Rinnai LS800 Manual
Rinnai
Varmeapparat
LS800
Læs nedenfor 📖 manual på dansk for Rinnai LS800 (38 sider) i kategorien Varmeapparat. Denne guide var nyttig for 11 personer og blev bedømt med 4.5 stjerner i gennemsnit af 2 brugere
Side 1/38
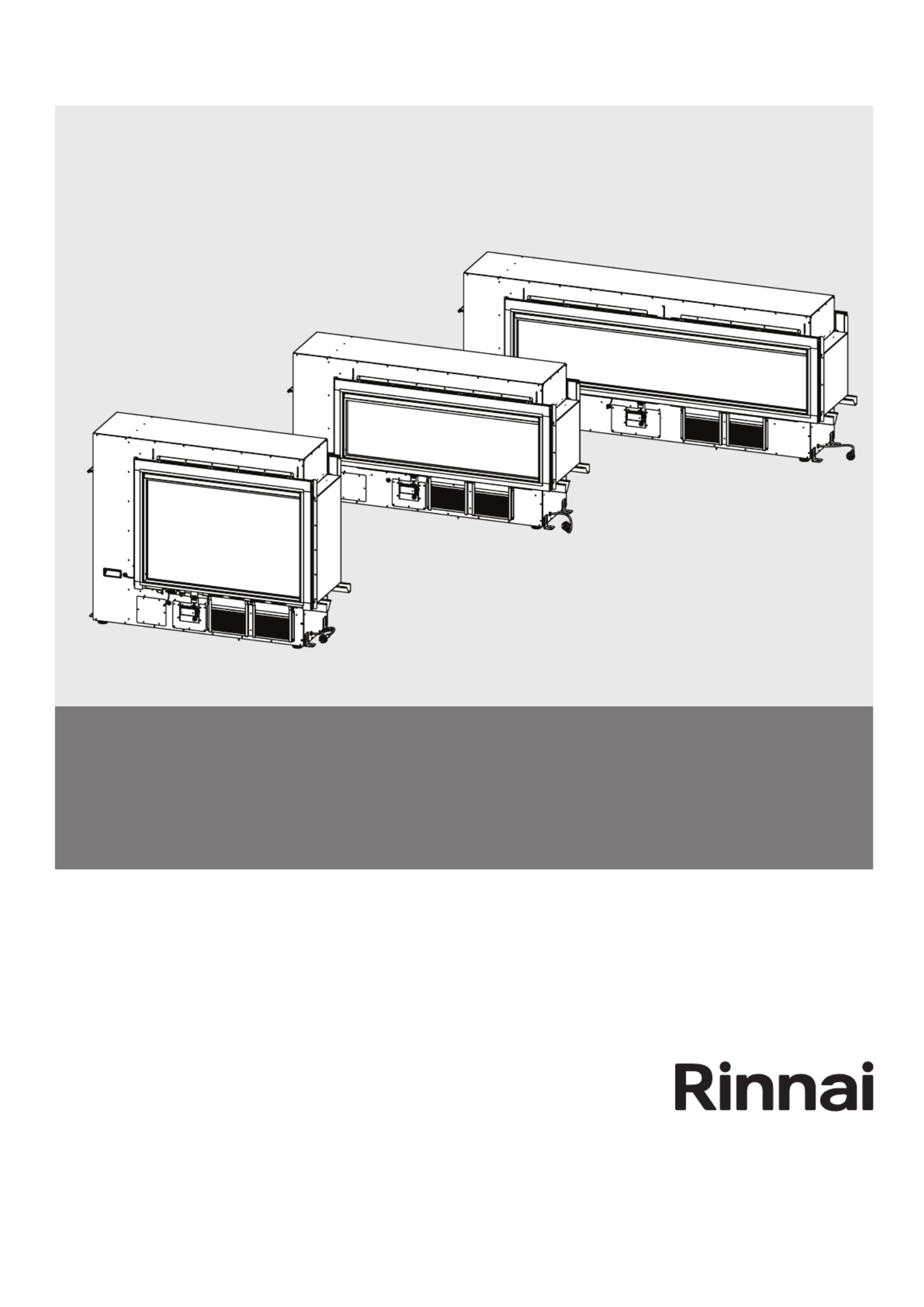
LS - Gas Fireplace
Installation Manual
Models:
Flametech® (RHFE0800F)
LS1000 (RHFE1000)
LS1500 (RHFE1500)
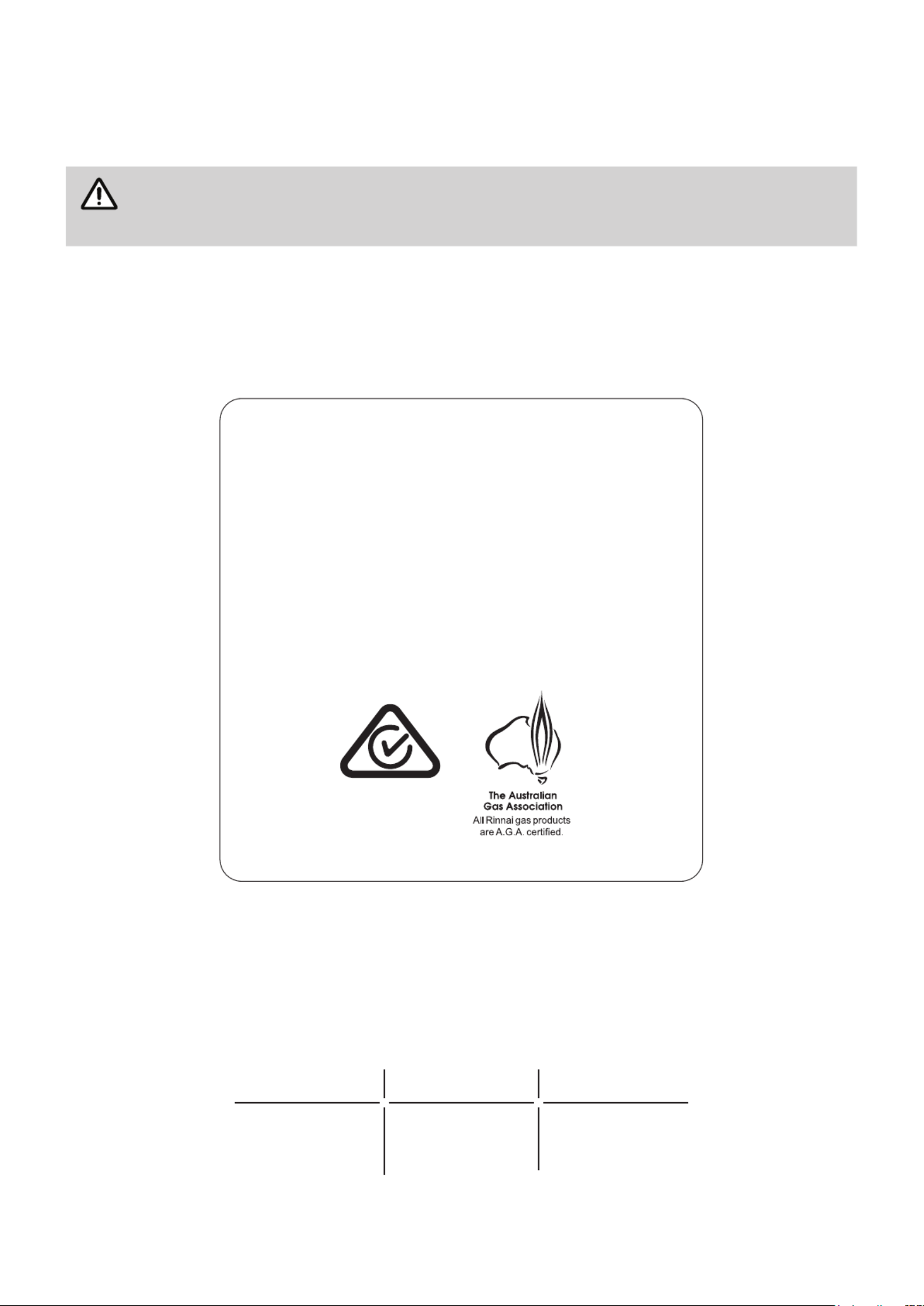
Rinnai 2 RHFE0800F_1000_1500 IM
Congratulations on the purchase of your Rinnai LS - Gas Fireplace. We trust you will have many years of comfort
and enjoyment from your appliance.
IMPORTANT
BEFORE INSTALLING OR USING THIS APPLIANCE
Before proceeding with the operation or installation read this manual thoroughly and gain a full
understanding of the appliance, to ensure safe and correct installation and use.
This appliance must be installed in accordance with:
• Manufacturer’s Installation Instructions
• Current AS/NZS 3500
• Plumbing Code of Australia (PCA)
• Local Regulations and Municipal Building Codes
including local OH&S requirements
This system must be installed, commissioned, serviced,
maintained and removed ONLY by an Authorised Person.
For continued safety this appliance it must be installed and of
maintained in accordance with the manufacturer’s instructions.
This manual to suit LS - Gas Fireplace Heater Models:
Flametech® * LS1000 LS1500
RHFE0800SF * RHFE1000S RHFE1500S
RHFE0800DF * RHFE1000D RHFE1500D
*Incorporates Flametech® self burning log technology.
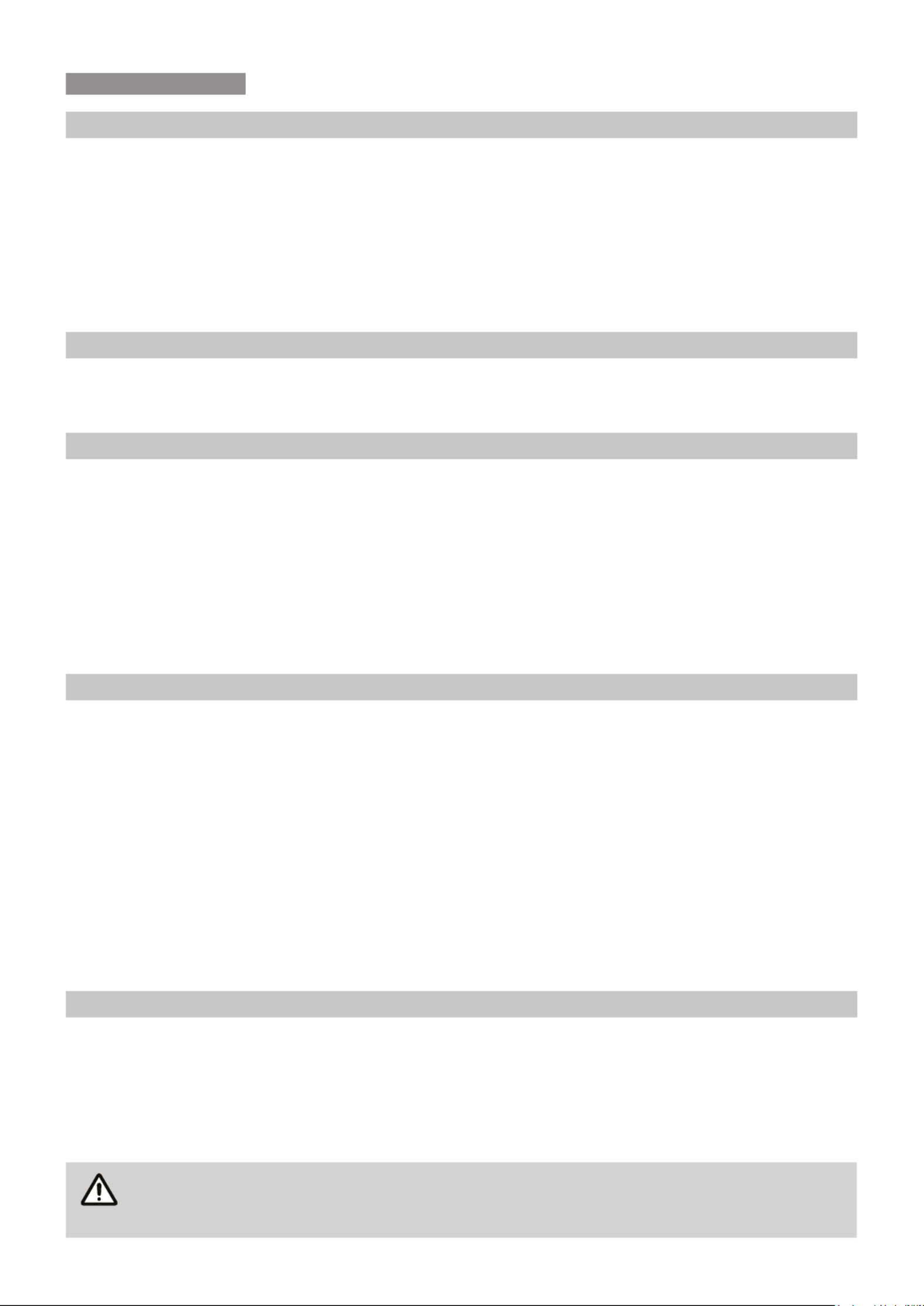
Rinnai 3 RHFE0800F_1000_1500 IM
WARNING
This appliance be installed, maintained and removed MUST ONLY by an Authorised Person.
For continued safety of this appliance it be installed and maintained in accordance with MUST
the manufacturers instructions.
Warnings & Important Information 5
Before Using or Installing This Appliance 5 ........................................................................................................................
Regulatory Information 5 .......................................................................................................................................................
Dress Guard Warnings 5 ........................................................................................................................................................
Mandatory Inspection prior to Installation 5 ........................................................................................................................
Modications. ....................................................................................................................................................................... 6
General Safety Warnings 6 ....................................................................................................................................................
General Installation Information 8
Location 8 ................................................................................................................................................................................
TV & Ornamentation Warning 8 .............................................................................................................................................
Framing 9
Framing Dimensions 9 ...........................................................................................................................................................
Base Board and Cut-outs 9 ��������������������������������������������������������������������������������������������������������������������������������������������������
Cavity Ventilation 9 .................................................................................................................................................................
Additional Framing Notes 9 ...................................................................................................................................................
Framing for RHFE0800F 10 ....................................................................................................................................................
Framing for RHFE1000 .......................................................................................................................................................11
Framing for RHFE1500 12 ......................................................................................................................................................
Supply Connections 13
Installing Engine Into Cavity 13 .............................................................................................................................................
Adjustable Feet 13 ���������������������������������������������������������������������������������������������������������������������������������������������������������������
Seismic Brackets 13 �������������������������������������������������������������������������������������������������������������������������������������������������������������
Removing the Burner Box Glass ...................................................................................................................................... 14
Gas Supply 15 .........................................................................................................................................................................
Installation of Consumer Piping 15 ��������������������������������������������������������������������������������������������������������������������������������������
Purging Gas Supply 15 ��������������������������������������������������������������������������������������������������������������������������������������������������������
Leak Testing the Connection 15 �������������������������������������������������������������������������������������������������������������������������������������������
Room thermistor 15 ................................................................................................................................................................
Electrical Supply 16 ................................................................................................................................................................
Direct Wired Installations 16 ������������������������������������������������������������������������������������������������������������������������������������������������
Flueing 17
Flue Exhaust & Air Inlet Connections 17 ..............................................................................................................................
Installation Conguration Warnings ................................................................................................................................ 18
Flue Terminal Location 20 ......................................................................................................................................................
Flue Components 21 ..............................................................................................................................................................
INSTALLATION TABLE OF CONTENTS
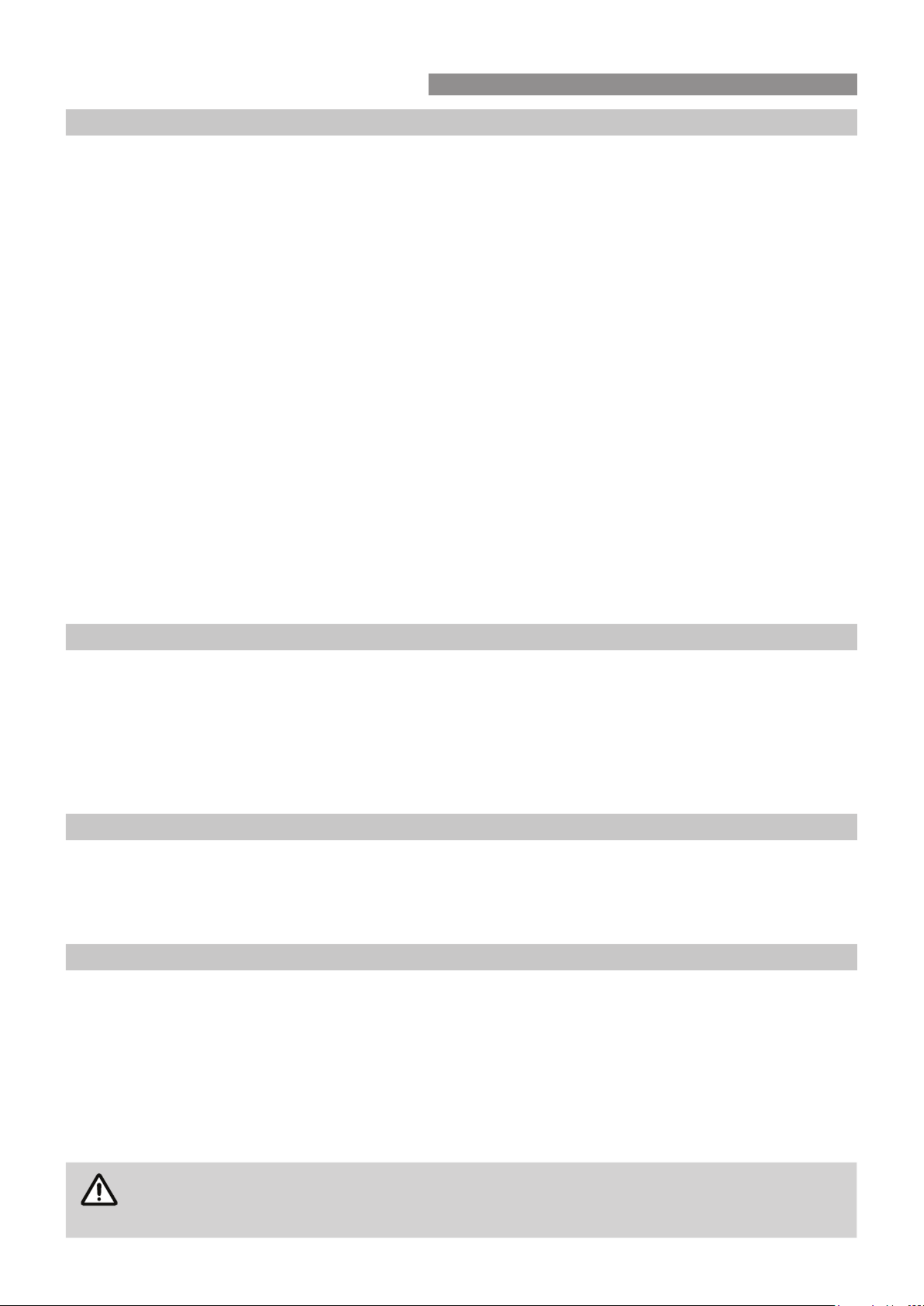
Rinnai 4 RHFE0800F_1000_1500 IM
WARNING
This appliance be installed, maintained and removed MUST ONLY by an Authorised Person.
For continued safety of this appliance it be installed and maintained in accordance with MUST
the manufacturers instructions.
Commissioning 22
General Information ........................................................................................................................................................... 22
