriseret Orbegozo
- Ikke kategoriseret BabyDan
- Ikke kategoriseret Geuther
- Ikke kategoriseret Lindam
- Ikke kategoriseret Munchkin
- Ikke kategoriseret Reer
- Ikke kategoriseret Ankarsrum
- Ikke kategoriseret Vaddio
- Ikke kategoriseret MySoda
- Ikke kategoriseret SodaStream
- Ikke kategoriseret Ambrogio
- Ikke kategoriseret Craftsman
- Ikke kategoriseret Fiskars
- Ikke kategoriseret Gtech
- Ikke kategoriseret Hurricane
- Ikke kategoriseret Powerplus
- Ikke kategoriseret Viking
- Ikke kategoriseret Gazelle
- Ikke kategoriseret Bresser
- Ikke kategoriseret Davis
- Ikke kategoriseret Jacob Jensen
- Ikke kategoriseret National Geographic
- Ikke kategoriseret Alcatel
- Ikke kategoriseret BeamZ
- Ikke kategoriseret Goobay
- Ikke kategoriseret Malmbergs
- Ikke kategoriseret Berner
- Ikke kategoriseret Würth
- Ikke kategoriseret Babybjörn
- Ikke kategoriseret Britax-Römer
- Ikke kategoriseret Ergobaby
- Ikke kategoriseret Joie
- Ikke kategoriseret Stokke
- Ikke kategoriseret Nûby
- Ikke kategoriseret Tommee Tippee
- Ikke kategoriseret Sensiplast
- Ikke kategoriseret CaterChef
- Ikke kategoriseret Rusta
- Ikke kategoriseret Western Digital
- Ikke kategoriseret Zeiss Ikon
- Ikke kategoriseret Franke
- Ikke kategoriseret Optimum
- Ikke kategoriseret Anker
- Ikke kategoriseret Dali
- Ikke kategoriseret Enermax
- Ikke kategoriseret KEF
- Ikke kategoriseret Streetz
- Ikke kategoriseret Technics
- Ikke kategoriseret Digitus
- Ikke kategoriseret Summit Audio
- Ikke kategoriseret Sigma
- Ikke kategoriseret Spanninga
- Ikke kategoriseret Zebra
- Ikke kategoriseret Cadac
- Ikke kategoriseret Char-Broil
- Ikke kategoriseret Jensen
- Ikke kategoriseret Koenig
- Ikke kategoriseret Landmann
- Ikke kategoriseret OutdoorChef
- Ikke kategoriseret Rösle
- Ikke kategoriseret BeSafe
- Ikke kategoriseret BRIO
- Ikke kategoriseret Britax
- Ikke kategoriseret Cybex
- Ikke kategoriseret Jane
- Ikke kategoriseret Nuna
- Ikke kategoriseret Osann
- Ikke kategoriseret Peg-Pérego
- Ikke kategoriseret Recaro
- Ikke kategoriseret Allibert
- Ikke kategoriseret Gamma
- Ikke kategoriseret Trigano
- Ikke kategoriseret Alecto
- Ikke kategoriseret Icom
- Ikke kategoriseret Krontaler
- Ikke kategoriseret Brita
- Ikke kategoriseret Lufe
- Ikke kategoriseret BBB
- Ikke kategoriseret Bryton
- Ikke kategoriseret Cateye
- Ikke kategoriseret Echowell
- Ikke kategoriseret Topmove
- Ikke kategoriseret Bugaboo
- Ikke kategoriseret Juwel
- Ikke kategoriseret Salter
- Ikke kategoriseret Taurus
- Ikke kategoriseret Pentax
- Ikke kategoriseret Rollei
- Ikke kategoriseret KidKraft
- Ikke kategoriseret Plum
- Ikke kategoriseret Catit
- Ikke kategoriseret Sencys
- Ikke kategoriseret Olympia
- Ikke kategoriseret Astro
- Ikke kategoriseret Cabstone
- Ikke kategoriseret Plantronics
- Ikke kategoriseret SteelSeries
- Ikke kategoriseret Thrustmaster
- Ikke kategoriseret Ansmann
- Ikke kategoriseret Dymond
- Ikke kategoriseret GP
- Ikke kategoriseret Varta
- Ikke kategoriseret Veripart
- Ikke kategoriseret Xiaomi
- Ikke kategoriseret Moultrie
- Ikke kategoriseret IMC Toys
- Ikke kategoriseret Babyzen
- Ikke kategoriseret Cosatto
- Ikke kategoriseret Emmaljunga
- Ikke kategoriseret Joovy
- Ikke kategoriseret Maclaren
- Ikke kategoriseret Faber
- Ikke kategoriseret Hecht
- Ikke kategoriseret Ninebot
- Ikke kategoriseret Pro User
- Ikke kategoriseret Westfalia
- Ikke kategoriseret Hobby
- Ikke kategoriseret Opus
- Ikke kategoriseret Balay
- Ikke kategoriseret Cata
- Ikke kategoriseret Exquisit
- Ikke kategoriseret Boneco
- Ikke kategoriseret HQ
- Ikke kategoriseret Kraftwerk
- Ikke kategoriseret Cougar
- Ikke kategoriseret Genesis
- Ikke kategoriseret Niceboy
- Ikke kategoriseret Serano
- Ikke kategoriseret Techly
- Ikke kategoriseret Pelgrim
- Ikke kategoriseret Youin
- Ikke kategoriseret Peerless-AV
- Ikke kategoriseret Elba
- Ikke kategoriseret Nodor
- Ikke kategoriseret Rommer
- Ikke kategoriseret Housegard
- Ikke kategoriseret Aiptek
- Ikke kategoriseret Homedics
- Ikke kategoriseret Tork
- Ikke kategoriseret Krüger&Matz
- Ikke kategoriseret Viewsonic
- Ikke kategoriseret Hamax
- Ikke kategoriseret Reich
- Ikke kategoriseret Rotho
- Ikke kategoriseret Dell
- Ikke kategoriseret RugGear
- Ikke kategoriseret Cruz
- Ikke kategoriseret G3
- Ikke kategoriseret Karibu
- Ikke kategoriseret Foppapedretti
- Ikke kategoriseret Roba
- Ikke kategoriseret Zenec
- Ikke kategoriseret EnerGenie
- Ikke kategoriseret Vema
- Ikke kategoriseret Schneider
- Ikke kategoriseret Vicks
- Ikke kategoriseret Pattfield
- Ikke kategoriseret ELO
- Ikke kategoriseret Novo Nordisk
- Ikke kategoriseret Vivitek
- Ikke kategoriseret Nibe
- Ikke kategoriseret Fujitsu
- Ikke kategoriseret MPM
- Ikke kategoriseret DJI
- Ikke kategoriseret Mustang
- Ikke kategoriseret Bissell
- Ikke kategoriseret Dirt Devil
- Ikke kategoriseret Primus
- Ikke kategoriseret Profilo
- Ikke kategoriseret Tornado
- Ikke kategoriseret Vax
- Ikke kategoriseret Marmitek
- Ikke kategoriseret Damixa
- Ikke kategoriseret Oras
- Ikke kategoriseret Basetech
- Ikke kategoriseret Toyotomi
- Ikke kategoriseret Venta
- Ikke kategoriseret Oppo
- Ikke kategoriseret Maxxter
- Ikke kategoriseret NGS
- Ikke kategoriseret Roccat
- Ikke kategoriseret Radionette
- Ikke kategoriseret Mamas & Papas
- Ikke kategoriseret AZZA
- Ikke kategoriseret Cooler Master
- Ikke kategoriseret Zalman
- Ikke kategoriseret PreSonus
- Ikke kategoriseret Tesla
- Ikke kategoriseret Kopul
- Ikke kategoriseret Linea
- Ikke kategoriseret Paidi
- Ikke kategoriseret Pinolino
- Ikke kategoriseret Cardiostrong
- Ikke kategoriseret Toorx
- Ikke kategoriseret Tunturi
- Ikke kategoriseret Keter
- Ikke kategoriseret Boso
- Ikke kategoriseret Lanaform
- Ikke kategoriseret Grohe
- Ikke kategoriseret MSI
- Ikke kategoriseret Voltcraft
- Ikke kategoriseret Hanseatic
- Ikke kategoriseret Debel
- Ikke kategoriseret Polaroid
- Ikke kategoriseret Ricoh
- Ikke kategoriseret ASSA ABLOY
- Ikke kategoriseret Dorma
- Ikke kategoriseret GEZE
- Ikke kategoriseret Ice Watch
- Ikke kategoriseret Concept2
- Ikke kategoriseret UX
- Ikke kategoriseret Crosscall
- Ikke kategoriseret Aerotec
- Ikke kategoriseret Lyman
- Ikke kategoriseret NEC
- Ikke kategoriseret G3 Ferrari
- Ikke kategoriseret Artec
- Ikke kategoriseret Trixie
- Ikke kategoriseret Godox
- Ikke kategoriseret Zeiss
- Ikke kategoriseret Stairville
- Ikke kategoriseret GEV
- Ikke kategoriseret Adidas
- Ikke kategoriseret TomTom
- Ikke kategoriseret Bruynzeel
- Ikke kategoriseret Unilux
- Ikke kategoriseret Soundmaster
- Ikke kategoriseret SABO
- Ikke kategoriseret Nexxt
- Ikke kategoriseret Thor
- Ikke kategoriseret Gardol
- Ikke kategoriseret Vogue
- Ikke kategoriseret V-Zug
- Ikke kategoriseret Aida
- Ikke kategoriseret Konica-Minolta
- Ikke kategoriseret OKI
- Ikke kategoriseret APC
- Ikke kategoriseret Maytag
- Ikke kategoriseret Foscam
- Ikke kategoriseret Gourmetmaxx
- Ikke kategoriseret Kathrein
- Ikke kategoriseret Domo
- Ikke kategoriseret CTOUCH
- Ikke kategoriseret Mellerware
- Ikke kategoriseret Mutec
- Ikke kategoriseret Auto Joe
- Ikke kategoriseret Kyocera
- Ikke kategoriseret Fieldmann
- Ikke kategoriseret GoPro
- Ikke kategoriseret Victrola
- Ikke kategoriseret BEEM
- Ikke kategoriseret Sonos
- Ikke kategoriseret Joranalogue
- Ikke kategoriseret Jøtul
- Ikke kategoriseret Fluval
- Ikke kategoriseret Velda
- Ikke kategoriseret NAD
- Ikke kategoriseret ESI
- Ikke kategoriseret Ferroli
- Ikke kategoriseret Lorex
- Ikke kategoriseret Testboy
- Ikke kategoriseret Ikan
- Ikke kategoriseret AJA
- Ikke kategoriseret GlobalTronics
- Ikke kategoriseret Puky
- Ikke kategoriseret Reflecta
- Ikke kategoriseret Irritrol
- Ikke kategoriseret Elation
- Ikke kategoriseret Rain Bird
- Ikke kategoriseret Tascam
- Ikke kategoriseret Datalogic
- Ikke kategoriseret Cobra
- Ikke kategoriseret Xblitz
- Ikke kategoriseret DPA
- Ikke kategoriseret Bogen
- Ikke kategoriseret Spear & Jackson
- Ikke kategoriseret Omnitronic
- Ikke kategoriseret Velleman
- Ikke kategoriseret LevelOne
- Ikke kategoriseret Marshall
- Ikke kategoriseret FLIR
- Ikke kategoriseret Atlantic
- Ikke kategoriseret Corsair
- Ikke kategoriseret Energy Sistem
- Ikke kategoriseret Perel
- Ikke kategoriseret Walkstool
- Ikke kategoriseret Sonance
- Ikke kategoriseret Telestar
- Ikke kategoriseret Saro
- Ikke kategoriseret Swann
- Ikke kategoriseret Dynamic
- Ikke kategoriseret Vivotek
- Ikke kategoriseret Baby Lock
- Ikke kategoriseret Mercusys
- Ikke kategoriseret Zoom
- Ikke kategoriseret TC Helicon
- Ikke kategoriseret Plant Craft
- Ikke kategoriseret Geneva
- Ikke kategoriseret Capital Sports
- Ikke kategoriseret Thomas
- Ikke kategoriseret Bravilor Bonamat
- Ikke kategoriseret Porter-Cable
- Ikke kategoriseret Blue Sky
- Ikke kategoriseret Bush
- Ikke kategoriseret Zodiac
- Ikke kategoriseret JUNG
- Ikke kategoriseret Iseki
- Ikke kategoriseret Fostex
- Ikke kategoriseret Levoit
- Ikke kategoriseret Creality3D
- Ikke kategoriseret Heylo
- Ikke kategoriseret Byron
- Ikke kategoriseret Vemer
- Ikke kategoriseret Baumr-AG
- Ikke kategoriseret ORNO
- Ikke kategoriseret Hamilton Beach
- Ikke kategoriseret Ambiano
- Ikke kategoriseret Binatone
- Ikke kategoriseret Olimpia Splendid
- Ikke kategoriseret GLP
- Ikke kategoriseret Honor
- Ikke kategoriseret Apogee
- Ikke kategoriseret Fitbit
- Ikke kategoriseret Bixolon
- Ikke kategoriseret Unold
- Ikke kategoriseret Dual
- Ikke kategoriseret Aspes
- Ikke kategoriseret ZyXEL
- Ikke kategoriseret Tiptel
- Ikke kategoriseret Stelton
- Ikke kategoriseret Electro-Voice
- Ikke kategoriseret HQ Power
- Ikke kategoriseret Federal Signal
- Ikke kategoriseret Bellini
- Ikke kategoriseret Korg
- Ikke kategoriseret Arturia
- Ikke kategoriseret Fredenstein
- Ikke kategoriseret Bestway
- Ikke kategoriseret Genaray
- Ikke kategoriseret Carmen
- Ikke kategoriseret Telex
- Ikke kategoriseret RME
- Ikke kategoriseret Salora
- Ikke kategoriseret Sagem
- Ikke kategoriseret Smith & Wesson
- Ikke kategoriseret Fortinet
- Ikke kategoriseret Onkyo
- Ikke kategoriseret Scancool
- Ikke kategoriseret Powerblade
- Ikke kategoriseret Focal
- Ikke kategoriseret AIC
- Ikke kategoriseret Nevir
- Ikke kategoriseret Amprobe
- Ikke kategoriseret Line 6
- Ikke kategoriseret HK Audio
- Ikke kategoriseret Teac
- Ikke kategoriseret Mousetrapper
- Ikke kategoriseret Imperial
- Ikke kategoriseret Autotek
- Ikke kategoriseret Eurochron
- Ikke kategoriseret TrekStor
- Ikke kategoriseret Alfi
- Ikke kategoriseret HPI Racing
- Ikke kategoriseret Nextbase
- Ikke kategoriseret Eden
- Ikke kategoriseret Tenda
- Ikke kategoriseret Magnat
- Ikke kategoriseret Vivo
- Ikke kategoriseret Ursus Trotter
- Ikke kategoriseret Saramonic
- Ikke kategoriseret Harvia
- Ikke kategoriseret Eureka
- Ikke kategoriseret Blumfeldt
- Ikke kategoriseret Inventum
- Ikke kategoriseret Koala
- Ikke kategoriseret Carson
- Ikke kategoriseret Edilkamin
- Ikke kategoriseret Thorens
- Ikke kategoriseret Eaton
- Ikke kategoriseret Eufy
- Ikke kategoriseret Marantz
- Ikke kategoriseret Anchor Audio
- Ikke kategoriseret Autel
- Ikke kategoriseret Ambient Recording
- Ikke kategoriseret Technoline
- Ikke kategoriseret Grillmeister
- Ikke kategoriseret SuperFish
- Ikke kategoriseret IBasso
- Ikke kategoriseret Oceanic
- Ikke kategoriseret JAYS
- Ikke kategoriseret Celestron
- Ikke kategoriseret ELAC
- Ikke kategoriseret Cleanmaxx
- Ikke kategoriseret Hartke
- Ikke kategoriseret Genelec
- Ikke kategoriseret Sven
- Ikke kategoriseret Soundcraft
- Ikke kategoriseret BabyGO
- Ikke kategoriseret AudioQuest
- Ikke kategoriseret Ring
- Ikke kategoriseret The Box Pro
- Ikke kategoriseret Vogel's
- Ikke kategoriseret Gre
- Ikke kategoriseret KRK
- Ikke kategoriseret Nivona
- Ikke kategoriseret Nvidia
- Ikke kategoriseret Fakir
- Ikke kategoriseret Weller
- Ikke kategoriseret McIntosh
- Ikke kategoriseret Simplified MFG
- Ikke kategoriseret Accu-Chek
- Ikke kategoriseret Wacker Neuson
- Ikke kategoriseret NZXT
- Ikke kategoriseret Swan
- Ikke kategoriseret IDance
- Ikke kategoriseret Fluke
- Ikke kategoriseret Hertz
- Ikke kategoriseret Lamax
- Ikke kategoriseret American Audio
- Ikke kategoriseret M-e
- Ikke kategoriseret Overmax
- Ikke kategoriseret Somfy
- Ikke kategoriseret Dreadbox
- Ikke kategoriseret Dantherm
- Ikke kategoriseret Khind
- Ikke kategoriseret EQ3
- Ikke kategoriseret Thermaltake
- Ikke kategoriseret Midea
- Ikke kategoriseret Stabila
- Ikke kategoriseret Synology
- Ikke kategoriseret Albrecht
- Ikke kategoriseret Napoleon
- Ikke kategoriseret Shimano
- Ikke kategoriseret Pardini
- Ikke kategoriseret CDA
- Ikke kategoriseret Laica
- Ikke kategoriseret Scott
- Ikke kategoriseret SBS
- Ikke kategoriseret Frigidaire
- Ikke kategoriseret Frilec
- Ikke kategoriseret Veho
- Ikke kategoriseret ART
- Ikke kategoriseret Bluesound
- Ikke kategoriseret Newland
- Ikke kategoriseret Yaesu
- Ikke kategoriseret Bimar
- Ikke kategoriseret Newline
- Ikke kategoriseret Zhiyun
- Ikke kategoriseret La Crosse Technology
- Ikke kategoriseret Lotus
- Ikke kategoriseret Techno Line
- Ikke kategoriseret Ridgid
- Ikke kategoriseret Rode
- Ikke kategoriseret Polk
- Ikke kategoriseret Midland
- Ikke kategoriseret Hikvision
- Ikke kategoriseret Ardes
- Ikke kategoriseret Husky
- Ikke kategoriseret Suntec
- Ikke kategoriseret ECS
- Ikke kategoriseret Archos
- Ikke kategoriseret Monacor
- Ikke kategoriseret Sun Joe
- Ikke kategoriseret Samson
- Ikke kategoriseret Sandisk
- Ikke kategoriseret ION
- Ikke kategoriseret Esatto
- Ikke kategoriseret Ctek
- Ikke kategoriseret Yealink
- Ikke kategoriseret JL Audio
- Ikke kategoriseret SVAN
- Ikke kategoriseret Paladin
- Ikke kategoriseret Spektrum
- Ikke kategoriseret Raymarine
- Ikke kategoriseret Petzl
- Ikke kategoriseret Black Diamond
- Ikke kategoriseret Dinstar
- Ikke kategoriseret Mobeye
- Ikke kategoriseret Vileda
- Ikke kategoriseret ADE
- Ikke kategoriseret Danby
- Ikke kategoriseret Brennenstuhl
- Ikke kategoriseret Sogo
- Ikke kategoriseret Alba
- Ikke kategoriseret RCA
- Ikke kategoriseret Koenic
- Ikke kategoriseret Scarlett
- Ikke kategoriseret Studiologic
- Ikke kategoriseret Rupert Neve Designs
- Ikke kategoriseret Cellular Line
- Ikke kategoriseret Ubiquiti Networks
- Ikke kategoriseret Izzy
- Ikke kategoriseret AVerMedia
- Ikke kategoriseret Cotech
- Ikke kategoriseret BlueWalker
- Ikke kategoriseret Aeon Labs
- Ikke kategoriseret Focus Electrics
