Midea MP86SQWBA2RCM Manual
Midea
Klimaanlæg
MP86SQWBA2RCM
Læs nedenfor 📖 manual på dansk for Midea MP86SQWBA2RCM (76 sider) i kategorien Klimaanlæg. Denne guide var nyttig for 25 personer og blev bedømt med 4.5 stjerner i gennemsnit af 2 brugere
Side 1/76
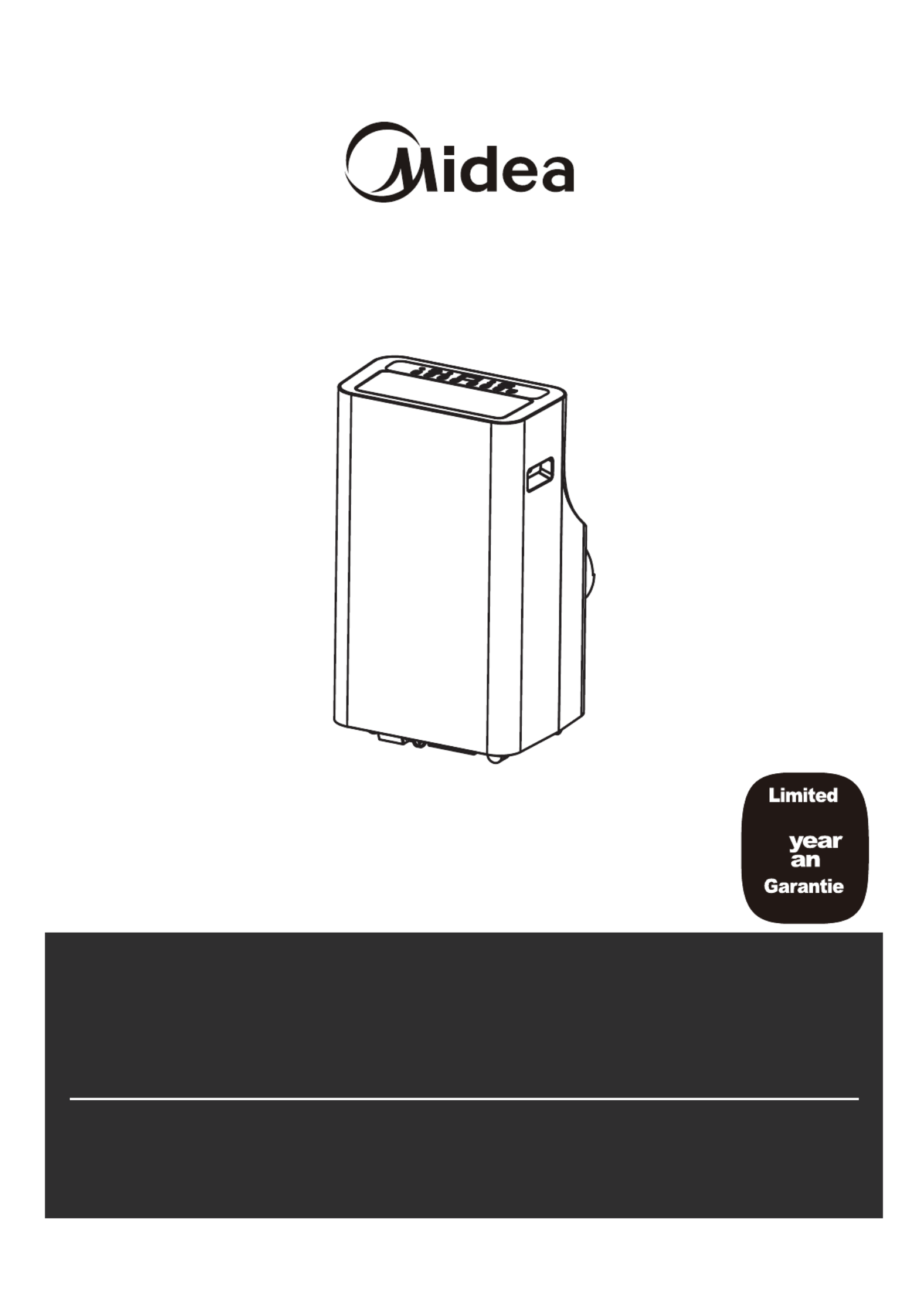
Item No. 888153 SKu No. 21615024 Model NO. MP72SQWBA2RCM
Item No. 888 21615025 Model NO. MP86SQWBA2RCM 149 SKu No.
information about this product, please call our toll-free number.
SAVE THIS MANUAL
Keep this manual and the original sales invoice in a safe, dry place for future reference.
Notre personnel du service à la clientèle est disponible pour vous aider. En cas de problème avec votre achat, ou pour
obtenir plus d’informations à propos de ce produit, veuillez composer notre numéro sans frais.
CONSERVEZ CE GUIDE
Conservez ce manuel avec la facture d’origine dans un endroit sûr et sec pour référence future.
Our customer service staff is available to help you. For any problem with your purchase, or to receive further
Customer Service / Service à la clientèle:
PORTABLE AIR CONDITIONER
Owner's Manual
1-866-646-4332
Warranty
Limitée
1
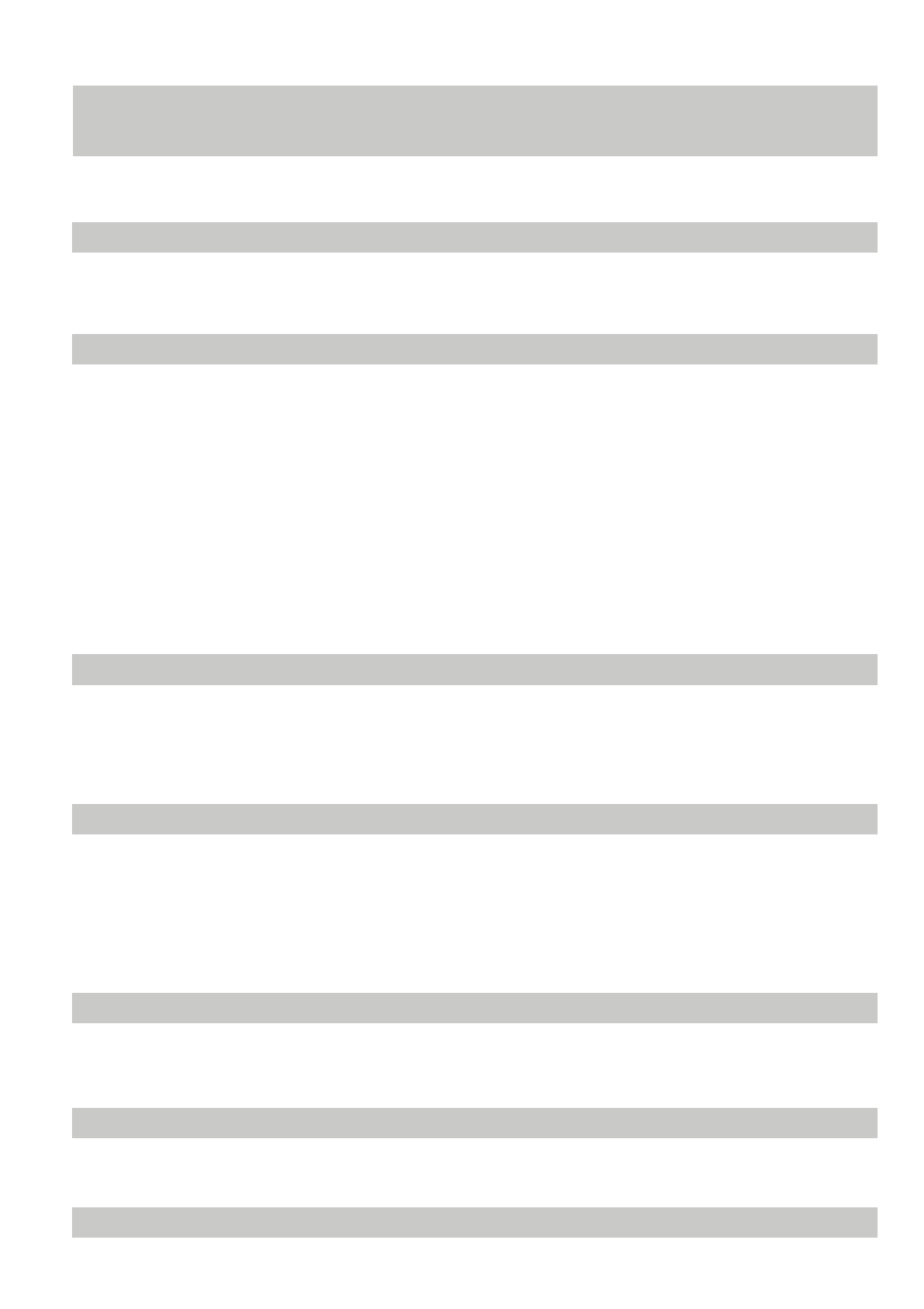
Safety Precautions
...........................................................................................................................................................