Gas Pressure Setting 22 ........................................................................................................................................................
Commissioning the PCB 23 ...................................................................................................................................................
Room Thermistor Oset ................................................................................................................................................... 23
Thermistor Oset Adjustment ������������������������������������������������������������������������������������������������������������������������������������������ 23
Gas Control Solenoids 23 ......................................................................................................................................................
Gas Pressures .................................................................................................................................................................... 24
Setting Gas Pressures 24 ......................................................................................................................................................
Checking the Supply Pressure 24 ����������������������������������������������������������������������������������������������������������������������������������������
Setting the Pilot Pressure 25 ������������������������������������������������������������������������������������������������������������������������������������������������
Setting the Operating Pressure 25 ���������������������������������������������������������������������������������������������������������������������������������������
Burn media installation 26 .....................................................................................................................................................
Test Operation and Lighting Sequence 26 ...........................................................................................................................
Abnormal Flame Pattern 26 ...................................................................................................................................................
Check W -F Connectivity 27i i .................................................................................................................................................
Resetting Wi-Fi Module 27 .....................................................................................................................................................
Installation Checklist & Installation Record 27 ....................................................................................................................
Wall Lining Installation 28
Plasterboard Wall With Plastered Finish 29 .........................................................................................................................
Edge Finishing Options 30 ....................................................................................................................................................
Tiled Or Second Skin Wall Linings 31 ...................................................................................................................................
Non-Combustible Thick Wall Linings 32 ..............................................................................................................................
Non-Combustible Recess Installations 33 ...........................................................................................................................
Specications 34
Table 1. Appliance Details 34 .................................................................................................................................................
Table 2. Dimensions 35 ..........................................................................................................................................................
Wiring Diagram 36 ..................................................................................................................................................................
Contacts 38
INSTALLATION TABLE OF CONTENTS
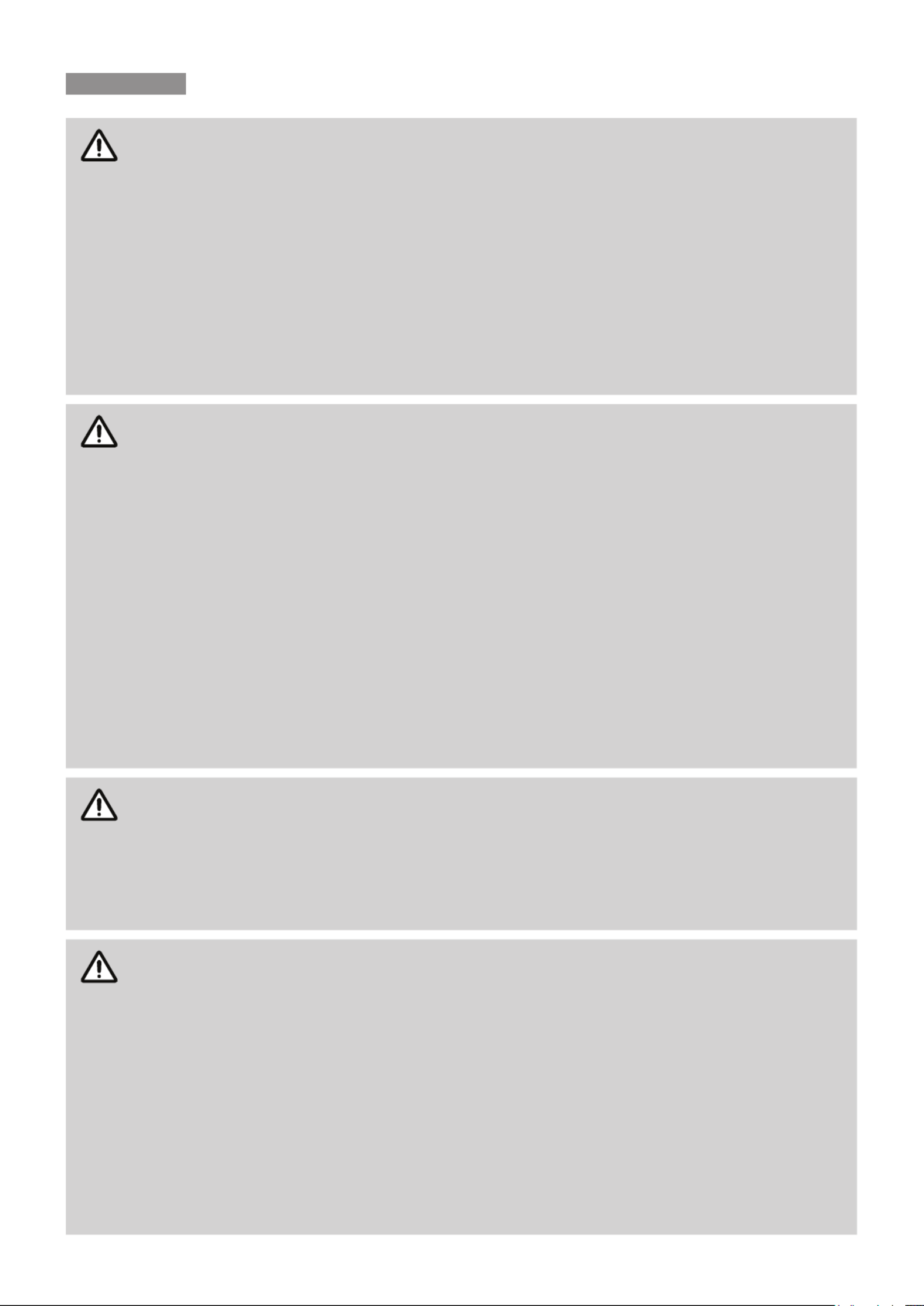
Rinnai 5 RHFE0800F_1000_1500 IM
IMPORTANT
BEFORE USING OR INSTALLING THIS APPLIANCE
Before proceeding with the operation or installation read this manual thoroughly and gain a full
understanding of the appliance, to ensure safe and correct use.
Failure to carefully read and follow all instructions in this manual can result in equipment
malfunction, property damage, personal injury and/or death.
DANGER: Indicates an imminently hazardous situation which, if not avoided, will result in
personal injury or death.
WARNINGS: Indicates a potentially hazardous situation which, if not avoided, could result in
personal injury or death.
CAUTIONS: Indicates a potentially hazardous situation which, if not avoided, could result in
minor or moderate injury or damage to the appliance. It may also be used to alert against unsafe
practices.
WARNING
REGULATORY INFORMATION
This appliance shall be installed in accordance with:
Manufacturer’s Installation Instructions.
Current AS/NZS 3000, AS/NZS 3500 & AS/NZS 5601.
Local Regulations and Municipal Building Codes including local OH&S requirements.
This appliance has been certied by the Australian Gas Association. The A.G.A. Certication
Number is shown on the data plate.
This appliance be installed, maintained and removed MUST ONLY by an Authorised Person.
For continued safety of this appliance it be installed and maintained in accordance with MUST
the manufacturers instructions.
NOTICE TO VICTORIAN CONSUMERS
This appliance be installed by a person licensed with the Victorian Building Authority. MUST
ONLY a licensed person will have insurance protecting their workmanship.
So make sure you use a licensed person to install this appliance and ask for your Compliance
Certicate. For further information contact the Victorian Building Authority on 1300 815 127.
WARNING
DRESS GUARD WARNINGS
The guard is tted to this appliance to reduce the risk of re or injury from burns and
no part of it should be permanently removed. For protection of young children or the
inrm, a secondary guard is required.
The glass dress guard supplied with this appliance MUST NOT be permanently removed as it
fulls an operational safety function. Additional dress guards including free standing types may
be used in conjunction with, but replace, the dress guard supplied with this appliance.NOT
WARNING
MANDATORY INSPECTION PRIOR TO INSTALLATION
Immediately report any damage or discrepancies to the Supplier of the appliance. This
appliance was inspected and tested at the time of manufacture and packaging, and released for
transportation without known damage. Upon receipt, inspect the exterior for evidence of rough
handling in shipment. Ensure that the appliance is labelled correctly for the gas and electrical
supply, and/or other services it is intended to be connected to.
For safety and warranty purposes, appliances that may be damaged or incorrect MUST NOT be
installed or operated under ANY circumstances. Installation of damaged or incorrect appliances
may contravene local government regulations. Rinnai disclaims any liability or responsibility
whatsoever in relation to the installation or operation of damaged or incorrect appliances.
Take care when opening or unpacking this appliance. Failure to do so may result in serious injury
or product failure.
Check the label for the correct gas type (refer rating plate, inside the appliance). Refer to local gas