- Ikke kategoriseret NOCO
- Ikke kategoriseret Keith MCmillen
- Ikke kategoriseret MTD
- Ikke kategoriseret ECG
- Ikke kategoriseret Traxxas
- Ikke kategoriseret Allen & Heath
- Ikke kategoriseret Jamo
- Ikke kategoriseret Playmobil
- Ikke kategoriseret Chamberlain
- Ikke kategoriseret Intergas
- Ikke kategoriseret Projecta
- Ikke kategoriseret GAO
- Ikke kategoriseret EnGenius
- Ikke kategoriseret AV:link
- Ikke kategoriseret FiiO
- Ikke kategoriseret Countryman
- Ikke kategoriseret Reolink
- Ikke kategoriseret DBX
- Ikke kategoriseret 4ms
- Ikke kategoriseret Snow Joe
- Ikke kategoriseret Warm Audio
- Ikke kategoriseret Devolo
- Ikke kategoriseret Solis
- Ikke kategoriseret Draper
- Ikke kategoriseret Saturn
- Ikke kategoriseret Grandstream
- Ikke kategoriseret Elgato
- Ikke kategoriseret Aerial
- Ikke kategoriseret TC Electronic
- Ikke kategoriseret Digigram
- Ikke kategoriseret Bialetti
- Ikke kategoriseret Trebs
- Ikke kategoriseret TeachLogic
- Ikke kategoriseret Endorphin.es
- Ikke kategoriseret EVE
- Ikke kategoriseret Wamsler
- Ikke kategoriseret Prixton
- Ikke kategoriseret Simrad
- Ikke kategoriseret EOTech
- Ikke kategoriseret MaxCom
- Ikke kategoriseret Horizon Fitness
- Ikke kategoriseret Radial Engineering
- Ikke kategoriseret Gossen
- Ikke kategoriseret Fritel
- Ikke kategoriseret Patton
- Ikke kategoriseret ColorKey
- Ikke kategoriseret Jumbo
- Ikke kategoriseret Galaxy Audio
- Ikke kategoriseret Alesis
- Ikke kategoriseret Renkforce
- Ikke kategoriseret Marshall Electronics
- Ikke kategoriseret Axxent
- Ikke kategoriseret Furuno
- Ikke kategoriseret Chord
- Ikke kategoriseret Eldom
- Ikke kategoriseret Navitel
- Ikke kategoriseret Cardo
- Ikke kategoriseret H.Koenig
- Ikke kategoriseret Hazet
- Ikke kategoriseret Alto
- Ikke kategoriseret Maxview
- Ikke kategoriseret Shape
- Ikke kategoriseret ThinkFun
- Ikke kategoriseret Shokz
- Ikke kategoriseret GVM
- Ikke kategoriseret Transcend
- Ikke kategoriseret Sachtler
- Ikke kategoriseret Ventev
- Ikke kategoriseret Sonnenkönig
- Ikke kategoriseret Manhattan
- Ikke kategoriseret SPC
- Ikke kategoriseret Aquatic AV
- Ikke kategoriseret Proline
- Ikke kategoriseret Xtorm
- Ikke kategoriseret BodyCraft
- Ikke kategoriseret Hunter
- Ikke kategoriseret Caliber
- Ikke kategoriseret ZTE
- Ikke kategoriseret Pentatech
- Ikke kategoriseret Waves
- Ikke kategoriseret Termozeta
- Ikke kategoriseret Dormakaba
- Ikke kategoriseret Waldbeck
- Ikke kategoriseret Calligaris .com
- Ikke kategoriseret Park Tool
- Ikke kategoriseret OneConcept
- Ikke kategoriseret Hobart
- Ikke kategoriseret Native Instruments
- Ikke kategoriseret Audiolab
- Ikke kategoriseret I3-Technologies
- Ikke kategoriseret Mikrotik
- Ikke kategoriseret Viessmann
- Ikke kategoriseret Crock-Pot
- Ikke kategoriseret Segway
- Ikke kategoriseret Blaser
- Ikke kategoriseret ProTeam
- Ikke kategoriseret Switel
- Ikke kategoriseret Deaf Bonce
- Ikke kategoriseret Stirling
- Ikke kategoriseret Electro Harmonix
- Ikke kategoriseret EcoFlow
- Ikke kategoriseret WAGAN
- Ikke kategoriseret A4Tech
- Ikke kategoriseret AVtech
- Ikke kategoriseret Arkon
- Ikke kategoriseret APart
- Ikke kategoriseret Mophie
- Ikke kategoriseret Laurastar
- Ikke kategoriseret Trio Lighting
- Ikke kategoriseret Mattel
- Ikke kategoriseret LogiLink
- Ikke kategoriseret Vortex
- Ikke kategoriseret Michigan
- Ikke kategoriseret Eberspacher
- Ikke kategoriseret Easy Home
- Ikke kategoriseret Testo
- Ikke kategoriseret Ergotron
- Ikke kategoriseret Be Cool
- Ikke kategoriseret Nobo
- Ikke kategoriseret Gladiator
- Ikke kategoriseret Polti
- Ikke kategoriseret Barska
- Ikke kategoriseret Portech
- Ikke kategoriseret GW Instek
- Ikke kategoriseret Brandson
- Ikke kategoriseret Simplecom
- Ikke kategoriseret Tandberg Data
- Ikke kategoriseret Ecoteck
- Ikke kategoriseret IK Multimedia
- Ikke kategoriseret Ravensburger
- Ikke kategoriseret Dreame
- Ikke kategoriseret Saitek
- Ikke kategoriseret Audeze
- Ikke kategoriseret Lasko
- Ikke kategoriseret RGV
- Ikke kategoriseret Eta
- Ikke kategoriseret Asaklitt
- Ikke kategoriseret Bullet
- Ikke kategoriseret Inglesina
- Ikke kategoriseret Turmix
- Ikke kategoriseret Viper
- Ikke kategoriseret Amazon
- Ikke kategoriseret Orbis
- Ikke kategoriseret HTC
- Ikke kategoriseret Bella
- Ikke kategoriseret Lynx
- Ikke kategoriseret Antec
- Ikke kategoriseret GoClever
- Ikke kategoriseret Yeastar
- Ikke kategoriseret Lupilu
- Ikke kategoriseret Qualcast
- Ikke kategoriseret DeLOCK
- Ikke kategoriseret Crucial
- Ikke kategoriseret DoorBird
- Ikke kategoriseret Navionics
- Ikke kategoriseret Max Pro
- Ikke kategoriseret Timbersled
- Ikke kategoriseret Orion
- Ikke kategoriseret Duux
- Ikke kategoriseret Eminent
- Ikke kategoriseret Brevi
- Ikke kategoriseret Kramer
- Ikke kategoriseret Antari
- Ikke kategoriseret Stiebel Eltron
- Ikke kategoriseret NutriBullet
- Ikke kategoriseret Rotel
- Ikke kategoriseret Metra
- Ikke kategoriseret QSC
- Ikke kategoriseret Kalorik
- Ikke kategoriseret Connect IT
- Ikke kategoriseret Martin
- Ikke kategoriseret Snazzy FX
- Ikke kategoriseret Bretford
- Ikke kategoriseret Hanwha
- Ikke kategoriseret MagTek
- Ikke kategoriseret Vacmaster
- Ikke kategoriseret ILive
- Ikke kategoriseret Reginox
- Ikke kategoriseret LaCie
- Ikke kategoriseret Vermeiren
- Ikke kategoriseret Gemini
- Ikke kategoriseret Intenso
- Ikke kategoriseret Black Lion Audio
- Ikke kategoriseret Naim
- Ikke kategoriseret Solid State Logic
- Ikke kategoriseret Tiptop Audio
- Ikke kategoriseret Paradigm
- Ikke kategoriseret Citronic
- Ikke kategoriseret Generac
- Ikke kategoriseret Thomann
- Ikke kategoriseret SuperTooth
- Ikke kategoriseret Etymotic
- Ikke kategoriseret Fantec
- Ikke kategoriseret Hasbro
- Ikke kategoriseret Tamiya
- Ikke kategoriseret Cecotec
- Ikke kategoriseret Escene
- Ikke kategoriseret ARRI
- Ikke kategoriseret Berg
- Ikke kategoriseret Cosori
- Ikke kategoriseret Hähnel
- Ikke kategoriseret Cinderella
- Ikke kategoriseret Rinnai
- Ikke kategoriseret Brydge
- Ikke kategoriseret Strymon
- Ikke kategoriseret Motu
- Ikke kategoriseret NOCH
- Ikke kategoriseret Grothe
- Ikke kategoriseret Rotho Babydesign
- Ikke kategoriseret Truper
- Ikke kategoriseret Jurox
- Ikke kategoriseret RDL
- Ikke kategoriseret Baby Brezza
- Ikke kategoriseret Lanberg
- Ikke kategoriseret Hive
- Ikke kategoriseret Noise Engineering
- Ikke kategoriseret BOHLT
- Ikke kategoriseret NAV-TV
- Ikke kategoriseret Senal
- Ikke kategoriseret Siedle
- Ikke kategoriseret BirdDog
- Ikke kategoriseret Mean Well
- Ikke kategoriseret Solac
- Ikke kategoriseret Osprey
- Ikke kategoriseret Evolveo
- Ikke kategoriseret Edision
- Ikke kategoriseret Audioline
- Ikke kategoriseret Roadstar
- Ikke kategoriseret BT
- Ikke kategoriseret VIZIO
- Ikke kategoriseret Clarion
- Ikke kategoriseret Royal Catering
- Ikke kategoriseret After Later Audio
- Ikke kategoriseret Sole Fitness
- Ikke kategoriseret Genius
- Ikke kategoriseret Watson
- Ikke kategoriseret Kipor
- Ikke kategoriseret IHome
- Ikke kategoriseret Rittal
- Ikke kategoriseret Atdec
- Ikke kategoriseret Cablexpert
- Ikke kategoriseret Yard Force
- Ikke kategoriseret Lazer
- Ikke kategoriseret EarthQuaker Devices
- Ikke kategoriseret Sound Devices
- Ikke kategoriseret Metabolic Devices
- Ikke kategoriseret Alright Devices
- Ikke kategoriseret Wharfedale
- Ikke kategoriseret Technika
- Ikke kategoriseret Anslut
- Ikke kategoriseret Zagg
- Ikke kategoriseret BakkerElkhuizen
- Ikke kategoriseret Quadro
- Ikke kategoriseret MSR
- Ikke kategoriseret Universal Audio
- Ikke kategoriseret Hercules
- Ikke kategoriseret Clingo
- Ikke kategoriseret Hexaglot
- Ikke kategoriseret Kopp
- Ikke kategoriseret Prowise
- Ikke kategoriseret Ravelli
- Ikke kategoriseret Efbe-Schott
- Ikke kategoriseret KJB Security Products
- Ikke kategoriseret Valueline
- Ikke kategoriseret Neumärker
- Ikke kategoriseret Seiki
- Ikke kategoriseret Siku
- Ikke kategoriseret GLORIA
- Ikke kategoriseret Ozone
- Ikke kategoriseret M-Audio
- Ikke kategoriseret Eton
- Ikke kategoriseret Monster
- Ikke kategoriseret Bauhn
- Ikke kategoriseret Rossmax
- Ikke kategoriseret PVI
- Ikke kategoriseret V7
- Ikke kategoriseret Fender
- Ikke kategoriseret Ideal
- Ikke kategoriseret Duke Fitness
- Ikke kategoriseret GPO
- Ikke kategoriseret Sirius
- Ikke kategoriseret 3B
- Ikke kategoriseret Vision
- Ikke kategoriseret Vantec
- Ikke kategoriseret MaxSMART
- Ikke kategoriseret Vorago
- Ikke kategoriseret Austrian Audio
- Ikke kategoriseret Wiko
- Ikke kategoriseret Barazza
- Ikke kategoriseret Ruger
- Ikke kategoriseret Primera
- Ikke kategoriseret Enduro
- Ikke kategoriseret Star Micronics
- Ikke kategoriseret Atomos
- Ikke kategoriseret BRA
- Ikke kategoriseret Majestic
- Ikke kategoriseret ESTAR
- Ikke kategoriseret Lorelli
- Ikke kategoriseret BWT
- Ikke kategoriseret Audiovox
- Ikke kategoriseret Analog Way
- Ikke kategoriseret Quantum
- Ikke kategoriseret Palson
- Ikke kategoriseret Electrosmith
- Ikke kategoriseret MuxLab
- Ikke kategoriseret Forza
- Ikke kategoriseret Fibaro
- Ikke kategoriseret Panduit
- Ikke kategoriseret Multimetrix
- Ikke kategoriseret Bentley
- Ikke kategoriseret Nanlite
- Ikke kategoriseret Umidigi
- Ikke kategoriseret Cool Head
- Ikke kategoriseret SAMAC
- Ikke kategoriseret Morel
- Ikke kategoriseret Traeger
- Ikke kategoriseret Beper
- Ikke kategoriseret Meireles
- Ikke kategoriseret Crofton
- Ikke kategoriseret Cricut
- Ikke kategoriseret Nostalgia
- Ikke kategoriseret Yukon
- Ikke kategoriseret Jabsco
- Ikke kategoriseret Blade
- Ikke kategoriseret Telstra
- Ikke kategoriseret Akasa
- Ikke kategoriseret Manitowoc
- Ikke kategoriseret Steinberg
- Ikke kategoriseret Arris
- Ikke kategoriseret Axis
- Ikke kategoriseret PellX
- Ikke kategoriseret N8WERK
- Ikke kategoriseret Spypoint
- Ikke kategoriseret Marvel
- Ikke kategoriseret Eurolite
- Ikke kategoriseret Stageworx
- Ikke kategoriseret ASA
- Ikke kategoriseret Dr. Brown's
- Ikke kategoriseret Vivitar
- Ikke kategoriseret Snom
- Ikke kategoriseret Eventide
- Ikke kategoriseret Eltako
- Ikke kategoriseret Mackie
- Ikke kategoriseret ACTi
- Ikke kategoriseret Polaris
- Ikke kategoriseret PowerXL
- Ikke kategoriseret Commercial Chef
- Ikke kategoriseret Emeril Lagasse
- Ikke kategoriseret CRUX
- Ikke kategoriseret Riccar
- Ikke kategoriseret Tower
- Ikke kategoriseret Milan
- Ikke kategoriseret Lionelo
- Ikke kategoriseret Avalon
- Ikke kategoriseret Wavtech
- Ikke kategoriseret Xantech
- Ikke kategoriseret Faytech
- Ikke kategoriseret Walrus Audio
- Ikke kategoriseret Reloop
- Ikke kategoriseret AudioThing
- Ikke kategoriseret Mebus
- Ikke kategoriseret Krom
- Ikke kategoriseret Team
- Ikke kategoriseret Schuberth
- Ikke kategoriseret Contour Design
- Ikke kategoriseret Purpleline
- Ikke kategoriseret Morley
- Ikke kategoriseret X-Sense
- Ikke kategoriseret Palram
- Ikke kategoriseret EMG
- Ikke kategoriseret Kunath
- Ikke kategoriseret Endress
- Ikke kategoriseret Kessler
- Ikke kategoriseret Tecnoinox
- Ikke kategoriseret Morris
- Ikke kategoriseret Meec Tools
- Ikke kategoriseret Akrobat
- Ikke kategoriseret Brüder Mannesmann
- Ikke kategoriseret Avantone Pro
- Ikke kategoriseret Noma
- Ikke kategoriseret Crest Audio
- Ikke kategoriseret Needit
- Ikke kategoriseret Hario
- Ikke kategoriseret Ansco
- Ikke kategoriseret Kasda
- Ikke kategoriseret XGIMI
- Ikke kategoriseret Bright Spark
- Ikke kategoriseret SIG Sauer
- Ikke kategoriseret Charge Amps
- Ikke kategoriseret Split
- Ikke kategoriseret Maze
- Ikke kategoriseret Dubatti
- Ikke kategoriseret Norton Clipper
- Ikke kategoriseret Goliath
- Ikke kategoriseret Ergotech
- Ikke kategoriseret Lindell Audio
- Ikke kategoriseret Xplora
- Ikke kategoriseret Coolabah Outdoor
- Ikke kategoriseret Thronmax
- Ikke kategoriseret Valeton
- Ikke kategoriseret Ledlenser
- Ikke kategoriseret EQ-3
- Ikke kategoriseret Iogear
- Ikke kategoriseret Clean Air Optima
- Ikke kategoriseret Chauvet
- Ikke kategoriseret Kenmore
- Ikke kategoriseret Brentwood
- Ikke kategoriseret Avanti
- Ikke kategoriseret EVOline
- Ikke kategoriseret JANDY
- Ikke kategoriseret XP-PEN
- Ikke kategoriseret Digi
- Ikke kategoriseret ATen
- Ikke kategoriseret Vestel
- Ikke kategoriseret U-Line
- Ikke kategoriseret Shure
- Ikke kategoriseret Sangean
- Ikke kategoriseret Vimar
- Ikke kategoriseret Power Dynamics
- Ikke kategoriseret Continental Edison
- Ikke kategoriseret Dynaudio
- Ikke kategoriseret Empress Effects
- Ikke kategoriseret Oricom
- Ikke kategoriseret Plustek
- Ikke kategoriseret Rockford Fosgate
- Ikke kategoriseret Proaim
- Ikke kategoriseret Klein Tools
- Ikke kategoriseret Perixx
- Ikke kategoriseret Oregon Scientific
- Ikke kategoriseret Iiyama
- Ikke kategoriseret Grace Design
- Ikke kategoriseret Aluratek
- Ikke kategoriseret PeakTech
- Ikke kategoriseret Keurig
- Ikke kategoriseret Smart-AVI
- Ikke kategoriseret GPX
- Ikke kategoriseret Schwinn
- Ikke kategoriseret VS Sassoon
- Ikke kategoriseret Martin Logan
- Ikke kategoriseret Arendo
- Ikke kategoriseret Corbero
- Ikke kategoriseret Zephyr
- Ikke kategoriseret Troy-Bilt
- Ikke kategoriseret Microchip
- Ikke kategoriseret MBM
- Ikke kategoriseret JIMMY
- Ikke kategoriseret Rigol
- Ikke kategoriseret Chief
- Ikke kategoriseret Dahua Technology
- Ikke kategoriseret Artusi
- Ikke kategoriseret Chacon
- Ikke kategoriseret Fosi Audio
- Ikke kategoriseret BrightSign
- Ikke kategoriseret Uni-T
- Ikke kategoriseret Orima
- Ikke kategoriseret Manfrotto
- Ikke kategoriseret Lenoxx
- Ikke kategoriseret Speed-Link
- Ikke kategoriseret SereneLife
- Ikke kategoriseret Terratec
- Ikke kategoriseret Kospel
- Ikke kategoriseret ZKTeco
- Ikke kategoriseret Lexibook
- Ikke kategoriseret Remko
- Ikke kategoriseret Vivolink
- Ikke kategoriseret My Wall
- Ikke kategoriseret Intel
- Ikke kategoriseret AG Neovo
- Ikke kategoriseret Scotsman
- Ikke kategoriseret Music Hero
- Ikke kategoriseret Phoenix Gold
- Ikke kategoriseret Stabo
- Ikke kategoriseret Magic Chef
- Ikke kategoriseret Sharkoon
- Ikke kategoriseret Memphis Audio
- Ikke kategoriseret Duronic
- Ikke kategoriseret Vonyx
- Ikke kategoriseret EtiamPro
- Ikke kategoriseret First Alert
- Ikke kategoriseret Spin Master
- Ikke kategoriseret Scosche
- Ikke kategoriseret Speco Technologies
- Ikke kategoriseret Prestigio
- Ikke kategoriseret Bavaria By Einhell
- Ikke kategoriseret Joy-It
- Ikke kategoriseret Boss