Safety Precautions
Installation Instructions
Operating Instructions
Maintenance
Table of Contents
Control Panel Features
Operation Instructions
Other features
Safety Precautions
Air Filter Cleaning
Troubleshooting Tips
Unit Cleaning
Store the unit when not in use
Preparation
........................................................................................................................................................
....................................................................................................................................................
....................................................................................................................................................
...................................................................................................................................
...................................................................................................................................
...................................................................................................................................
........................................................................................................................................................
........................................................................................................................................................
...................................................................................................................................................
...................................................................................................................................................
...........................................................................................................................................
.......................................................................................................................
...........................................................................................................................................
.....................................................................................................................................
........................................................................................................................
....................................................................................................................
................................................................................................................................
..............................................................................................................................
.........................................................................................................................
......................................................................................
Design Notice
Ambient Temperature Range For Unit Operating
Exhaust Hose Installation
Choosing The Right Location
Tools Needed
Accessories
Window Installation Kit
Installation
Troubleshooting Tips
03
12
12
Energy Rating Information 13
12
12
13
14
14
14
15
17
19
20
21
21
21
22
22
Remote controller lllustration
Remote controller lllustration
23
Air conditioner limited warranty
Air conditioner limited warranty
36

(Required
for
R32
u ly)nits on
IMPORT NO s alANT TE:Read thi manu
carefu y for stalli o eratingll be e in ng r op
your new air c itioni uni ak sureond ng t. M e
to his save t
m l or utur nceanua f f e refere
.
• Do not use means to accelerate the defrosting process or to clean, other than those
recommended by the manufacturer.
• The appliance shall be stored in a room without continuously operating ignition
sources (for example: open ames, an operating gas appliance) and ignition sourcesor
(for example:an operating electric heater) close to the appliance. The appliance shall
be stored in a room without continuously operating ignition sources (for example:
open ames, an operating gas appliance or an operating electric heater).
• Do not pierce or burn.
• Be aware that the refrigerants may not contain an odour.
• Compliance with national gas regulations shall be observed.
• Keep ventilation openings clear of obstruction.
• The appliance shall be stored so as to prevent mechanical damage from occurring.
• A warning that the appliance shall be stored in a well-ventilated area where the room
size corresponds to the room area as specied for operation.
• Any person who is involved with working on or breaking into a refrigerant circuit
should hold a current valid certicate from an industry-accredited assessment
authority, which authorises their competence to handle refrigerants safely in
accordance with an industry recognised assessment specication.
• Servicing shall only be performed as recommended by the equipment manufacturer.
Maintenance and repair requiring the assistance of other skilled personnel shall be
carried out under the supervision of the person competent in the use of ammable
refrigerants.
• DO NOT modify the length of the power cord or use an extension cord to power the
unit. DO NOT share a single outlet with other electrical appliances. Improper power
supply can cause re or electrical shock.
• Please follow the instruction carefully to handle, install, clear, service the air
conditioner to avoid any damage or hazard. Flammable Refrigerant R32 is used
within air conditioner. When maintaining or disposing the air conditioner, the
refrigerant (R32) shall be recovered properly, shall not discharge to air directly.
•
Please follow the instruction carefully to store or maintain the air conditioner to
No any open re or device like switch which may generate spark/arcing shall be
around air conditioner to avoid causing ignition of the ammable refrigerant used.
prevent mechanical damage from occurring.
• Flammable refrigerant -R32 is used in air conditioner. Please follow the instruction
carefully to avoid any hazard. For specic information on the type of gas and the
amount, please refer to the relevant label on the unit itself.
WARNING (for using R32 refrigerant only)
Page 6
Safety
Precautions
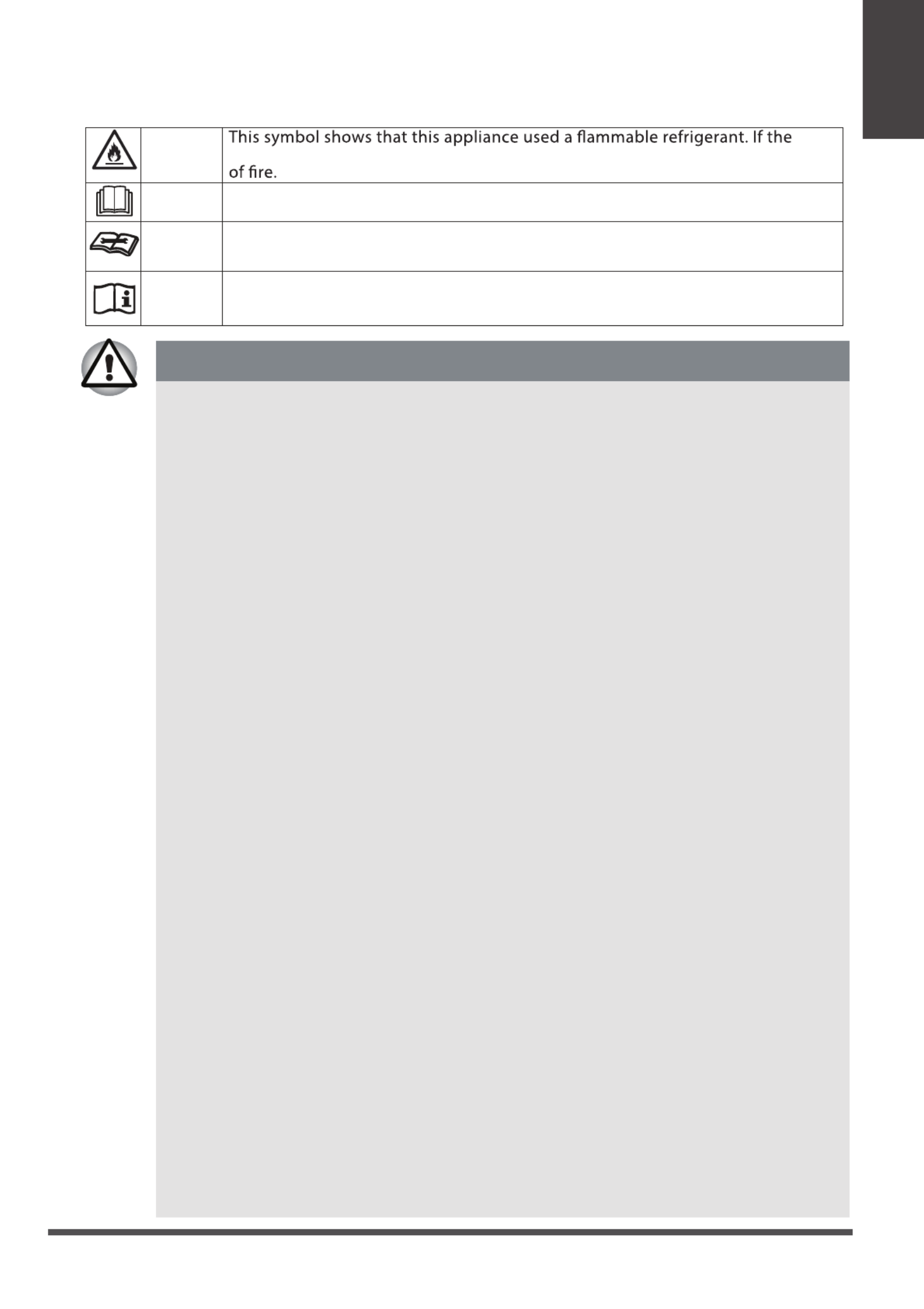
Exp nation of symb l n ):la ol dis sp ayed o the unit(For the unit adopts R32 Refrigerant only
WARNING
refriger t kean i eas l d n a nal ignitio our her s a risk a d exposed to n exter n s ce, t e i
CAUTION
CAUTION
CAUTION
This symbo sho a o nual shoul rea ca fully.l ws th t the operati n ma d be d re
This symbo sho a s should handli thisl ws th t a ervice personnel be ng
equ i ren manual.ipment w th refe ce to the installation
This symbo shows t n a o suc as t o ratingl tha i form ti n is available h he pe
manu stalla o a al.al or in ti n m nu
•
See transport regulations.