authority for conrmation of the gas type if you are in doubt.
WARNINGS & IMPORTANT INFORMATION
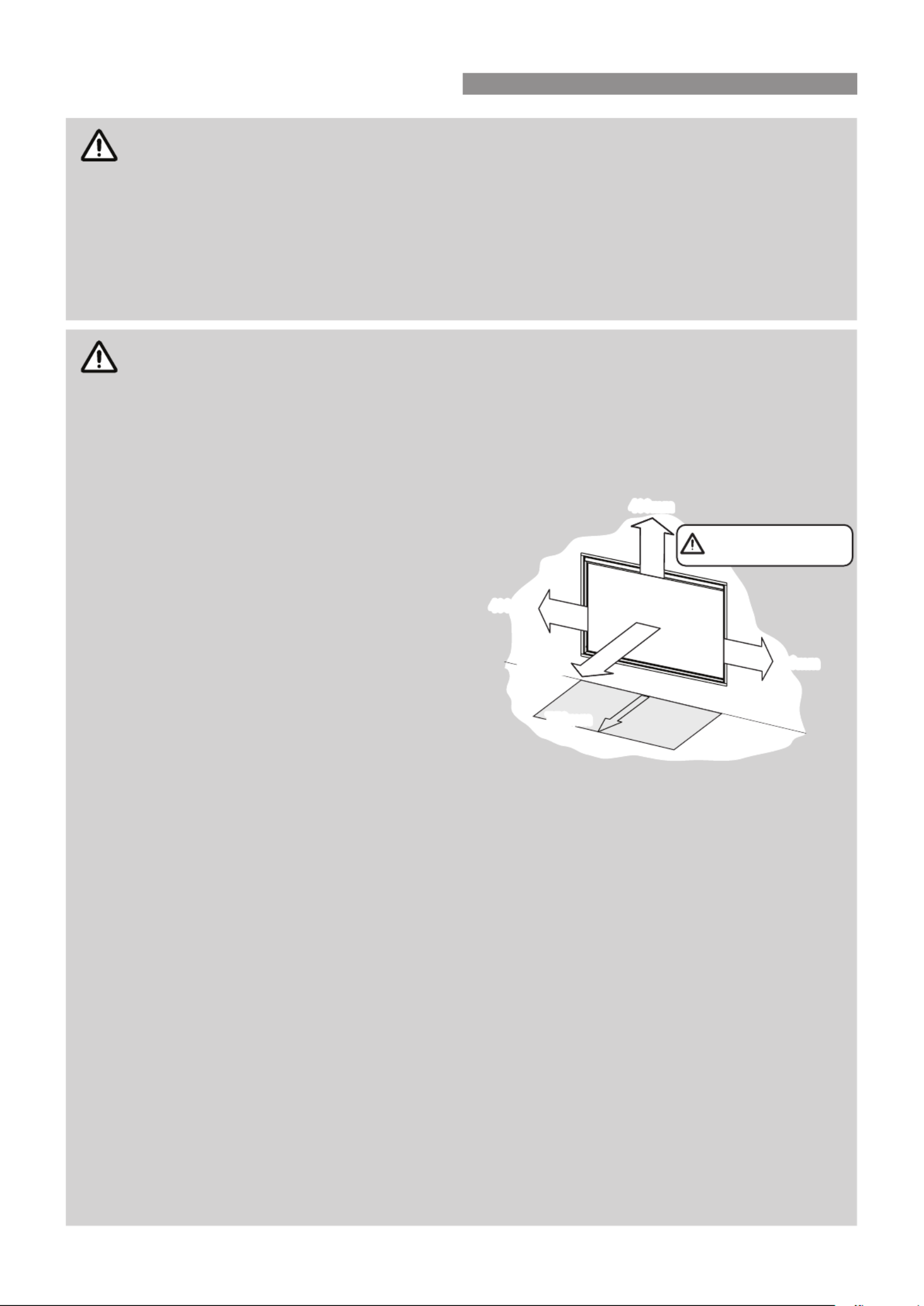
Rinnai 6 RHFE0800F_1000_1500 IM
WARNING
MODIFICATIONS.
DO NOT MODIFY THIS APPLIANCE, modifying from original specications may create a
dangerous situation and will void your warranty. Failure to comply with these instructions could
result in a re or explosion, which could cause serious injury, death or property damage.
DO NOT modify the electrical wiring of this appliance.
If the power cord is damaged or deteriorated then it be replaced by an authorised person. MUST
Failure to do so may result in electric shock, re, serious injury or product failure.
Improper installation, adjustments, service or maintenance can cause serious injury, death or
property damage. Such work MUST ONLY be performed by an authorised person.
WARNING
GENERAL SAFETY WARNINGS
This appliance is HEAVY, during installation the use of a mechanical lifting aid is recommended,
noting that improper lifting may result in serious injury.
WARNING MUST: This heater NOT be used if any of the glass panels are damaged.
Flue terminal always vent directly to outdoors. MUST DO NOT extend the ue vertically or
horizontally in ways other than prescribed in this appliance manufacturer’s installation
instructions. ONLY the ue components specied by Rinnai must be used.
When considering installation ensure
minimum clearances as follows are adhered
to, refer Fig. 1.
Heat radiating from the front of this heater
may over time aect the appearance of
some materials used for ooring such as
carpet, vinyl, cork or timber. This eect may
be amplied if the air in the room contains
cooking vapours, candle vapours and
cigarette smoke, etc. To avoid this possibility,
it is recommended that a mat or similar
protective sheet be placed in front of the
appliance, extending at least 750 mm in front
of the dress guard. Refer to the installation
manual for mantle clearances, additional
installation information and warnings.
This appliance be installed where curtains or other combustible materials could MUST NOT
come into contact with it. In some cases curtains may need restraining.
This appliance is intended for use by persons (including children) with reduced physical, NOT
sensory or mental capabilities or lack of experience and knowledge, unless they have been given
supervision or instruction concerning use of the appliance by a person responsible for their
safety.
The appliance is NOT intended for use by young children or inrm persons without supervision.
Young children and the inrm SHOULD be supervised at all times when in the vicinity of this
heater while it is in operation.
The heater be located immediately below a power socket outlet.MUST NOT
A dedicated 230 V earthed 10 Amp power point must be used with this appliance.
Suitable ONLY for indoor installation.
DO NOT operate this appliance before leak checking hoses and gas cylinder connection.
NOT to be connected to an LP gas cylinder located indoors.
Please keep this instruction booklet in a safe place for future reference. All dimensions referred
to in these instructions are in millimetres, unless otherwise specied.
DO NOT SPRAY AEROSOLS IN THE VICINITY OF THIS APPLIANCE.
DO NOT USE OR STORE FLAMMABLE MATERIALS IN OR NEAR THIS APPLIANCE.
DO NOT PLACE ARTICLES ON OR NEAR THIS APPLIANCE.
Note that side and vertical
clearances are measured
from the edge of the glass.
400mm
400mm
400mm
750mm
1000mm
400mm
Fig .1
400mm
400mm
750mm
1000mm
WARNINGS & IMPORTANT INFORMATION
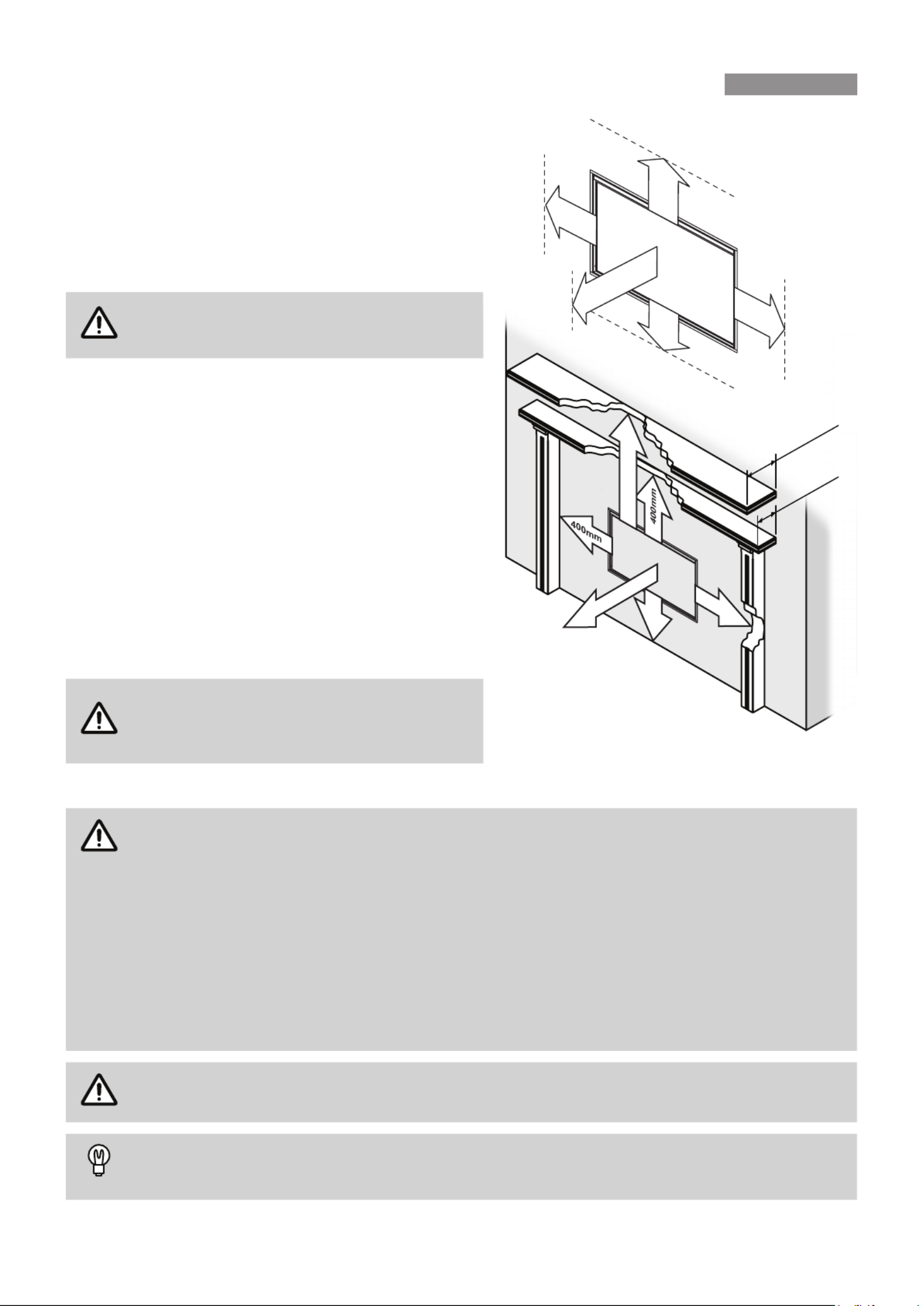
Rinnai 8 RHFE0800F_1000_1500 IM
LOCATION
When positioning the heater, the main variables governing
the location are Flueing and Warm Air Distribution.
This heater MUST NOT be installed where curtains or
other combustible materials could come into contact with
it. In some cases curtains may need restraining. Refer to
"General Safety Warnings" on page 6 for additional
safety considerations.
IMPORTANT
Horizontal and vertical clearances are
measured from the edge of the burner box
glass.
Combustible mantles and surrounds can be added to
compliment the design provided that they conform to the
following clearances requirements.
The minimum clearance from the edge of the burner box
glass is 400 mm. The depth of the mantle or surround (A)
at this minimum clearance may not exceed 250 mm.
An additional 100 mm of clearance is required for every
extra 50 mm of mantle depth. The depth of the mantle
or surround ( ) at 500 mm of clearance may not exceed B
300 mm.
Refer to the section "Wall Lining Installation" starting on
page 27 for additional information.
Refer "Cavity Ventilation" on page 9 for cavity ventilation
details.
NOTE
Combustion product spillage testing must be
conducted during appliance commissioning.
This testing may show a need for additional
xed ventilation.
TV & ORNAMENTATION WARNING
CAUTION
INSTALLATION OF TV OR ORNAMENTATION ABOVE THE HEATER
The installation of electrical appliances above and in the vicinity of the heater such as, but
not limited to, Plasma TV, LCD TV, Home Theatre Screens, Speakers, etc must comply with
their manufacturers' instructions. It is the responsibility of the installer/end-user to check the
installation instructions of these items and to ensure the location is suitable.
This caution also extends to, but is not limited to, ornaments such as: Paintings, Prints,
Photographs, Tapestries, Mirrors, Stued Animals, etc.
Please note the recommended clearances as per the diagram above. The temperature of the wall
surface directly above the appliance may be elevated and may discolour paint nishes or distort
vinyl wall coverings. For durability of surfaces you should contact the relevant manufacturer for
their specication.
WARNING
RINNAI DOES NOT TAKE ANY RESPONSIBILITY FOR ANY DAMAGE OCCURRING TO
ANY ITEMS INSTALLED ABOVE AND IN THE VICINITY OF THE HEATER.
IDEA
Use either a shelf or mantle below the TV or ornament or alternately you can construct a recess
to mount TV or ornament in. Check the manufacturers installation instructions for these items
and ensure the recess is suitable.
400mm
257mm
1000mm
500mm
A = 250mm
B = 300mm
400mm 400mm
400mm
257mm
1000mm
GENERAL INSTALLATION INFORMATION
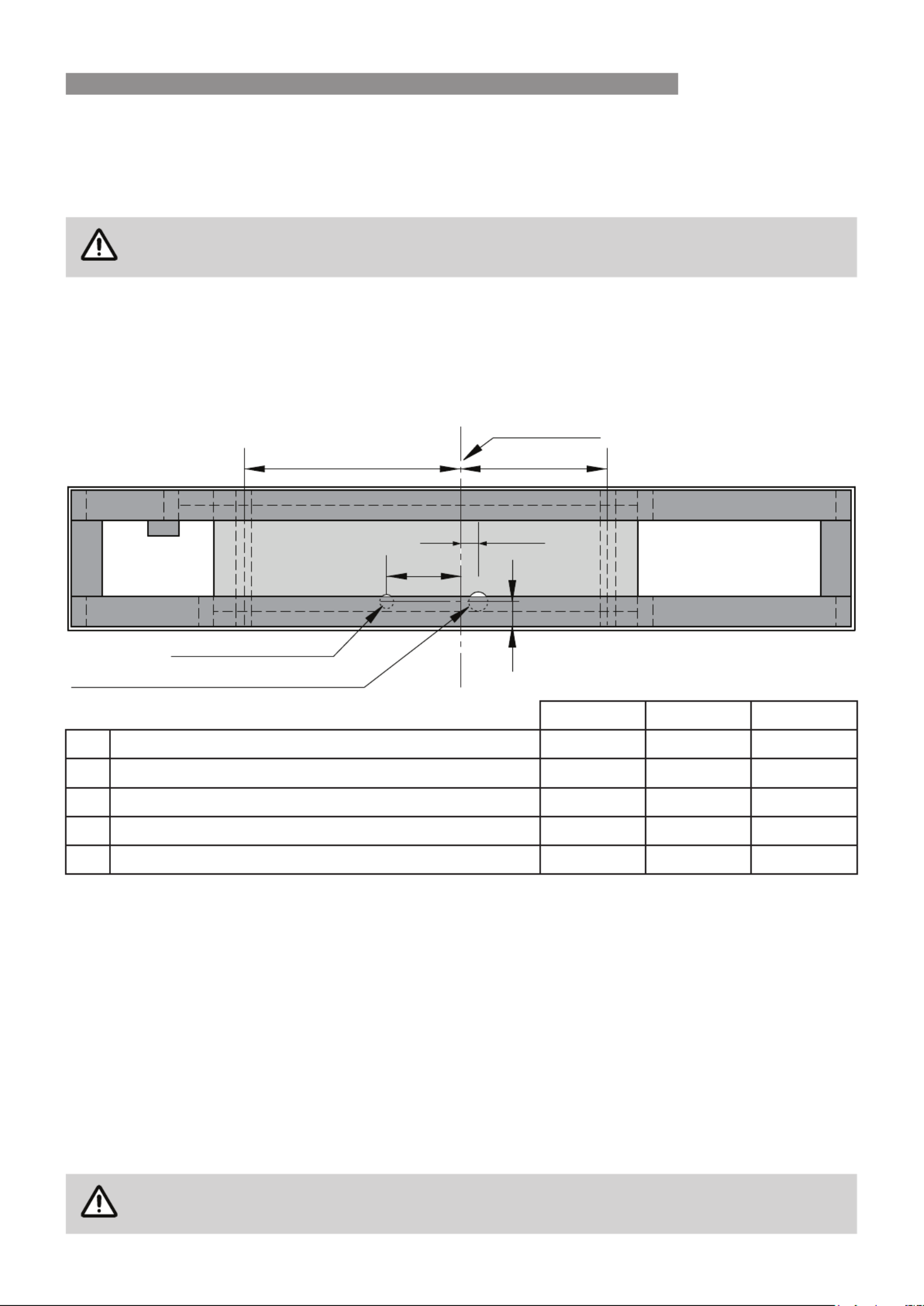
Rinnai 9 RHFE0800F_1000_1500 IM
FRAMING DIMENSIONS
Framework of the installation must conform to local building codes. Non-combustible materials need not be used.
If the appliance is elevated from the ground within the structure, a base must be constructed using suitable material
with supporting joists capable of supporting a minimum of 1.5 times the weight of the appliance.
CAUTION
AS/NZS 5601 “GAS INSTALLATIONS” requires that ue components be supported independently
of the appliance.
For the following framing dimensions it is important to be aware that the studs are oset—the cavity needs to be
framed based on the centreline of the glass, not the opening size.
Base Board and Cut-outs
To ensure everything lines up and ts properly, it is recommended that on the base the following dimensions are
pencilled; glass centreline, unit depth centreline, feet position, gas and room thermistor cut-outs.
* Assumes 10mm plasterboard / All dimensions in mm RHFE0800F RHFE1000 RHFE1500
A Thermistor / ambient air access - right glass of centreline 50 50 225
B Gas supply access - left of glass centreline 220 220 220
C Support feet centres - left of glass centreline 640 740 990
D Support feet centres - right glass of centreline 360 460 710
E Gas supply / thermistor access - from front of enclosure* 77 77 77
CAVITY VENTILATION