- Ikke kategoriseret Ruark Audio
- Ikke kategoriseret Spelsberg
- Ikke kategoriseret Nexa
- Ikke kategoriseret Klark Teknik
- Ikke kategoriseret 8BitDo
- Ikke kategoriseret Supermicro
- Ikke kategoriseret Fresh 'n Rebel
- Ikke kategoriseret MyPhone
- Ikke kategoriseret Broan
- Ikke kategoriseret True
- Ikke kategoriseret StarTech.com
- Ikke kategoriseret Draytek
- Ikke kategoriseret Conceptronic
- Ikke kategoriseret Realme
- Ikke kategoriseret Noctua
- Ikke kategoriseret Rocstor
- Ikke kategoriseret Wiha
- Ikke kategoriseret Bluetti
- Ikke kategoriseret Duracell
- Ikke kategoriseret S.M.S.L
- Ikke kategoriseret Bestron
- Ikke kategoriseret Philco
- Ikke kategoriseret Livarno Lux
- Ikke kategoriseret Waring Commercial
- Ikke kategoriseret HT Instruments
- Ikke kategoriseret Teltonika
- Ikke kategoriseret Turbosound
- Ikke kategoriseret Benavent
- Ikke kategoriseret FBT
- Ikke kategoriseret Doepke
- Ikke kategoriseret TrueLife
- Ikke kategoriseret Pulsar
- Ikke kategoriseret InLine
- Ikke kategoriseret Kern
- Ikke kategoriseret Sôlt
- Ikke kategoriseret Novy
- Ikke kategoriseret Focusrite
- Ikke kategoriseret AcuRite
- Ikke kategoriseret Bunn
- Ikke kategoriseret Adder
- Ikke kategoriseret IStarUSA
- Ikke kategoriseret Ciclo
- Ikke kategoriseret Toolcraft
- Ikke kategoriseret Avidsen
- Ikke kategoriseret Chauvin Arnoux
- Ikke kategoriseret Cameo
- Ikke kategoriseret Blackstar
- Ikke kategoriseret Blackmagic Design
- Ikke kategoriseret BDI
- Ikke kategoriseret Crestron
- Ikke kategoriseret DAP-Audio
- Ikke kategoriseret PATLITE
- Ikke kategoriseret Kunft
- Ikke kategoriseret Nitecore
- Ikke kategoriseret Revel
- Ikke kategoriseret Taylor
- Ikke kategoriseret American International
- Ikke kategoriseret SPL
- Ikke kategoriseret Ground Zero
- Ikke kategoriseret Simpson
- Ikke kategoriseret Domyos
- Ikke kategoriseret Vincent
- Ikke kategoriseret EZ Dupe
- Ikke kategoriseret Salewa
- Ikke kategoriseret Crimson
- Ikke kategoriseret Showtec
- Ikke kategoriseret Subaru
- Ikke kategoriseret Kelty
- Ikke kategoriseret Lindy
- Ikke kategoriseret Ortofon
- Ikke kategoriseret Fuxtec
- Ikke kategoriseret Tineco
- Ikke kategoriseret Summit
- Ikke kategoriseret GoGen
- Ikke kategoriseret Kogan
- Ikke kategoriseret Russound
- Ikke kategoriseret LERAN
- Ikke kategoriseret Audison
- Ikke kategoriseret Best Service
- Ikke kategoriseret ComNet
- Ikke kategoriseret Crown
- Ikke kategoriseret AVMATRIX
- Ikke kategoriseret BH Fitness
- Ikke kategoriseret Joby
- Ikke kategoriseret Levenhuk
- Ikke kategoriseret Megger
- Ikke kategoriseret President
- Ikke kategoriseret Barco
- Ikke kategoriseret Healthy Choice
- Ikke kategoriseret Sungrow
- Ikke kategoriseret DCG
- Ikke kategoriseret Coyote
- Ikke kategoriseret New Pol
- Ikke kategoriseret AGM
- Ikke kategoriseret Kanto
- Ikke kategoriseret Oliveri
- Ikke kategoriseret Hammond
- Ikke kategoriseret Gravity
- Ikke kategoriseret ADATA
- Ikke kategoriseret Shindaiwa
- Ikke kategoriseret Ixxat
- Ikke kategoriseret Delta
- Ikke kategoriseret SMART Technologies
- Ikke kategoriseret Scala
- Ikke kategoriseret Emerson
- Ikke kategoriseret Lumantek
- Ikke kategoriseret Elektrobock
- Ikke kategoriseret Lancom
- Ikke kategoriseret Ravanson
- Ikke kategoriseret Rolls
- Ikke kategoriseret Kugoo
- Ikke kategoriseret Waterpik
- Ikke kategoriseret Geomag
- Ikke kategoriseret MooreCo
- Ikke kategoriseret Conair
- Ikke kategoriseret Esylux
- Ikke kategoriseret Proviel
- Ikke kategoriseret Magnus
- Ikke kategoriseret Fulgor Milano
- Ikke kategoriseret Hoshizaki
- Ikke kategoriseret BLANCO
- Ikke kategoriseret Cyrus
- Ikke kategoriseret Phonak
- Ikke kategoriseret Airlux
- Ikke kategoriseret Solplanet
- Ikke kategoriseret Ambient Weather
- Ikke kategoriseret Kindercraft
- Ikke kategoriseret Foster
- Ikke kategoriseret BLUEPALM
- Ikke kategoriseret NEO Tools
- Ikke kategoriseret Energizer
- Ikke kategoriseret RIKON
- Ikke kategoriseret Werma
- Ikke kategoriseret Gerni
- Ikke kategoriseret Fusion
- Ikke kategoriseret Definitive Technology
- Ikke kategoriseret Kemo
- Ikke kategoriseret Hacienda
- Ikke kategoriseret Numatic
- Ikke kategoriseret Delta Dore
- Ikke kategoriseret Insignia
- Ikke kategoriseret Adastra
- Ikke kategoriseret SIME
- Ikke kategoriseret Lectrosonics
- Ikke kategoriseret Smith-Victor
- Ikke kategoriseret Sunding
- Ikke kategoriseret AstralPool
- Ikke kategoriseret Veritas
- Ikke kategoriseret Natec
- Ikke kategoriseret Audac
- Ikke kategoriseret JETI
- Ikke kategoriseret Konig & Meyer
- Ikke kategoriseret Promise Technology
- Ikke kategoriseret Oster
- Ikke kategoriseret Neutrik
- Ikke kategoriseret CYP
- Ikke kategoriseret RAVPower
- Ikke kategoriseret Sitecom
- Ikke kategoriseret LC-Power
- Ikke kategoriseret TDE Instruments
- Ikke kategoriseret Atlas Sound
- Ikke kategoriseret Consul
- Ikke kategoriseret Jocel
- Ikke kategoriseret Olight
- Ikke kategoriseret Biostar
- Ikke kategoriseret Broil King
- Ikke kategoriseret Beyerdynamic
- Ikke kategoriseret Heller
- Ikke kategoriseret Finnlo
- Ikke kategoriseret Kayoba
- Ikke kategoriseret AKG
- Ikke kategoriseret AEA
- Ikke kategoriseret Millenium
- Ikke kategoriseret Signature
- Ikke kategoriseret DiO
- Ikke kategoriseret AMX
- Ikke kategoriseret Waterco
- Ikke kategoriseret Minox
- Ikke kategoriseret Jack Wolfskin
- Ikke kategoriseret Ufesa
- Ikke kategoriseret ADDAC System
- Ikke kategoriseret Harley Benton
- Ikke kategoriseret Tannoy
- Ikke kategoriseret Homematic IP
- Ikke kategoriseret InAlto
- Ikke kategoriseret Keystone
- Ikke kategoriseret Ultimate
- Ikke kategoriseret H-Tronic
- Ikke kategoriseret MXL
- Ikke kategoriseret Intellinet
- Ikke kategoriseret Satechi
- Ikke kategoriseret DreamGEAR
- Ikke kategoriseret V-TAC
- Ikke kategoriseret Iomega
- Ikke kategoriseret Corel
- Ikke kategoriseret August
- Ikke kategoriseret Xoro
- Ikke kategoriseret AudioControl
- Ikke kategoriseret JILONG
- Ikke kategoriseret DeepCool
- Ikke kategoriseret RCBS
- Ikke kategoriseret Manta
- Ikke kategoriseret Whale
- Ikke kategoriseret Vornado
- Ikke kategoriseret Heritage Audio
- Ikke kategoriseret Holzmann
- Ikke kategoriseret Godex
- Ikke kategoriseret Burris
- Ikke kategoriseret HyperX
- Ikke kategoriseret Losi
- Ikke kategoriseret MARTOR
- Ikke kategoriseret ResMed
- Ikke kategoriseret Hamron
- Ikke kategoriseret Enphase
- Ikke kategoriseret Mooer
- Ikke kategoriseret Audiotec Fischer
- Ikke kategoriseret Growatt
- Ikke kategoriseret Maglite
- Ikke kategoriseret Dash
- Ikke kategoriseret Bugera
- Ikke kategoriseret IDIS
- Ikke kategoriseret Lofrans
- Ikke kategoriseret Legrand
- Ikke kategoriseret Kingston
- Ikke kategoriseret Compex
- Ikke kategoriseret OM SYSTEM
- Ikke kategoriseret CTA Digital
- Ikke kategoriseret Lincoln Electric
- Ikke kategoriseret Tepro
- Ikke kategoriseret EMSA
- Ikke kategoriseret Silverstone
- Ikke kategoriseret Impact
- Ikke kategoriseret Shelly
- Ikke kategoriseret TVLogic
- Ikke kategoriseret SkyRC
- Ikke kategoriseret Aim TTi
- Ikke kategoriseret InfaSecure
- Ikke kategoriseret SunBriteTV
- Ikke kategoriseret Audix
- Ikke kategoriseret Märklin
- Ikke kategoriseret Kidde
- Ikke kategoriseret Geovision
- Ikke kategoriseret Schwaiger
- Ikke kategoriseret ClimeMET
- Ikke kategoriseret Yamato
- Ikke kategoriseret Ibiza Sound
- Ikke kategoriseret Postium
- Ikke kategoriseret Sound Machines
- Ikke kategoriseret Wilson
- Ikke kategoriseret Lite-On
- Ikke kategoriseret GAM
- Ikke kategoriseret Campart
- Ikke kategoriseret Steren
- Ikke kategoriseret Ghibli
- Ikke kategoriseret Razor
- Ikke kategoriseret Evenflo
- Ikke kategoriseret Jinbei
- Ikke kategoriseret Gossen Metrawatt
- Ikke kategoriseret Multibrackets
- Ikke kategoriseret LifeSpan
- Ikke kategoriseret Christmas Time
- Ikke kategoriseret Neewer
- Ikke kategoriseret Heitronic
- Ikke kategoriseret Lund
- Ikke kategoriseret Ocean Matrix
- Ikke kategoriseret MAK
- Ikke kategoriseret Comprehensive
- Ikke kategoriseret Dobot
- Ikke kategoriseret Toro
- Ikke kategoriseret Orava
- Ikke kategoriseret PowerBass
- Ikke kategoriseret Ocean Way Audio
- Ikke kategoriseret Elmo
- Ikke kategoriseret Yato
- Ikke kategoriseret Gastronoma
- Ikke kategoriseret Reflexion
- Ikke kategoriseret SurgeX
- Ikke kategoriseret T.I.P.
- Ikke kategoriseret Bolt
- Ikke kategoriseret Digitalinx
- Ikke kategoriseret Dot Line
- Ikke kategoriseret Easyrig
- Ikke kategoriseret Xvive
- Ikke kategoriseret Anton/Bauer
- Ikke kategoriseret QOMO
- Ikke kategoriseret Kaiser
- Ikke kategoriseret Anybus
- Ikke kategoriseret Equip
- Ikke kategoriseret WHD
- Ikke kategoriseret Match
- Ikke kategoriseret Alfatron
- Ikke kategoriseret APA
- Ikke kategoriseret HiFi ROSE
- Ikke kategoriseret Govee
- Ikke kategoriseret SoundMagic
- Ikke kategoriseret Beha-Amprobe
- Ikke kategoriseret Sumiko
- Ikke kategoriseret Savio
- Ikke kategoriseret Graphite
- Ikke kategoriseret XQ-lite
- Ikke kategoriseret Diforo
- Ikke kategoriseret Nord
- Ikke kategoriseret Indiana Line
- Ikke kategoriseret Extralink
- Ikke kategoriseret Esperanza
- Ikke kategoriseret Cocraft
- Ikke kategoriseret Emko
- Ikke kategoriseret Sebo
- Ikke kategoriseret Arctic Cooling
- Ikke kategoriseret Topeak
- Ikke kategoriseret Maestro
- Ikke kategoriseret Salicru
- Ikke kategoriseret Haeger
- Ikke kategoriseret TechBite
- Ikke kategoriseret Lupine
- Ikke kategoriseret Ugreen
- Ikke kategoriseret Classé
- Ikke kategoriseret EAT
- Ikke kategoriseret TensCare
- Ikke kategoriseret Hikmicro
- Ikke kategoriseret REVO
- Ikke kategoriseret Maytronics
- Ikke kategoriseret DPM
- Ikke kategoriseret Create
- Ikke kategoriseret Inverx
- Ikke kategoriseret Audioengine
- Ikke kategoriseret PCE
- Ikke kategoriseret Beautifly
- Ikke kategoriseret Nutrichef
- Ikke kategoriseret Musical Fidelity
- Ikke kategoriseret Advance Acoustic
- Ikke kategoriseret NuPrime
- Ikke kategoriseret REL Acoustics
- Ikke kategoriseret Mistral
- Ikke kategoriseret Adventuridge
- Ikke kategoriseret Casa Deco
- Ikke kategoriseret Gamdias
- Ikke kategoriseret Ketron
- Ikke kategoriseret Aqara
- Ikke kategoriseret Blackburn
- Ikke kategoriseret HMS Premium
- Ikke kategoriseret Ernitec
- Ikke kategoriseret Knog
- Ikke kategoriseret Zotac
- Ikke kategoriseret PRIME3
- Ikke kategoriseret Media-Tech
- Ikke kategoriseret Glem Gas
- Ikke kategoriseret IBEAM
- Ikke kategoriseret XCell
- Ikke kategoriseret Bearware
- Ikke kategoriseret I.safe Mobile
- Ikke kategoriseret Artsound
- Ikke kategoriseret Tecnoware
- Ikke kategoriseret Yellow Garden Line
- Ikke kategoriseret Oreck
- Ikke kategoriseret Microair
- Ikke kategoriseret Flama
- Ikke kategoriseret Sevenoak
- Ikke kategoriseret Perfect Christmas
- Ikke kategoriseret Core SWX
- Ikke kategoriseret BSS Audio
- Ikke kategoriseret Anywhere Cart
- Ikke kategoriseret Glide Gear
- Ikke kategoriseret Hosa
- Ikke kategoriseret Gen Energy
- Ikke kategoriseret Fiilex
- Ikke kategoriseret Sonel
- Ikke kategoriseret BZBGear
- Ikke kategoriseret CEDAR
- Ikke kategoriseret Intellijel
- Ikke kategoriseret Key Digital
- Ikke kategoriseret Murideo
- Ikke kategoriseret Lewitt
- Ikke kategoriseret KanexPro
- Ikke kategoriseret Sonifex
- Ikke kategoriseret ChyTV
- Ikke kategoriseret K&M
- Ikke kategoriseret Erica Synths
- Ikke kategoriseret Gefen
- Ikke kategoriseret Drake
- Ikke kategoriseret Explore Scientific
- Ikke kategoriseret Trijicon
- Ikke kategoriseret Lemair
- Ikke kategoriseret Wimberley
- Ikke kategoriseret Vertex
- Ikke kategoriseret Sky-Watcher
- Ikke kategoriseret Serpent
- Ikke kategoriseret Platinum Tools
- Ikke kategoriseret ARC
- Ikke kategoriseret Pawa
- Ikke kategoriseret Soundsphere
- Ikke kategoriseret Cranborne Audio
- Ikke kategoriseret Lian Li
- Ikke kategoriseret Panamax
- Ikke kategoriseret Kahayan
- Ikke kategoriseret TV One
- Ikke kategoriseret Sescom
- Ikke kategoriseret PTZ Optics
- Ikke kategoriseret OWC
- Ikke kategoriseret Whirlwind
- Ikke kategoriseret Apantac
- Ikke kategoriseret SmallRig
- Ikke kategoriseret Robus
- Ikke kategoriseret RGBlink
- Ikke kategoriseret ToughTested
- Ikke kategoriseret Stamina
- Ikke kategoriseret Rosco
- Ikke kategoriseret Ewbank
- Ikke kategoriseret Beverage-Air
- Ikke kategoriseret AVer
- Ikke kategoriseret KiddyGuard
- Ikke kategoriseret Daitsu
- Ikke kategoriseret Ferguson
- Ikke kategoriseret Moxa
- Ikke kategoriseret Wolfcraft
- Ikke kategoriseret Seaward
- Ikke kategoriseret Thermador
- Ikke kategoriseret SRS
- Ikke kategoriseret Budda
- Ikke kategoriseret Mac Tools
- Ikke kategoriseret Kambrook
- Ikke kategoriseret Goodis
- Ikke kategoriseret Acefast
- Ikke kategoriseret Mad Dog
- Ikke kategoriseret Revlon
- Ikke kategoriseret Oromed
- Ikke kategoriseret Xmusic
- Ikke kategoriseret Xomax
- Ikke kategoriseret Marbo Sport
- Ikke kategoriseret Grixx
- Ikke kategoriseret Bea-fon
- Ikke kategoriseret Atosa
- Ikke kategoriseret Waterdrop
- Ikke kategoriseret Profile
- Ikke kategoriseret Hestan
- Ikke kategoriseret Aconatic
- Ikke kategoriseret Blustream
- Ikke kategoriseret C2G
- Ikke kategoriseret WyreStorm
- Ikke kategoriseret Artecta
- Ikke kategoriseret Agfa
- Ikke kategoriseret Dangerous Music
- Ikke kategoriseret Advance
- Ikke kategoriseret A.O. Smith
- Ikke kategoriseret Allnet
- Ikke kategoriseret Aligator
- Ikke kategoriseret Alphatronics
- Ikke kategoriseret Allied Telesis
- Ikke kategoriseret Alienware
- Ikke kategoriseret Amfra
- Ikke kategoriseret The Box
- Ikke kategoriseret Kluge
- Ikke kategoriseret Roidmi
- Ikke kategoriseret KDK
- Ikke kategoriseret IFi Audio
- Ikke kategoriseret Cabasse
- Ikke kategoriseret Eufab
- Ikke kategoriseret Twelve South
- Ikke kategoriseret Klavis
- Ikke kategoriseret Patching Panda
- Ikke kategoriseret Xaoc
- Ikke kategoriseret AYA
- Ikke kategoriseret Alcon
- Ikke kategoriseret Airlive
- Ikke kategoriseret Ampeg
- Ikke kategoriseret Amplicom
- Ikke kategoriseret Amiko
- Ikke kategoriseret Aeris
- Ikke kategoriseret Ascom
- Ikke kategoriseret Act
- Ikke kategoriseret Alpen Kreuzer
- Ikke kategoriseret Royal Sovereign
- Ikke kategoriseret ACME
- Ikke kategoriseret Dreamland
- Ikke kategoriseret Argus
- Ikke kategoriseret ATN
- Ikke kategoriseret Ziggo
- Ikke kategoriseret Intermatic
- Ikke kategoriseret Toolland
- Ikke kategoriseret Icy Box
- Ikke kategoriseret MJX
- Ikke kategoriseret Hirschmann
- Ikke kategoriseret Kruidvat
- Ikke kategoriseret Absima
- Ikke kategoriseret GMB Gaming
- Ikke kategoriseret Sanitaire