Transport of equipment containing ammable refrigerants.
• Marking of equipment using signs.
See local regulations.
•
See national regulations.
Disposal of equipment using ammable refrigerants.
• Storage of equipment/appliances.
The storage of equipment should be in accordance with the manufacturer's
instructions.
• Storage of packed (unsold) equipment.
Storage package protection should be constructed such that mechanical damage
to the equipment inside the package will not cause a leak of the refrigerant charge.
The maximum number of pieces of equipment permitted to be stored together will
be determined by local regulations.
• Information on servicing.
1)Checks to the area
checks are necessary to ensure that the risk of ignition is minimised. For repair to
Prior to beginning work on systems containing ammable refrigerants, safety
the refrigerating system, the following precautions shall be complied with prior to
conducting work on the system.
2)Work procedure
Work shall be undertaken under a controlled procedure so as to minimise the risk
of a ammable gas or vapour being present while the work is being performed.
3)General work area
All maintenance sta and others working in the local area shall be instructed on the
nature of work being carried out. Work in conned spaces shall be avoided. The
area around the workspace shall be sectioned o. Ensure that the conditions within
the area have been made safe by control of ammable material.
4)Checking for presence of refrigerant
5)Presence of re extinguisher
The area shall be checked with an appropriate refrigerant detector prior to and
during work, to ensure the technician is aware of potentially ammable atmospheres.
Ensure that the leak detection equipment being used is suitable for use with
ammable refrigerants, i.e. non-sparking, adequately sealed or intrinsically safe.
If any hot work is to be conducted on the refrigeration equipment or any associated
parts, appropriate re extinguishing equipment shall be available to hand. Have a
dry powder or CO2 re extinguisher adjacent to the charging area.
WARNINGS (for using R32 refrigerant only)
Safety
Precautions
Page 7
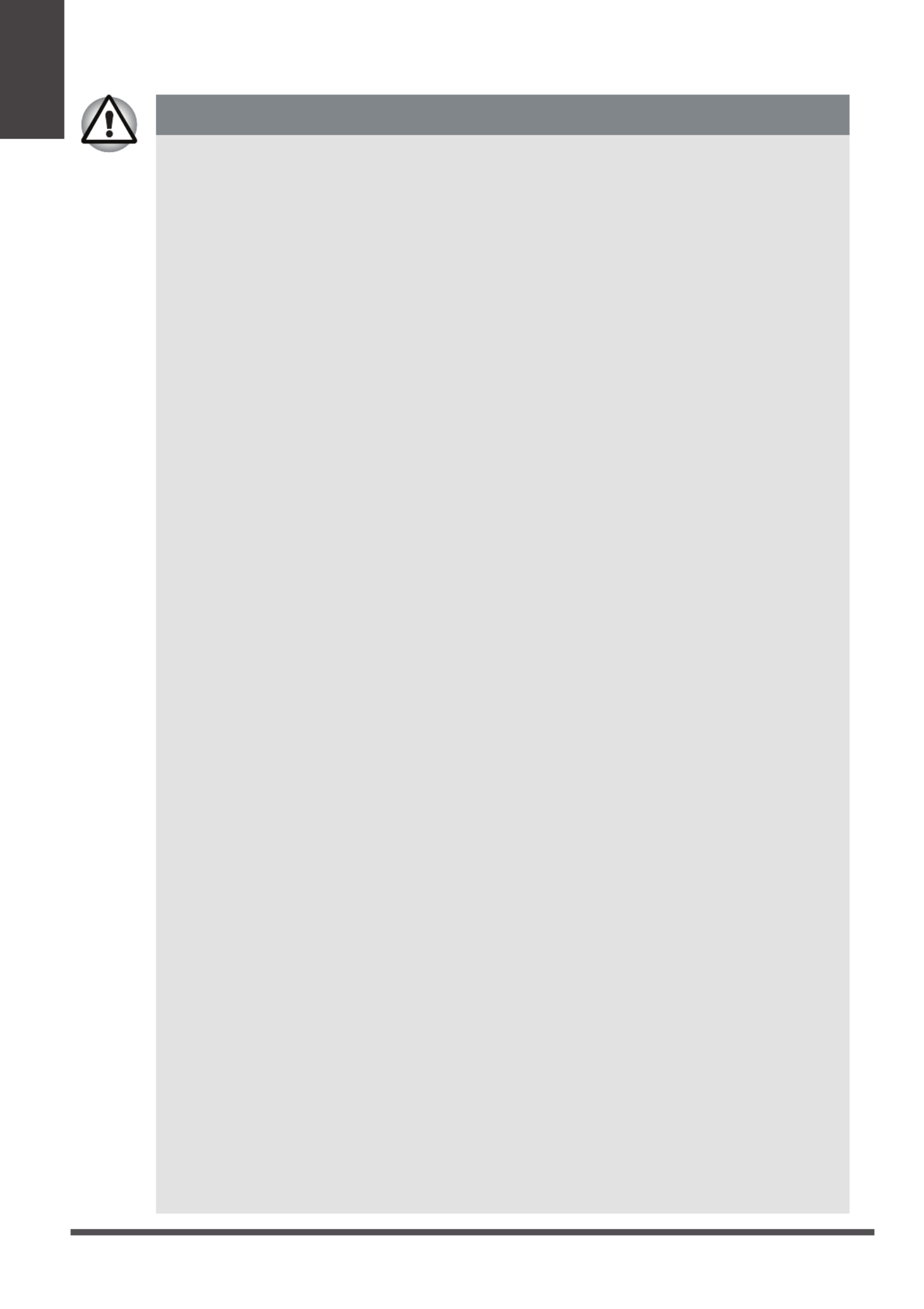
6)No ignition sources
No person carrying out work in relation to a refrigeration system which involves
away from the site of installation, repairing, removing and disposal, during which
taking place, the area around the equipment is to be surveyed to make sure that there
7)Ventilated area
Ensure that the area is in the open or that it is adequately ventilated before breaking
into the system or conducting any hot work. A degree of ventilation shall continue
during the period that the work is carried out. The ventilation should safely disperse
any released refrigerant and preferably expel it externally into the atmosphere.