Ventilation of at least 2000 mm² is required in the cavity ideally below the base of the heater engine. This is to
provide room air at ambient room temperature to the re thermistor located in the base of the heater engine.
Ventilation can be via a vent or an open toe kick at the base of the cavity, however it MUST be in the same room
and wall cavity as the heater.
Additionally the top of the cavity needs to be ventilated into the room or another space. This ventilation opening
MUST be at least 2000 mm². This opening is to prevent heat build-up within the cavity, which if left unventilated
could potentially cause damage to wall surfaces or coverings and / or cause the appliance to cut out.
ADDITIONAL FRAMING NOTES
Plaster board is set 1 mm back from the front edge of the frame to allow for a slim edge plaster nish.
To ensure the appliance performs correctly, without rattling, the heater engine MUST be installed on a at level
support base.
IMPORTANT
Issues caused by rattling res not installed on a at level base, as detailed in this guide, will NOT
be covered by warranty.
E
A
B
Gas supply access
Thermistor / ambient air access Ø 40 mm
Glass centreline
Dimension
E
assumes 10 mm plaster board
Drawing is for a top down view
C D
FRAMING
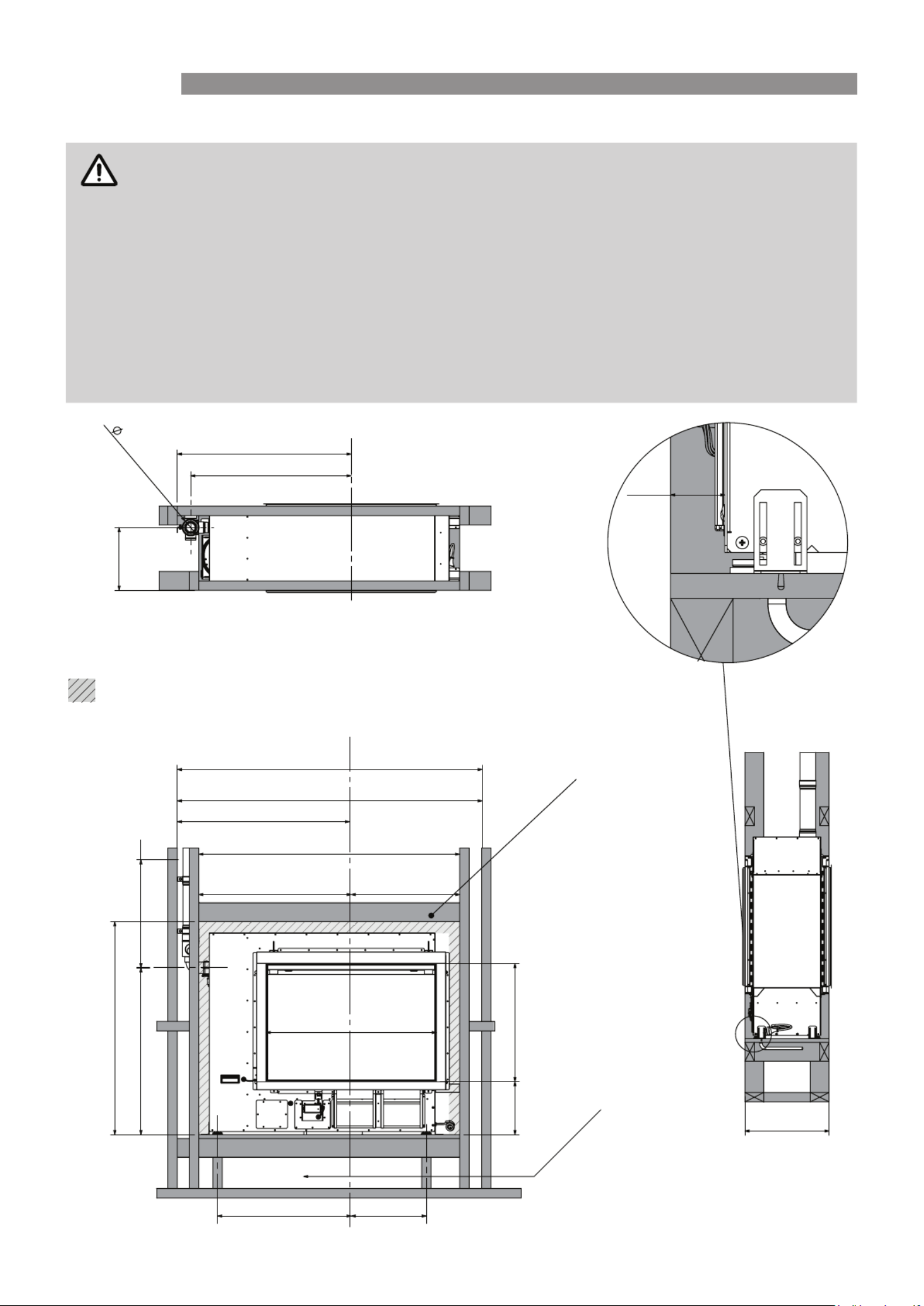
Rinnai 10 RHFE0800F_1000_1500 IM
FRAMING FOR RHFE0800F
IMPORTANT
To prevent the transfer of heat from the heater engine to surfaces (including to surfaces of non-
combustible materials), a minimum 50 mm clearance be maintained. Failure to provide this MUST
clearance (especially at the non ue connection end of the heater engine) may cause permanent
heat damage to adjacent wall materials.
All dimensions are assuming a 10 mm plaster board.
Studs and joists are required directly below the support feet of the appliance.
Framing shown is 90 x 45 mm and the re platform shown is 18 mm plywood.
Allow room underneath the appliance for the gas supply to enter the re cavity (min. 100 mm).
The framing dimensions have the studs oset. This is because the cavity needs to be framed
based on the centreline of the Linear glass, the opening size.NOT
Where there is a requirement for a symmetrical installation, the cavity size will need to increase,
refer to the diagram below.
520 Min 730 Min
1250 min.
1020 Min
~800
640 360
500 **
816 *
300
770
845
80**
39 mm assumes
10 mm wallboard
403 mm assumes a 10 mm wallboard
on both sides of a double-sided unit.
415 mm is the min. for a single-sided
unit to maintain 50 mm clearance to
the back of the fire.
Glass centreline
Glass centreline
39
566 *
257 ±5 *
1365 min.
1690 (for symmetrical cavity)
845 min.
Min. 100 mm
underneath to allow
for gas supply to
enter cavity
403
Recommended that lintel is left
until heater engine is installed so
minimum clearances can be
maintained
*** For symmetrical cavities, make this dimension the same as the left hand dimension (730mm)
** Maintain 25 mm clearance to combustibles for first 500mm of flue
* Plaster board cutout for finishing trim
Shaded area is the clearance required around the heater engine ( ). On the non Min. 50 mm
flue end of the heater enginge this is automatically achieved with the carry bar.
FRAMING
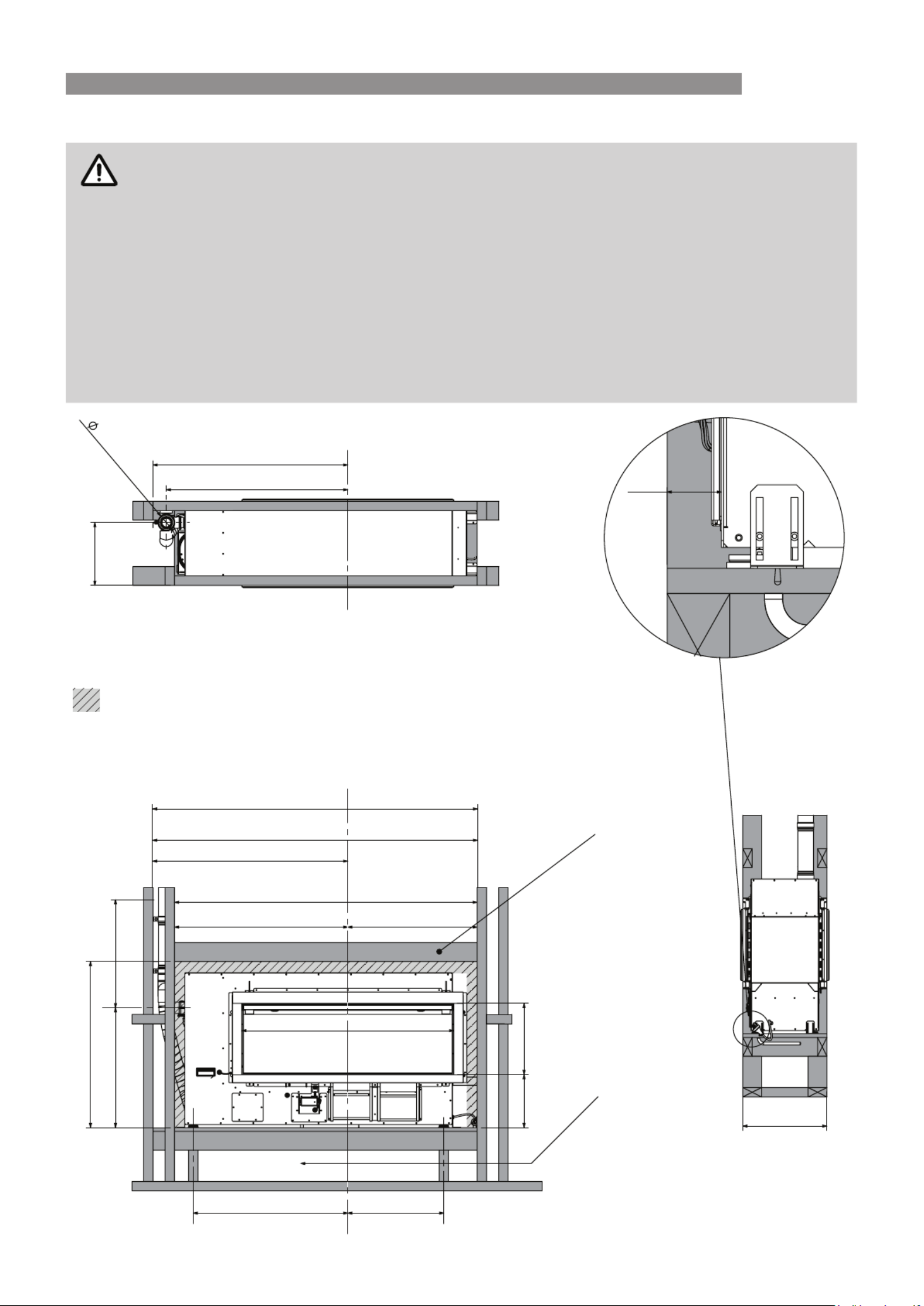
Rinnai 11 RHFE0800F_1000_1500 IM
FRAMING FOR RHFE1000
IMPORTANT
To prevent the transfer of heat from the heater engine to surfaces (including to surfaces of non-
combustible materials), a minimum 50 mm clearance be maintained. Failure to provide this MUST
clearance (especially at the non ue connection end of the heater engine) may cause permanent
heat damage to adjacent wall materials.
All dimensions are assuming a 10 mm plaster board.
Studs and joists are required directly below the support feet of the appliance.
Framing shown is 90 x 45 mm and the re platform shown is 18 mm plywood.
Allow room underneath the appliance for the gas supply to enter the re cavity (min. 100 mm).
The framing dimensions have the studs oset. This is because the cavity needs to be framed
based on the centreline of the Linear glass, the opening size.NOT
Where there is a requirement for a symmetrical installation, the cavity size will need to increase,
refer to the diagram below.
1450 min.
796 Min
341 *
257 ±5 *
1016 *
500 **
~ 575
620 *** 830
740 460
300
80**
870
945
403
39 mm assumes
10 mm wallboard
39
403 mm assumes a 10 mm wallboard
on both sides of a double-sided unit.
415 mm is the min. for a single-sided
unit to maintain 50 mm clearance to
the back of the fire.
Glass centreline
Glass centreline
1565 min.
1890 (for symmetrical cavity)
945 min.
Min. 100 mm
underneath to allow
for gas supply to
enter cavity
Recommended that lintel is left
until heater engine is installed so
minimum clearances can be
maintained
*** For symmetrical cavities, make this dimension the same as the left hand dimension (830mm)
** Maintain 25 mm clearance to combustibles for first 500mm of flue
* Plaster board cutout for finishing trim
Shaded area is the clearance required around the heater engine ( ). On the non Min. 50 mm
flue end of the heater enginge this is automatically achieved with the carry bar.
FRAMING
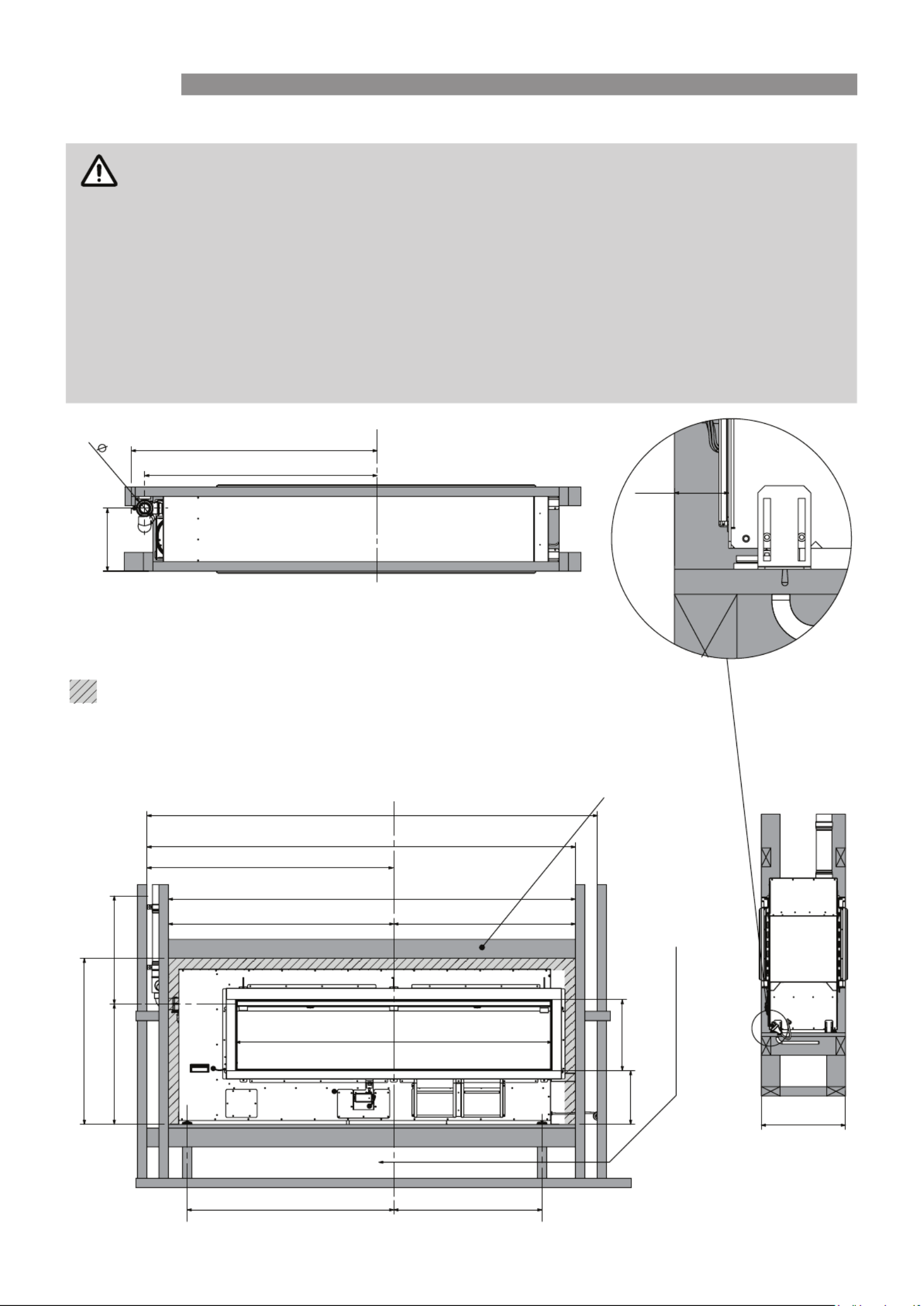
Rinnai 12 RHFE0800F_1000_1500 IM
FRAMING FOR RHFE1500
IMPORTANT
To prevent the transfer of heat from the heater engine to surfaces (including to surfaces of non-
combustible materials), a minimum 50 mm clearance be maintained. Failure to provide this MUST
clearance (especially at the non ue connection end of the heater engine) may cause permanent
heat damage to adjacent wall materials.
All dimensions are assuming a 10 mm plaster board.
Studs and joists are required directly below the support feet of the appliance.
Framing shown is 90 x 45 mm and the re platform shown is 18 mm plywood.
Allow room underneath the appliance for the gas supply to enter the re cavity (min. 100 mm).
The framing dimensions have the studs oset. This is because the cavity needs to be framed
based on the centreline of the Linear glass, the opening size.NOT
Where there is a requirement for a symmetrical installation, the cavity size will need to increase,
refer to the diagram below.
1950 min.
796 Min
341 *
257 ±5 *
1516 *
500 **
~ 575
870 Min ***
1080 Min
990 710
300
80**
1120
1195
*** For symmetrical cavities, make this dimension the same as the left hand dimension (1080mm)
** Maintain 25 mm clearance to combustibles for first 500mm of flue
* Plaster board cutout for finishing trim
Shaded area is the clearance required around the heater engine ( ). On the non Min. 50 mm
flue end of the heater enginge this is automatically achieved with the carry bar.
403 mm assumes a 10 mm wallboard
on both sides of a double-sided unit.
415 mm is the min. for a single-sided
unit to maintain 50 mm clearance to
the back of the fire.
Glass centreline
2065 min.
2390 (for symmetrical cavity)
1195 min.
Glass centreline
403
Min. 100 mm
underneath to allow
for gas supply to
enter cavity
Recommended that lintel is left
until heater engine is installed so
minimum clearances can be
maintained
39 mm assumes
10 mm wallboard
39
FRAMING
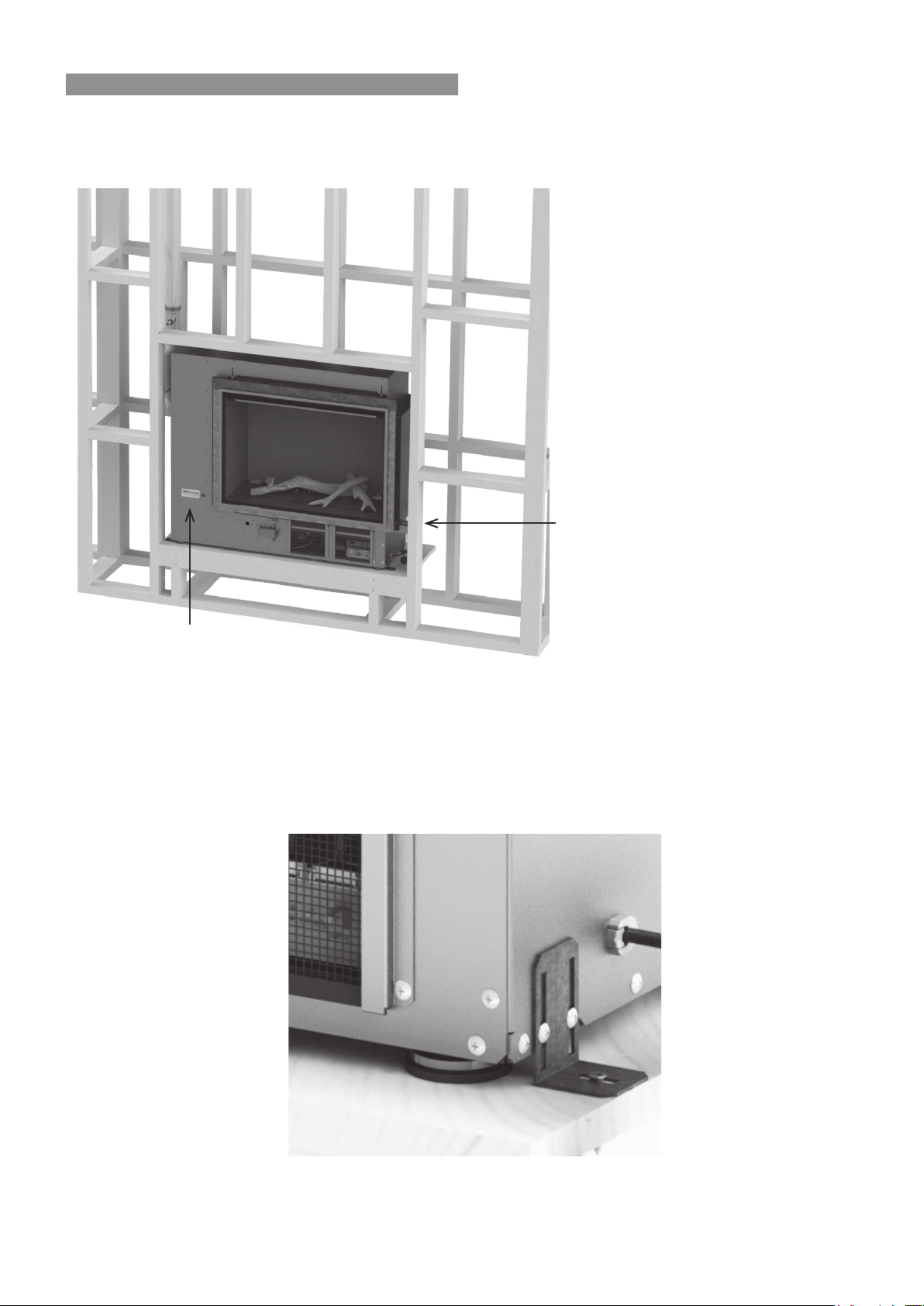
Rinnai 13 RHFE0800F_1000_1500 IM
INSTALLING ENGINE INTO CAVITY
Using the handholds (white slots on the left hand end and carry bars on the right hand end), carefully lift and slide
the heater engine into the enclosure and position in place.
Adjustable Feet
Use the feet on all corners of the unit to adjust the re so that it is level. The feet are adjustable. Having the unit
level is critical to the installation, so the wall lining can be installed ush with the frame edge of the appliance.
Seismic Brackets