- Ikke kategoriseret Aputure
- Ikke kategoriseret Workzone
- Ikke kategoriseret Salton
- Ikke kategoriseret Proteca
- Ikke kategoriseret Body Solid
- Ikke kategoriseret Tryton
- Ikke kategoriseret Arthur Martin
- Ikke kategoriseret Tevion
- Ikke kategoriseret Proscan
- Ikke kategoriseret Kichler
- Ikke kategoriseret Jata
- Ikke kategoriseret VirtuFit
- Ikke kategoriseret Itho
- Ikke kategoriseret Q-CONNECT
- Ikke kategoriseret Sicce
- Ikke kategoriseret Monogram
- Ikke kategoriseret Maxdata
- Ikke kategoriseret Hard Head
- Ikke kategoriseret Orbit
- Ikke kategoriseret Valore
- Ikke kategoriseret Accucold
- Ikke kategoriseret Teesa
- Ikke kategoriseret KlikaanKlikuit
- Ikke kategoriseret Stinger
- Ikke kategoriseret Heinner
- Ikke kategoriseret Kensington
- Ikke kategoriseret Cresta
- Ikke kategoriseret Brigmton
- Ikke kategoriseret Sunstech
- Ikke kategoriseret Nabo
- Ikke kategoriseret Guzzanti
- Ikke kategoriseret Defy
- Ikke kategoriseret Sylvania
- Ikke kategoriseret Campomatic
- Ikke kategoriseret Igloo
- Ikke kategoriseret Swissvoice
- Ikke kategoriseret Vaude
- Ikke kategoriseret Marquant
- Ikke kategoriseret First Austria
- Ikke kategoriseret Ednet
- Ikke kategoriseret Visage
- Ikke kategoriseret Matrox
- Ikke kategoriseret Rangemaster
- Ikke kategoriseret Chipolino
- Ikke kategoriseret Nero
- Ikke kategoriseret Lumens
- Ikke kategoriseret Kubo
- Ikke kategoriseret Exagerate
- Ikke kategoriseret Air King
- Ikke kategoriseret Coby
- Ikke kategoriseret King
- Ikke kategoriseret Mac Audio
- Ikke kategoriseret TOTO
- Ikke kategoriseret Metz
- Ikke kategoriseret Kelvinator
- Ikke kategoriseret Life Fitness
- Ikke kategoriseret Belgacom
- Ikke kategoriseret Phoenix
- Ikke kategoriseret Prenatal
- Ikke kategoriseret TacTic
- Ikke kategoriseret Lescha
- Ikke kategoriseret Vello
- Ikke kategoriseret Jenn-Air
- Ikke kategoriseret R-Vent
- Ikke kategoriseret Carpigiani
- Ikke kategoriseret ICU
- Ikke kategoriseret Nacon
- Ikke kategoriseret Edesa
- Ikke kategoriseret Farberware
- Ikke kategoriseret CasaFan
- Ikke kategoriseret Milectric
- Ikke kategoriseret Macally
- Ikke kategoriseret Profoon
- Ikke kategoriseret Cilio
- Ikke kategoriseret Itho-Daalderop
- Ikke kategoriseret BabyOno
- Ikke kategoriseret SMA
- Ikke kategoriseret Kayser
- Ikke kategoriseret Safety 1st
- Ikke kategoriseret Evga
- Ikke kategoriseret AS - Schwabe
- Ikke kategoriseret Fissler
- Ikke kategoriseret Inkbird
- Ikke kategoriseret Valcom
- Ikke kategoriseret Hammer
- Ikke kategoriseret Challenge
- Ikke kategoriseret Bigben
- Ikke kategoriseret Naish
- Ikke kategoriseret Blaze
- Ikke kategoriseret Hombli
- Ikke kategoriseret Lümme
- Ikke kategoriseret Springfree
- Ikke kategoriseret Goodram
- Ikke kategoriseret Sygonix
- Ikke kategoriseret Body Sculpture
- Ikke kategoriseret Yongnuo
- Ikke kategoriseret Rocketfish
- Ikke kategoriseret Laser
- Ikke kategoriseret Creda
- Ikke kategoriseret Baninni
- Ikke kategoriseret Naxa
- Ikke kategoriseret Nemef
- Ikke kategoriseret Luvion
- Ikke kategoriseret Godrej
- Ikke kategoriseret Innovaphone
- Ikke kategoriseret Mamiya
- Ikke kategoriseret Active Era
- Ikke kategoriseret LEX
- Ikke kategoriseret Busch And Müller
- Ikke kategoriseret Cello
- Ikke kategoriseret Vakoss
- Ikke kategoriseret Zehnder
- Ikke kategoriseret Mx Onda
- Ikke kategoriseret Zenit
- Ikke kategoriseret Xterra
- Ikke kategoriseret Nanni
- Ikke kategoriseret Fuji
- Ikke kategoriseret Swissonic
- Ikke kategoriseret Elkay
- Ikke kategoriseret IHealth
- Ikke kategoriseret Logicom
- Ikke kategoriseret Alfen
- Ikke kategoriseret Nelson
- Ikke kategoriseret Havsö
- Ikke kategoriseret Aviom
- Ikke kategoriseret UPM
- Ikke kategoriseret BABY Born
- Ikke kategoriseret Miniland
- Ikke kategoriseret Ematic
- Ikke kategoriseret Winix
- Ikke kategoriseret Xavax
- Ikke kategoriseret Fantini Cosmi
- Ikke kategoriseret X4-Tech
- Ikke kategoriseret Sekonic
- Ikke kategoriseret Minolta
- Ikke kategoriseret Victor
- Ikke kategoriseret Edgestar
- Ikke kategoriseret ACE
- Ikke kategoriseret Maxicool
- Ikke kategoriseret For_Q
- Ikke kategoriseret Schaudt
- Ikke kategoriseret Avocor
- Ikke kategoriseret Lanzar
- Ikke kategoriseret McGregor
- Ikke kategoriseret Humax
- Ikke kategoriseret Swarovski Optik
- Ikke kategoriseret Gira
- Ikke kategoriseret Huion
- Ikke kategoriseret Blue
- Ikke kategoriseret Brinsea
- Ikke kategoriseret Genexis
- Ikke kategoriseret Inspire
- Ikke kategoriseret 4moms
- Ikke kategoriseret Interlogix
- Ikke kategoriseret Dnt
- Ikke kategoriseret Eizo
- Ikke kategoriseret Etekcity
- Ikke kategoriseret Café
- Ikke kategoriseret Arovec
- Ikke kategoriseret Vankyo
- Ikke kategoriseret TDK-Lambda
- Ikke kategoriseret Murr Elektronik
- Ikke kategoriseret Equator
- Ikke kategoriseret Phil And Teds
- Ikke kategoriseret Mr Handsfree
- Ikke kategoriseret Sommer
- Ikke kategoriseret DAS Audio
- Ikke kategoriseret DSC
- Ikke kategoriseret OSO
- Ikke kategoriseret Fito
- Ikke kategoriseret Ewent
- Ikke kategoriseret Shuttle
- Ikke kategoriseret Clage
- Ikke kategoriseret Cre8audio
- Ikke kategoriseret Kupper
- Ikke kategoriseret Ledger
- Ikke kategoriseret Expobar
- Ikke kategoriseret Boyo
- Ikke kategoriseret IKRA
- Ikke kategoriseret IOttie
- Ikke kategoriseret Profoto
- Ikke kategoriseret BOYA
- Ikke kategoriseret Verizon
- Ikke kategoriseret XPG
- Ikke kategoriseret Valco Baby
- Ikke kategoriseret Argoclima
- Ikke kategoriseret Integra
- Ikke kategoriseret Rio
- Ikke kategoriseret Ipevo
- Ikke kategoriseret Princeton Tec
- Ikke kategoriseret Iget
- Ikke kategoriseret Revox
- Ikke kategoriseret Emtec
- Ikke kategoriseret Kioxia
- Ikke kategoriseret ISDT
- Ikke kategoriseret Abac
- Ikke kategoriseret Stannah
- Ikke kategoriseret Comelit
- Ikke kategoriseret Baja Mobility
- Ikke kategoriseret SecureSafe
- Ikke kategoriseret Xline
- Ikke kategoriseret Omnires
- Ikke kategoriseret Furman
- Ikke kategoriseret Unicol
- Ikke kategoriseret Aiphone
- Ikke kategoriseret Chrome-Q
- Ikke kategoriseret Lowell
- Ikke kategoriseret Libec
- Ikke kategoriseret Thermalright
- Ikke kategoriseret Celly
- Ikke kategoriseret Kindermann
- Ikke kategoriseret Comica
- Ikke kategoriseret Globo
- Ikke kategoriseret ZLine
- Ikke kategoriseret EverFocus
- Ikke kategoriseret Audient
- Ikke kategoriseret Adesso
- Ikke kategoriseret Hegel
- Ikke kategoriseret Infantino
- Ikke kategoriseret Natuzzi
- Ikke kategoriseret Grunkel
- Ikke kategoriseret Satel
- Ikke kategoriseret Bazooka
- Ikke kategoriseret PAX
- Ikke kategoriseret K&K Sound
- Ikke kategoriseret Dutchbone
- Ikke kategoriseret Fanvil
- Ikke kategoriseret PAC
- Ikke kategoriseret Wentronic
- Ikke kategoriseret Peerless
- Ikke kategoriseret Hooker
- Ikke kategoriseret Luxman
- Ikke kategoriseret Gitzo
- Ikke kategoriseret SeaLife
- Ikke kategoriseret Infinity
- Ikke kategoriseret Nesco
- Ikke kategoriseret Karlik
- Ikke kategoriseret Comark
- Ikke kategoriseret Coline
- Ikke kategoriseret Petri
- Ikke kategoriseret Masport
- Ikke kategoriseret Grizzly
- Ikke kategoriseret 4smarts
- Ikke kategoriseret Qute
- Ikke kategoriseret Syma
- Ikke kategoriseret Interstuhl
- Ikke kategoriseret Home Electric
- Ikke kategoriseret Bora
- Ikke kategoriseret Magic Care
- Ikke kategoriseret Raclet
- Ikke kategoriseret Glock
- Ikke kategoriseret Linn
- Ikke kategoriseret Swift
- Ikke kategoriseret Elta
- Ikke kategoriseret Iluv
- Ikke kategoriseret Monitor Audio
- Ikke kategoriseret Monoprice
- Ikke kategoriseret Aplic
- Ikke kategoriseret G-Technology
- Ikke kategoriseret Imarflex
- Ikke kategoriseret Wëasy
- Ikke kategoriseret Sauter
- Ikke kategoriseret Promethean
- Ikke kategoriseret HyperIce
- Ikke kategoriseret Home Easy
- Ikke kategoriseret Basil
- Ikke kategoriseret Nxg
- Ikke kategoriseret Autodesk
- Ikke kategoriseret Diana
- Ikke kategoriseret Viridian
- Ikke kategoriseret Areca
- Ikke kategoriseret SKROSS
- Ikke kategoriseret Sikkens
- Ikke kategoriseret DEXP
- Ikke kategoriseret GolfBuddy
- Ikke kategoriseret Proel
- Ikke kategoriseret Thermor
- Ikke kategoriseret Edge
- Ikke kategoriseret Deutz
- Ikke kategoriseret FIMI
- Ikke kategoriseret Flavel
- Ikke kategoriseret Bracketron
- Ikke kategoriseret Springlane
- Ikke kategoriseret DB Technologies
- Ikke kategoriseret IPGARD
- Ikke kategoriseret Pointer
- Ikke kategoriseret XYZprinting
- Ikke kategoriseret Computherm
- Ikke kategoriseret Metapace
- Ikke kategoriseret Neets
- Ikke kategoriseret Wooden Camera
- Ikke kategoriseret AdHoc
- Ikke kategoriseret SEH
- Ikke kategoriseret Hayter
- Ikke kategoriseret OSD Audio
- Ikke kategoriseret WMD
- Ikke kategoriseret Andover
- Ikke kategoriseret Simpark
- Ikke kategoriseret Beafon
- Ikke kategoriseret Maruyama
- Ikke kategoriseret Zepter
- Ikke kategoriseret Giordani
- Ikke kategoriseret Petmate
- Ikke kategoriseret Havis
- Ikke kategoriseret Nite Ize
- Ikke kategoriseret Cowon
- Ikke kategoriseret Soundstream
- Ikke kategoriseret Crayola
- Ikke kategoriseret Fischer
- Ikke kategoriseret Medel
- Ikke kategoriseret Livington
- Ikke kategoriseret Instant
- Ikke kategoriseret Gabor
- Ikke kategoriseret Meister Craft
- Ikke kategoriseret Meade
- Ikke kategoriseret Unify
- Ikke kategoriseret Sagemcom
- Ikke kategoriseret Laserworld
- Ikke kategoriseret Billow
- Ikke kategoriseret Chuango
- Ikke kategoriseret West Elm
- Ikke kategoriseret Block
- Ikke kategoriseret Lelit
- Ikke kategoriseret Hori
- Ikke kategoriseret Bikemate
- Ikke kategoriseret Garden Lights
- Ikke kategoriseret ETiger
- Ikke kategoriseret Bison
- Ikke kategoriseret Foxconn
- Ikke kategoriseret Icy Dock
- Ikke kategoriseret Make Noise
- Ikke kategoriseret Ronco
- Ikke kategoriseret Lumag
- Ikke kategoriseret Berker
- Ikke kategoriseret Premier
- Ikke kategoriseret Ibm
- Ikke kategoriseret META
- Ikke kategoriseret TEF
- Ikke kategoriseret Datacard
- Ikke kategoriseret ZYCOO
- Ikke kategoriseret Macrom
- Ikke kategoriseret Kontakt Chemie
- Ikke kategoriseret Purell
- Ikke kategoriseret Contax
- Ikke kategoriseret Batavia
- Ikke kategoriseret Klarfit
- Ikke kategoriseret Gutfels
- Ikke kategoriseret Mega Bloks
- Ikke kategoriseret Gardenline
- Ikke kategoriseret MSpa
- Ikke kategoriseret View Quest
- Ikke kategoriseret Drayton
- Ikke kategoriseret Crane
- Ikke kategoriseret Formuler
- Ikke kategoriseret Maximum
- Ikke kategoriseret Sonnet
- Ikke kategoriseret Oertli
- Ikke kategoriseret Nerf
- Ikke kategoriseret X4-LIFE
- Ikke kategoriseret Auray
- Ikke kategoriseret WilTec
- Ikke kategoriseret Girmi
- Ikke kategoriseret Welby
- Ikke kategoriseret Gamesir
- Ikke kategoriseret Geneinno
- Ikke kategoriseret Backyard Discovery
- Ikke kategoriseret Solid
- Ikke kategoriseret NUK
- Ikke kategoriseret Baby Annabell
- Ikke kategoriseret Axkid
- Ikke kategoriseret SVS
- Ikke kategoriseret Heatit
- Ikke kategoriseret ProForm
- Ikke kategoriseret Think Tank
- Ikke kategoriseret Lec
- Ikke kategoriseret LTC
- Ikke kategoriseret Drawmer
- Ikke kategoriseret Dunlop
- Ikke kategoriseret Valeo
- Ikke kategoriseret Noxon
- Ikke kategoriseret Velbus
- Ikke kategoriseret IQAir
- Ikke kategoriseret Sanus Systems
- Ikke kategoriseret Tormatic
- Ikke kategoriseret Berkel
- Ikke kategoriseret Idec
- Ikke kategoriseret Verbatim
- Ikke kategoriseret 2hp
- Ikke kategoriseret IXS
- Ikke kategoriseret Samlex
- Ikke kategoriseret AirTurn
- Ikke kategoriseret Turbo Air
- Ikke kategoriseret Zega
- Ikke kategoriseret CreativeWorKs
- Ikke kategoriseret Horizon
- Ikke kategoriseret Plugwise
- Ikke kategoriseret Tektronix
- Ikke kategoriseret Tempmate
- Ikke kategoriseret Suevia
- Ikke kategoriseret Ultimate Support
- Ikke kategoriseret Interphone
- Ikke kategoriseret Prince
- Ikke kategoriseret Inter-Tech
- Ikke kategoriseret James
- Ikke kategoriseret Bicker Elektronik
- Ikke kategoriseret Iadea
- Ikke kategoriseret Blizzard
- Ikke kategoriseret SIIG
- Ikke kategoriseret BIOS Medical
- Ikke kategoriseret Advantech
- Ikke kategoriseret PSSO
- Ikke kategoriseret Wise
- Ikke kategoriseret Stalco
- Ikke kategoriseret Merkel
- Ikke kategoriseret Biohort
- Ikke kategoriseret Globe
- Ikke kategoriseret Rossi
- Ikke kategoriseret Heckler Design
- Ikke kategoriseret Propellerhead
- Ikke kategoriseret Nanuk
- Ikke kategoriseret Digital Watchdog
- Ikke kategoriseret Riviera And Bar
- Ikke kategoriseret Apelson
- Ikke kategoriseret Kreiling
- Ikke kategoriseret Scanstrut
- Ikke kategoriseret Marker
- Ikke kategoriseret Safco
- Ikke kategoriseret Xunzel
- Ikke kategoriseret Oklahoma Sound
- Ikke kategoriseret Thames & Kosmos
- Ikke kategoriseret Kali Audio
- Ikke kategoriseret Betso
- Ikke kategoriseret Fortia
- Ikke kategoriseret Moen
- Ikke kategoriseret Babysense
- Ikke kategoriseret Namco Bandai Games
- Ikke kategoriseret Sealy
- Ikke kategoriseret Wet Sounds
- Ikke kategoriseret CRU
- Ikke kategoriseret MoFi
- Ikke kategoriseret Umarex
- Ikke kategoriseret Televés
- Ikke kategoriseret AbleNet
- Ikke kategoriseret Exalux
- Ikke kategoriseret Leap Frog
- Ikke kategoriseret Sightmark
- Ikke kategoriseret Eissound
- Ikke kategoriseret Ganz
- Ikke kategoriseret MTX Audio
- Ikke kategoriseret Astell&Kern
- Ikke kategoriseret SAVS
- Ikke kategoriseret Carlsbro
- Ikke kategoriseret Grundfos
- Ikke kategoriseret Sport-Tronic
- Ikke kategoriseret Xlyne
- Ikke kategoriseret Hughes & Kettner
- Ikke kategoriseret Manley
- Ikke kategoriseret Micro Matic
- Ikke kategoriseret MEE Audio
- Ikke kategoriseret Thermomate
- Ikke kategoriseret Steiner
- Ikke kategoriseret Acard
- Ikke kategoriseret NordicTrack
- Ikke kategoriseret Burigotto
- Ikke kategoriseret Itechworld
- Ikke kategoriseret Orbsmart
- Ikke kategoriseret Triton
- Ikke kategoriseret STANDIVARIUS
- Ikke kategoriseret Mobotix
- Ikke kategoriseret Extron
- Ikke kategoriseret Avocent
- Ikke kategoriseret Q Acoustics
- Ikke kategoriseret PureLink
- Ikke kategoriseret Ltech
- Ikke kategoriseret UNYKAch
- Ikke kategoriseret DCS
- Ikke kategoriseret Getac
- Ikke kategoriseret Franklin
- Ikke kategoriseret RTS
- Ikke kategoriseret Ontech
- Ikke kategoriseret Koss
- Ikke kategoriseret Swingline
- Ikke kategoriseret Kwikset
- Ikke kategoriseret Infomir
- Ikke kategoriseret RaySafe
- Ikke kategoriseret Di4
- Ikke kategoriseret Hohner
- Ikke kategoriseret Ashly
- Ikke kategoriseret Sanli
- Ikke kategoriseret HEOS
- Ikke kategoriseret Philos
- Ikke kategoriseret Legamaster
- Ikke kategoriseret SteelBody
- Ikke kategoriseret Siemon
- Ikke kategoriseret Block & Block