8)Checks to the refrigeration equipment
guidelines shall be followed. If in doubt consult the manufacturer's technical
department for assistance.
The charge size is in accordance with the room size within which the refrigerant
containing parts are installed;
Theventilation machinery and outlets are operating adequately and are not obstructed;
If an indirect refrigerating circuit is being used, the secondary circuit shall be checked
for the presence of refrigerant;
Marking to the equipment continues to be visible and legible. Markings and signs that
are illegible shall be corrected;
Refrigeration pipe or components are installed in a position where they are unlikely to
be exposed to any substance which may corrode refrigerant containing components,
unless the components are constructed of materials which are inherently resistant to
being corroded or are suitably protected against being so corroded.
9)Checks to electrical devices
Repair and maintenance to electrical components shall include initial safety checks
and component inspection procedures. If a fault exists that could compromise safety,
then no electrical supply shall be connected to the circuit until it is satisfactorily dealt
with. If the fault cannot be corrected immediately but it is necessary to continue
operation, an adequate temporary solution shall be used. This shall be reported to the
owner of the equipment so all parties are advised.
Initial safety checks shall include:
That capacitors are discharged: this shall be done in a safe manner to avoid
possibility of sparking;
That there no live electrical components and wiring are exposed while charging,
recovering or purging the system;
That there is continuity of earth bonding.
• Repairs to sealed components
1)During repairs to sealed components, all electrical supplies shall be disconnected
from the equipment being worked upon prior to any removal of sealed covers, etc.
If it isabsolutely necessary to have an electrical supply to equipment during
servicing, then a permanently operating form of leak detection shall be located at
the most critical point to warn of a potentially hazardous situation.
WARNINGS (for using R32 refrigerant only)
exposing any pipe work that contains or has contained ammable refrigerant shall use
any sources of ignition in such a manner that it may lead to the risk of re or explosion.
All possible ingition sources, including cigarette smoking, should be kept suciently far
ammble refrigerant can possibly be released to the surrounding space. Prior to work
are no ammable hazards or ignition risks. No Smoking signs shall be displayed.
Where electrical components are being chaged, they shall be t for the purpose and
to the correct specication. At all times the manufactures’s maintenance and service
The following checks shall be applied to installations using ammable refrigerants:
Safety
Precautions
Page 8
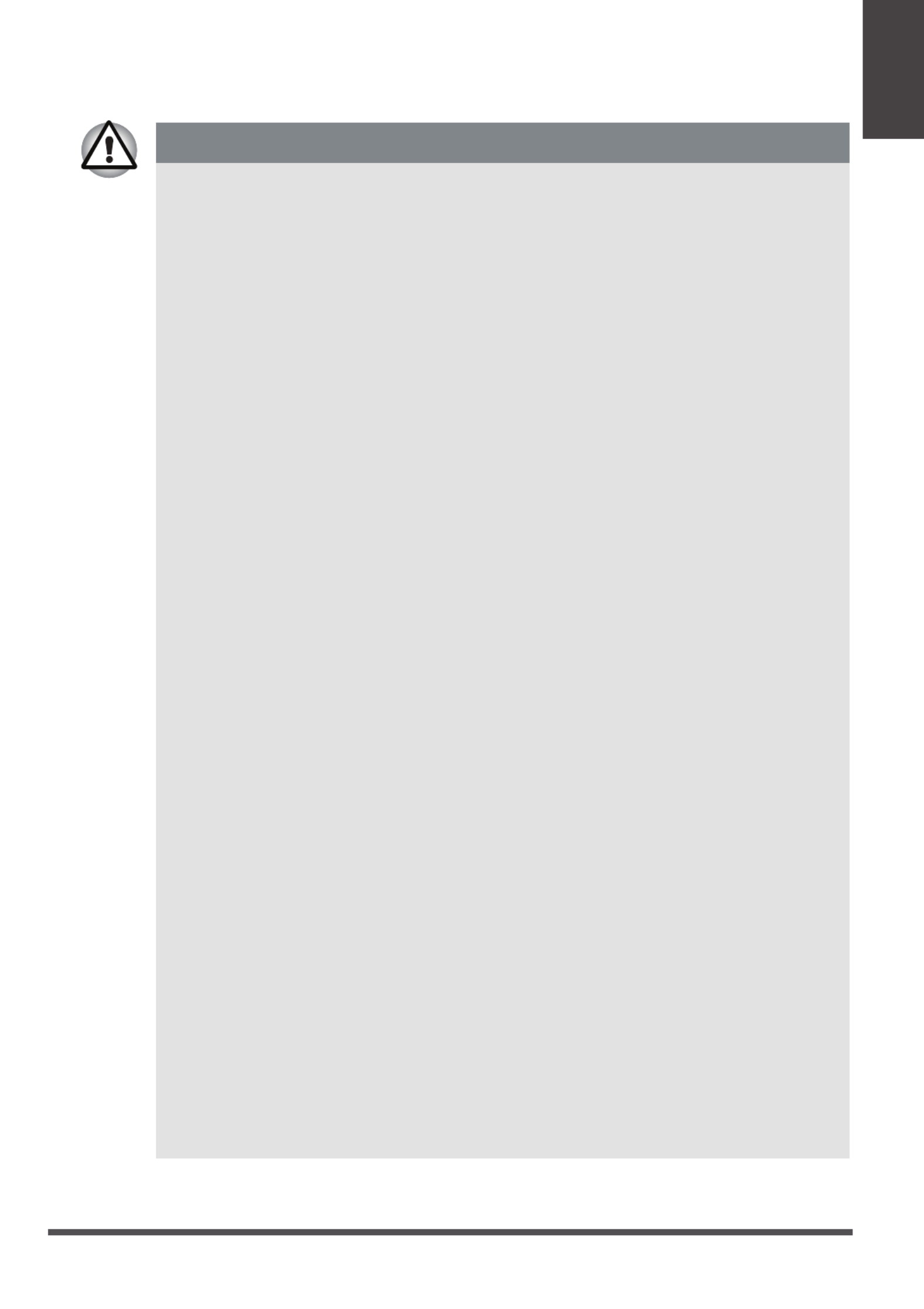
2)Particular attention shall be paid to the following to ensure that by working on
electrical components, the casing is not altered in such a way that the level of
This shall include damage to cables, excessive number of connections, terminals
Ensure that apparatus is mounted securely.
Ensure that seals or sealing materials have not degraded such that they no longer
detection equipment. Intrinsically safe components do not have to be isolated prior
to working on them.
• Repair to intrinsically safe components
Do not apply any permanent inductive or capacitance loads to the circuit without
ensuring that this will not exceed the permissible voltage and current permitted for
the equipment in use.
Intrinsically safe components are the only types that can be worked on while live in the
result in the ignition of refrigerant in the atmosphere from a leak.
• Cabling
Check that cabling will not be subject to wear, corrosion, excessive pressure,
as compressors or fans.
•
Under no circumstances shall potential sources of ignition be used in the searching
for or detection of refrigerant leaks. A halide torch (or any other detector using a
• Leak detection methods
The following leak detection methods are deemed acceptable for systems containing
refrigerants, but the sensitivity may not be adequate, or may need re-calibration.