In areas where seismic activity can be expected. Secure the heater engine to the bottom of the cavity using the
four seismic brackets.
To level the unit and not aect where the feet go, the seismic brackets need to be elevated before the unit is
installed into the cavity
Hand hold
Carry bar position, two carry bars
SUPPLY CONNECTIONS
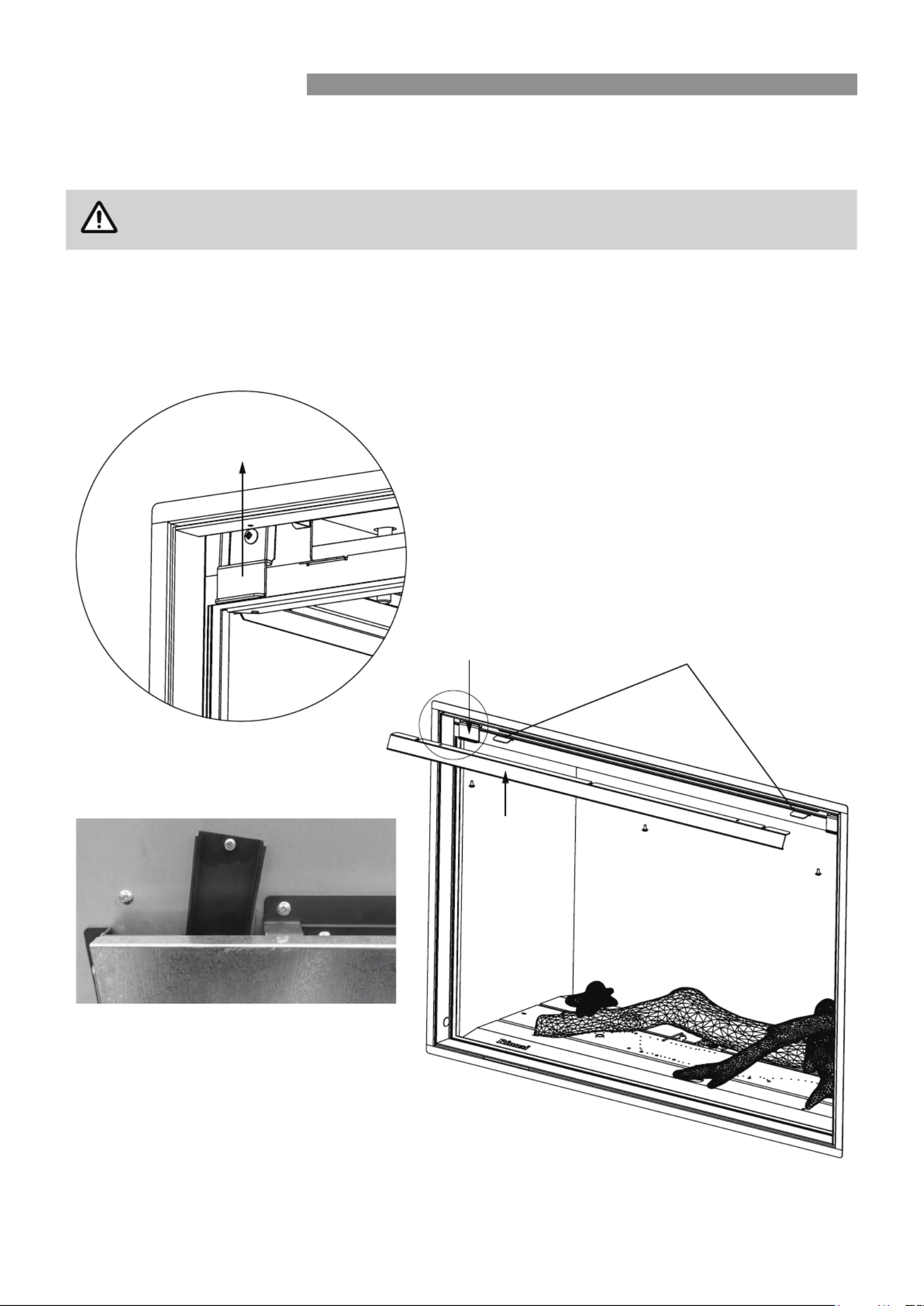
Rinnai 14 RHFE0800F_1000_1500 IM
REMOVING THE BURNER BOX GLASS
The glass front sits in a narrow channel at the bottom of the re and is held in place by glass retainer latches
positioned at the top, either side of the unit (the 1500 model has an extra glass retainer latch in the centre).
IMPORTANT
Take care when lifting the glass from the engine noting the glass for the RHFE1500 weighs
approximately 7 kg.
Removal Procedure:
Using a screwdriver, loosen the three screws holding the louvre in place, remove the louvre, and then remove the
screws (so the glass can come out) and put the louvre to one side.
1. Push the top glass retainer latches up and slightly to one side to release the top section of the glass. These
will stay in the upright position if moved slightly to one side
2. Using the frame tabs at the top of the glass frame, lift up and gently slide to the right and rotate the glass until
the left section comes free, then move the glass panel to the left to remove the right section.
Glass retainer latch
Louvre
Glass frame tabs
Push up the latch and to the
side to release the glass
SUPPLY CONNECTIONS
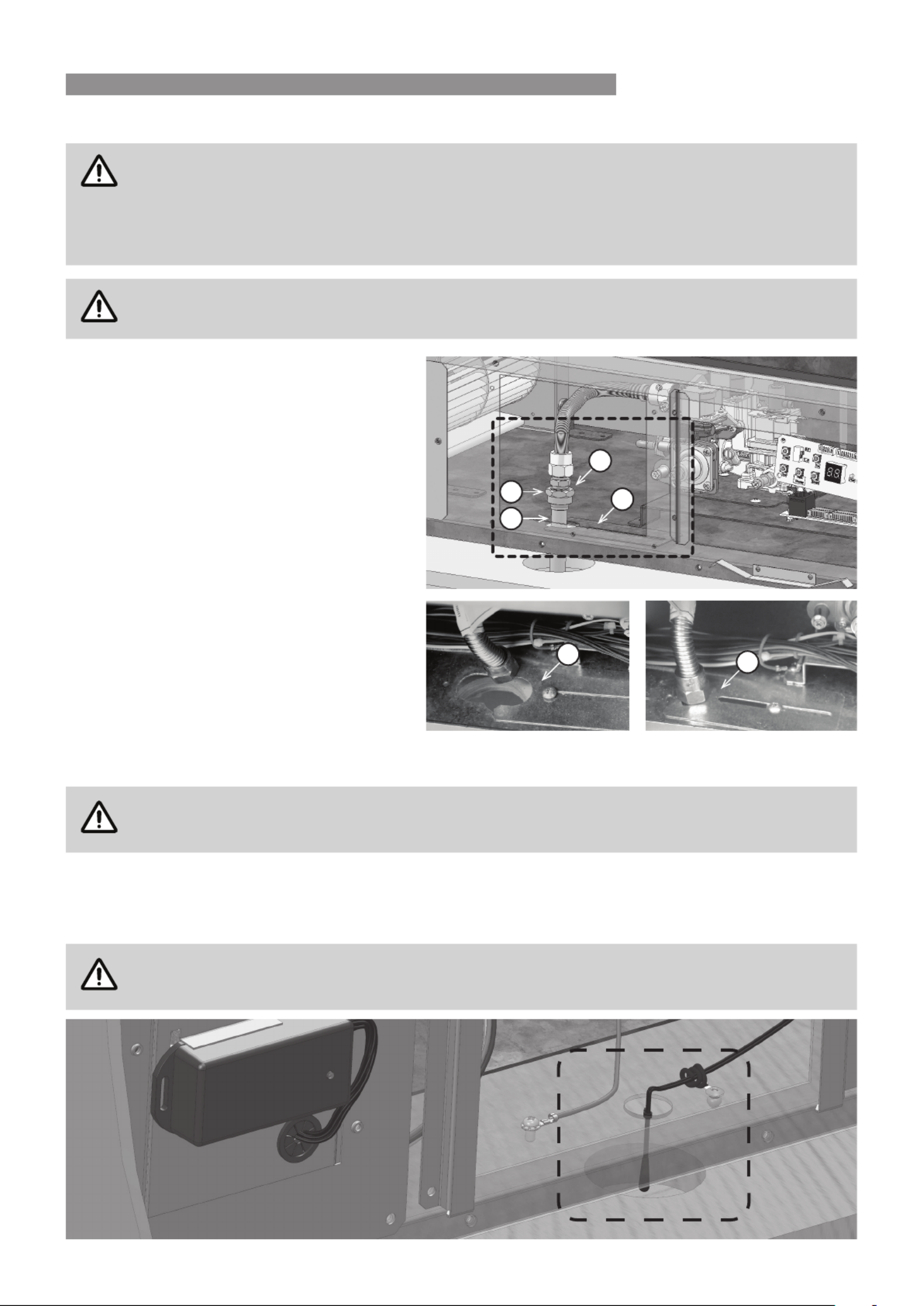
Rinnai 15 RHFE0800F_1000_1500 IM
GAS SUPPLY
WARNING
Gas pipe sizing must consider the gas input to this appliance as well as all other gas appliances
in the premises. The gas meter and regulator must be specied for the total gas rate.
A suitable sizing chart such as the one in AS/NZS 5601 should be used.
The use of rubber hose for any gas connection to a xed appliance is NOT authorised by the
manufacturer.
IMPORTANT
Conrm correct gas type (see labels located on top or rear panels). Refer to local gas authority
for conrmation of gas type if you are in doubt.
Installation of Consumer Piping
The gas supply (consumer piping), termination is
inside the heater and enters through the base of
the appliance.
A ½” BSP ared nut (A) and a ½” BSP Male Flare
x ½” Barrel Union ( ) are provided for connection B
to the consumer piping ( ). They are shipped C
inside the engine attached to on the gas inlet
connection of the heater.
Once the gas connection is made lock the sliding
plate ( ) in place to stop the connection rattling, D
refer to the images right.
Purging Gas Supply
Foreign materials and debris such as swarf,
lings, etc. MUST be purged / removed from the
gas supply, failure to do so may cause damage
to the gas control valve causing it to malfunction.
Leak Testing the Connection
Plug the end of the consumer piping gas and leak test all joints.
CAUTION
Use a soapy solution to test all gas connections. If a leak is present bubbles will form at the leak
point. When nished remove any residue with a rag. Prevent any soapy solution from coming in
contact with electrical components.
ROOM THERMISTOR
Once installed the room temperature thermistor should be set so the bulb on the end is outside of the re box and
into an area where room air will be drawn over it from the lower room ventilation, refer to the image below.
IMPORTANT
The room temperature thermistor is provided with a 1.5 metre lead and is to be positioned so that
it is in the air ow of the cavity ventilation. It may be mounted directly to the inside of an air vent
grill. The thermistor be accessible for servicing after the wall linings have been installed.MUST
B
C
A
DD
D
SUPPLY CONNECTIONS
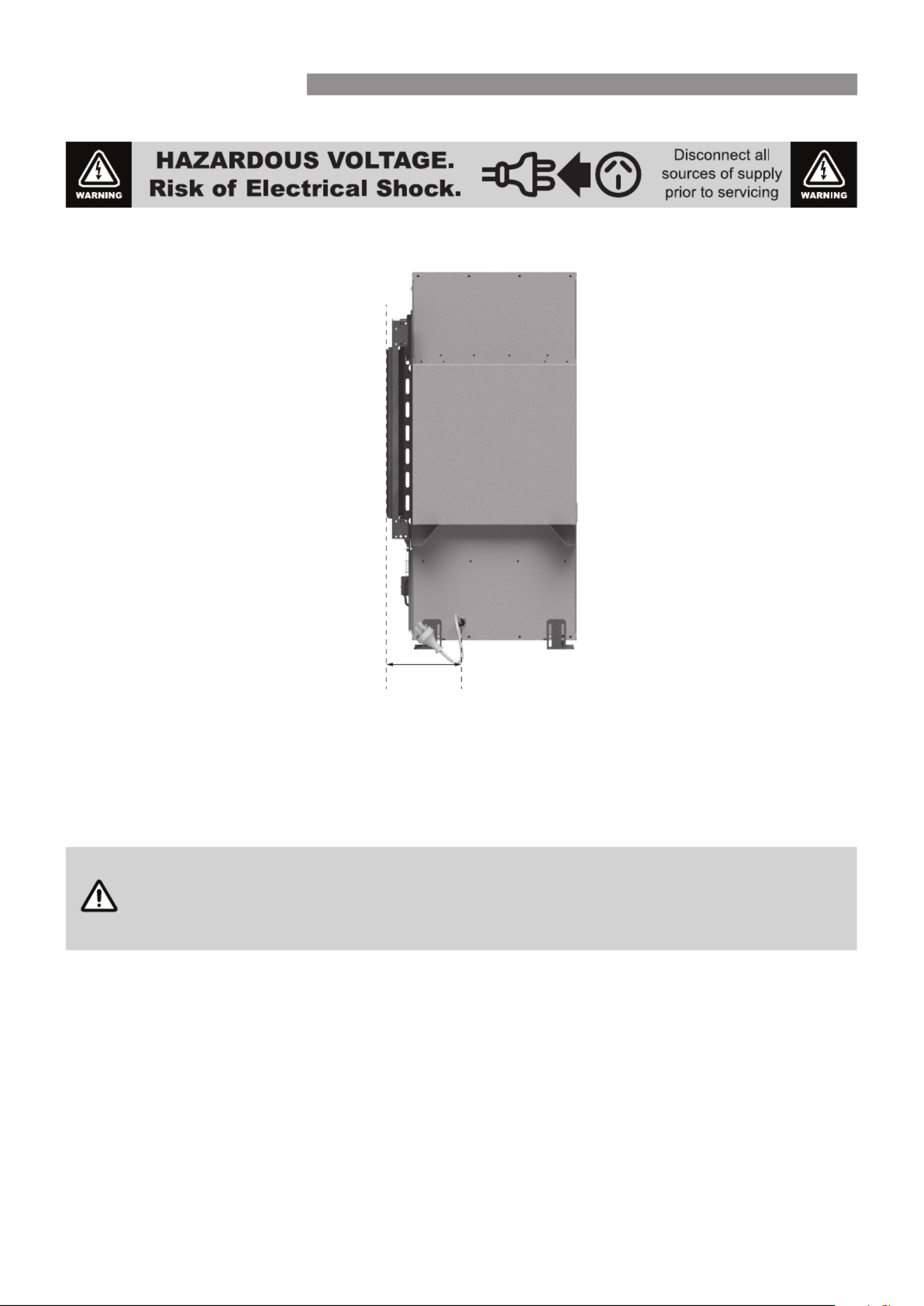
Rinnai 16 RHFE0800F_1000_1500 IM
ELECTRICAL SUPPLY
This heater has a 1.5 m power cord with a three pin plug supplied. The power cord passes through a slot in the
front right hand side of the appliance, approximately 140 mm from the front of the unit.
If a power point is used it be 230 V, rated at 10A and be earthed.MUST MUST
This power point MUST NOT be located above the heater and a switch provided to electrically isolate the
appliance for servicing.
Direct Wired Installations
Alternatively the appliance can be direct wired to conceal the power supply.
IMPORTANT
A qualied electrician will need to be consulted where a direct wired installation is required.
A switch is to be provided to electrically isolate the appliance for servicing.
Any such installation must comply with the requirements of AS/NZS 5601, AS/NZS 3000 and any
other relevant local regulations.
approx.
140 mm
SUPPLY CONNECTIONS
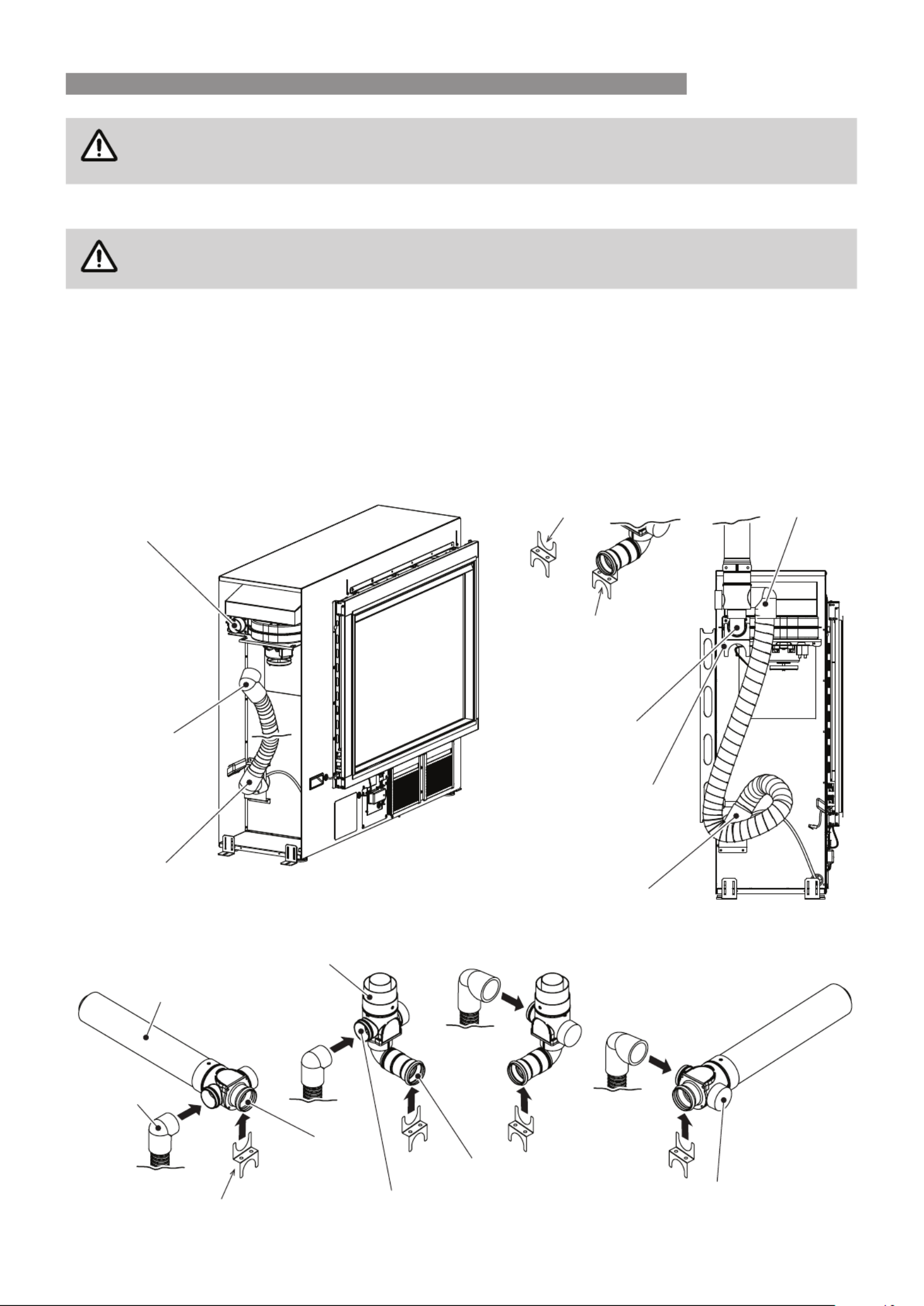
Rinnai 17 RHFE0800F_1000_1500 IM
IMPORTANT
The following information is provided as a basic overview of the ue system requirements. Refer
to the LS - Gas Fireplace, Flue Installation Manual which is provided with ue transition
components for comprehensive details regrading the installation of the ue system .
FLUE EXHAUST & AIR INLET CONNECTIONS
WARNING
The following steps in the installation are critical. If the connections are not secured correctly,
then products of combustion could disperse into the room being heated.
1. Connect the ue terminal exhaust connection to the ue exhaust outlet, and secure in place (two screws) with
the ue locking bracket (supplied in the accessories plastic bag with the remote control).
2. Secure the ue transition to the framing using a wall clip (supplied with LSFKIT01/02 or ASPDFK).
3. Attach the air intake hose to the large air inlet connection on the ue transition (LSFKIT01/02 or ASPDFK)
and secure in place with the supplied cable tie (also supplied), noting that the other end of the air inlet hose
is already pre-installed to the appliance.
4. Ensure that the rubber cap remains secured in place on the unused (small) air inlet connection.
Air inlet hose
(This end is supplied
pre-fitted to the appliance)
Air inlet hose
(This end is supplied pre-fitted to the appliance)
Flue exhaust outlet
Flue exhaust
locking bracket
Flue exhaust
connection
Flue exhaust
locking bracket
(shown installed)
Flue exhaust
connection
Small air inlet connection
Large air inlet
connection
LSFDFK01
LSFKIT01/02
(Extension piece not shown)
Air inlet hose
Flue exhaust
connection
(Rubber cap remain in place)MUST
Air inlet hose
(shown installed)
Flue exhaust
locking bracket
Flue exhaust
locking bracket
(shown installed)
Air inlet hose
(This end is to be
fitted to LSFKIT01/02
or LSFDFK01)
FLUEING
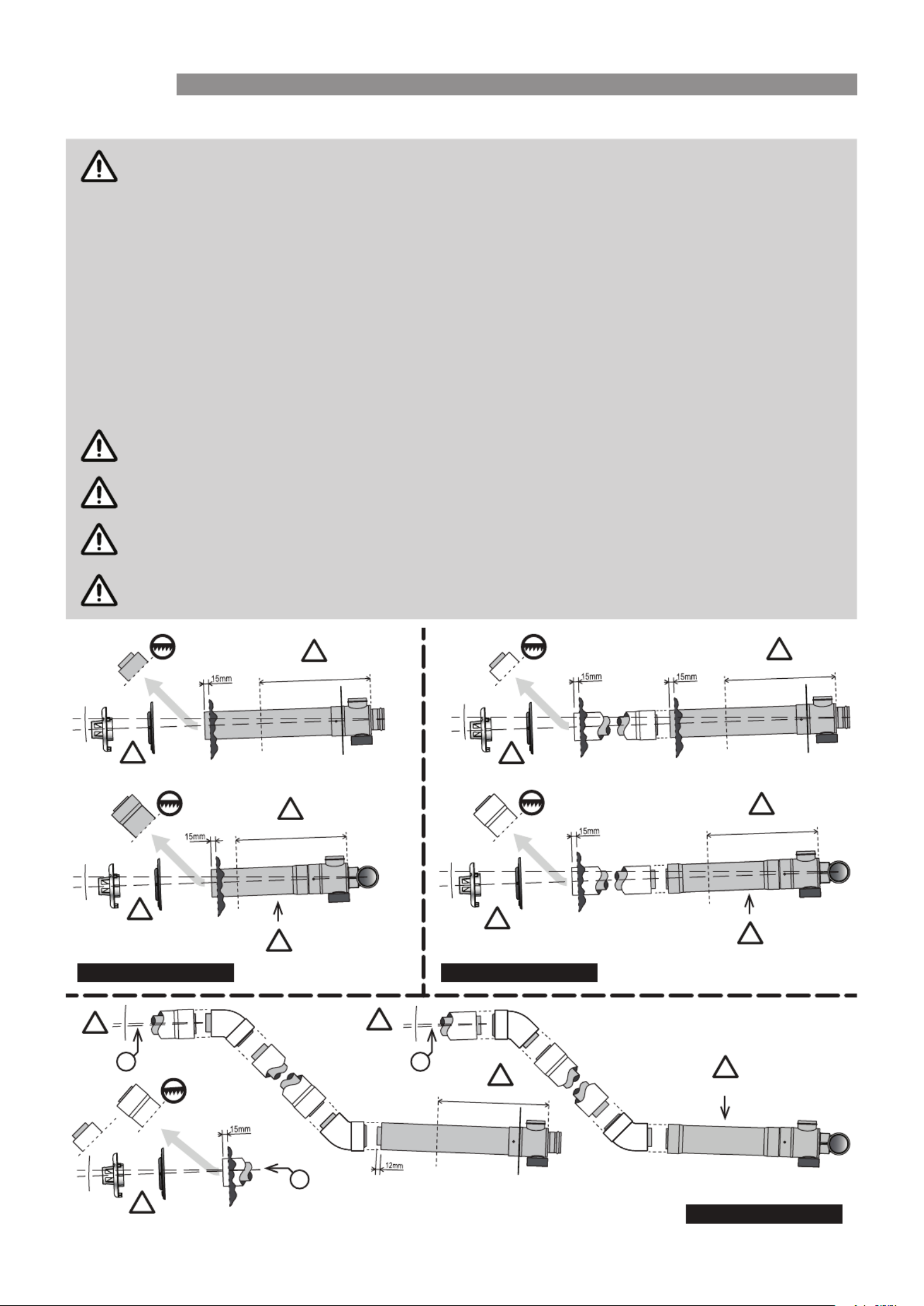
Rinnai 18 RHFE0800F_1000_1500 IM
INSTALLATION CONFIGURATION WARNINGS
WARNING
ONLY the Rinnai ue system components specied in this reference manual MUST be used.
Components NOT specied in these manuals, whether manufactured by Rinnai or otherwise, are
NOT compatible and MUST NOT be used! Rinnai appliance warranty conditions may be voided if
non Rinnai ue components are tted.
Use ONLY the supplied silicone grease when lubricating the O-rings.
ONLY MUSTan authorised person install, service and remove the Rinnai heater & ue system.
The maximum ue length is 8.5m (1) and the maximum number of 90° bends is 3 (2).
(1) For every 90 ° bend, the overall ue length MUST be reduced by 1m.
(2) The 90° bend of the ue transition piece is NOT counted as a 90 ° bend.
LS / Flametech series heaters combustion settings are factory set for "long ue", which is for ue
lengths that are 3 metres or greater. For ue lengths shorter than 3 metres it may be necessary to
change dip switch setting, refer to the commissioning instructions for full details.
NOTE
Note 1. When cutting the ue transition for joining to other components the minimum total