- Ikke kategoriseret Brondell
- Ikke kategoriseret Four Hands
- Ikke kategoriseret Oben
- Ikke kategoriseret Avteq
- Ikke kategoriseret Perlick
- Ikke kategoriseret DAB
- Ikke kategoriseret SLV
- Ikke kategoriseret Wasp
- Ikke kategoriseret Gamewright
- Ikke kategoriseret VAVA
- Ikke kategoriseret EarFun
- Ikke kategoriseret Premier Mounts
- Ikke kategoriseret Botex
- Ikke kategoriseret Moza
- Ikke kategoriseret Escort
- Ikke kategoriseret EK Water Blocks
- Ikke kategoriseret Claypaky
- Ikke kategoriseret Rothenberger
- Ikke kategoriseret Integral LED
- Ikke kategoriseret Leviton
- Ikke kategoriseret VAIS Technology
- Ikke kategoriseret Tru Components
- Ikke kategoriseret HomePilot
- Ikke kategoriseret Pelco
- Ikke kategoriseret Approx
- Ikke kategoriseret Mammut
- Ikke kategoriseret Lunt Solar Systems
- Ikke kategoriseret ChargeHub
- Ikke kategoriseret Gymform
- Ikke kategoriseret Modbap Modular
- Ikke kategoriseret Maxsa
- Ikke kategoriseret Tripp
- Ikke kategoriseret TRIUS
- Ikke kategoriseret Fine Dine
- Ikke kategoriseret ClearOne
- Ikke kategoriseret Source Audio
- Ikke kategoriseret Industrial Music Electronics
- Ikke kategoriseret Bluestork
- Ikke kategoriseret Caretero
- Ikke kategoriseret Digitech
- Ikke kategoriseret Everdure
- Ikke kategoriseret Heidemann
- Ikke kategoriseret Medeli
- Ikke kategoriseret Superrollo
- Ikke kategoriseret Goldtouch
- Ikke kategoriseret Braun Phototechnik
- Ikke kategoriseret Black Decker
- Ikke kategoriseret Muller
- Ikke kategoriseret SXT
- Ikke kategoriseret Essenza
- Ikke kategoriseret Seecode
- Ikke kategoriseret Rugged Geek
- Ikke kategoriseret Nubert
- Ikke kategoriseret Dave Smith
- Ikke kategoriseret Skymaster
- Ikke kategoriseret Palmer
- Ikke kategoriseret CGV
- Ikke kategoriseret Dorr
- Ikke kategoriseret Minn Kota
- Ikke kategoriseret Vocopro
- Ikke kategoriseret ICarsoft
- Ikke kategoriseret Helix
- Ikke kategoriseret TFA Dostmann
- Ikke kategoriseret Durable
- Ikke kategoriseret Zenza Bronica
- Ikke kategoriseret Greisinger
- Ikke kategoriseret Suprema
- Ikke kategoriseret Ziehl
- Ikke kategoriseret VAIS
- Ikke kategoriseret Perma
- Ikke kategoriseret Scandes
- Ikke kategoriseret Glorious
- Ikke kategoriseret Vicoustic
- Ikke kategoriseret Enovate
- Ikke kategoriseret Winegard
- Ikke kategoriseret Pigtronix
- Ikke kategoriseret Wagner SprayTech
- Ikke kategoriseret KWC
- Ikke kategoriseret Soul
- Ikke kategoriseret Laney
- Ikke kategoriseret Theragun
- Ikke kategoriseret Weil
- Ikke kategoriseret Plantiflor
- Ikke kategoriseret LAS
- Ikke kategoriseret Rosseto
- Ikke kategoriseret Redrock Micro
- Ikke kategoriseret Kata
- Ikke kategoriseret Minix
- Ikke kategoriseret The Grainfather
- Ikke kategoriseret Emga
- Ikke kategoriseret Devialet
- Ikke kategoriseret Briggs & Stratton
- Ikke kategoriseret USAopoly
- Ikke kategoriseret Gami
- Ikke kategoriseret Igloohome
- Ikke kategoriseret Doffler
- Ikke kategoriseret Kenko
- Ikke kategoriseret Zennio
- Ikke kategoriseret Vixen
- Ikke kategoriseret Sram
- Ikke kategoriseret Praktica
- Ikke kategoriseret Elinchrom
- Ikke kategoriseret Boori
- Ikke kategoriseret CamRanger
- Ikke kategoriseret Hasselblad
- Ikke kategoriseret Madrix
- Ikke kategoriseret Spacedec
- Ikke kategoriseret Bontempi
- Ikke kategoriseret Summer Infant
- Ikke kategoriseret Cooper & Quint
- Ikke kategoriseret Deltex
- Ikke kategoriseret Adax
- Ikke kategoriseret Adam
- Ikke kategoriseret Eonon
- Ikke kategoriseret SMC
- Ikke kategoriseret INOGENI
- Ikke kategoriseret GMB Audio
- Ikke kategoriseret Middle Atlantic
- Ikke kategoriseret OBSBOT
- Ikke kategoriseret Ibico
- Ikke kategoriseret OXO Good Grips
- Ikke kategoriseret Exit Toys
- Ikke kategoriseret Profizelt24
- Ikke kategoriseret Helios Preisser
- Ikke kategoriseret YSI
- Ikke kategoriseret Yeyian
- Ikke kategoriseret Paulmann
- Ikke kategoriseret Nitek
- Ikke kategoriseret Snoes
- Ikke kategoriseret Alpatronix
- Ikke kategoriseret TK Audio
- Ikke kategoriseret Nearity
- Ikke kategoriseret GVision
- Ikke kategoriseret Carry-on
- Ikke kategoriseret Best
- Ikke kategoriseret Labelmate
- Ikke kategoriseret Playtive
- Ikke kategoriseret Martin Audio
- Ikke kategoriseret Schertler
- Ikke kategoriseret Teradek
- Ikke kategoriseret Sissel
- Ikke kategoriseret SolarEdge
- Ikke kategoriseret GOgroove
- Ikke kategoriseret ViewCast
- Ikke kategoriseret Tennsco
- Ikke kategoriseret FireKing
- Ikke kategoriseret RAM Mounts
- Ikke kategoriseret Novus
- Ikke kategoriseret Dedra
- Ikke kategoriseret Arebos
- Ikke kategoriseret Kreg
- Ikke kategoriseret Morningstar
- Ikke kategoriseret DMax
- Ikke kategoriseret Cambium Networks
- Ikke kategoriseret POGS
- Ikke kategoriseret Minuteman
- Ikke kategoriseret Brady
- Ikke kategoriseret RéVive
- Ikke kategoriseret Mega
- Ikke kategoriseret Woodland Scenics
- Ikke kategoriseret Chapin
- Ikke kategoriseret J. Rockett Audio Designs
- Ikke kategoriseret Pancontrol
- Ikke kategoriseret Satisfyer
- Ikke kategoriseret Hämmerli
- Ikke kategoriseret Verto
- Ikke kategoriseret Soma
- Ikke kategoriseret Posiflex
- Ikke kategoriseret Point 65
- Ikke kategoriseret ReTrak
- Ikke kategoriseret Avantree
- Ikke kategoriseret LYYT
- Ikke kategoriseret Jay-tech
- Ikke kategoriseret Old Blood Noise
- Ikke kategoriseret Vulcan
- Ikke kategoriseret CradlePoint
- Ikke kategoriseret Rovo Kids
- Ikke kategoriseret Catalyst
- Ikke kategoriseret Antelope Audio
- Ikke kategoriseret Brinno
- Ikke kategoriseret Venom
- Ikke kategoriseret CE Labs
- Ikke kategoriseret Z CAM
- Ikke kategoriseret Digium
- Ikke kategoriseret Giardino
- Ikke kategoriseret Mulex
- Ikke kategoriseret Novation
- Ikke kategoriseret Socomec
- Ikke kategoriseret System Sensor
- Ikke kategoriseret San Jamar
- Ikke kategoriseret IPort
- Ikke kategoriseret X-Rite
- Ikke kategoriseret Wetelux
- Ikke kategoriseret Talkaphone
- Ikke kategoriseret Merax
- Ikke kategoriseret GermGuardian
- Ikke kategoriseret R-Go Tools
- Ikke kategoriseret Urbanista
- Ikke kategoriseret Sagitter
- Ikke kategoriseret Rainbow
- Ikke kategoriseret Riello
- Ikke kategoriseret Gagato
- Ikke kategoriseret General
- Ikke kategoriseret Ooni
- Ikke kategoriseret ECTIVE
- Ikke kategoriseret Ebro
- Ikke kategoriseret Tzumi
- Ikke kategoriseret BERTSCHAT
- Ikke kategoriseret Schumacher
- Ikke kategoriseret Michael Todd Beauty
- Ikke kategoriseret Cygnett
- Ikke kategoriseret Germania
- Ikke kategoriseret Victorio
- Ikke kategoriseret Platinum
- Ikke kategoriseret Foreo
- Ikke kategoriseret Intertechno
- Ikke kategoriseret Parklands
- Ikke kategoriseret Avid
- Ikke kategoriseret ModeCom
- Ikke kategoriseret ENTES
- Ikke kategoriseret Anova
- Ikke kategoriseret ZILR
- Ikke kategoriseret Koolatron
- Ikke kategoriseret Black Hydra
- Ikke kategoriseret D-Jix
- Ikke kategoriseret Coca-Cola
- Ikke kategoriseret X Rocker
- Ikke kategoriseret RetroSound
- Ikke kategoriseret GoldenEar
- Ikke kategoriseret Prompter People
- Ikke kategoriseret APsystems
- Ikke kategoriseret Helios
- Ikke kategoriseret EKO
- Ikke kategoriseret BIG
- Ikke kategoriseret SureFire
- Ikke kategoriseret Graflex
- Ikke kategoriseret Coolaroo
- Ikke kategoriseret Insta360
- Ikke kategoriseret Gioteck
- Ikke kategoriseret Kenton
- Ikke kategoriseret Cypress
- Ikke kategoriseret Foliatec
- Ikke kategoriseret Mauser
- Ikke kategoriseret Silhouette
- Ikke kategoriseret South Shore
- Ikke kategoriseret Discovery
- Ikke kategoriseret T4E
- Ikke kategoriseret Speck
- Ikke kategoriseret Roku
- Ikke kategoriseret Generation
- Ikke kategoriseret Ecler
- Ikke kategoriseret Phase One
- Ikke kategoriseret Little Giant
- Ikke kategoriseret Röhm
- Ikke kategoriseret Ulanzi
- Ikke kategoriseret Accsoon
- Ikke kategoriseret Viscount
- Ikke kategoriseret Anex
- Ikke kategoriseret Majella
- Ikke kategoriseret Ashdown Engineering
- Ikke kategoriseret Century
- Ikke kategoriseret Unger
- Ikke kategoriseret Inverto
- Ikke kategoriseret Special-T
- Ikke kategoriseret Ygnis
- Ikke kategoriseret Esotec
- Ikke kategoriseret True & Tidy
- Ikke kategoriseret NovaStar
- Ikke kategoriseret Petkit
- Ikke kategoriseret Icon
- Ikke kategoriseret Fuzzix
- Ikke kategoriseret Kitchen Brains
- Ikke kategoriseret Schellenberg
- Ikke kategoriseret Challenge Xtreme
- Ikke kategoriseret Flycam
- Ikke kategoriseret NetAlly
- Ikke kategoriseret Peltor
- Ikke kategoriseret JAR Systems
- Ikke kategoriseret Global
- Ikke kategoriseret Moleskine
- Ikke kategoriseret Beghelli
- Ikke kategoriseret Nanoleaf
- Ikke kategoriseret Bytecc
- Ikke kategoriseret Strex
- Ikke kategoriseret One Stop Systems
- Ikke kategoriseret Cool Maker
- Ikke kategoriseret Neo
- Ikke kategoriseret DoughXpress
- Ikke kategoriseret Parasound
- Ikke kategoriseret SPT
- Ikke kategoriseret Promate
- Ikke kategoriseret Berger & Schröter
- Ikke kategoriseret Step2
- Ikke kategoriseret Dension
- Ikke kategoriseret Crystal Quest
- Ikke kategoriseret Pit Boss
- Ikke kategoriseret MiPow
- Ikke kategoriseret GoldenEar Technology
- Ikke kategoriseret Colt
- Ikke kategoriseret Elite Screens
- Ikke kategoriseret Ultron
- Ikke kategoriseret Choice
- Ikke kategoriseret Roswell
- Ikke kategoriseret King Craft
- Ikke kategoriseret FOX ESS
- Ikke kategoriseret Airman
- Ikke kategoriseret Cascade Audio Engineering
- Ikke kategoriseret B-Speech
- Ikke kategoriseret Nimbus
- Ikke kategoriseret Vanish
- Ikke kategoriseret Grosfillex
- Ikke kategoriseret Beemoo
- Ikke kategoriseret Hollyland
- Ikke kategoriseret Platinet
- Ikke kategoriseret Santos
- Ikke kategoriseret Evoc
- Ikke kategoriseret Versare
- Ikke kategoriseret Tractive
- Ikke kategoriseret SpeakerCraft
- Ikke kategoriseret Celexon
- Ikke kategoriseret Epcom
- Ikke kategoriseret ZeeVee
- Ikke kategoriseret Viatek
- Ikke kategoriseret Simplicity
- Ikke kategoriseret Doomoo
- Ikke kategoriseret MBZ
- Ikke kategoriseret Davey
- Ikke kategoriseret Mettler
- Ikke kategoriseret Metalux
- Ikke kategoriseret Heitech
- Ikke kategoriseret Potenza
- Ikke kategoriseret LOQED
- Ikke kategoriseret Hatco
- Ikke kategoriseret KONFTEL
- Ikke kategoriseret Canicom
- Ikke kategoriseret Mitsai
- Ikke kategoriseret Selfsat
- Ikke kategoriseret Leef
- Ikke kategoriseret Tusa
- Ikke kategoriseret Hovicon
- Ikke kategoriseret Starlyf
- Ikke kategoriseret American BioTech Supply
- Ikke kategoriseret Lagrange
- Ikke kategoriseret Noris
- Ikke kategoriseret KS Tools
- Ikke kategoriseret Koliber
- Ikke kategoriseret Schmidt & Bender
- Ikke kategoriseret Mesa Boogie
- Ikke kategoriseret Improv
- Ikke kategoriseret LandRoller
- Ikke kategoriseret Wegman
- Ikke kategoriseret Lockncharge
- Ikke kategoriseret Merlin
- Ikke kategoriseret Standard Horizon
- Ikke kategoriseret Goal Zero
- Ikke kategoriseret HealthPostures
- Ikke kategoriseret Heaven Fresh
- Ikke kategoriseret Lutec
- Ikke kategoriseret Champion Sports
- Ikke kategoriseret Molotow
- Ikke kategoriseret Herlag
- Ikke kategoriseret Dux
- Ikke kategoriseret FALLER
- Ikke kategoriseret Miditech
- Ikke kategoriseret SE Electronics
- Ikke kategoriseret TTM
- Ikke kategoriseret Paw Patrol
- Ikke kategoriseret ISi
- Ikke kategoriseret LELO
- Ikke kategoriseret Apricorn
- Ikke kategoriseret Mermade
- Ikke kategoriseret MXR
- Ikke kategoriseret SKLZ
- Ikke kategoriseret Herma
- Ikke kategoriseret Syrp
- Ikke kategoriseret Ugolini
- Ikke kategoriseret Cosina
- Ikke kategoriseret Heckler & Koch
- Ikke kategoriseret Whistler
- Ikke kategoriseret Twisper
- Ikke kategoriseret ESX
- Ikke kategoriseret J5create
- Ikke kategoriseret Hushmat
- Ikke kategoriseret Xigmatek
- Ikke kategoriseret Tema
- Ikke kategoriseret ALM
- Ikke kategoriseret Topaz
- Ikke kategoriseret Toddy
- Ikke kategoriseret Aicon
- Ikke kategoriseret Doepfer
- Ikke kategoriseret Fun Generation
- Ikke kategoriseret Karma
- Ikke kategoriseret Hugo Muller
- Ikke kategoriseret Vinci
- Ikke kategoriseret Jordan
- Ikke kategoriseret Duromax
- Ikke kategoriseret DataComm
- Ikke kategoriseret Powercube
- Ikke kategoriseret Kasp
- Ikke kategoriseret Dimavery
- Ikke kategoriseret WestBend
- Ikke kategoriseret Mr Coffee
- Ikke kategoriseret Sherlock
- Ikke kategoriseret SEA-PRO
- Ikke kategoriseret Cavius
- Ikke kategoriseret Omiindustriies
- Ikke kategoriseret Weltevree
- Ikke kategoriseret Phoenix Contact
- Ikke kategoriseret AMS Neve
- Ikke kategoriseret LVSUN
- Ikke kategoriseret Aston Microphones
- Ikke kategoriseret Netsys
- Ikke kategoriseret Polarlite
- Ikke kategoriseret Companion
- Ikke kategoriseret Mr. Beams
- Ikke kategoriseret Morphor
- Ikke kategoriseret Lapp
- Ikke kategoriseret XO
- Ikke kategoriseret PcDuino
- Ikke kategoriseret LECO
- Ikke kategoriseret Maretron
- Ikke kategoriseret Hortus
- Ikke kategoriseret Razorri
- Ikke kategoriseret Fetch
- Ikke kategoriseret Zoetis
- Ikke kategoriseret Prem-i-air
- Ikke kategoriseret NWS
- Ikke kategoriseret Scale Computing
- Ikke kategoriseret Naturn Living
- Ikke kategoriseret Aeotec
- Ikke kategoriseret Catlink
- Ikke kategoriseret FitterFirst
- Ikke kategoriseret Raveland
- Ikke kategoriseret Mr. Heater
- Ikke kategoriseret Welltech
- Ikke kategoriseret Trumeter
- Ikke kategoriseret Seidio
- Ikke kategoriseret Sincreative
- Ikke kategoriseret JDC
- Ikke kategoriseret HammerSmith
- Ikke kategoriseret Yeaz
- Ikke kategoriseret Hidrate
- Ikke kategoriseret Sonicware
- Ikke kategoriseret Nexibo
- Ikke kategoriseret Jolin
- Ikke kategoriseret MoTip
- Ikke kategoriseret Stenda
- Ikke kategoriseret Pro-Lift
- Ikke kategoriseret HIOAZO
- Ikke kategoriseret Malstrom
- Ikke kategoriseret Laserluchs
- Ikke kategoriseret Powersoft
- Ikke kategoriseret Casetastic
- Ikke kategoriseret UClear
- Ikke kategoriseret BikeLogger
- Ikke kategoriseret Tor Rey
- Ikke kategoriseret Momo Design
- Ikke kategoriseret Esdec
- Ikke kategoriseret AJH Synth
- Ikke kategoriseret LifeStraw
- Ikke kategoriseret Magnavox
- Ikke kategoriseret Toolit
- Ikke kategoriseret Egnater
- Ikke kategoriseret DutchOne
- Ikke kategoriseret Feitian
- Ikke kategoriseret Ergie
- Ikke kategoriseret Reltech
- Ikke kategoriseret Armcross
- Ikke kategoriseret Huntleigh
- Ikke kategoriseret Beeletix
- Ikke kategoriseret Gehmann
- Ikke kategoriseret Batronix
- Ikke kategoriseret Franzis
- Ikke kategoriseret Gridbyt
- Ikke kategoriseret LONQ
- Ikke kategoriseret Em-Trak
- Ikke kategoriseret Wonky Monkey
- Ikke kategoriseret Dresden Elektronik
- Ikke kategoriseret Atmel
- Ikke kategoriseret Flavour Blaster