(Detection equipment shall be calibrated in a refrigerant-free area.) Ensure that the
detector is not a potential source of ignition and is suitable for the refrigerant used.
Leak detection equipment shall be set at a percentage of the LFL of the refrigerant
and shall be calibrated to the refrigerant employed and the appropriate percentage of
most refrigerants but the use of detergents containing chlorine shall be avoided as the
chlorine may react with the refrigerant and corrode the copper pipe-work. If a leak is
refrigerant is found which requires brazing, all of the refrigerant shall be recovered
remote from the leak. Oxygen free nitrogen (OFN) shall then be purged through the
system both before and during the brazing process.
WARNINGS (for using R32 refrigerant only)
protection is aected.
not made to original specication, damage to seals, incorrect tting of glands, etc.
serve the purpose of preventing the ingress of ammable atmospheres. Replacement
parts shall be in accordance with the manufacturer’s specications.
NOTE: The use of silicon sealant may inhibit the eectiveness of some types of leak
presence of a ammable atmosphere. The test apparatus shall be at the correct rating.
Replace components only with parts specied by the manufacturer. Other parts may
vibration, sharp edges or any other adverse environmental eects. The check shall
also take into account the eects of aging or continual vibration from sources such
Detection of ammable refrigerants
naked ame) shall not be used.
ammable refrigerants. Electronic leak detectors shall be used to detect ammable
gas (25 % maximum) is conrmed. Leak detection uids are suitable for use with
suspected, all naked ames shall be removed/ extinguished. If a leakage of
from the system, or isolated (by means of shut o valves) in a part of the system
Safety
Precautions
Page 9
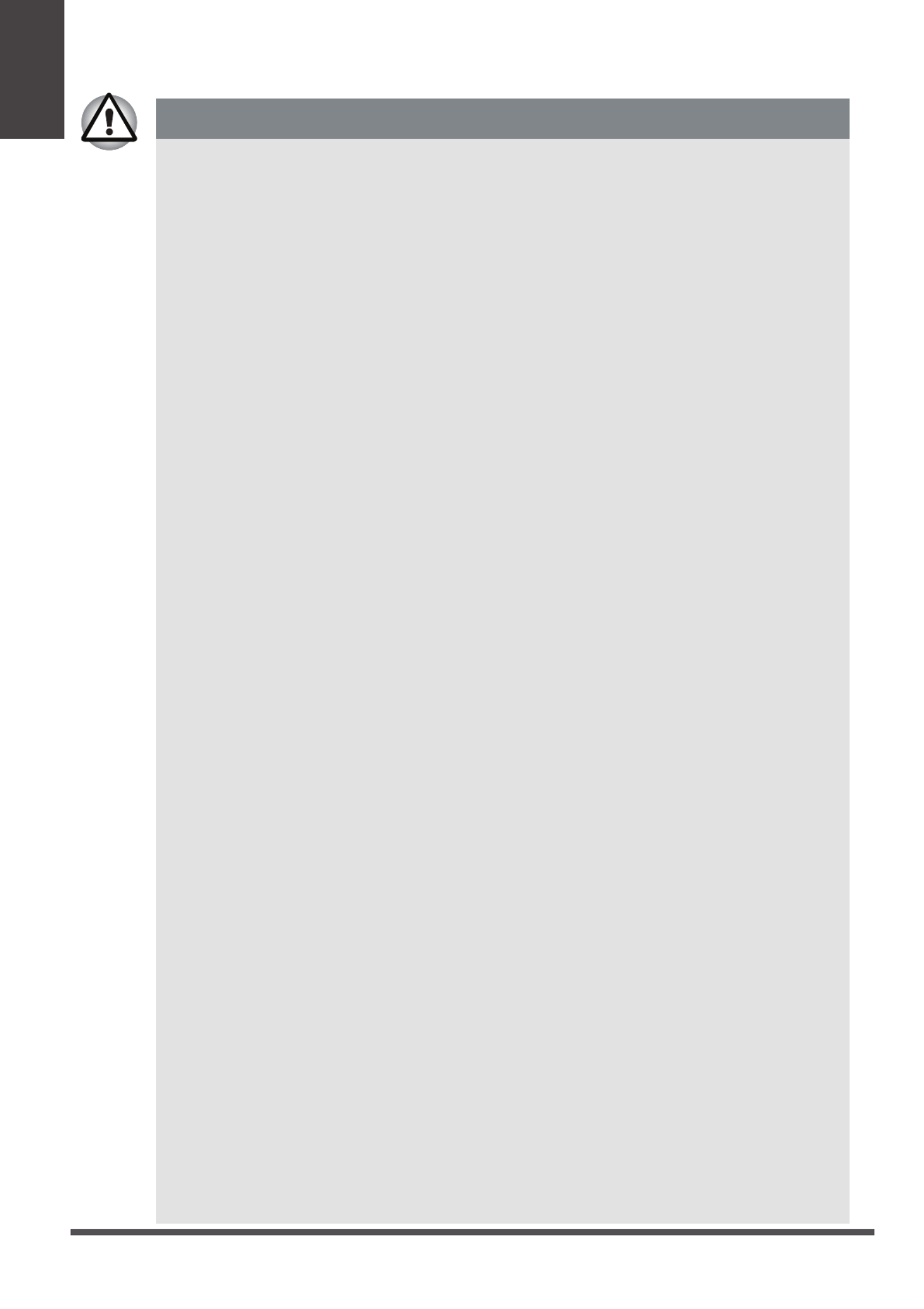
Removal and evacuation
When breaking into the refrigerant circuit to make repairs or for any other purpose
conventional procedures shall be used. However, it is important that best practice is
shall not be done by brazing.
The following procedure shall be adhered to:
Remove refrigerant;
Purge the circuit with inert gas;
Evacuate;
Purge again with inert gas;
Open the circuit by cutting or brazing.
The refrigerant charge shall be recovered into the correct recovery cylinders. The
to be repeated several times. Compressed air or oxygen shall not be used for this
task. Flushing shall be achieved by breaking the vacuum in the system with OFN
system shall be vented down to atmospheric pressure to enable work to take place.
This operation is absolutely vital if brazing operations on the pipe-work are to take
place.
Ensure that the outlet for the vacuum pump is not close to any ignition sources and
there is ventilation available.
• Charging procedures
In addition to conventional charging procedures, the following requirements shall be
using charging equipment. Hoses or lines shall be as short as possible to minimise
the amount of refrigerant contained in them.
Cylinders shall be kept upright.
Ensure that the refrigeration system is earthed prior to charging the system with
refrigerant. Label the system when charging is complete (if not already).
Prior to recharging the system it shall be pressure tested with OFN. The system
shall be leak tested on completion of charging but prior to commissioning. A follow
up leak test shall be carried out prior to leaving the site.
• Decommissioning
Before carrying out this procedure, it is essential that the technician is completely
familiar with the equipment and all its detail. It is recommended good practice that
all refrigerants are recovered safely. Prior to the task being carried out, an oil and
refrigerant sample shall be taken in case analysis is required prior to re-use of
reclaimed refrigerant. It is essential that electrical power is available before the
task is commenced.
a) Become familiar with the equipment and its operation.
b) Isolate system electrically.
c) Before attempting the procedure ensure that:
Mechanical handling equipment is available, if required, for handling refrigerant
cylinders;
All personal protective equipment is available and being used correctly;
The recovery process is supervised at all times by a competent person;
Recovery equipment and cylinders conform to the appropriate standards.