length be less than 300mm!MUST NOT
NOTE
Note 2. The all aluminium ue extension component MUST be tted at this point.
NOTE
Note 3. Where stipulated a Minimum 2° fall towards the terminal is required to ensure correct
drainage of condensation formed in the discharge ue.
NOTE
Note 4. Where stipulated a Minimum 2° fall towards the appliance is required to ensure correct
drainage of condensation formed in the discharge ue.
See Note 1.
!
Cut to correct
length & discard
See Note 3.
!
DIRECT DIRECT EXTENDED
OFFSET
LSFDFK01
LSFDFK01
See Note 1.
!
Cut to correct
length & discard
See Note 3.
!
See Note 2.
!
LSFKIT01
ESWTERM
See Note 1.
!
See Note 3.
!
Cut to correct
length & discard
LSFDFK01
ESPIPE900
See Note 2.
!
See Note 1.
!
Cut to correct
length & discard
LSFKIT01
ESPIPE900
ESWTERM
See Notes 1 & 4.
!
See Notes 2 & 4.
!
A A
Cut to correct
length & discard
See note 3.
!
A
See note 3.
!
See note 3.
!
LSFKIT01
See Note 3.
!
FLUEING
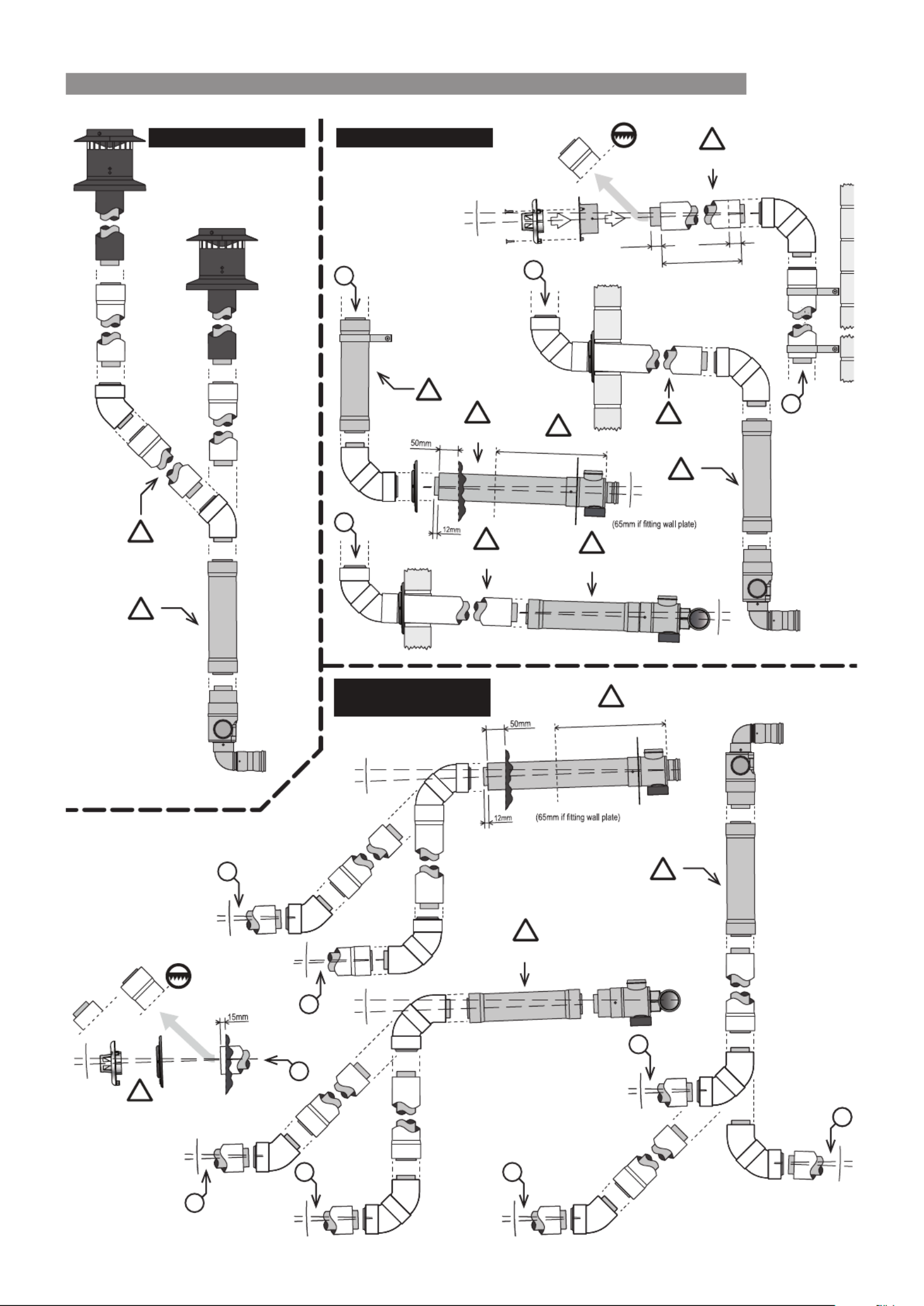
Rinnai 19 RHFE0800F_1000_1500 IM
27mm 31mm
Minimum 70mm
Cut to correct
length & discard
ESWTKIT2
(Flue Terminal, Terminal Adapter,
Wall Plate & Fixings)
VERTICAL ROOF
See Note 4.
!
See Notes 2 & 3.
!
B
B
B
See Notes 1 & 3.
!
*
*
B
B
B
B
B
See Note 3.
!
Cut to correct
length & discard
B
VERTICAL ON-WALL
DOWN & OUT / UNDER
UNDER FLOOR
See Note 2.
!
See Note 2.
!
C
See Note 2.
!
*
*
See Note 1.
!
See Note 2.
!
See Note 2.
!
C
C
C
See Note 4.
!
See Note 3.
!
See Note 4.
!
See Note 4.
!
LSFEXTKIT01
FLUEING
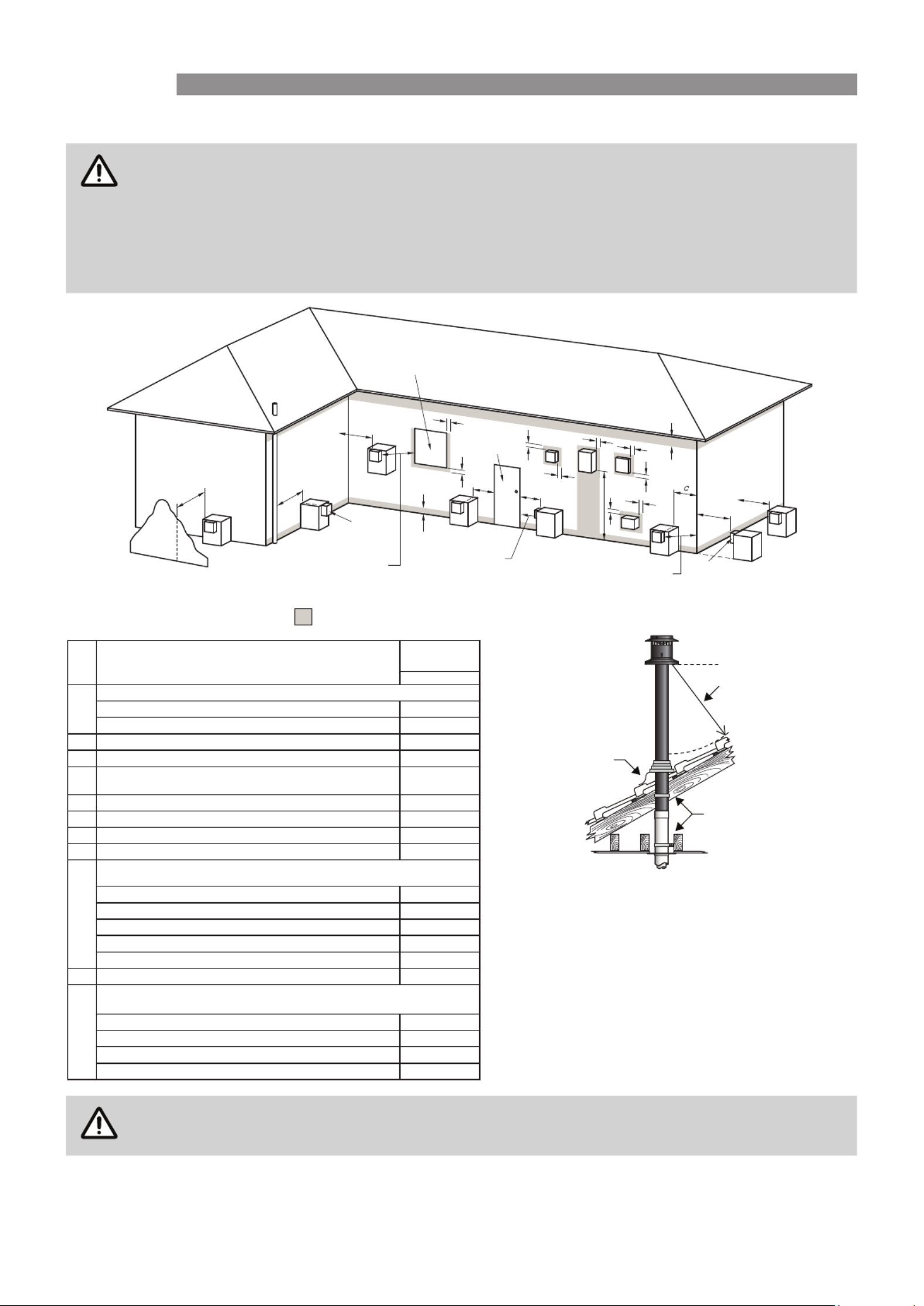
Rinnai 20 RHFE0800F_1000_1500 IM
FLUE TERMINAL LOCATION
WARNING
Ensure that the location of the ue terminal can comply with the requirements of AS/NZS 5601 -
Fig. 6.2 which is reproduced in part below.
AS/NZ 5601 was current at the time of printing but may have been superseded. It is the installer’s
responsibility to ensure that requirements of the current version of AS/NZS 5601 are met.
Refer to separately supplied Rinnai LS - Gas Fireplace - Flue Installation Manual for comprehensive
ue installation details.
1Where dimensions or cannot be achieved an equivalent horizontal distance c, j k
measured diagonally from the nearest discharge point of the terminal to the opening
may be deemed by the Technical Regulator to comply.
2 See Clause 6.9.4 for restrictions on a flue terminal under a covered area.
3 See Figure J3 for clearances required from a flue terminal to an LP Gas cylinder.
A is considered to be a source of ignition.flue terminal
4 For not addressed above acceptance should be obtained from the appliances
Technical Regulator.
FIGURE 6.2 (in-part) MINIMUM CLEARANCES REQUIRED FOR FAN-ASSISTED FLUE TERMINALS,
ROOM-SEALED APPLIANCE TERMINALS AND OPENINGS OF OUTDOOR APPLIANCES
* - unless is for closer installationappliance certified
NOTES:
† - Pr er .ohibited area below electricity met or fuse box extends to ground level
Sh ad i n in d i c a t e s p r o h it e d a r e a o u e r m l sg ib f r f l te in a
LE G EN D :
I = M e c h an i ca ai r in l etl
M = Ga s m e te r
P = El e ctr i c i t me o fu s boxy ter r e
S = St r u c etu r
T = Fl u e ter m lin a
Z = Fa n - ass i st e ap p l i an c e o yd n l
Di re n ofcti o
d i s r gc h a e
Se e N o t e 1 Se e N o t e 1
Op g toe n i n in
a i gbu ldin
T
T
T
T
T
T
T
C
M
d
d
e
e
h
j
j
j
n
b
f
a
h
P
Z
S
k
k
g
g
g
I
T
Door
Min. Clearances
(mm)
Fan Assisted
• up to 50 MJ/h inputAppliances 200
• over 50 MJ/h inputAppliances 300
300* ecafrus rehto ro ynoclab a evoba ,dnuorg eht morFb
300* renroc lanretxe ro llaw nruter a tnorFc
d
From a gas (M) (see 5.11.5.9 for vent terminal location of )meter regulator
(see Table 6.6 for New Zealand requirements) 1000
e From an electricity or (P) †meter fuse box 500
epip lios ro epip niard a morFf
g Horizontally from any building structure* = or obstruction facing a terminal 500
h From any other , c l, com sti air i ke †flue terminal ow or bu on nta 300
• up to 150 MJ/h input *Appliances 300
• over 150 MJ/h input up to 200 MJ/h input *Appliances 300
• over 200 MJ/h input up to 250 MJ/h input *Appliances 500
• over 250 MJ/h input *Appliances 1500
• All fan-assisted , in the direction of dischargeflue appliances 1500
1500rewolb aps a gnidulcni ,telni ria lacinahcem a morFk
150tupni rh/JM 05 ot pu sretaeh ecapS •
• Other up to 50 MJ/hr inputappliances 500
• over 50 MJ/h input and up to 150 MJ/h inputAppliances 1000
• over 150 MJ/h inputAppliances 1500
metI.feR
a
Below eaves, balconies and other projections:
n
j
Horizontally from an openable window, door, non-mechanical air inlet, or any other opening into a
building with the exception of sub-floor ventilation:
Vertically below an openable window, non-mechanical air inlet, or any other opening into a
building with the exception of sub-floor ventilation:
75
i
ii
iii
i Minimum clearance 500mm to nearest part of roof
ii Minimum clearance 25mm to any combustible materials
iii Decktite or lead collar flashing
WARNING
The ue terminal should be positioned away ammable materials.
FLUEING
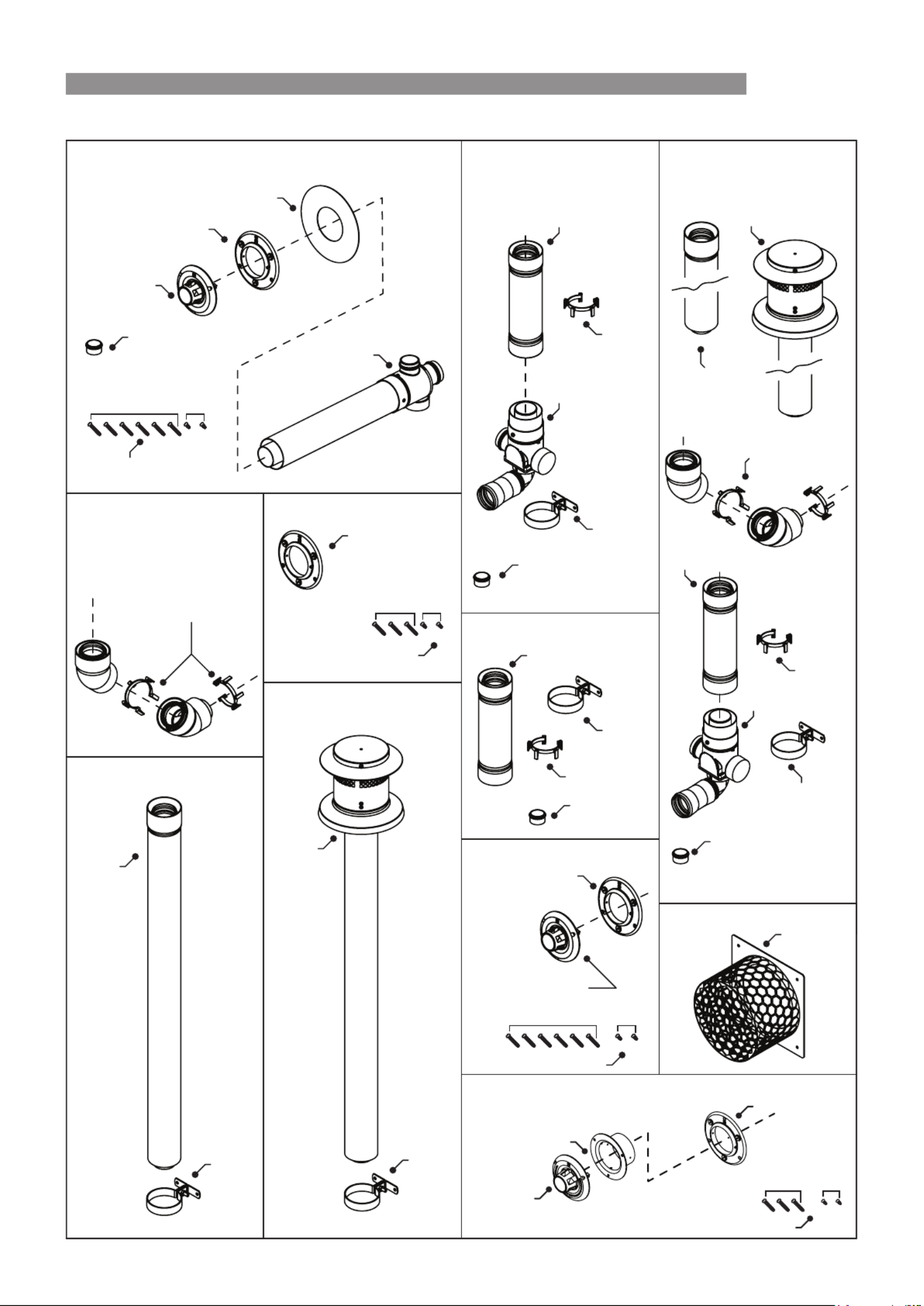
Rinnai 21 RHFE0800F_1000_1500 IM
FLUE COMPONENTS
Flue Transition
Transition Extension Pipe
ASPDFK2
(Direct Flue Kit for Rinnai Flamefires)
LSFKIT01
(Flue Adaption Kit)
LSFKIT02
(Extended Flue Adaption Kit)
Mounting/Securing Screws
Silicon Grease
ESROOFCOWL
Co-ax
Vertical
Terminal
Wall
Clip
Wall Clip
Silicon Grease
Internal Wall Plate
External Wall Plate
Flue Terminal
ESPLATE
External Wall Plate
Mounting/Securing Screws
ESWTERM
7mm
x2
22mm
x6
22mm
x3
7mm
x2
Flue Transition
ESPIPE900
Co-ax
Pipe
Wall
Clip
ESWTKIT2
(On-Wall Terminal Kit) External Wall Plate
Mounting/Securing Screws
Flue Terminal
M4 x 22mm
x3
8g x 10mm
x2
Terminal Adaptor
ESBEND
Co-ax Bends & Pipe Locating
Spacer x2
Co-ax Bends & Pipe
Locating Spacers x 2
Extension Pipe
Silicon Grease x2
Wall Clips p21-x5
BOTH spacers are
required for all offset
and extended offset
installations!
(This manual also included)
(This manual also included)
(This manual also included)
Mounting/Securing Screws
Flue Terminal
External Wall Plate
7mm
x2
22mm
x6
Spacer
Spacer
3x Co-ax Pipe
Co-ax Vertical Terminal
ESWFG
Flue Guard
LSFEXTKIT01
Spacer
Transition Extension Pipe
Wall Clip
Silicon Grease
Transition Extension Pipe
FLUEING
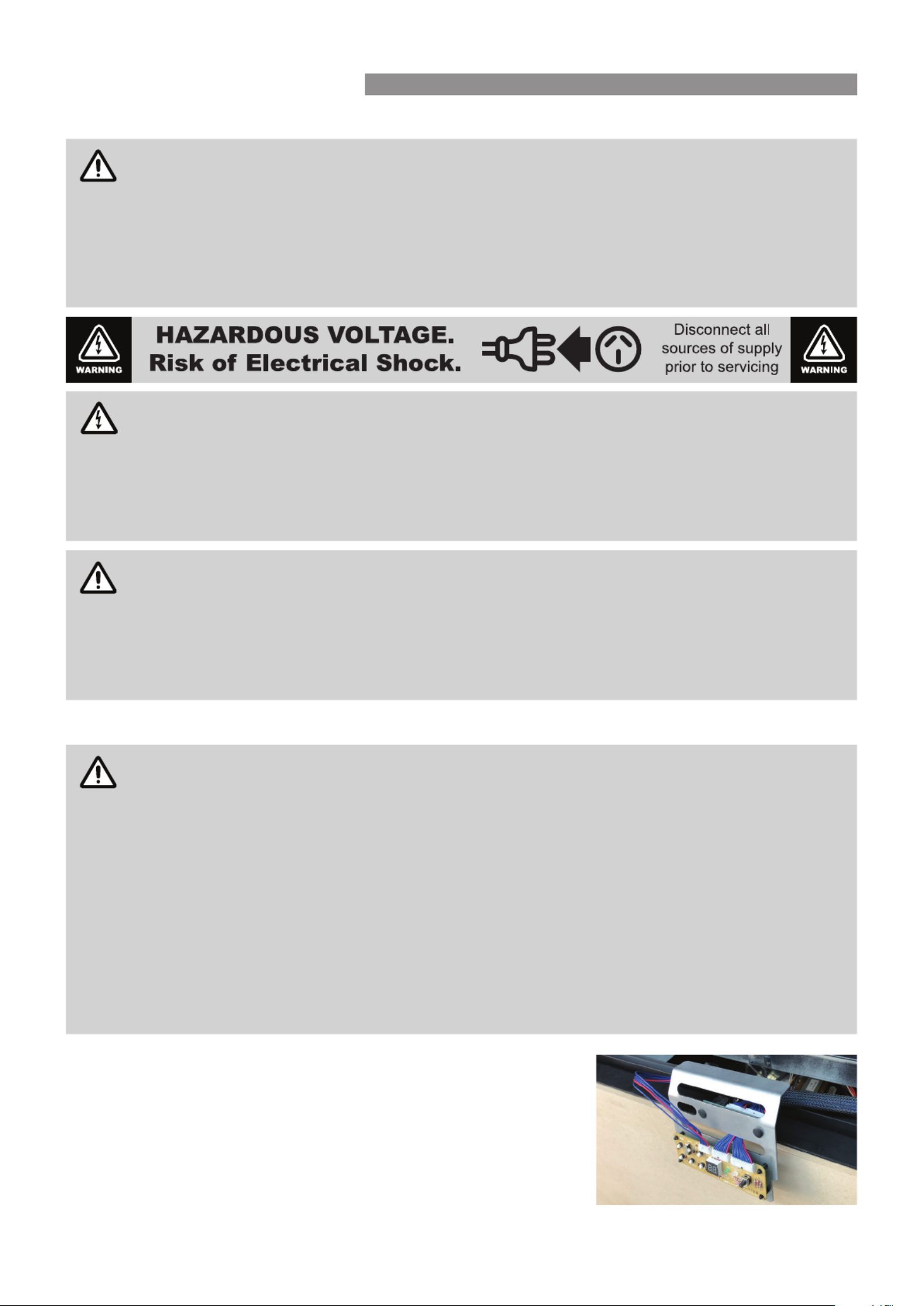
Rinnai 22 RHFE0800F_1000_1500 IM
GENERAL INFORMATION
NOTE
Accessing the commissioning instructions installed in the bottom of the unit will not normally
occur during installation, which is why the instructions are detailed in this section of the manual.
For servicing and maintenance purposes the commissioning instructions are also included in the
service manual. The location of the commissioning instruction pouch within the appliance is as
follows:
RHFE1500 - Located to the right hand side of the gas control
RHFE0800F/1000 - Located tucked in behind the Wi-Fi module
WARNING
When performing the commissioning, the appliance electrical power will need to be connected.
Exercise CAUTION as there is potential for electric shock from the exposed wiring and circuitry.
DO NOT leave the appliance unattended when power is connected and the panels are removed.
Installation and commissioning must be carried out by an Authorised person.
Wiring inside this appliance may be at 240V potential.
DO NOT test for gas escapes with an open ame.
IMPORTANT
LS - Gas Fireplace heaters have two dipswitch settings for ue length.
L-F (Long Flue) this is the factory set default and in general will not require alteration.
S-F (Short Flue) refer to service manual or contact Rinnai for further details.
During commissioning the plastic push buttons on the PCB are required to be pressed to make