- Ikke kategoriseret Esoteric
- Ikke kategoriseret SmartAVI
- Ikke kategoriseret EPH Elektronik
- Ikke kategoriseret InfiRay
- Ikke kategoriseret Markbass
- Ikke kategoriseret IMG Stage Line
- Ikke kategoriseret IMAC
- Ikke kategoriseret Metz Connect
- Ikke kategoriseret MGL Avionics
- Ikke kategoriseret Eikon
- Ikke kategoriseret Casablanca
- Ikke kategoriseret Nemco
- Ikke kategoriseret Wireless Solution
- Ikke kategoriseret Sparco
- Ikke kategoriseret Barber Tech
- Ikke kategoriseret Estella
- Ikke kategoriseret Oehlbach
- Ikke kategoriseret Minkels
- Ikke kategoriseret Lenmar
- Ikke kategoriseret Arduino
- Ikke kategoriseret Ave Six
- Ikke kategoriseret Bestar
- Ikke kategoriseret Gardigo
- Ikke kategoriseret Nothing
- Ikke kategoriseret Highpoint
- Ikke kategoriseret Puls Dimension
- Ikke kategoriseret Fischer Amps
- Ikke kategoriseret CHINT
- Ikke kategoriseret Sirus
- Ikke kategoriseret Gretsch
- Ikke kategoriseret Pentacon
- Ikke kategoriseret Winia
- Ikke kategoriseret Bolsey
- Ikke kategoriseret Louis Tellier
- Ikke kategoriseret Simeo
- Ikke kategoriseret Baracuda
- Ikke kategoriseret Kstar
- Ikke kategoriseret Air Guard
- Ikke kategoriseret MediaMatrix
- Ikke kategoriseret Tuur
- Ikke kategoriseret ONE Smart Control
- Ikke kategoriseret Edelkrone
- Ikke kategoriseret InSinkErator
- Ikke kategoriseret AREXX
- Ikke kategoriseret IVT
- Ikke kategoriseret Elite Force
- Ikke kategoriseret JK Audio
- Ikke kategoriseret DEHN
- Ikke kategoriseret Piko
- Ikke kategoriseret Lifan
- Ikke kategoriseret Jomox
- Ikke kategoriseret Burley
- Ikke kategoriseret Lexicon
- Ikke kategoriseret Icarus Blue
- Ikke kategoriseret Command
- Ikke kategoriseret IRIS
- Ikke kategoriseret Neno
- Ikke kategoriseret Starburst
- Ikke kategoriseret Futurelight
- Ikke kategoriseret AVPro Edge
- Ikke kategoriseret Cactus
- Ikke kategoriseret Dragonshock
- Ikke kategoriseret Fluance
- Ikke kategoriseret PCE Instruments
- Ikke kategoriseret Garden Place
- Ikke kategoriseret Moldex
- Ikke kategoriseret Cudy
- Ikke kategoriseret MaximaVida
- Ikke kategoriseret Firefriend
- Ikke kategoriseret DOD
- Ikke kategoriseret LightZone
- Ikke kategoriseret Robinhood
- Ikke kategoriseret Bliss Outdoors
- Ikke kategoriseret Fontiso
- Ikke kategoriseret Varytec
- Ikke kategoriseret Altra
- Ikke kategoriseret Omnilux
- Ikke kategoriseret Socket Mobile
- Ikke kategoriseret Quartet
- Ikke kategoriseret Shadow
- Ikke kategoriseret IP-COM
- Ikke kategoriseret Comtek
- Ikke kategoriseret Fishman
- Ikke kategoriseret Tams Elektronik
- Ikke kategoriseret Digital Juice
- Ikke kategoriseret Eschenbach
- Ikke kategoriseret ASM
- Ikke kategoriseret Elektron
- Ikke kategoriseret Kiev
- Ikke kategoriseret Caroline
- Ikke kategoriseret Zomo
- Ikke kategoriseret Synco
- Ikke kategoriseret Buchla & TipTop Audio
- Ikke kategoriseret Tiny Audio
- Ikke kategoriseret Kiloview
- Ikke kategoriseret Pyramid
- Ikke kategoriseret Maico
- Ikke kategoriseret SHX
- Ikke kategoriseret LEA
- Ikke kategoriseret On-Q
- Ikke kategoriseret SetonixSynth
- Ikke kategoriseret Horex
- Ikke kategoriseret Inno-Hit
- Ikke kategoriseret AvaValley
- Ikke kategoriseret INTIMINA
- Ikke kategoriseret Monzana
- Ikke kategoriseret FCC BBQ
- Ikke kategoriseret Auto XS
- Ikke kategoriseret Toomax
- Ikke kategoriseret Aqua Marina
- Ikke kategoriseret Hameg
- Ikke kategoriseret Greemotion
- Ikke kategoriseret Winter Modular
- Ikke kategoriseret FED
- Ikke kategoriseret Synamodec
- Ikke kategoriseret Grotime
- Ikke kategoriseret Pico Macom
- Ikke kategoriseret RadonTec
- Ikke kategoriseret Katrin
- Ikke kategoriseret Kendau
- Ikke kategoriseret Kisag
- Ikke kategoriseret NUX
- Ikke kategoriseret Coxreels
- Ikke kategoriseret Nous
- Ikke kategoriseret Overade
- Ikke kategoriseret Liemke
- Ikke kategoriseret Copco
- Ikke kategoriseret Reber
- Ikke kategoriseret Acros
- Ikke kategoriseret Mach Power
- Ikke kategoriseret Vent-A-Hood
- Ikke kategoriseret Adventure Kings
- Ikke kategoriseret Testec
- Ikke kategoriseret Vanson
- Ikke kategoriseret Canyon
- Ikke kategoriseret Carcomm
- Ikke kategoriseret Style Me Up
- Ikke kategoriseret Swedish Posture
- Ikke kategoriseret Melnor
- Ikke kategoriseret CDVI
- Ikke kategoriseret Excalibur
- Ikke kategoriseret Holman
- Ikke kategoriseret Leaptel
- Ikke kategoriseret Lifenaxx
- Ikke kategoriseret Powertec
- Ikke kategoriseret Waterbird
- Ikke kategoriseret Dreambaby
- Ikke kategoriseret AOpen
- Ikke kategoriseret Angler
- Ikke kategoriseret Casaria
- Ikke kategoriseret Selleys
- Ikke kategoriseret WindFall
- Ikke kategoriseret Ameristep
- Ikke kategoriseret KM-fit
- Ikke kategoriseret Mircom
- Ikke kategoriseret ESUN
- Ikke kategoriseret TSC
- Ikke kategoriseret Durex
- Ikke kategoriseret Wachendorff
- Ikke kategoriseret AeroCool
- Ikke kategoriseret Vantage Point
- Ikke kategoriseret Jokari
- Ikke kategoriseret BeeSecure
- Ikke kategoriseret MantelMount
- Ikke kategoriseret Fisher Paykel
- Ikke kategoriseret Lasita Maja
- Ikke kategoriseret Meccano
- Ikke kategoriseret Parallels
- Ikke kategoriseret Oatey
- Ikke kategoriseret QUIO
- Ikke kategoriseret Fisher
- Ikke kategoriseret Gretsch Guitars
- Ikke kategoriseret Banoch
- Ikke kategoriseret Atmotube
- Ikke kategoriseret Sun Pumps
- Ikke kategoriseret Electrify
- Ikke kategoriseret Leatt
- Ikke kategoriseret Bleep Labs
- Ikke kategoriseret FontaFit
- Ikke kategoriseret Gossmann
- Ikke kategoriseret Comatec
- Ikke kategoriseret Jonard Tools
- Ikke kategoriseret HMD
- Ikke kategoriseret WEG
- Ikke kategoriseret Atech Flash Technology
- Ikke kategoriseret AutoParkTime
- Ikke kategoriseret Hudora
- Ikke kategoriseret Facal
- Ikke kategoriseret Planet Audio
- Ikke kategoriseret Datacolor
- Ikke kategoriseret Silicon Power
- Ikke kategoriseret Sabrent
- Ikke kategoriseret JAXY
- Ikke kategoriseret WARN
- Ikke kategoriseret TikkTokk
- Ikke kategoriseret Roco
- Ikke kategoriseret Flexson
- Ikke kategoriseret Camec
- Ikke kategoriseret Wibrain
- Ikke kategoriseret Rolly Toys
- Ikke kategoriseret Deditec
- Ikke kategoriseret Level Mount
- Ikke kategoriseret Teenage Engineering
- Ikke kategoriseret Elipson
- Ikke kategoriseret CommScope
- Ikke kategoriseret Videotec
- Ikke kategoriseret Orange
- Ikke kategoriseret Extralife Instruments
- Ikke kategoriseret GoXtreme
- Ikke kategoriseret Huslog
- Ikke kategoriseret Genki Instruments
- Ikke kategoriseret Mauser Sitzkultur
- Ikke kategoriseret Accezz
- Ikke kategoriseret A4 Tech
- Ikke kategoriseret Full Boar
- Ikke kategoriseret Zedar
- Ikke kategoriseret Yli Electronic
- Ikke kategoriseret Dals
- Ikke kategoriseret Bulman
- Ikke kategoriseret TOOLMATE
- Ikke kategoriseret SleepPro
- Ikke kategoriseret Muama
- Ikke kategoriseret Lepu Medical
- Ikke kategoriseret Beringer
- Ikke kategoriseret Revamp
- Ikke kategoriseret Phonic
- Ikke kategoriseret ZCover
- Ikke kategoriseret Vasagle
- Ikke kategoriseret Aquatica
- Ikke kategoriseret Goaliath
- Ikke kategoriseret 909 Outdoor
- Ikke kategoriseret Viomi
- Ikke kategoriseret Empirical Labs
- Ikke kategoriseret Grimm Audio
- Ikke kategoriseret Ciarra
- Ikke kategoriseret Global Water
- Ikke kategoriseret Deye
- Ikke kategoriseret IOptron
- Ikke kategoriseret Götze & Jensen
- Ikke kategoriseret Weston
- Ikke kategoriseret STI
- Ikke kategoriseret Better Life
- Ikke kategoriseret Dayclocks
- Ikke kategoriseret Phidgets
- Ikke kategoriseret Hawk-Woods
- Ikke kategoriseret Novo
- Ikke kategoriseret Novis
- Ikke kategoriseret Dexibell
- Ikke kategoriseret IsoAcoustics
- Ikke kategoriseret Memphis
- Ikke kategoriseret Engel
- Ikke kategoriseret Clifford
- Ikke kategoriseret Atlona
- Ikke kategoriseret Cambo
- Ikke kategoriseret Hedbox
- Ikke kategoriseret Adviti
- Ikke kategoriseret Maclean
- Ikke kategoriseret 9.solutions
- Ikke kategoriseret Hotone
- Ikke kategoriseret WEN
- Ikke kategoriseret Trace Elliot
- Ikke kategoriseret Lockwood
- Ikke kategoriseret Nexera
- Ikke kategoriseret Goodway
- Ikke kategoriseret BlueDri
- Ikke kategoriseret Seenergy
- Ikke kategoriseret Meinl
- Ikke kategoriseret Analogis
- Ikke kategoriseret BBQ Premium
- Ikke kategoriseret Stäubli
- Ikke kategoriseret RAB
- Ikke kategoriseret Schabus
- Ikke kategoriseret Eoslift
- Ikke kategoriseret Bron-Coucke
- Ikke kategoriseret Steelton
- Ikke kategoriseret FeinTech
- Ikke kategoriseret BioChef
- Ikke kategoriseret Masterbuilt
- Ikke kategoriseret T-Rex
- Ikke kategoriseret Euro Cuisine
- Ikke kategoriseret GFM
- Ikke kategoriseret Tot Tutors
- Ikke kategoriseret Tonar
- Ikke kategoriseret Peterson
- Ikke kategoriseret CFH
- Ikke kategoriseret Emeril Everyday
- Ikke kategoriseret Kostal
- Ikke kategoriseret Waterstone
- Ikke kategoriseret Best Fitness
- Ikke kategoriseret WarmlyYours
- Ikke kategoriseret Könner & Söhnen
- Ikke kategoriseret Rockboard
- Ikke kategoriseret Nivian
- Ikke kategoriseret L.R.Baggs
- Ikke kategoriseret Millennia
- Ikke kategoriseret Vermona Modular
- Ikke kategoriseret Drive Medical
- Ikke kategoriseret Hitron
- Ikke kategoriseret Bliss Hammocks
- Ikke kategoriseret Fortis
- Ikke kategoriseret Singular Sound
- Ikke kategoriseret Maneco Labs
- Ikke kategoriseret BISWIND
- Ikke kategoriseret ABE Arnhold
- Ikke kategoriseret Mermade Hair
- Ikke kategoriseret Hover-1
- Ikke kategoriseret VCM
- Ikke kategoriseret Auer Signal
- Ikke kategoriseret HELGI
- Ikke kategoriseret Forge Adour
- Ikke kategoriseret Eliminator Lighting
- Ikke kategoriseret Darkglass
- Ikke kategoriseret Blow
- Ikke kategoriseret Paasche
- Ikke kategoriseret Vistus
- Ikke kategoriseret GMW
- Ikke kategoriseret AER
- Ikke kategoriseret Dynavox
- Ikke kategoriseret Columbus
- Ikke kategoriseret IWH
- Ikke kategoriseret UGo
- Ikke kategoriseret Code Mercenaries
- Ikke kategoriseret Diamex
- Ikke kategoriseret Sunset
- Ikke kategoriseret Avital
- Ikke kategoriseret Ondis24
- Ikke kategoriseret D'Addario
- Ikke kategoriseret BBE
- Ikke kategoriseret Warwick
- Ikke kategoriseret MyAVR
- Ikke kategoriseret EBS
- Ikke kategoriseret WEICON
- Ikke kategoriseret Rotronic
- Ikke kategoriseret Edsyn
- Ikke kategoriseret Urban Glide
- Ikke kategoriseret EISL
- Ikke kategoriseret RCS
- Ikke kategoriseret Nicai Systems
- Ikke kategoriseret IDENTsmart
- Ikke kategoriseret Sharper Image
- Ikke kategoriseret Altrad
- Ikke kategoriseret Revier Manager
- Ikke kategoriseret Homak
- Ikke kategoriseret Statron
- Ikke kategoriseret Tycon Systems
- Ikke kategoriseret Selve
- Ikke kategoriseret Lumel
- Ikke kategoriseret Paingone
- Ikke kategoriseret Howard Leight
- Ikke kategoriseret Martens
- Ikke kategoriseret Palmako
- Ikke kategoriseret Desview
- Ikke kategoriseret ActiveJet
- Ikke kategoriseret Allsee
- Ikke kategoriseret Softing
- Ikke kategoriseret Pulse ShowerSpas
- Ikke kategoriseret Alogic
- Ikke kategoriseret GFB
- Ikke kategoriseret Sonicsmith
- Ikke kategoriseret Toraiz
- Ikke kategoriseret Ergodyne
- Ikke kategoriseret Maturmeat
- Ikke kategoriseret Eowave
- Ikke kategoriseret Imperia
- Ikke kategoriseret Autocue
- Ikke kategoriseret Nature2
- Ikke kategoriseret Baby Trend
- Ikke kategoriseret AMERRY
- Ikke kategoriseret Walther
- Ikke kategoriseret ShelterLogic
- Ikke kategoriseret Varad
- Ikke kategoriseret UDG Gear
- Ikke kategoriseret KMA Machines
- Ikke kategoriseret Motus
- Ikke kategoriseret Elcom
- Ikke kategoriseret AtomoSynth
- Ikke kategoriseret Innr
- Ikke kategoriseret Benidub
- Ikke kategoriseret Protector
- Ikke kategoriseret Winston
- Ikke kategoriseret Solidsteel
- Ikke kategoriseret Dracast
- Ikke kategoriseret Dream
- Ikke kategoriseret Malouf
- Ikke kategoriseret PureTools
- Ikke kategoriseret SiriusXM
- Ikke kategoriseret Earthwise
- Ikke kategoriseret DoubleSight
- Ikke kategoriseret Raya
- Ikke kategoriseret NANO Modules
- Ikke kategoriseret Artex
- Ikke kategoriseret Bobrick
- Ikke kategoriseret Verbos Electronics
- Ikke kategoriseret Ark
- Ikke kategoriseret DLO
- Ikke kategoriseret ENS
- Ikke kategoriseret Listen
- Ikke kategoriseret Pentair
- Ikke kategoriseret Oscium
- Ikke kategoriseret Benchmark USA
- Ikke kategoriseret Python
- Ikke kategoriseret Littelfuse
- Ikke kategoriseret Game Factor
- Ikke kategoriseret NComputing
- Ikke kategoriseret Brändi
- Ikke kategoriseret Mode Machines
- Ikke kategoriseret Legends
- Ikke kategoriseret AS Synthesizers
- Ikke kategoriseret Nexcom
- Ikke kategoriseret Janitza
- Ikke kategoriseret SatKing
- Ikke kategoriseret Fulltone
- Ikke kategoriseret Advantix
- Ikke kategoriseret Wampler
- Ikke kategoriseret VAEMI
- Ikke kategoriseret Aguilar
- Ikke kategoriseret Narva
- Ikke kategoriseret DOK
- Ikke kategoriseret OzCharge
- Ikke kategoriseret MIYO
- Ikke kategoriseret Cioks
- Ikke kategoriseret Neopower
- Ikke kategoriseret AvMap
- Ikke kategoriseret Arlec
- Ikke kategoriseret Sanwa
- Ikke kategoriseret REDARC
- Ikke kategoriseret Guardian
- Ikke kategoriseret Radio Flyer
- Ikke kategoriseret Gaslock
- Ikke kategoriseret Gaffgun
- Ikke kategoriseret Mazzer
- Ikke kategoriseret AquaMAX
- Ikke kategoriseret DigitSole
- Ikke kategoriseret Portsmith
- Ikke kategoriseret Flame
- Ikke kategoriseret Rome
- Ikke kategoriseret DW
- Ikke kategoriseret BEA
- Ikke kategoriseret Disty
- Ikke kategoriseret OXI Instruments
- Ikke kategoriseret AvaTime
- Ikke kategoriseret Xhose
- Ikke kategoriseret MYVU
- Ikke kategoriseret Kopykake
- Ikke kategoriseret Konstant Lab
- Ikke kategoriseret Turbo Scrub
- Ikke kategoriseret Tenderfoot Electronics
- Ikke kategoriseret Kask
- Ikke kategoriseret Callpod
- Ikke kategoriseret Dorman
- Ikke kategoriseret 2box
- Ikke kategoriseret Enlight
- Ikke kategoriseret Franken
- Ikke kategoriseret RUBI
- Ikke kategoriseret Europa Leisure
- Ikke kategoriseret GAMO
- Ikke kategoriseret Musser
- Ikke kategoriseret Edge Products
- Ikke kategoriseret IClever
- Ikke kategoriseret HN-Power
- Ikke kategoriseret BIONIK
- Ikke kategoriseret King Canopy
- Ikke kategoriseret HeadRush
- Ikke kategoriseret Flover
- Ikke kategoriseret Milestone Systems
- Ikke kategoriseret Micsig
- Ikke kategoriseret Dodow
- Ikke kategoriseret Spring
- Ikke kategoriseret Red Panda
- Ikke kategoriseret OJ ELECTRONICS
- Ikke kategoriseret Aquasure
- Ikke kategoriseret Banana Pi
- Ikke kategoriseret Ilford
- Ikke kategoriseret Crazy Tube Circuits
- Ikke kategoriseret J.P. Instruments
- Ikke kategoriseret Proclip
- Ikke kategoriseret SainSmart
- Ikke kategoriseret Kaona
- Ikke kategoriseret DPW Design