WARNINGS (for using R32 refrigerant only)
followed since ammability is a consideration. Opening of the refrigeration systems
system shall be ushed with OFN to render the unit safe. This process may need
and continuing to ll until the working pressure is achieved, then venting to
atmosphere, and nally pulling down to a vacuum. This process shall be repeated
until no refrigerant is within the system. When the nal OFN charge is used, the
followed. Ensure that contamination of dierent refrigerants does not occur when
Extreme care shall be taken not to overll the refrigeration system.
Safety
Precautions
Page 10
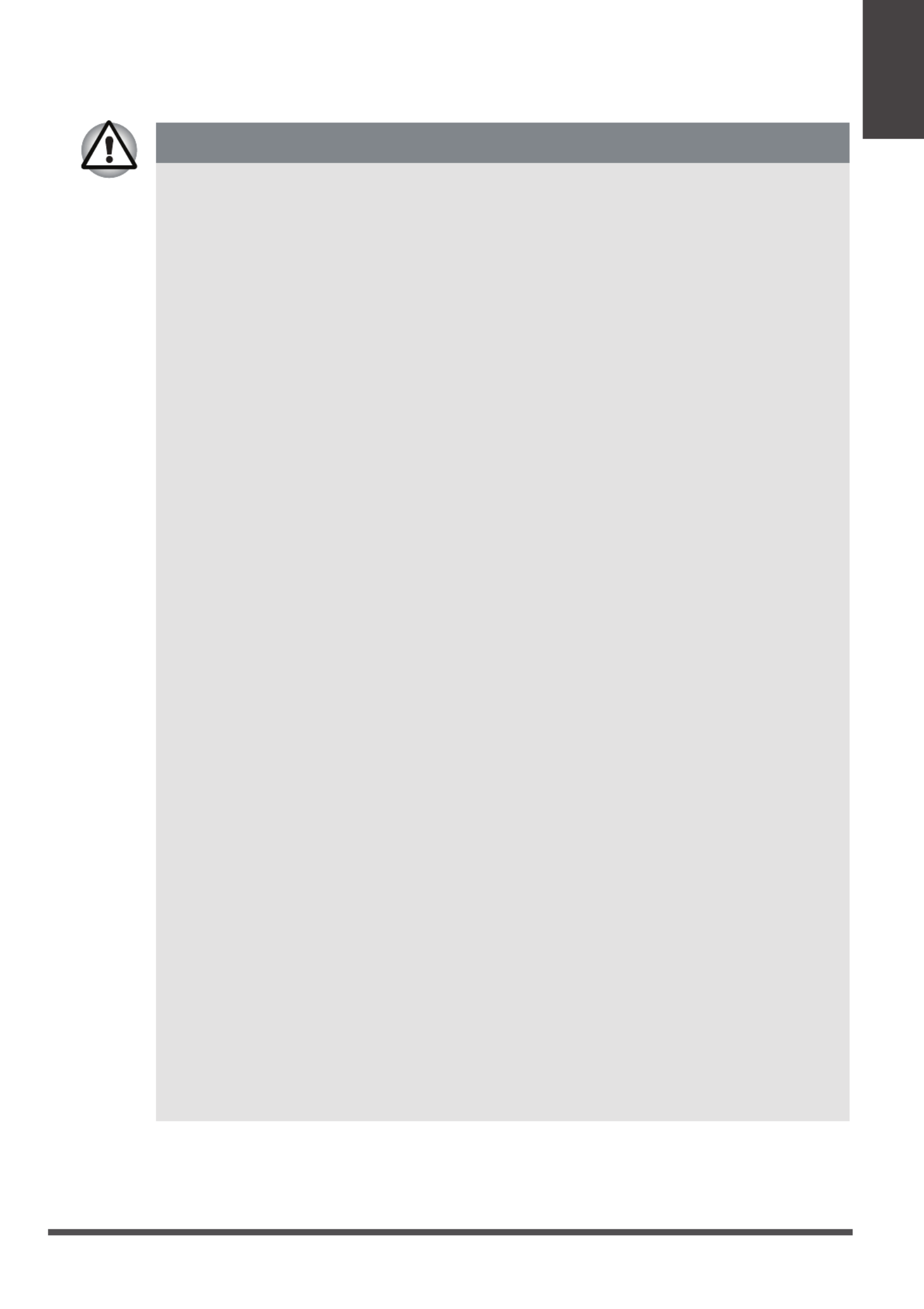
d) Pump down refrigerant system, if possible.
e) If a vacuum is not possible, make a manifold so that refrigerant can be removed
from various parts of the system.
f) Make sure that cylinder is situated on the scales before recovery takes place.
g) Start the recovery machine and operate in accordance with manufacturer's
instructions.
i) Do not exceed the maximum working pressure of the cylinder, even temporarily.
sure that the cylinders and the equipment are removed from site promptly and all
iless
it has been cleaned and checked.
• Labelling
Equipment shall be labelled stating that it has been de-commissioned and emptied
of refrigerant. The label shall be dated and signed. Ensure that there are labels on
the equipment stating the equipment contains ammable refrigerant.
• Recovery
When removing refrigerant from a system, either for servicing or decommissioning,
it is recommended good practice that all refrigerants are removed safely.
When transferring refrigerant into cylinders, ensure that only appropriate refrigerant
recovery cylinders are employed. Ensure that the correct number of cylinders for
holding the total system charge is available. All cylinders to be used are designated
for the recovered refrigerant and labelled for that refrigerant (i.e. special cylinders
for the recovery of refrigerant). Cylinders shall be complete with pressure relief
cylinders are evacuated and, if possible, cooled before recovery occurs.
The recovery equipment shall be in good working order with a set of instructions
concerning the equipment that is at hand and shall be suitable for the recovery of
available and in good working order. Hoses shall be complete with leak-free
disconnect couplings and in good condition. Before using the recovery machine,
check that it is in satisfactory working order, has been properly maintained and that
any associated electrical components are sealed to prevent ignition in the event of
a refrigerant release. Consult manufacturer if in doubt.
The recovered refrigerant shall be returned to the refrigerant supplier in the correct
recovery cylinder, and the relevant Waste Transfer Note arranged. Do not mix
refrigerants in recovery units and especially not in cylinders. If compressors or
compressor oils are to be removed, ensure that they have been evacuated to an
the lubricant. The evacuation process shall be carried out prior to returning the
compressor to the suppliers. Only electric heating to the compressor body shall be
employed to accelerate this process. When oil is drained from a system, it shall be
carried out safely.
WARNINGS (for using R32 refrigerant only)
h) Do not overll cylinders. (No more than 80 % volume liquid charge).
j) When the cylinders have been lled correctly and the process completed, make
isolation valves on the equipment are closed o.