adjustments. DO NOT use mechanical items such as screwdrivers to depress these button as
this may lead to breakage.
GAS PRESSURE SETTING
IMPORTANT
The LS - Gas Fireplace heaters come with the high and low operating pressures factory pre-set.
Gas Supply and Burner pressures checked during installation and prior to the MUST BE
installation of the burn media. This is to be done with the glass o and before the burn media*
is added. Make adjustments if the unit is not operating correctly after all other possible other
causes have been eliminated.
Inlet supply pressure to the appliance be checked and set within the operating parameters MUST
of the appliance in all instances. If the appliance cannot be adjusted to perform correctly contact
Rinnai for advice.
Conrm gas type: this appliance available in either Natural or Propane gas, check labelling on top
panel to verify gas type. Contact local gas authority to conrm gas supply type if you are in doubt.
* For heaters tted with the Flametech® burner media (models RHFE0800SF/DF), the two large
logs supplied with the burn media are also the main burners for these appliances. As such it is
necessary to temporarily install these logs onto the aeration sleeves during commissioning.
The pressures can be checked by operating the buttons on the control panel
PCB through the front access panels of the heater before the wall lining has
been installed, or by pulling out the control panel PCB and accessing the
buttons through the opening from the front of the appliance as shown right.
Check the pressures against those printed on the data plate of the appliance.
If the data plate is not easily accessible the pressures are also detailed
on the next page. Even if no adjustment of the gas pressures is required,
access to the 'SET' button may be required to proceed to the next setting.
COMMISSIONING
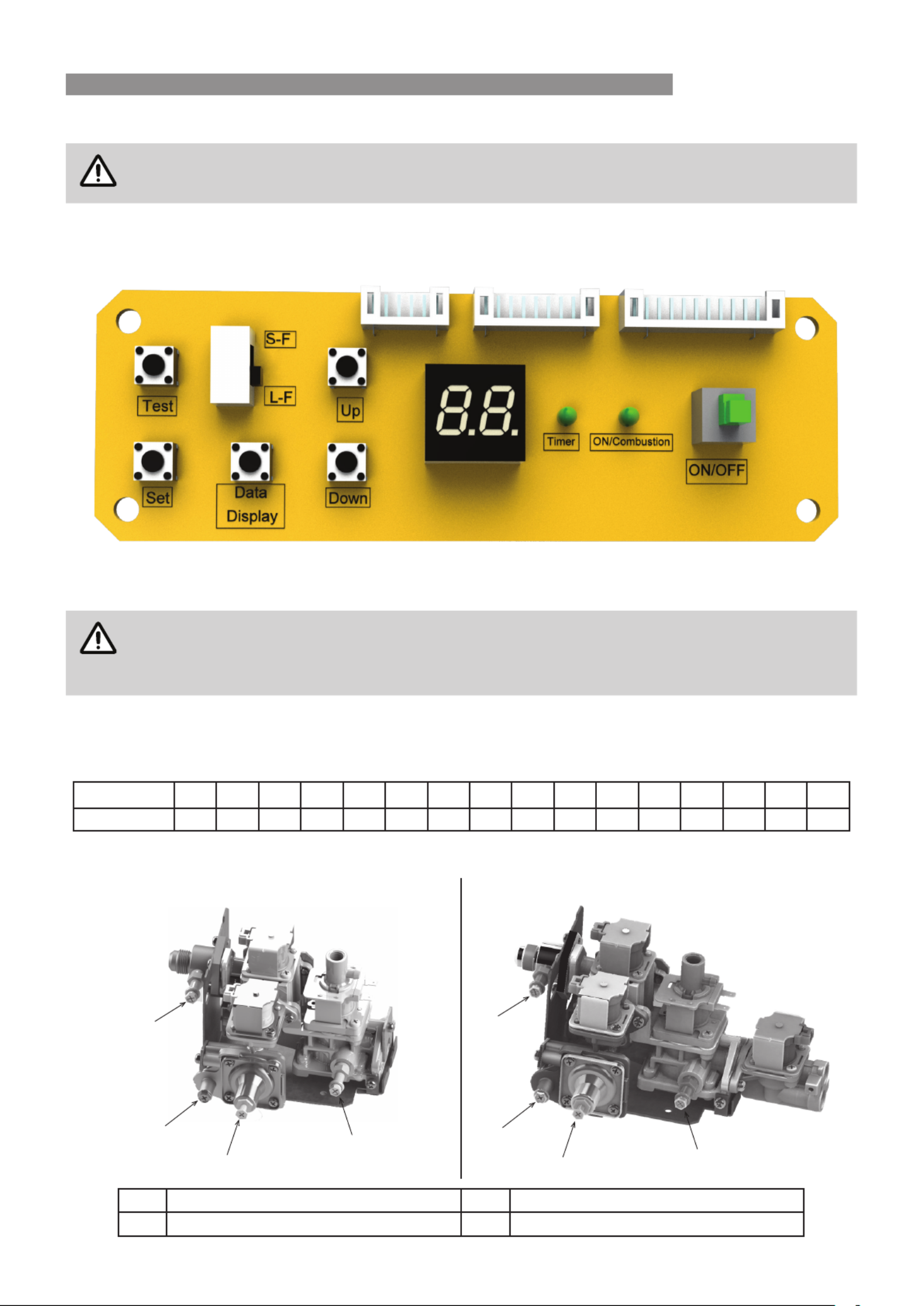
Rinnai 23 RHFE0800F_1000_1500 IM
COMMISSIONING THE PCB
IMPORTANT
PCB commissioning steps are ONLY to be done if the PCB is being replaced or after
a gas conversion.
1. Turn on the gas and power supply.
2. Press the 'Test' button, the display will now show the gas code (A1 = Natural, L1 = Propane). Press the
'Up' and 'Down' buttons to obtain the gas code for the unit, and press 'Set' to lock in the code.
Commissioning of the PCB is now complete and the gas pressures can now be checked.
ROOM THERMISTOR OFFSET
IMPORTANT
The PCB has an additional LED display sequence which will appear after the gas code. This is for
the setting of room thermistor oset. By default this is factory pre-set to 0 (0°C) and ONLY needs
adjustment if there is signicant variation in the thermistor reading and the actual temperature of
the room. Adjustment of this setting is typically NOT required and is part of commissioning.NOT
Thermistor Offset Adjustment
When required adjustment of the oset can be made in 1/3°C steps to ±5°C. Pressing the 'Up' button osets the
temperature +°C, pressing the 'Down' button osets the temperature -°C. Refer below for the full adjustment range.
± Display Value 0 1 2 3 4 5 6 7 8 9 10 11 12 13 14 15
± Temp. Offset °C 0 1/3 2/3 1 1 1/3 1 2/3 2 2 1/3 2 2/3 3 3 1/3 3 2/3 4 4 1/3 4 2/3 5
GAS CONTROL SOLENOIDS
Gas control RHFE0800F/1000 Gas control RHFE1500 (additional solenoid)
1
2
3
4
1
2
34
1Inlet pressure test point screw 3Pilot pressure adjustment screw
2Pilot pressure test point screw 4Main burner pressure test point screw
COMMISSIONING
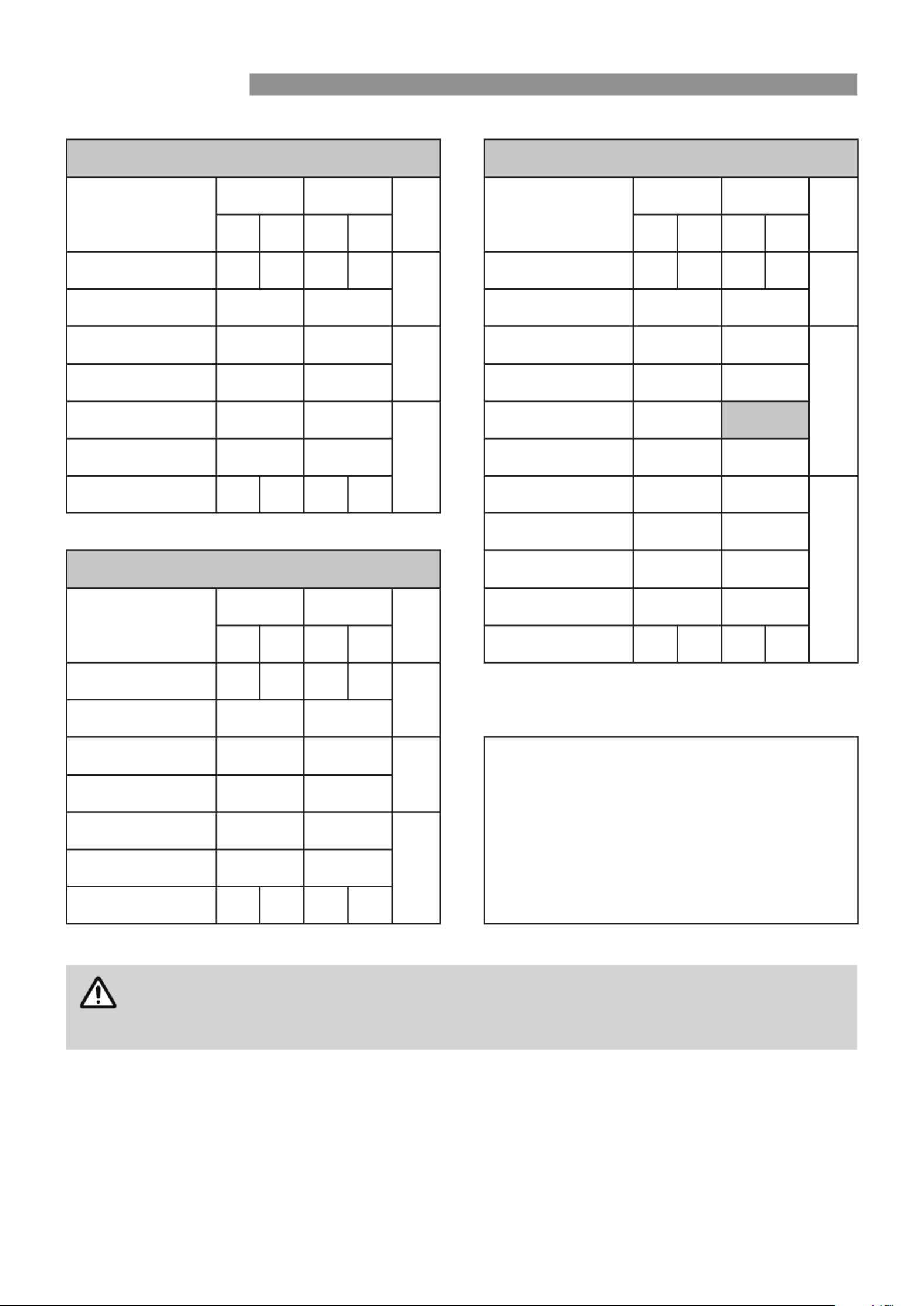
Rinnai 24 RHFE0800F_1000_1500 IM
GAS PRESSURES
RHFE0800SF/DF RHFE1500S/D
Gas Type
Natural Propane
Unit Gas Type
Natural Propane
Unit
S-F L-F S-F L-F S-F L-F S-F L-F
Gas rate Hi 35 32 35 32
MJ/hr
Gas rate Hi 40 37 40 37
MJ/hr
Gas rate Lo Gas rate Lo15 15 14 14
LH RH injector Ø 2.0 1.30
mm
Main injector Ø 2.3 1.4
mm
Aeration sleeve LH RH LH RH injector Ø4.5 x 1 9 x 2 1.6 0.95
Pilot 0.98 2.0
kPa
Aeration sleeve centre 22.5 N/A
PL Aeration sleeve LH RH0.20 0.25 21 17
PH Pilot0.95 0.79 1.70 1.35 0.98 2.0
kPa
PL 0.3 1.0
RHFE1000S/D PF 0.87 2.0
Gas Type
Natural Propane
Unit
PA 0.59 1.0
S-F L-F S-F L-F PH 0.80 0.67 1.90 1.54
Gas rate Hi 34 31 32 29
MJ/hr
Gas rate Lo 15 14
LH RH injector Ø 2.8 1.7
mm S-F = Short Flue Setting
L-F = Long Flue Setting
LH = Left Hand
RH = Right Hand
PL = Main burner on Low
PF = Main burner on High
PA = All burners on Low
PH = All burners on High
Aeration sleeve LH RH 22 0
Pilot 0.98 2.0
kPaPL 0.19 0.40
PH 0.80 0.65 1.85 1.57
SETTING GAS PRESSURES
IMPORTANT
The sequence will vary slightly depending on the model:
Linear 800, 1000: PL > PH
Linear 1500: PL > PF > PA > PH
Checking the Supply Pressure
1. Remove the inlet test point screw and connect the manometer hose.
2. Press the heater 'ON/OFF' button to start the ignition sequence, ensuring the correct inlet pressure is available
with all other gas appliances operating on high.
3. Press the heater 'ON/OFF' button to stop the heater operation.
4. Disconnect the manometer hose and replace the inlet test point screw.
COMMISSIONING
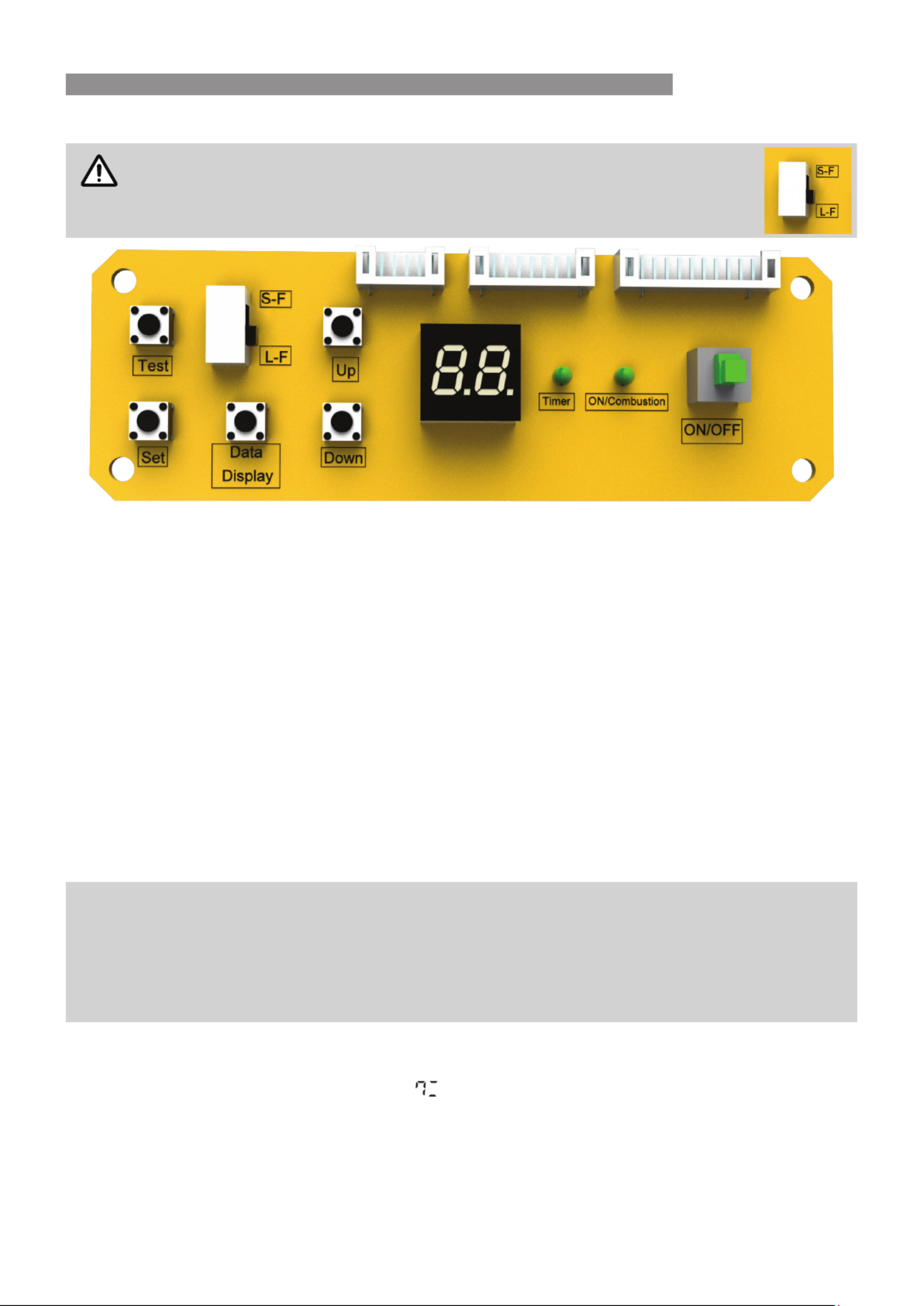
Rinnai 25 RHFE0800F_1000_1500 IM
Setting the Pilot Pressure
IMPORTANT
Before commencing with the setting of the burner pressures the correct ue length
MUST be set.
The ue length dip switch is factory set to L-F (long ue). For information regarding
the S-F (short ue) setting, refer to the service manual or contact Rinnai.
1. Remove the pilot test point screw and connect the manometer hose.
2. Press the heater 'ON/OFF' button to start the ignition sequence, ensuring the correct inlet pressure is available
with all other gas appliances operating on high.
3. Press the 'Test' button twice, the heater will light to main burner on its lowest setting (stage 1) and the display
will show PL.
4. Adjust the pilot pressure as required by manually adjusting the pilot pressure adjustment screw. Press the
'ON/OFF' button to stop the heater operation.
5. Disconnect the manometer hose and replace the pilot test point screw.
Setting the Operating Pressure
1. Remove the main burner test point screw and connect the positive manometer hose.
2. Press the heater 'ON/OFF' button to start the heater.
3. Press the 'Test' button twice, the heater will light to the main burner on its lowest setting (stage 1) and the
digital display will show PL.
4. Press the 'Up' or 'Down' buttons to set the pressure for the appropriate gas type. Press the 'Set' button once
to save the setting.
For RHFE1500 ONLY:
5. The display will now show PF (main burner stage 3). Press the 'Up' or 'Down' buttons to set the pressure for
the appropriate gas type. Press the 'Set' button once to save the setting.
6. The display will show PA (main burner stage 4). Press the 'Up' and 'Down' buttons to set the pressure for
the appropriate gas type. Press the 'Set' button once to save the setting. It can take several seconds for the
solenoid to open and the pressure to stabilise.
7. The display will show PH (main burner stage 7). Press the 'Up' or 'Down' buttons to set the dierential for the
appropriate gas type. Press the 'Set' button once to save the setting.
8. For RHFE0800F/1000 the display will show:
For RHFE1500 the display will show: 70
If the display does not change, then there is a commissioning error - repeat steps.
9. Press the 'ON/OFF' button to stop the unit.
10. Remove the manometer hose and replace the gas control test point screw.
Commissioning is now complete.
COMMISSIONING
Produkt Specifikationer
Mærke: | Rinnai |
Kategori: | Varmeapparat |
Model: | LS800 |
Har du brug for hjælp?
Hvis du har brug for hjælp til Rinnai LS800 stil et spørgsmål nedenfor, og andre brugere vil svare dig
Varmeapparat Rinnai Manualer