- Ikke kategoriseret SinuPulse
- Ikke kategoriseret The T.bone
- Ikke kategoriseret DIEZEL
- Ikke kategoriseret VMB
- Ikke kategoriseret Z.Vex
- Ikke kategoriseret Seymour Duncan
- Ikke kategoriseret BluGuitar
- Ikke kategoriseret Lehle
- Ikke kategoriseret Bricasti Design
- Ikke kategoriseret T.akustik
- Ikke kategoriseret Dwarf Connection
- Ikke kategoriseret JL Cooper
- Ikke kategoriseret StrikeMaster
- Ikke kategoriseret ProUser
- Ikke kategoriseret Bēm Wireless
- Ikke kategoriseret Aqua-Vu
- Ikke kategoriseret Millecroquettes
- Ikke kategoriseret GR Bass
- Ikke kategoriseret Sure-Fi
- Ikke kategoriseret Copernicus
- Ikke kategoriseret Gumdrop
- Ikke kategoriseret Tellur
- Ikke kategoriseret Gallien-Krueger
- Ikke kategoriseret Jetway
- Ikke kategoriseret Texsport
- Ikke kategoriseret SSV Works
- Ikke kategoriseret Terre
- Ikke kategoriseret Sanitec
- Ikke kategoriseret Pangea Audio
- Ikke kategoriseret Hogue
- Ikke kategoriseret ATP
- Ikke kategoriseret Pfannenberg
- Ikke kategoriseret Scytek
- Ikke kategoriseret MotorScrubber
- Ikke kategoriseret Krone
- Ikke kategoriseret Kraftmax
- Ikke kategoriseret Steelplay
- Ikke kategoriseret PCTV Systems
- Ikke kategoriseret Cooper Lighting
- Ikke kategoriseret Code Corporation
- Ikke kategoriseret Now TV
- Ikke kategoriseret Beautiful
- Ikke kategoriseret Voodoo Lab
- Ikke kategoriseret Insect Lore
- Ikke kategoriseret Kitronik
- Ikke kategoriseret Hamlet
- Ikke kategoriseret SumUp
- Ikke kategoriseret Microlab
- Ikke kategoriseret Rotolight
- Ikke kategoriseret Mr Gardener
- Ikke kategoriseret Lumu
- Ikke kategoriseret WAYDOO
- Ikke kategoriseret Fimer
- Ikke kategoriseret ASIWO
- Ikke kategoriseret 2N
- Ikke kategoriseret Lexar
- Ikke kategoriseret Vent-Axia
- Ikke kategoriseret Firefield
- Ikke kategoriseret E-Power
- Ikke kategoriseret RectorSeal
- Ikke kategoriseret Red Digital Cinema
- Ikke kategoriseret Marathon
- Ikke kategoriseret Cartrend
- Ikke kategoriseret Kaiser Nienhaus
- Ikke kategoriseret Freeplay
- Ikke kategoriseret Roller Grill
- Ikke kategoriseret Cleco
- Ikke kategoriseret Dataflex
- Ikke kategoriseret Handy Lux
- Ikke kategoriseret Rossum Electro-Music
- Ikke kategoriseret Panta
- Ikke kategoriseret Pentel
- Ikke kategoriseret Wallas
- Ikke kategoriseret MagnaPool
- Ikke kategoriseret Aquadon
- Ikke kategoriseret Raidsonic
- Ikke kategoriseret Neunaber
- Ikke kategoriseret Leotec
- Ikke kategoriseret VOREL
- Ikke kategoriseret POWEREX
- Ikke kategoriseret DayStar Filters
- Ikke kategoriseret Flexispot
- Ikke kategoriseret OP/TECH
- Ikke kategoriseret A-NeuVideo
- Ikke kategoriseret Bellari
- Ikke kategoriseret ETC
- Ikke kategoriseret Nuki
- Ikke kategoriseret SWIT
- Ikke kategoriseret Aspen
- Ikke kategoriseret CAD Audio
- Ikke kategoriseret Frequency Central
- Ikke kategoriseret Sacrament
- Ikke kategoriseret Feelworld
- Ikke kategoriseret Trident
- Ikke kategoriseret Schoeps
- Ikke kategoriseret COLBOR
- Ikke kategoriseret Favini
- Ikke kategoriseret Dnipro
- Ikke kategoriseret Polsen
- Ikke kategoriseret IFootage
- Ikke kategoriseret Sonuus
- Ikke kategoriseret Saint Algue
- Ikke kategoriseret Oecolux
- Ikke kategoriseret SoundLAB
- Ikke kategoriseret ACL
- Ikke kategoriseret Mars Gaming
- Ikke kategoriseret Radiant
- Ikke kategoriseret G.Skill
- Ikke kategoriseret Edbak
- Ikke kategoriseret Integral
- Ikke kategoriseret Roline
- Ikke kategoriseret Virax
- Ikke kategoriseret MSW
- Ikke kategoriseret Amaran
- Ikke kategoriseret Gill
- Ikke kategoriseret AMC
- Ikke kategoriseret Triangle
- Ikke kategoriseret I-Tec
- Ikke kategoriseret Anthro
- Ikke kategoriseret DreamLine
- Ikke kategoriseret Tumbleweed
- Ikke kategoriseret Alutruss
- Ikke kategoriseret Sunpentown
- Ikke kategoriseret OKAY
- Ikke kategoriseret Bitspower
- Ikke kategoriseret NEP
- Ikke kategoriseret Lexivon
- Ikke kategoriseret Envertech
- Ikke kategoriseret Lauten Audio
- Ikke kategoriseret Avenview
- Ikke kategoriseret Grendel
- Ikke kategoriseret Coravin
- Ikke kategoriseret Catler
- Ikke kategoriseret Weidmüller
- Ikke kategoriseret O&O Software
- Ikke kategoriseret Warmup
- Ikke kategoriseret Brastemp
- Ikke kategoriseret Satco
- Ikke kategoriseret AMT
- Ikke kategoriseret Artrom
- Ikke kategoriseret Adonit
- Ikke kategoriseret Point Source Audio
- Ikke kategoriseret ANDYCINE
- Ikke kategoriseret AmpliVox
- Ikke kategoriseret Pippi
- Ikke kategoriseret Casalux
- Ikke kategoriseret CyberData Systems
- Ikke kategoriseret Omnitron Systems
- Ikke kategoriseret Stewart Systems
- Ikke kategoriseret SwitchBot
- Ikke kategoriseret Qubino
- Ikke kategoriseret Eurosound
- Ikke kategoriseret Williams Sound
- Ikke kategoriseret Magewell
- Ikke kategoriseret Globalo
- Ikke kategoriseret Adam Hall
- Ikke kategoriseret SoundTube
- Ikke kategoriseret Flaem
- Ikke kategoriseret Therabody
- Ikke kategoriseret Infortrend
- Ikke kategoriseret Kohersen
- Ikke kategoriseret Rug Doctor
- Ikke kategoriseret Raspberry Pi
- Ikke kategoriseret Bals
- Ikke kategoriseret Balt
- Ikke kategoriseret AJ.BA
- Ikke kategoriseret ESKA
- Ikke kategoriseret Lascar Electronics
- Ikke kategoriseret EWON
- Ikke kategoriseret Frient
- Ikke kategoriseret AXESS
- Ikke kategoriseret Glemm
- Ikke kategoriseret Ridem
- Ikke kategoriseret Alga
- Ikke kategoriseret WesAudio
- Ikke kategoriseret Musicmate
- Ikke kategoriseret Robust
- Ikke kategoriseret Quik Lok
- Ikke kategoriseret Tsakalis AudioWorks
- Ikke kategoriseret Jupiter
- Ikke kategoriseret Sony Optiarc
- Ikke kategoriseret Colortone
- Ikke kategoriseret Lowel
- Ikke kategoriseret Super Rod
- Ikke kategoriseret Carnielli
- Ikke kategoriseret Luminex
- Ikke kategoriseret Epiphan
- Ikke kategoriseret HiLook
- Ikke kategoriseret Deltaco Gaming
- Ikke kategoriseret P3 International
- Ikke kategoriseret Beckmann & Egle
- Ikke kategoriseret Seek Thermal
- Ikke kategoriseret VintageView
- Ikke kategoriseret Alfresco
- Ikke kategoriseret Bintec-elmeg
- Ikke kategoriseret Crane Song
- Ikke kategoriseret W'eau
- Ikke kategoriseret Belena
- Ikke kategoriseret Fanox
- Ikke kategoriseret Crouzet
- Ikke kategoriseret Megarevo
- Ikke kategoriseret Tech 21
- Ikke kategoriseret BlendMount
- Ikke kategoriseret Sedona
- Ikke kategoriseret CaterRacks
- Ikke kategoriseret Besco
- Ikke kategoriseret Prologue
- Ikke kategoriseret Soltection
- Ikke kategoriseret Kool-It
- Ikke kategoriseret KeepOut
- Ikke kategoriseret LawnMaster
- Ikke kategoriseret Deltronic
- Ikke kategoriseret Eligent
- Ikke kategoriseret Meris
- Ikke kategoriseret Procare
- Ikke kategoriseret AmerBox
- Ikke kategoriseret Qu-Bit
- Ikke kategoriseret Blue Lantern
- Ikke kategoriseret StarIink
- Ikke kategoriseret DivKid
- Ikke kategoriseret Uniross
- Ikke kategoriseret FaseLunare
- Ikke kategoriseret (Recovery)
- Ikke kategoriseret Twinkly
- Ikke kategoriseret Squarp Instruments
- Ikke kategoriseret EtherWAN
- Ikke kategoriseret Econ Connect
- Ikke kategoriseret Shimbol
- Ikke kategoriseret GC Audio
- Ikke kategoriseret Einhell Bavaria
- Ikke kategoriseret Motrona
- Ikke kategoriseret Thalheimer
- Ikke kategoriseret Ergotools Pattfield
- Ikke kategoriseret FeiYu-Tech
- Ikke kategoriseret VisionTek
- Ikke kategoriseret FeiyuTech
- Ikke kategoriseret Bessey
- Ikke kategoriseret A3
- Ikke kategoriseret Serge
- Ikke kategoriseret Mobli
- Ikke kategoriseret Sonoff
- Ikke kategoriseret Caroma
- Ikke kategoriseret Sungale
- Ikke kategoriseret Befaco
- Ikke kategoriseret Waltec
- Ikke kategoriseret Eartec
- Ikke kategoriseret Elvid
- Ikke kategoriseret Portkeys
- Ikke kategoriseret Westcott
- Ikke kategoriseret Tempo
- Ikke kategoriseret EXSYS
- Ikke kategoriseret Digiquest
- Ikke kategoriseret Gewiss
- Ikke kategoriseret Hagor
- Ikke kategoriseret Glyph
- Ikke kategoriseret Seco-Larm
- Ikke kategoriseret Camille Bauer
- Ikke kategoriseret Massoth
- Ikke kategoriseret Envitec
- Ikke kategoriseret Mimo Monitors
- Ikke kategoriseret Alula
- Ikke kategoriseret Blebox
- Ikke kategoriseret Redsbaby
- Ikke kategoriseret Algo
- Ikke kategoriseret Peloton
- Ikke kategoriseret Gentrax
- Ikke kategoriseret Gamber-Johnson
- Ikke kategoriseret Brocade
- Ikke kategoriseret ICC
- Ikke kategoriseret Insteon
- Ikke kategoriseret Amer
- Ikke kategoriseret Altronix
- Ikke kategoriseret ELTA Music
- Ikke kategoriseret Juniper
- Ikke kategoriseret Longvie
- Ikke kategoriseret Warner Bros
- Ikke kategoriseret Vinotemp
- Ikke kategoriseret Silent Knight
- Ikke kategoriseret Mosconi
- Ikke kategoriseret Ditek
- Ikke kategoriseret Kingston Technology
- Ikke kategoriseret Axxess
- Ikke kategoriseret Goki
- Ikke kategoriseret My Arcade
- Ikke kategoriseret Enttec
- Ikke kategoriseret Tescoma
- Ikke kategoriseret RF Elements
- Ikke kategoriseret ALC
- Ikke kategoriseret Ikelite
- Ikke kategoriseret Holland Electronics
- Ikke kategoriseret Arista
- Ikke kategoriseret Chenbro Micom
- Ikke kategoriseret Triumph Sports
- Ikke kategoriseret Gasmate
- Ikke kategoriseret Crelando
- Ikke kategoriseret Ionmax
- Ikke kategoriseret Seville Classics
- Ikke kategoriseret TechLogix Networx
- Ikke kategoriseret NuTone
- Ikke kategoriseret Meross
- Ikke kategoriseret EchoMaster
- Ikke kategoriseret Bxterra
- Ikke kategoriseret Renogy
- Ikke kategoriseret Babylonia
- Ikke kategoriseret HeartSine
- Ikke kategoriseret Joseph Joseph
- Ikke kategoriseret Morrison
- Ikke kategoriseret Ordo
- Ikke kategoriseret Alphacool
- Ikke kategoriseret Asetek
- Ikke kategoriseret Audibax
- Ikke kategoriseret TechN
- Ikke kategoriseret Eversolo
- Ikke kategoriseret Davita
- Ikke kategoriseret Giga Copper
- Ikke kategoriseret Elsner
- Ikke kategoriseret Séura
- Ikke kategoriseret Cube Controls
- Ikke kategoriseret Meridian
- Ikke kategoriseret Donexon
- Ikke kategoriseret Eve Audio
- Ikke kategoriseret Axagon
- Ikke kategoriseret Linq
- Ikke kategoriseret Wortmann AG
- Ikke kategoriseret DiGiGrid
- Ikke kategoriseret Sanofi
- Ikke kategoriseret Mitzu
- Ikke kategoriseret Omega Altise
- Ikke kategoriseret Fizzics
- Ikke kategoriseret XFX
- Ikke kategoriseret Leynew
- Ikke kategoriseret Cropico
- Ikke kategoriseret Sunwoda
- Ikke kategoriseret Schleich
- Ikke kategoriseret Unitech
- Ikke kategoriseret FXLab
- Ikke kategoriseret Kincrome
- Ikke kategoriseret BC Acoustique
- Ikke kategoriseret Brockhaus HEUER
- Ikke kategoriseret Reishunger
- Ikke kategoriseret Ergotec
- Ikke kategoriseret Dupla
- Ikke kategoriseret IODD
- Ikke kategoriseret BYD
- Ikke kategoriseret Aqua Medic
- Ikke kategoriseret Gold Note
- Ikke kategoriseret Pylontech
- Ikke kategoriseret Fire Sense
- Ikke kategoriseret Grüniq
- Ikke kategoriseret Goodwe
- Ikke kategoriseret Moki
- Ikke kategoriseret Enertex
- Ikke kategoriseret IOTAVX
- Ikke kategoriseret Creality
- Ikke kategoriseret Ovation
- Ikke kategoriseret MDT
- Ikke kategoriseret Enviroswim
- Ikke kategoriseret Dobar
- Ikke kategoriseret Vevor
- Ikke kategoriseret Ovente
- Ikke kategoriseret PowerColor
- Ikke kategoriseret ISpring
- Ikke kategoriseret WeFix
- Ikke kategoriseret BCA
- Ikke kategoriseret Saki
- Ikke kategoriseret Smart365
- Ikke kategoriseret PUR
- Ikke kategoriseret Eldat
- Ikke kategoriseret SoundSwitch
- Ikke kategoriseret Sera
- Ikke kategoriseret Dostmann Electronic
- Ikke kategoriseret JBC
- Ikke kategoriseret DV Mark
- Ikke kategoriseret MOON
- Ikke kategoriseret Shinybow
- Ikke kategoriseret Cuggl
- Ikke kategoriseret HABAU
- Ikke kategoriseret CVW
- Ikke kategoriseret Majority
- Ikke kategoriseret Earbreeze
- Ikke kategoriseret Möhlenhoff
- Ikke kategoriseret Taqua
- Ikke kategoriseret NightStick
- Ikke kategoriseret Brainstorm
- Ikke kategoriseret Colonial Elegance
- Ikke kategoriseret Overtone Labs
- Ikke kategoriseret Bühnen
- Ikke kategoriseret Blukac
- Ikke kategoriseret BendixKing
- Ikke kategoriseret Tube-Tech
- Ikke kategoriseret TCW Technologies
- Ikke kategoriseret UNITEK
- Ikke kategoriseret CoolerMaster
- Ikke kategoriseret Rexing
- Ikke kategoriseret The T.mix
- Ikke kategoriseret Regula-Werk King
- Ikke kategoriseret Inter-M
- Ikke kategoriseret MIDI Solutions
- Ikke kategoriseret Positive Grid
- Ikke kategoriseret Amgrow
- Ikke kategoriseret Xaphoon
- Ikke kategoriseret Winchester
- Ikke kategoriseret Lampa
- Ikke kategoriseret Sinus Live
- Ikke kategoriseret Sureguard
- Ikke kategoriseret QuickCool
- Ikke kategoriseret Smit Visual
- Ikke kategoriseret NZR
- Ikke kategoriseret Toparc
- Ikke kategoriseret Oro-Med
- Ikke kategoriseret Hex
- Ikke kategoriseret Baby Cakes
- Ikke kategoriseret Deflecto
- Ikke kategoriseret ELMEKO
- Ikke kategoriseret Tesseract Modular
- Ikke kategoriseret Sport Dog
- Ikke kategoriseret Nowsonic
- Ikke kategoriseret On Air
- Ikke kategoriseret Acoustic Solutions
- Ikke kategoriseret E-ast
- Ikke kategoriseret Hubble Connected
- Ikke kategoriseret We-Vibe
- Ikke kategoriseret Electronics International
- Ikke kategoriseret Lamar
- Ikke kategoriseret Atlantis Land
- Ikke kategoriseret White Lightning
- Ikke kategoriseret Kaiser Fototechnik
- Ikke kategoriseret Hoymiles
- Ikke kategoriseret Vishay
- Ikke kategoriseret Sonorous
- Ikke kategoriseret Rooboost
- Ikke kategoriseret JMAZ Lighting
- Ikke kategoriseret Comar
- Ikke kategoriseret Freedor
- Ikke kategoriseret Start International
- Ikke kategoriseret AXITEC
- Ikke kategoriseret Lingg & Janke
- Ikke kategoriseret Auralex
- Ikke kategoriseret Pieps
- Ikke kategoriseret Innovative
- Ikke kategoriseret Lynx Technik
- Ikke kategoriseret Yuede
- Ikke kategoriseret Pliant Technologies
- Ikke kategoriseret Astropet
- Ikke kategoriseret Busch + Müller
- Ikke kategoriseret Canopia
- Ikke kategoriseret Wabeco
- Ikke kategoriseret Swingline GBC
- Ikke kategoriseret Staudte-Hirsch
- Ikke kategoriseret Universal Remote Control
- Ikke kategoriseret Lantronix
- Ikke kategoriseret Kino Flo
- Ikke kategoriseret Aqua Computer
- Ikke kategoriseret HEDD
- Ikke kategoriseret Vinpower Digital
- Ikke kategoriseret Magivaac
- Ikke kategoriseret Lindemann
- Ikke kategoriseret Silent Angel
- Ikke kategoriseret Prowork
- Ikke kategoriseret Creamsource
- Ikke kategoriseret ZWO
- Ikke kategoriseret Bbf
- Ikke kategoriseret Club 3D
- Ikke kategoriseret Sprolink
- Ikke kategoriseret Thermionic Culture
- Ikke kategoriseret Watercool
- Ikke kategoriseret Skaarhoj
- Ikke kategoriseret Microboards
- Ikke kategoriseret Whitestone
- Ikke kategoriseret BMB
- Ikke kategoriseret Arylic
- Ikke kategoriseret Gem Toys
- Ikke kategoriseret Mount-It!