valve and associated shut-o valves in good working order. Empty recovery
ammable refrigerants. In addition, a set of calibrated weighing scales shall be
acceptable level to make certain that ammable refrigerant does not remain within
Safety
Precautions
Page 11
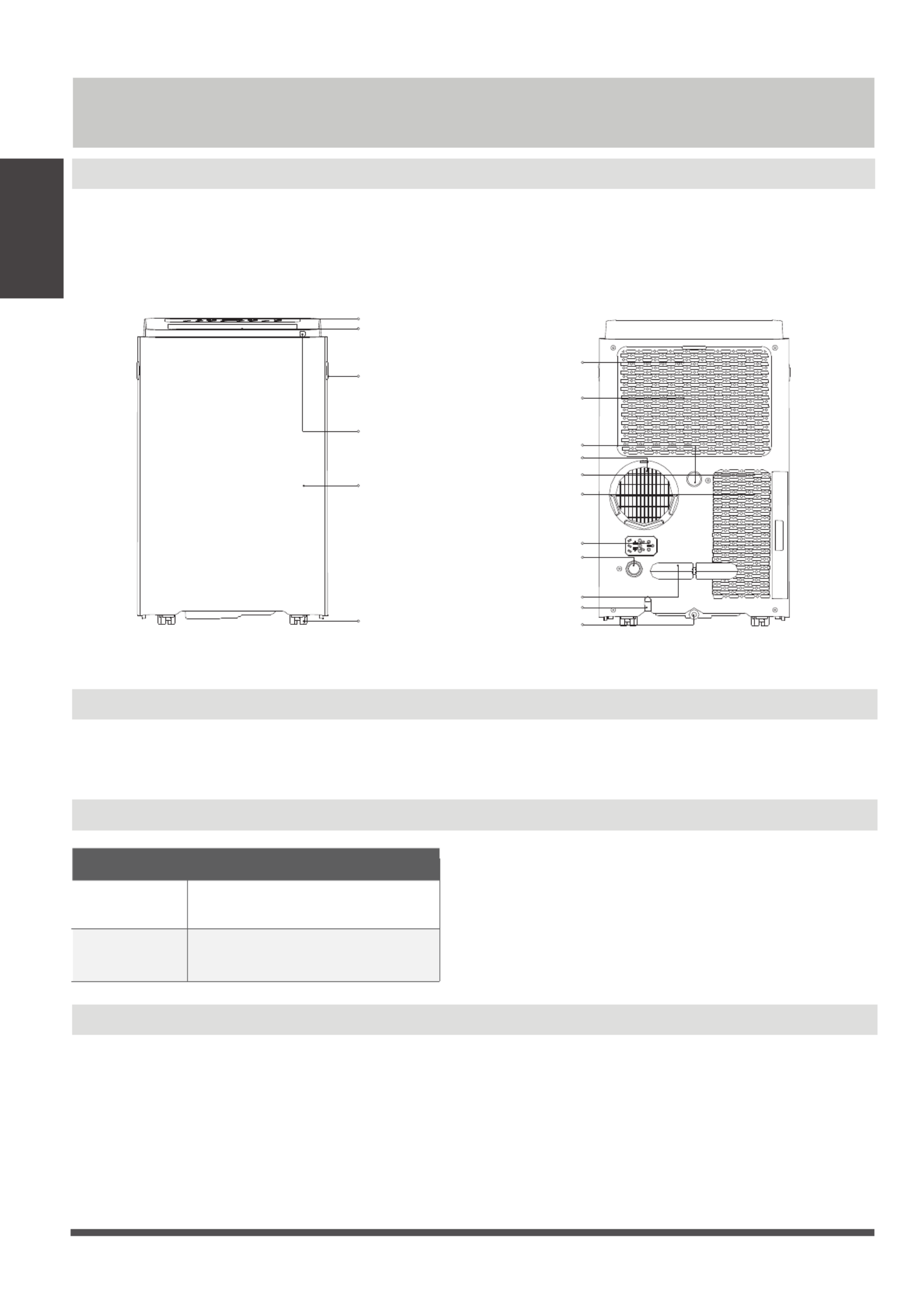
Installation
Instructions
Installation Instructions
Preparation
NOTE:
All the illustrations in the manual are for explanation purpose only. Your machine may be slightly dierent.
The actual shape shall prevail. The unit can be controlled by the unit control panel alone or with the remote
controller.
MODE Temperature Range
Design Notice
Ambient Temperature Range For Unit Operating
Exhaust Hose Installation
In order to ensure the optimal performance of our products, the design specifications of the unit and
remote control are subject to change without prior notice.
Cool 17-35°C (62-95°F)
Dry 13-35°C (55-95°F)
control panel
handle
(both sides)
horizontal louver
blade
(swing automatically)
Caster
Panel
remote signal
receptor
power plug socket
power cord buckle
bottom tray
drain outlet
power cord outlet
drain outlet
(only for pump
heating mode)
upper air lter
(behind the grille)
upper air intake
air outlet
lower air lter
lower air intake
drain outlet
rearfront
The exhaust hose and adaptor must be installed or removed in accordance with the usage mode. For
COOL,HEAT(heat pump type) or AUTO mode must be installed exhaust hose. For FAN, DRY or HEAT
(electrical heat type) mode must be removed exhaust hose.
Page 12
Produkt Specifikationer
Mærke: | Midea |
Kategori: | Klimaanlæg |
Model: | MP86SQWBA2RCM |
Har du brug for hjælp?
Hvis du har brug for hjælp til Midea MP86SQWBA2RCM stil et spørgsmål nedenfor, og andre brugere vil svare dig
Klimaanlæg Midea Manualer
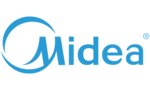
18 Februar 2025
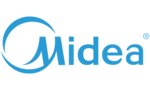
18 Februar 2025
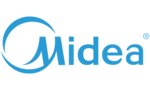
17 Februar 2025
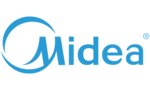
12 Februar 2025
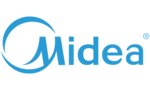
12 Februar 2025
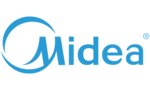
12 Februar 2025
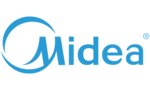
11 Februar 2025
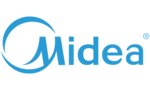
24 December 2024
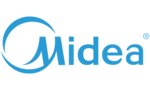
5 December 2024
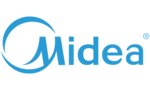
5 December 2024
Klimaanlæg Manualer
- Klimaanlæg DeLonghi
- Klimaanlæg Bosch
- Klimaanlæg Sencor
- Klimaanlæg TCL
- Klimaanlæg Zibro
- Klimaanlæg Siemens
- Klimaanlæg Day
- Klimaanlæg Samsung
- Klimaanlæg Wilfa
- Klimaanlæg GE
- Klimaanlæg Daikin
- Klimaanlæg Zanussi
- Klimaanlæg CyberPower
- Klimaanlæg Panasonic
- Klimaanlæg Gorenje
- Klimaanlæg Tectro
- Klimaanlæg VOX
- Klimaanlæg Concept
- Klimaanlæg OK
- Klimaanlæg LG
- Klimaanlæg AEG
- Klimaanlæg Electrolux
- Klimaanlæg Bauknecht
- Klimaanlæg Whirlpool
- Klimaanlæg Mitsubishi
- Klimaanlæg Master
- Klimaanlæg Sharp
- Klimaanlæg Hotpoint
- Klimaanlæg Melissa
- Klimaanlæg ARGO
- Klimaanlæg Qlima
- Klimaanlæg Daewoo
- Klimaanlæg Korona
- Klimaanlæg Arçelik
- Klimaanlæg Soler & Palau
- Klimaanlæg Sanyo
- Klimaanlæg Baxi
- Klimaanlæg Grundig
- Klimaanlæg Progress
- Klimaanlæg Hotpoint Ariston
- Klimaanlæg Livoo
- Klimaanlæg Toshiba
- Klimaanlæg Klarstein
- Klimaanlæg Furrion
- Klimaanlæg Infiniton
- Klimaanlæg Trisa
- Klimaanlæg Matsui
- Klimaanlæg Nedis
- Klimaanlæg Emerio
- Klimaanlæg Bartscher
- Klimaanlæg Be Quiet!