24 August 2024

23 August 2024

23 August 2024

23 August 2024

23 August 2024

23 August 2024

23 August 2024

23 August 2024

23 August 2024

23 August 2024
Varmeapparat Manualer
- Varmeapparat DeLonghi
- Varmeapparat Scheppach
- Varmeapparat Sinbo
- Varmeapparat Bosch
- Varmeapparat SilverCrest
- Varmeapparat Sencor
- Varmeapparat EasyMaxx
- Varmeapparat Maxxmee
- Varmeapparat Zibro
- Varmeapparat Wilfa
- Varmeapparat Beurer
- Varmeapparat Breville
- Varmeapparat Zanussi
- Varmeapparat Candy
- Varmeapparat Gorenje
- Varmeapparat DeWalt
- Varmeapparat AENO
- Varmeapparat Tectro
- Varmeapparat VOX
- Varmeapparat RYOBI
- Varmeapparat Philips
- Varmeapparat Caso
- Varmeapparat Concept
- Varmeapparat Steba
- Varmeapparat Vitek
- Varmeapparat Medisana
- Varmeapparat Rommelsbacher
- Varmeapparat OK
- Varmeapparat AEG
- Varmeapparat Electrolux
- Varmeapparat Bauknecht
- Varmeapparat Master
- Varmeapparat Melissa
- Varmeapparat Emos
- Varmeapparat ARGO
- Varmeapparat Qlima
- Varmeapparat Korona
- Varmeapparat HP
- Varmeapparat Soler & Palau
- Varmeapparat Aduro
- Varmeapparat Baxi
- Varmeapparat Livoo
- Varmeapparat Klarstein
- Varmeapparat Güde
- Varmeapparat Tefal
- Varmeapparat Real Flame
- Varmeapparat Infiniton
- Varmeapparat Trisa
- Varmeapparat Princess
- Varmeapparat Nedis
- Varmeapparat Emerio
- Varmeapparat Severin
- Varmeapparat Logik
- Varmeapparat Hendi
- Varmeapparat Bartscher
- Varmeapparat Vonroc
- Varmeapparat Sunbeam
- Varmeapparat Hama
- Varmeapparat Thomson
- Varmeapparat Hyundai
- Varmeapparat Milwaukee
- Varmeapparat Dyson
- Varmeapparat Imetec
- Varmeapparat TriStar
- Varmeapparat Blyss
- Varmeapparat Trumatic
- Varmeapparat Parkside
- Varmeapparat Adler
- Varmeapparat Black And Decker
- Varmeapparat Camry
- Varmeapparat Dometic
- Varmeapparat Mestic
- Varmeapparat FERM
- Varmeapparat Barbecook
- Varmeapparat Eurom
- Varmeapparat Sunred
- Varmeapparat Trotec
- Varmeapparat Blaupunkt
- Varmeapparat Einhell
- Varmeapparat Becken
- Varmeapparat BEKO
- Varmeapparat Stanley
- Varmeapparat Honeywell
- Varmeapparat Alpina
- Varmeapparat Clatronic
- Varmeapparat Mesko
- Varmeapparat Quigg
- Varmeapparat Rowenta
- Varmeapparat Noveen
- Varmeapparat Fagor
- Varmeapparat König
- Varmeapparat Atika
- Varmeapparat Truma
- Varmeapparat AFK
- Varmeapparat Bomann
- Varmeapparat Russell Hobbs
- Varmeapparat Ariete
- Varmeapparat Elro
- Varmeapparat Innoliving
- Varmeapparat Zelmer
- Varmeapparat United
- Varmeapparat Boretti
- Varmeapparat FIAP
- Varmeapparat Vivax
- Varmeapparat EvoHeat
- Varmeapparat Thermex
- Varmeapparat Bionaire
- Varmeapparat EWT
- Varmeapparat Stadler Form
- Varmeapparat Powerfix
- Varmeapparat Hayward
- Varmeapparat Maginon
- Varmeapparat Calor
- Varmeapparat Dri-Eaz
- Varmeapparat Danfoss
- Varmeapparat Tesy
- Varmeapparat Dimplex
- Varmeapparat Eberle
- Varmeapparat Cuisinart
- Varmeapparat Cadel
- Varmeapparat Primo
- Varmeapparat Lervia
- Varmeapparat Orbegozo
- Varmeapparat Reer
- Varmeapparat Malmbergs
- Varmeapparat CaterChef
- Varmeapparat Optimum
- Varmeapparat Taurus
- Varmeapparat Olympia
- Varmeapparat Xiaomi
- Varmeapparat Westfalia
- Varmeapparat Exquisit
- Varmeapparat HQ
- Varmeapparat Pelgrim
- Varmeapparat Enders
- Varmeapparat MPM
- Varmeapparat Basetech
- Varmeapparat Toyotomi
- Varmeapparat G3 Ferrari
- Varmeapparat Domo
- Varmeapparat Mellerware
- Varmeapparat Mill
- Varmeapparat Jøtul
- Varmeapparat Fluval
- Varmeapparat Ferroli
- Varmeapparat Velleman
- Varmeapparat Perel
- Varmeapparat La Nordica
- Varmeapparat Zodiac
- Varmeapparat Heylo
- Varmeapparat Vemer
- Varmeapparat Ambiano
- Varmeapparat Olimpia Splendid
- Varmeapparat Unold
- Varmeapparat Bestway
- Varmeapparat Zibro Kamin
- Varmeapparat Nevir
- Varmeapparat Eden
- Varmeapparat Harvia
- Varmeapparat Eureka
- Varmeapparat Blumfeldt
- Varmeapparat Inventum
- Varmeapparat Carson
- Varmeapparat SuperFish
- Varmeapparat Gre
- Varmeapparat Fakir
- Varmeapparat Swan
- Varmeapparat Dantherm
- Varmeapparat Midea
- Varmeapparat Napoleon
- Varmeapparat Bimar
- Varmeapparat Evolar
- Varmeapparat Ardes
- Varmeapparat Suntec
- Varmeapparat Sun Joe
- Varmeapparat SVAN
- Varmeapparat Danby
- Varmeapparat Sogo
- Varmeapparat Koenic
- Varmeapparat Hema
- Varmeapparat Scarlett
- Varmeapparat Izzy
- Varmeapparat Cotech
- Varmeapparat ECG
- Varmeapparat Solis
- Varmeapparat Wamsler
- Varmeapparat Eldom
- Varmeapparat Maxwell
- Varmeapparat H.Koenig
- Varmeapparat Sonnenkönig
- Varmeapparat SPC
- Varmeapparat Proline
- Varmeapparat Termozeta
- Varmeapparat Waldbeck
- Varmeapparat OneConcept
- Varmeapparat Invicta
- Varmeapparat WAGAN
- Varmeapparat Just Fire
- Varmeapparat Nobo
- Varmeapparat Brandson
- Varmeapparat Ecoteck
- Varmeapparat Lasko
- Varmeapparat Eta
- Varmeapparat Lynx
- Varmeapparat Orion
- Varmeapparat Duux
- Varmeapparat Nectre
- Varmeapparat Stiebel Eltron
- Varmeapparat Rotel
- Varmeapparat Lavorwash
- Varmeapparat Kalorik
- Varmeapparat Euromac
- Varmeapparat Generac
- Varmeapparat Cecotec
- Varmeapparat Solac
- Varmeapparat Anslut
- Varmeapparat Beper
- Varmeapparat Haas+Sohn
- Varmeapparat Eurolite
- Varmeapparat Outdoor Order
- Varmeapparat Team
- Varmeapparat Supra
- Varmeapparat Clean Air Optima
- Varmeapparat Chauvet
- Varmeapparat Kenmore
- Varmeapparat Brentwood
- Varmeapparat JANDY
- Varmeapparat Corbero
- Varmeapparat Otsein-Hoover
- Varmeapparat Lenoxx
- Varmeapparat SereneLife
- Varmeapparat Remko
- Varmeapparat Duronic
- Varmeapparat Broan
- Varmeapparat Conceptronic
- Varmeapparat Bestron
- Varmeapparat Philco
- Varmeapparat Kunft
- Varmeapparat Kogan
- Varmeapparat DCG
- Varmeapparat Ravanson
- Varmeapparat NEO Tools
- Varmeapparat AstralPool
- Varmeapparat Jocel
- Varmeapparat Heller
- Varmeapparat Signature
- Varmeapparat Ufesa
- Varmeapparat Vornado
- Varmeapparat Devanti
- Varmeapparat Orava
- Varmeapparat NewAir
- Varmeapparat Maestro
- Varmeapparat Haeger
- Varmeapparat Create
- Varmeapparat PRIME3
- Varmeapparat Lifesmart
- Varmeapparat Yellow Garden Line
- Varmeapparat Flama
- Varmeapparat Kambrook
- Varmeapparat Profile
- Varmeapparat AKO
- Varmeapparat Royal Sovereign
- Varmeapparat Haverland
- Varmeapparat Jata
- Varmeapparat Teesa
- Varmeapparat Nestor Martin
- Varmeapparat Heinner
- Varmeapparat Fenix
- Varmeapparat Cresta
- Varmeapparat Guzzanti
- Varmeapparat Defy
- Varmeapparat Air King
- Varmeapparat King
- Varmeapparat Piazzetta
- Varmeapparat Kent
- Varmeapparat Arnold Rak
- Varmeapparat Listo
- Varmeapparat CasaFan
- Varmeapparat Alpatec
- Varmeapparat Blaze
- Varmeapparat Sygonix
- Varmeapparat Creda
- Varmeapparat Plieger
- Varmeapparat Zehnder
- Varmeapparat Igenix
- Varmeapparat Essentiel B
- Varmeapparat Havsö
- Varmeapparat Fantini Cosmi
- Varmeapparat Zephir
- Varmeapparat Equator
- Varmeapparat Brixton
- Varmeapparat Superior
- Varmeapparat Vasco
- Varmeapparat Argoclima
- Varmeapparat Mirpol
- Varmeapparat Grunkel
- Varmeapparat PAX
- Varmeapparat Jaga
- Varmeapparat Masport
- Varmeapparat Home Electric
- Varmeapparat Extraflame
- Varmeapparat Livington
- Varmeapparat Hartig And Helling
- Varmeapparat Gutfels
- Varmeapparat Crane
- Varmeapparat TAIDEN
- Varmeapparat Veito
- Varmeapparat Etherma
- Varmeapparat Eva Calor
- Varmeapparat Nordic Fire
- Varmeapparat Eurotronic
- Varmeapparat Ausclimate
- Varmeapparat DCS
- Varmeapparat Wanders
- Varmeapparat Tecno Air System
- Varmeapparat Perfect Aire
- Varmeapparat Everdure
- Varmeapparat Grandhall
- Varmeapparat Emga
- Varmeapparat Adax
- Varmeapparat Heatstrip
- Varmeapparat Escea
- Varmeapparat Dedra
- Varmeapparat Braemar
- Varmeapparat Bromic Heating
- Varmeapparat Martec
- Varmeapparat Jindara
- Varmeapparat Global
- Varmeapparat Neo
- Varmeapparat SPT
- Varmeapparat Hatco
- Varmeapparat Starlyf
- Varmeapparat Aerian
- Varmeapparat IXL
- Varmeapparat XPower
- Varmeapparat True North
- Varmeapparat WestBend
- Varmeapparat Hortus
- Varmeapparat Prem-i-air
- Varmeapparat Quadra-Fire
- Varmeapparat Mr. Heater
- Varmeapparat Stenda
- Varmeapparat Magnavox
- Varmeapparat VIESTA
- Varmeapparat Apricus
- Varmeapparat Heatsome
- Varmeapparat Brivis
- Varmeapparat Hubbell
- Varmeapparat HeatStar
- Varmeapparat Pacific Energy
- Varmeapparat Regency
- Varmeapparat Burley
- Varmeapparat SHX
- Varmeapparat Monzana
- Varmeapparat Invroheat
- Varmeapparat Kaden
- Varmeapparat Jarden
- Varmeapparat GoldAir
- Varmeapparat Noirot
- Varmeapparat Ouellet
- Varmeapparat AccuLux
- Varmeapparat Gossmann
- Varmeapparat Wulfe
- Varmeapparat Big Ass Fans
- Varmeapparat Duro Pro
- Varmeapparat Herschel
- Varmeapparat Casaya
- Varmeapparat HyCell
- Varmeapparat TURBRO
- Varmeapparat Radialight
- Varmeapparat Sunheat
- Varmeapparat Heidenfeld
- Varmeapparat Hcalory
- Varmeapparat Rowi
- Varmeapparat Neopower
- Varmeapparat Arlec
- Varmeapparat Guardian
- Varmeapparat Pureheat
- Varmeapparat Bromic
- Varmeapparat MSW
- Varmeapparat Solamagic
- Varmeapparat Contura
- Varmeapparat Alkari
- Varmeapparat Longvie
- Varmeapparat Blue Rhino
- Varmeapparat Rheem
- Varmeapparat Gasmate
- Varmeapparat Ionmax
- Varmeapparat Airo
- Varmeapparat Mission Air
- Varmeapparat Omega Altise
- Varmeapparat Scandia
- Varmeapparat Vasner
- Varmeapparat Fire Sense
- Varmeapparat InfraNomic
- Varmeapparat Heat Storm
- Varmeapparat Excelair
- Varmeapparat Heatscope
- Varmeapparat Heat1
- Varmeapparat Rose LM
- Varmeapparat Thermotec
- Varmeapparat Kemlan
- Varmeapparat AustWood
- Varmeapparat Uniprodo
- Varmeapparat Yamazen
- Varmeapparat Infratech
- Varmeapparat TANSUN
- Varmeapparat Universal Blue
- Varmeapparat Air&Me
- Varmeapparat Reznor
- Varmeapparat Heat4All
Nyeste Varmeapparat Manualer

3 April 2025

2 April 2025

26 Marts 2025

16 Marts 2025

16 Marts 2025

13 Marts 2025

13 Marts 2025

26 Februar 2025

26 Februar 2025

25 Februar 2025