- Ikke kategoriseret Cloud
- Ikke kategoriseret Sandia Aerospace
- Ikke kategoriseret Lamptron
- Ikke kategoriseret PS Audio
- Ikke kategoriseret Gudsen
- Ikke kategoriseret Zendure
- Ikke kategoriseret Phanteks
- Ikke kategoriseret Prism Sound
- Ikke kategoriseret Gosund
- Ikke kategoriseret ID-Tech
- Ikke kategoriseret DMT
- Ikke kategoriseret FSP/Fortron
- Ikke kategoriseret CM Storm
- Ikke kategoriseret Meopta
- Ikke kategoriseret SEADA
- Ikke kategoriseret Honey-Can-Do
- Ikke kategoriseret Deity
- Ikke kategoriseret Patriot
- Ikke kategoriseret Taga Harmony
- Ikke kategoriseret B.E.G.
- Ikke kategoriseret Fixpoint
- Ikke kategoriseret Enerdrive
- Ikke kategoriseret Respironics
- Ikke kategoriseret ChamSys
- Ikke kategoriseret TESLA Electronics
- Ikke kategoriseret Intesis
- Ikke kategoriseret Nethix
- Ikke kategoriseret Pluto
- Ikke kategoriseret Laine
- Ikke kategoriseret 3Doodler
- Ikke kategoriseret Soundskins
- Ikke kategoriseret Middle Atlantic Products
- Ikke kategoriseret Datapath
- Ikke kategoriseret Loctite
- Ikke kategoriseret Antelope
- Ikke kategoriseret Vertiv
- Ikke kategoriseret Astera
- Ikke kategoriseret Polyend
- Ikke kategoriseret BASSBOSS
- Ikke kategoriseret Sabco
- Ikke kategoriseret Sensative
- Ikke kategoriseret Magmatic
- Ikke kategoriseret Plasma Cloud
- Ikke kategoriseret Flo
- Ikke kategoriseret Sheeran Looper
- Ikke kategoriseret Applico
- Ikke kategoriseret Jungle Gym
- Ikke kategoriseret Smart Media
- Ikke kategoriseret TOGU
- Ikke kategoriseret Roadinger
- Ikke kategoriseret Christmaxx
- Ikke kategoriseret Code
- Ikke kategoriseret Mivar
- Ikke kategoriseret SolaX Power
- Ikke kategoriseret AURALiC
- Ikke kategoriseret AkYtec
- Ikke kategoriseret Absco
- Ikke kategoriseret Schatten Design
- Ikke kategoriseret LEDs-ON
- Ikke kategoriseret Bestgreen
- Ikke kategoriseret MyPOS
- Ikke kategoriseret Truetone
- Ikke kategoriseret Stages
- Ikke kategoriseret Starlink
- Ikke kategoriseret HDFury
- Ikke kategoriseret Favero
- Ikke kategoriseret Durvet
- Ikke kategoriseret KNEKT
- Ikke kategoriseret Gator Frameworks
- Ikke kategoriseret Teia
- Ikke kategoriseret The Joy Factory
- Ikke kategoriseret Yuer
- Ikke kategoriseret OSEE
- Ikke kategoriseret OLLO
- Ikke kategoriseret Axor
- Ikke kategoriseret Gustard
- Ikke kategoriseret Enhance
- Ikke kategoriseret MEPROLIGHT
- Ikke kategoriseret Tactical Fiber Systems
- Ikke kategoriseret Veber
- Ikke kategoriseret PurAthletics
- Ikke kategoriseret SMS
- Ikke kategoriseret Carlo Gavazzi
- Ikke kategoriseret Richgro
- Ikke kategoriseret Varaluz
- Ikke kategoriseret Milesight
- Ikke kategoriseret Dehner
- Ikke kategoriseret Edwards
- Ikke kategoriseret Victor Technology
- Ikke kategoriseret Lastolite
- Ikke kategoriseret Lowepro
- Ikke kategoriseret MIOPS
- Ikke kategoriseret WiiM
- Ikke kategoriseret Bluebird
- Ikke kategoriseret Cotek
- Ikke kategoriseret EA Elektro Automatik
- Ikke kategoriseret CMI
- Ikke kategoriseret Grand Effects
- Ikke kategoriseret SunPower
- Ikke kategoriseret Hensel
- Ikke kategoriseret Westland
- Ikke kategoriseret Bahr
- Ikke kategoriseret Black Line
- Ikke kategoriseret Sodapop
- Ikke kategoriseret Enbrighten
- Ikke kategoriseret Albert Heijn
- Ikke kategoriseret Yphix
- Ikke kategoriseret TAURUS Titanium
- Ikke kategoriseret Magliner
- Ikke kategoriseret Comfortisse
- Ikke kategoriseret Cayin
- Ikke kategoriseret Videotel Digital
- Ikke kategoriseret Zylight
- Ikke kategoriseret HuddleCamHD
- Ikke kategoriseret Technical Pro
- Ikke kategoriseret BIOS Living
- Ikke kategoriseret Connection
- Ikke kategoriseret Blind Spot
- Ikke kategoriseret Badiona
- Ikke kategoriseret VMV
- Ikke kategoriseret Expressive E
- Ikke kategoriseret Merging
- Ikke kategoriseret CSL
- Ikke kategoriseret Altman
- Ikke kategoriseret EXO
- Ikke kategoriseret Hawke
- Ikke kategoriseret Defender
- Ikke kategoriseret Betty Bossi
- Ikke kategoriseret FoxFury
- Ikke kategoriseret Eller
- Ikke kategoriseret Rotatrim
- Ikke kategoriseret Peak Design
- Ikke kategoriseret Uniropa
- Ikke kategoriseret Eura
- Ikke kategoriseret ESE
- Ikke kategoriseret Meriden
- Ikke kategoriseret Hecate
- Ikke kategoriseret Gra-Vue
- Ikke kategoriseret On-Stage
- Ikke kategoriseret Primewire
- Ikke kategoriseret Titanwolf
- Ikke kategoriseret Uplink
- Ikke kategoriseret Mybeo
- Ikke kategoriseret Medicinalis
- Ikke kategoriseret Liam&Daan
- Ikke kategoriseret Traco Power
- Ikke kategoriseret Bebob
- Ikke kategoriseret Xcellon
- Ikke kategoriseret CAME-TV
- Ikke kategoriseret Nureva
- Ikke kategoriseret Revic
- Ikke kategoriseret Galcon
- Ikke kategoriseret Telmax
- Ikke kategoriseret Apollo Design
- Ikke kategoriseret DEERSYNC
- Ikke kategoriseret JoeCo
- Ikke kategoriseret Holosun
- Ikke kategoriseret CubuSynth
- Ikke kategoriseret Exelpet
- Ikke kategoriseret Noyafa
- Ikke kategoriseret AddLiving
- Ikke kategoriseret IOIO
- Ikke kategoriseret City Theatrical
- Ikke kategoriseret Redback Technologies
- Ikke kategoriseret Bome
- Ikke kategoriseret One Control
- Ikke kategoriseret EQ Acoustics
- Ikke kategoriseret AV Tool
- Ikke kategoriseret Aquael
- Ikke kategoriseret NEXTO DI
- Ikke kategoriseret Thermarest
- Ikke kategoriseret Fortinge
- Ikke kategoriseret RF-Links
- Ikke kategoriseret LiveU
- Ikke kategoriseret Austral
- Ikke kategoriseret Luxul
- Ikke kategoriseret Cherub
- Ikke kategoriseret ProLights
- Ikke kategoriseret Xinfrared
- Ikke kategoriseret Brizo
- Ikke kategoriseret I-PRO
- Ikke kategoriseret Europalms
- Ikke kategoriseret DuroStar
- Ikke kategoriseret Mr Steam
- Ikke kategoriseret Sensei
- Ikke kategoriseret DVDO
- Ikke kategoriseret A-Designs
- Ikke kategoriseret Henry Engineering
- Ikke kategoriseret Primacoustic
- Ikke kategoriseret HomeCraft
- Ikke kategoriseret Heusinkveld
- Ikke kategoriseret EnOcean
- Ikke kategoriseret Storcube
- Ikke kategoriseret Varia
- Ikke kategoriseret Gurari
- Ikke kategoriseret Fezz
- Ikke kategoriseret ASI
- Ikke kategoriseret Swiss Eye
- Ikke kategoriseret Cane Creek
- Ikke kategoriseret EPEVER
- Ikke kategoriseret KED
- Ikke kategoriseret Caberg
- Ikke kategoriseret Exped
- Ikke kategoriseret Lawn Star
- Ikke kategoriseret Edouard Rousseau
- Ikke kategoriseret GameDay
- Ikke kategoriseret Sparkle
- Ikke kategoriseret Söll
- Ikke kategoriseret X-Lite
- Ikke kategoriseret Røde
- Ikke kategoriseret Envertec
- Ikke kategoriseret Nordic Winter
- Ikke kategoriseret Volcano
- Ikke kategoriseret XS Power
- Ikke kategoriseret Noritz
- Ikke kategoriseret Aimpoint
- Ikke kategoriseret Wire Technologies
- Ikke kategoriseret Taco Tuesday
- Ikke kategoriseret CEEM
- Ikke kategoriseret IMM Photonics
- Ikke kategoriseret Field Optics
- Ikke kategoriseret Signature Hardware
- Ikke kategoriseret UAvionix
- Ikke kategoriseret Roesle
- Ikke kategoriseret Robern
- Ikke kategoriseret GRAUGEAR
- Ikke kategoriseret Livall
- Ikke kategoriseret Sure Petcare
- Ikke kategoriseret Beaphar
- Ikke kategoriseret Van Der Valk
- Ikke kategoriseret Sortimo
- Ikke kategoriseret Primus WindPower
- Ikke kategoriseret AtomStack
- Ikke kategoriseret Mr. Beam
- Ikke kategoriseret Rixen&Kaul
- Ikke kategoriseret Mebby
- Ikke kategoriseret TONI&GUY
- Ikke kategoriseret Balam Rush
- Ikke kategoriseret Oreg
- Ikke kategoriseret Karran
- Ikke kategoriseret Topex
- Ikke kategoriseret OOONO
- Ikke kategoriseret CaviLock
- Ikke kategoriseret Origin Storage
- Ikke kategoriseret Saphe
- Ikke kategoriseret Stamos
- Ikke kategoriseret Ulsonix
- Ikke kategoriseret Stamony
- Ikke kategoriseret Uniprodo
- Ikke kategoriseret Pro Tuning
- Ikke kategoriseret PITSOS
- Ikke kategoriseret Physa
- Ikke kategoriseret Yamazen
- Ikke kategoriseret Sharkbite
- Ikke kategoriseret Netter Vibration
- Ikke kategoriseret YA-MAN
- Ikke kategoriseret Cressi
- Ikke kategoriseret Stelzner
- Ikke kategoriseret Belulu
- Ikke kategoriseret CRAFT + MAIN
- Ikke kategoriseret Hellberg
- Ikke kategoriseret V-Tone
- Ikke kategoriseret ORCA
- Ikke kategoriseret Symmons
- Ikke kategoriseret LARQ
- Ikke kategoriseret Corona
- Ikke kategoriseret Uvex
- Ikke kategoriseret Dynon Avionics
- Ikke kategoriseret Rocada
- Ikke kategoriseret IMC Networks
- Ikke kategoriseret Matterport
- Ikke kategoriseret Nicols
- Ikke kategoriseret Vitec
- Ikke kategoriseret Burgwachter
- Ikke kategoriseret Das Keyboard
- Ikke kategoriseret Schaffner
- Ikke kategoriseret Avinity
- Ikke kategoriseret NeoMounts
- Ikke kategoriseret Jacuzzi
- Ikke kategoriseret Noordi
- Ikke kategoriseret Freewell
- Ikke kategoriseret Sea&Sea
- Ikke kategoriseret Contours
- Ikke kategoriseret Kolcraft
- Ikke kategoriseret Bulgin
- Ikke kategoriseret Pure 100
- Ikke kategoriseret Triplett
- Ikke kategoriseret RC Allen
- Ikke kategoriseret STANDARD
- Ikke kategoriseret BigBlue
- Ikke kategoriseret Plastkon
- Ikke kategoriseret Wiesenfield
- Ikke kategoriseret Tele Vue
- Ikke kategoriseret Pyrex
- Ikke kategoriseret Vigitron
- Ikke kategoriseret Icron
- Ikke kategoriseret AstrHori
- Ikke kategoriseret Studio Titan
- Ikke kategoriseret Platypus
- Ikke kategoriseret Tilta
- Ikke kategoriseret Luxli
- Ikke kategoriseret Decimator
- Ikke kategoriseret Ferrofish
- Ikke kategoriseret Chimera
- Ikke kategoriseret Blonder Tongue
- Ikke kategoriseret Crystal Video
- Ikke kategoriseret ButtKicker
- Ikke kategoriseret PAG
- Ikke kategoriseret Really Right Stuff
- Ikke kategoriseret HPRC
- Ikke kategoriseret Petite Chérie
- Ikke kategoriseret Njoy
- Ikke kategoriseret Contemporary Research
- Ikke kategoriseret VCDS
- Ikke kategoriseret ProFlo
- Ikke kategoriseret Trezor
- Ikke kategoriseret Senseca
- Ikke kategoriseret Western Co.
- Ikke kategoriseret Ruggard
- Ikke kategoriseret Moman
- Ikke kategoriseret Aalberg Audio
- Ikke kategoriseret Violectric
- Ikke kategoriseret DiversiTech
- Ikke kategoriseret Bolin Technology
- Ikke kategoriseret Total Chef
- Ikke kategoriseret Total
- Ikke kategoriseret PoLabs
- Ikke kategoriseret Taiji
- Ikke kategoriseret Evooch
- Ikke kategoriseret Fellow
- Ikke kategoriseret Pfister
- Ikke kategoriseret Digi-Pas
- Ikke kategoriseret Klauke
- Ikke kategoriseret Harder & Steenbeck
- Ikke kategoriseret Axler
- Ikke kategoriseret Gerber
- Ikke kategoriseret Royale
- Ikke kategoriseret Venicci
- Ikke kategoriseret ARNOLD Lichttechnik
- Ikke kategoriseret Momini
- Ikke kategoriseret MK
- Ikke kategoriseret API Audio
- Ikke kategoriseret Altech UEC
- Ikke kategoriseret Moomin
- Ikke kategoriseret Jedo
- Ikke kategoriseret Bayco
- Ikke kategoriseret Coors Light
- Ikke kategoriseret Arco
- Ikke kategoriseret KoolScapes
- Ikke kategoriseret Califone
- Ikke kategoriseret LightKeeper Pro
- Ikke kategoriseret Lenz
- Ikke kategoriseret BMAX
- Ikke kategoriseret Singercon
- Ikke kategoriseret Pivo
- Ikke kategoriseret CatSynth
- Ikke kategoriseret Lantus
- Ikke kategoriseret Sifflus
- Ikke kategoriseret Ember
- Ikke kategoriseret LittleHippo
- Ikke kategoriseret ACOPower
- Ikke kategoriseret SafeMi
- Ikke kategoriseret Cosi Home
- Ikke kategoriseret Magnima
- Ikke kategoriseret Kurgo
- Ikke kategoriseret URC
- Ikke kategoriseret Telycam
- Ikke kategoriseret JLCooper
- Ikke kategoriseret DQ
- Ikke kategoriseret Rock N Roller
- Ikke kategoriseret XTRARM
- Ikke kategoriseret Paxton
- Ikke kategoriseret Twisted Electrons
- Ikke kategoriseret Pulsar Observatories
- Ikke kategoriseret Doona
- Ikke kategoriseret USL
- Ikke kategoriseret SolidDrive
- Ikke kategoriseret SKB
- Ikke kategoriseret Cyber Acoustics
- Ikke kategoriseret Bright Starts
- Ikke kategoriseret MSolutions
- Ikke kategoriseret QZ
- Ikke kategoriseret Singularity Computers
- Ikke kategoriseret Sesame Street
- Ikke kategoriseret Ingenuity
- Ikke kategoriseret Digital Forecast
- Ikke kategoriseret Autoscript
- Ikke kategoriseret Minisforum
- Ikke kategoriseret SmartGyro
- Ikke kategoriseret Hoya
- Ikke kategoriseret Miyota
- Ikke kategoriseret Phase Technology
- Ikke kategoriseret CkeyiN
- Ikke kategoriseret Casr
- Ikke kategoriseret Louroe Electronics
- Ikke kategoriseret Zaahn
- Ikke kategoriseret Pasquini
- Ikke kategoriseret Sportime
- Ikke kategoriseret Speaker Snap
- Ikke kategoriseret CLIMAQUA
- Ikke kategoriseret Quasar Science
- Ikke kategoriseret Zeapon
- Ikke kategoriseret Vuze
- Ikke kategoriseret Beltronics
- Ikke kategoriseret Jan Nowak
- Ikke kategoriseret Kiano
- Ikke kategoriseret Prido
- Ikke kategoriseret Homekraft
- Ikke kategoriseret HiRO
- Ikke kategoriseret Forodi
- Ikke kategoriseret CELLFAST
- Ikke kategoriseret MOZOS
- Ikke kategoriseret Bioogród
- Ikke kategoriseret Elight
- Ikke kategoriseret Laifen
- Ikke kategoriseret MQ
- Ikke kategoriseret Mikavi
- Ikke kategoriseret Controly
- Ikke kategoriseret Mesmed
- Ikke kategoriseret PetRhein
- Ikke kategoriseret Pengo
- Ikke kategoriseret Racktime
- Ikke kategoriseret Leba
- Ikke kategoriseret Zapf
- Ikke kategoriseret Infosec
- Ikke kategoriseret Therm-a-Rest
- Ikke kategoriseret Hoffman
- Ikke kategoriseret Redback
Nyeste Ikke kategoriseret Manualer

10 April 2025
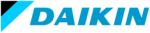
10 April 2025
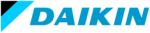
10 April 2025
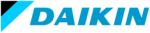
10 April 2025
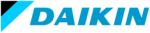
10 April 2025
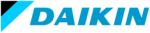
10 April 2025
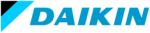
10 April 2025
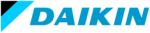
9 April 2025
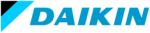
9 April 2025

9 April 2025