- Klimaanlæg Sauber
- Klimaanlæg Westinghouse
- Klimaanlæg Element
- Klimaanlæg Thomson
- Klimaanlæg Hyundai
- Klimaanlæg AKAI
- Klimaanlæg Hisense
- Klimaanlæg TriStar
- Klimaanlæg Brandt
- Klimaanlæg Adler
- Klimaanlæg Camry
- Klimaanlæg Dometic
- Klimaanlæg Eurom
- Klimaanlæg TecLime
- Klimaanlæg Trotec
- Klimaanlæg Blaupunkt
- Klimaanlæg Einhell
- Klimaanlæg Becken
- Klimaanlæg BEKO
- Klimaanlæg Honeywell
- Klimaanlæg Clatronic
- Klimaanlæg Hitachi
- Klimaanlæg Rowenta
- Klimaanlæg Noveen
- Klimaanlæg Ariston Thermo
- Klimaanlæg Haier
- Klimaanlæg Truma
- Klimaanlæg Bomann
- Klimaanlæg Innoliving
- Klimaanlæg Zelmer
- Klimaanlæg Vivax
- Klimaanlæg Thermex
- Klimaanlæg Vaillant
- Klimaanlæg Alaska
- Klimaanlæg Zanker
- Klimaanlæg Galanz
- Klimaanlæg Amana
- Klimaanlæg Amcor
- Klimaanlæg Carrier
- Klimaanlæg Comfee
- Klimaanlæg Gree
- Klimaanlæg Dimplex
- Klimaanlæg Tripp Lite
- Klimaanlæg Primo
- Klimaanlæg Orbegozo
- Klimaanlæg Malmbergs
- Klimaanlæg Sigma
- Klimaanlæg Koenig
- Klimaanlæg Taurus
- Klimaanlæg Xiaomi
- Klimaanlæg Exquisit
- Klimaanlæg HQ
- Klimaanlæg Proklima
- Klimaanlæg Elba
- Klimaanlæg Air Breeze
- Klimaanlæg Fujitsu
- Klimaanlæg Inventor
- Klimaanlæg MPM
- Klimaanlæg Toyotomi
- Klimaanlæg Frigor
- Klimaanlæg TOSOT
- Klimaanlæg APC
- Klimaanlæg Domo
- Klimaanlæg Ferroli
- Klimaanlæg Saunier Duval
- Klimaanlæg Heylo
- Klimaanlæg Olimpia Splendid
- Klimaanlæg Aspes
- Klimaanlæg Eden
- Klimaanlæg Blumfeldt
- Klimaanlæg Inventum
- Klimaanlæg Altech
- Klimaanlæg Carson
- Klimaanlæg Fakir
- Klimaanlæg White Knight
- Klimaanlæg Dantherm
- Klimaanlæg Khind
- Klimaanlæg Frigidaire
- Klimaanlæg Frilec
- Klimaanlæg Evolar
- Klimaanlæg Ridgid
- Klimaanlæg Ardes
- Klimaanlæg Suntec
- Klimaanlæg SVAN
- Klimaanlæg Everglades
- Klimaanlæg Danby
- Klimaanlæg RCA
- Klimaanlæg ECG
- Klimaanlæg General Electric
- Klimaanlæg Eldom
- Klimaanlæg H.Koenig
- Klimaanlæg Sonnenkönig
- Klimaanlæg Termozeta
- Klimaanlæg OneConcept
- Klimaanlæg Stirling
- Klimaanlæg Just Fire
- Klimaanlæg Be Cool
- Klimaanlæg Duux
- Klimaanlæg ElectriQ
- Klimaanlæg Kalorik
- Klimaanlæg Cecotec
- Klimaanlæg Airwell
- Klimaanlæg Anslut
- Klimaanlæg MundoClima
- Klimaanlæg Jocca
- Klimaanlæg Orima
- Klimaanlæg SereneLife
- Klimaanlæg Remko
- Klimaanlæg Friedrich
- Klimaanlæg Whynter
- Klimaanlæg Bestron
- Klimaanlæg Philco
- Klimaanlæg Fuave
- Klimaanlæg Avidsen
- Klimaanlæg Climadiff
- Klimaanlæg Kogan
- Klimaanlæg Ravanson
- Klimaanlæg Airlux
- Klimaanlæg Jocel
- Klimaanlæg Ufesa
- Klimaanlæg Keystone
- Klimaanlæg ActronAir
- Klimaanlæg Orava
- Klimaanlæg NewAir
- Klimaanlæg IFB
- Klimaanlæg Create
- Klimaanlæg Daitsu
- Klimaanlæg Daizuki
- Klimaanlæg Profile
- Klimaanlæg AireMax
- Klimaanlæg Aconatic
- Klimaanlæg Aermec
- Klimaanlæg Acson
- Klimaanlæg Andrews
- Klimaanlæg Akira
- Klimaanlæg Aircooler
- Klimaanlæg Airview
- Klimaanlæg Aertesi
- Klimaanlæg Royal Sovereign
- Klimaanlæg Alberello
- Klimaanlæg Salton
- Klimaanlæg Haverland
- Klimaanlæg Rasonic
- Klimaanlæg Mabe
- Klimaanlæg Heinner
- Klimaanlæg Nabo
- Klimaanlæg AlpicAir
- Klimaanlæg Kelvinator
- Klimaanlæg Tatung
- Klimaanlæg Milectric
- Klimaanlæg Lloyd
- Klimaanlæg Alpatec
- Klimaanlæg Godrej
- Klimaanlæg Maiko
- Klimaanlæg Aircool
- Klimaanlæg Igenix
- Klimaanlæg Edgestar
- Klimaanlæg Maxicool
- Klimaanlæg Argoclima
- Klimaanlæg Home Electric
- Klimaanlæg Teco
- Klimaanlæg Tarrington House
- Klimaanlæg Gutfels
- Klimaanlæg Telair
- Klimaanlæg Klarbach
- Klimaanlæg Mobile Airco
- Klimaanlæg Heiko
- Klimaanlæg Qlima - Zibro
- Klimaanlæg VänEE
- Klimaanlæg Handson
- Klimaanlæg Bryant
- Klimaanlæg Klima1stKlaas
- Klimaanlæg Emmeti
- Klimaanlæg Evapolar
- Klimaanlæg Ausclimate
- Klimaanlæg ARCTIC WIND
- Klimaanlæg Perfect Aire
- Klimaanlæg Black Decker
- Klimaanlæg TechnoLife
- Klimaanlæg Shinco
- Klimaanlæg Innova
- Klimaanlæg D-Let
- Klimaanlæg Domair
- Klimaanlæg General
- Klimaanlæg SEEGER
- Klimaanlæg Thermo Comfort
- Klimaanlæg Mizushi
- Klimaanlæg Sinclair
- Klimaanlæg Arcoaire
- Klimaanlæg Zymbo
- Klimaanlæg GoldAir
- Klimaanlæg Saneo
- Klimaanlæg Columbia Vac
- Klimaanlæg Kostal
- Klimaanlæg SMD
- Klimaanlæg Artrom
- Klimaanlæg Commercial Cool
- Klimaanlæg Coolix
- Klimaanlæg Omega Altise
- Klimaanlæg Koldfront
- Klimaanlæg Yamazen
- Klimaanlæg Corona
- Klimaanlæg Symphony
- Klimaanlæg Universal Blue
- Klimaanlæg Air&Me
- Klimaanlæg Onix
Nyeste Klimaanlæg Manualer

4 April 2025

2 April 2025
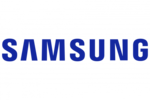
28 Marts 2025

27 Marts 2025

17 Marts 2025

17 Marts 2025

14 Marts 2025

6 Marts 2025

3 Marts 2025

3 Marts 2025